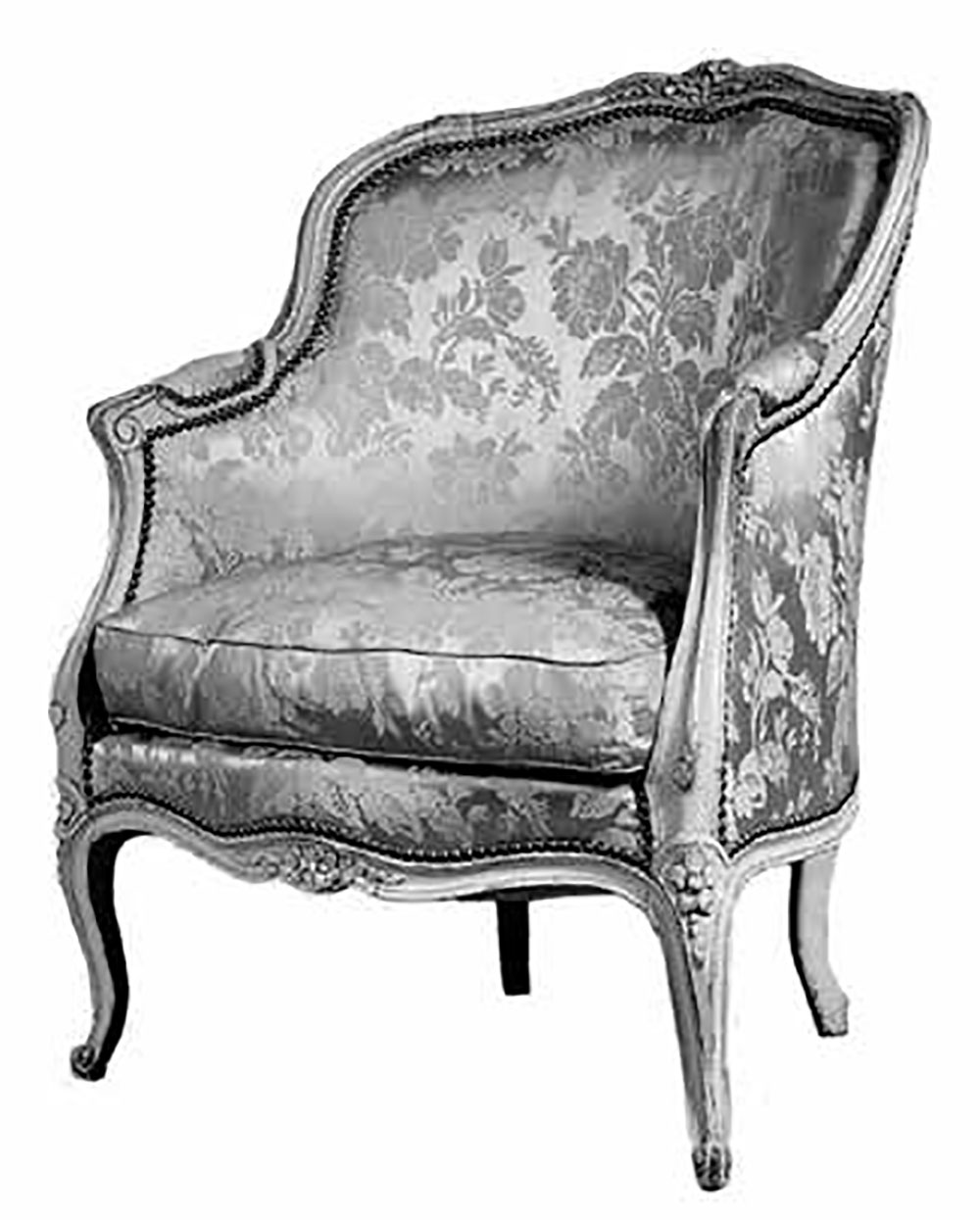
This is an excerpt from “With All the Precision Possible: Roubo on Furniture” by André-Jacob Roubo; translation by Donald C. Williams, Michele Pietryka-Pagán & Philippe Lafargue.
So Roubo could not very well do a comprehensive book on furniture making without including some mention of how to prepare frames for upholstery, and yet in his opening line he gives a real clue as to his general feelings about the matter. He says, “…seats in general are finished with fabric or caning…where the former is the most utilized and totally the province of the upholsterer.” It is not difficult to imagine Roubo arguing with an irate upholsterer over the details of a frame, just the way that modern upholsterers complain about the placement of tacking rails, and in the end just let the upholsterer figure out how to complete the chair. Roubo is clear on how to prepare loose or “slip” seats, those that are removable from the chair, but when he discusses how upholstery materials are permanently attached, it was just not so.
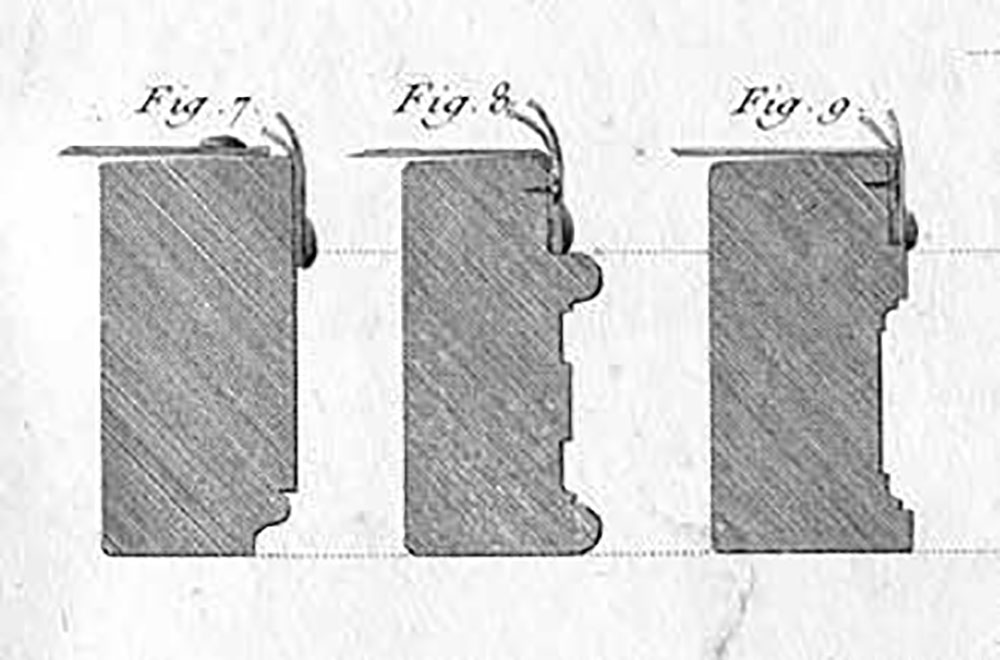
In Plate 227 Roubo provides three figures in profile of the attachment of webbing to massive carved frames, these are figures 7, 8 & 9. Upon first seeing this plate, my reaction was simply, “Impossible!” But knowing Roubo’s meticulous drawing skill and thorough work, there had to be an answer.
Figure 8 clearly shows (from left) the webbing attached to the side of the rail, tacked near the top, a next layer of under upholstery (muslin) tacked below that, and finally a show cover attached with decorative tacks right at the top of the decorative moulding. As a student of the English tradition of upholstery, this was unfamiliar to me, as the English securely tack the webbing to the top of the frame (as shown in Figure 7) and thereby have good access to stretch or “strain” it tight. So then why is Roubo showing the webbing in Figure 8 this way? I put this question to everyone I thought could help until I was fortunate to meet the gifted, classically trained and very French master upholsterer Bruno Paulin-Lopez. Interestingly, Roubo, was not required reading for his training, though he was familiar with the well-known and contemporary book on the trades by Denis Diderot, and another massive text called Tapisseire D’Ameublement by Claude Ossut (not translated into English), both of which explain in quite some detail how to web a chair frame.
First and foremost, the French tradition of webbing requires the webs to be placed tight, side by side with no gaps, unlike the English, which employs an open weave pattern, and this is critical to understanding what Roubo is portraying. And secondly, this type of un-sprung upholstery (chair, ottoman, chaise, etc.) would have a considerable, in some cases massive, pillow on top of the webbed “deck.” Finally, Roubo, seemingly aware that he is not being clear, gives us some information in a long footnote. To paraphrase, “…most upholsterers feel that the webbing should be on the side, while others are convinced that it could be on the top of the frame, which would make it very firm.”
With Bruno’s guidance, I have come to believe that the “most upholsterers” Roubo consulted were the older generation who grew up tacking everything on the side of the rails and whom Roubo did not dare slight in his representation of how this should be done. And the “others” are those talented pioneers desperately trying to make sure their upholstery methods could keep up with the fast-changing furniture styles of the opulent French court, such as the elegant gentleman craftsman portrayed by Diderot.
The following is a recreation to scale of Figure 8 and shows an interpretation of how the webbing would have been placed unfolded on the rabbeted edge, followed by a muslin layer tacked slightly above, and finally the show cover tacked right at the edge with decorative tacks. Because the webbing is side by side, there is a smooth surface for the succeeding layers, and because the piece is un-sprung it would not be necessary to stretch the webbing as tightly, and would actually give the bottom of the pillow a place to nestle.
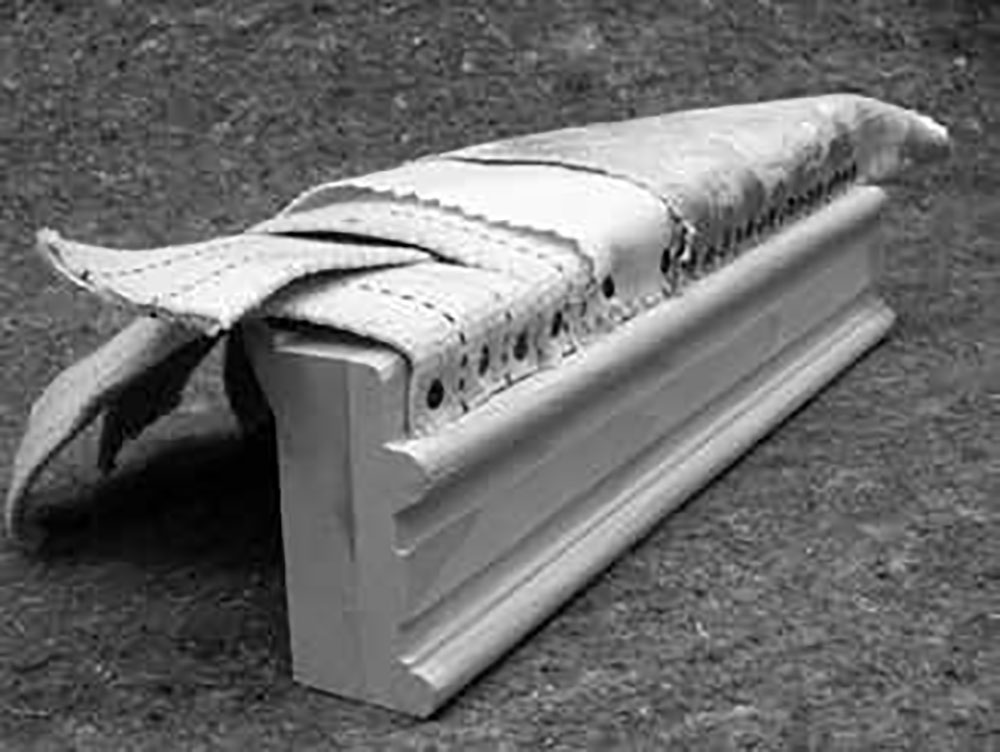
The next recreation uses the same frame pattern and shows a more “modern” approach with webbing folded under, tacked on top of the rail, followed by a layer of linen hessian tacked on a beveled edge to save the space on the front of the rail for the tacking of the show cover. This technique is similar to the English style.
The final recreation shows a full hand-sewn foundation using a coarse “first stuffing” material, which is drawn by careful stitching to form a firm seat and a rolled edge. This technique evolved in both the French and English traditions, and creates a custom, extremely durable base for a softer second stuffing and made possible the upholstery of many complex furniture designs.
I feel confident in saying that Roubo would be truly pleased to know that the techniques he illustrated as well as their many variations are still practiced by the finest upholsterers working today. — Michael Mascelli
— MB