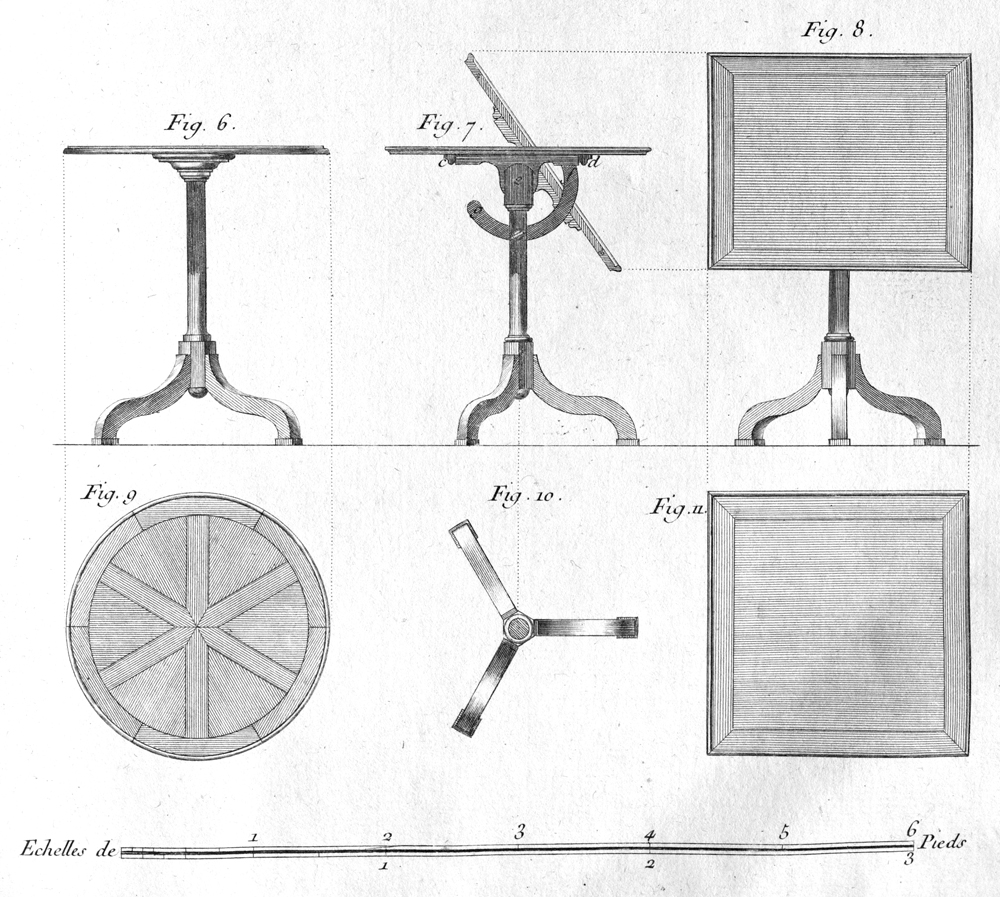
We are making the final pass through “Roubo on Furniture” during the next couple weeks. Kara Gebhart Uhl is looking for mistakes that have eluded us for the last three years, Suzanne Ellison is updating the index and I’m building the book’s table of contents.
We plan to go to press with the standard edition of “Roubo on Furniture” in early January with a mid-February release. We also will publish a deluxe edition, which design Wesley Tanner will begin working on shortly. Details to come on how to order the deluxe version.
In the meantime, take a look at the table of contents. Whew.
— Christopher Schwarz
Preface xi
A Key to the Text xiv
The Woods Appropriate for Joinery 3
Section I. The Different Qualities of Wood 3
Section II. Fashioning and Stacking of Wood 7
Section III. The Cutting of Wood 13
The Art of Assembly, its Uses and Proportions 21
Section I. Different Ways to Elongate Wood 25
Some Tools Belonging to Woodworkers, Their Different Types, Forms and Uses 29
Section I. Tools of the Shop 32
Section II. The Tools Belonging to the Workmen 33
Section III. Some Tools Appropriate for Cutting and Planing the Wood 34
The Plate 11 Workbench: How it (Really) Works 38
Make Roubo’s ‘Winding Sticks’ 54
Section IV. The Tools for Marking and Making Joints 59
Section V. The Tools for Fretwork, and those for Cutting the Straight and Curved Mouldings 76
The Art of Drawing 89
Section I. The Way to Take Measurements 89
The Way to Draw the Work on the Plan 93
The Way to Prepare Joinery to Receive Carved Ornaments 95
Section II. The Way to Glue Wood 99
The Way to Construct Columns in Wood; Bases, Capitals, Entablature and Pedestals 103
Section III. The Way of Gluing Curved Wood 109
Joinery in Furniture, in General, and the Different Types 112
Section I. The Tools and Woods appropriate for Furniture 114
Ancient Furniture in General 115
Some Different Types of Seats in Use at Present 119
Section II. The Description of Folding Chairs, Stools, Benches, etc. Their Forms, Proportion and Construction 120
Section III. Descriptions of all sorts of [side] chairs, their decorations, forms, proportions and construction 126
The Way to Prepare Seats to Receive Fabric Ornamentation 135
Roubo on Upholstery 137
Section IV. The Upholstery of Chairs with Caning and the Art of Caning in General 141
The Way to Prepare Seats for Caning 141
Selection of the cane, the way of splitting it and the caners’ tools 145
Various Methods of Weaving and Diverse Operations of the Caner 149
Different Sorts of Seating Forms, Proportions & Construction 155
Roubo, Meet Reality: The Making of A Classical French Chairmaker 164
Section I. Description of all the major seats, like canapés, sofas, ottomans, etc. 181
Section II. Description of Private Apartment Seats, like Bathing-tubs, Demi-bathing tubs, etc. 193
Of Beds in General and the Different Sorts 201
Section I. The Beds of France: Forms, Proportions & Construction 202
Canopies of Beds, Commonly Called Pavilions or Imperials; Their Forms and Construction 210
Section II. Description of Polish-style Beds, their Proportions, Shapes & Decoration 220
Section III. Description of different types of campaign Beds, their shapes and construction 226
Section IV. Description of Daybeds, some Cradles and Cots 235
Tables in General and the Different Types 239
Section I. Different Forms and Constructions of Dining Tables 245
Section II. Game Tables and their different types, forms and constructions 249
Description of a Billiard Table, its form, proportion and construction 249
Description of Gaming Tables, their form, proportions and construction 261
Section III. Tables for writing and their different types, forms and constructions 270
Description of Dressing Tables and Night Tables, and others 293
Description of Screens and Windbreaks; their forms and proportions 296
Case Pieces Known under the General Name of Large Pieces 301
Section I. Description of Armoires; their decoration, proportions and construction 302
Description of Buffets; their forms, proportions, decoration & construction 309
Description of Commodes; their forms, proportions and construction 315
Of Solid Cabinetry Or Assembly in General 325
Section I. Description of the Tools of the Furniture Maker, their assembly and how to use them 327
Section II. Basic Elements on the Part of the Art of Turning necessary for the Furniture Maker 331
Some Screw Taps and Wooden Dies used by Cabinetmakers 343
The Machines Appropriate for Making Fluting for Cylinders and Cones 347
Description of the Machine commonly called the tool for waves 358
Reproducing and Using Moxon’s ‘Waving Engine’ 366
Section III. Different Locksmithing Tools for the Furniture Maker 378
The Way to fit the iron work for cabinetry 392
The Manner of polishing iron and copper relative to cabinetry 402
Section IV. Different Kinds of Solid or Assembled Cabinetry in General 404 Description of different sorts of embroidery frames 405
Description of a printing cabinet 417
Description of Gueridons and Small Tables 427
Description of Different Forms of Desks 430
Necessaries and Other Types of Boxes 437
Afterword to ‘Roubo on Furniture’ 443
Appendix: André-Jacob Roubo 445
Index 451
Like this:
Like Loading...