
Editor’s note: “Henry Boyd’s Freedom Bed” by Whitney LB Miller is the true story of an incredible 19th-century furniture maker who fought for his freedom, invented a renowned (and patented) bed and helped many enslaved people escape to freedom. For the last 25 years I have walked the same streets as Boyd and thought a lot about his neighborhood and his life.
Almost every morning I take a long walk – usually four or five miles – into a different district of Covington, Newport or Cincinnati. I especially love to go down the brick alleys that have been unchanged for 200 years (and are in better shape than the asphalt main roads).
But the most interesting days are when I visit Henry Boyd’s neighborhood, which is almost unrecognizable from when he lived there in the early 19th century. Though I am always looking for clues from his time.
Boyd lived on the east side of downtown Cincinnati. And starting about 1834 his address was on New Street. New Street definitely lives up to its name, even today. Everything on it is new. There are no houses or period buildings. It’s all just parking garages that service the big downtown firms, such as Procter & Gamble. The company’s world headquarters is just a couple blocks south.
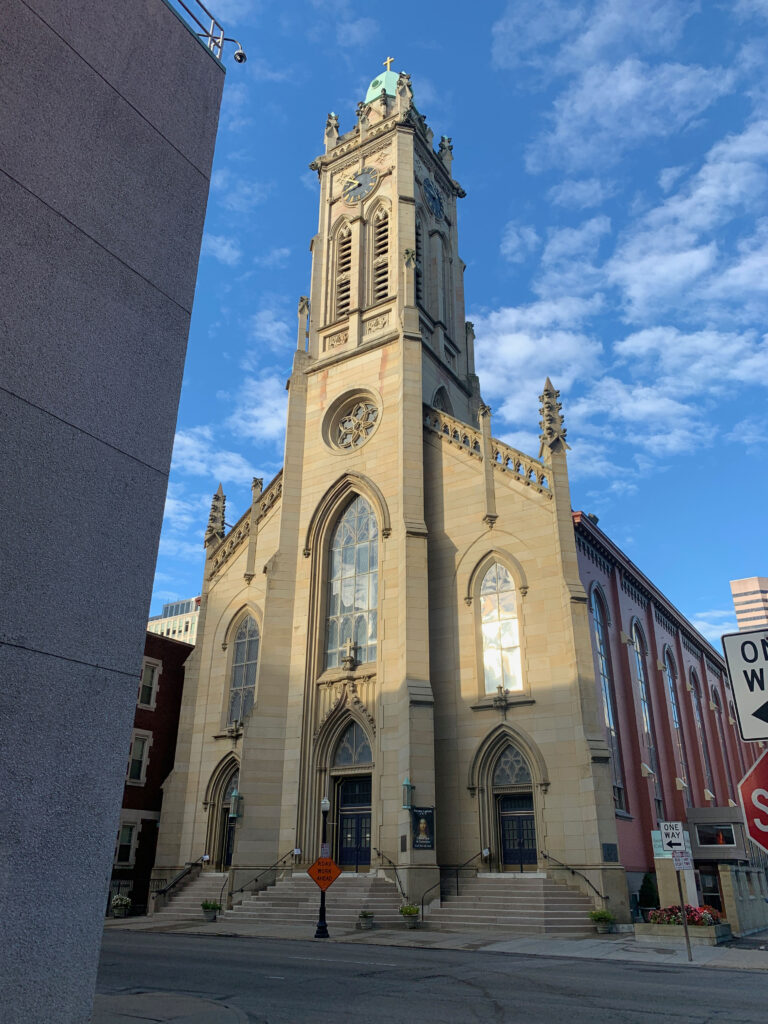
When I walk down New Street, I look for any landmark that Henry Boyd would recognize. There are a couple. First is St. Francis Xavier Church. Established in 1826, this church stands on Sycamore Street and looks down New Street. When Boyd left his house for work, this was likely the largest structure in his neighborhood.
The building would have looked different then. The current St. Francis is a huge masonry structure. The original one was a frame structure that was moved to this location on wheels.
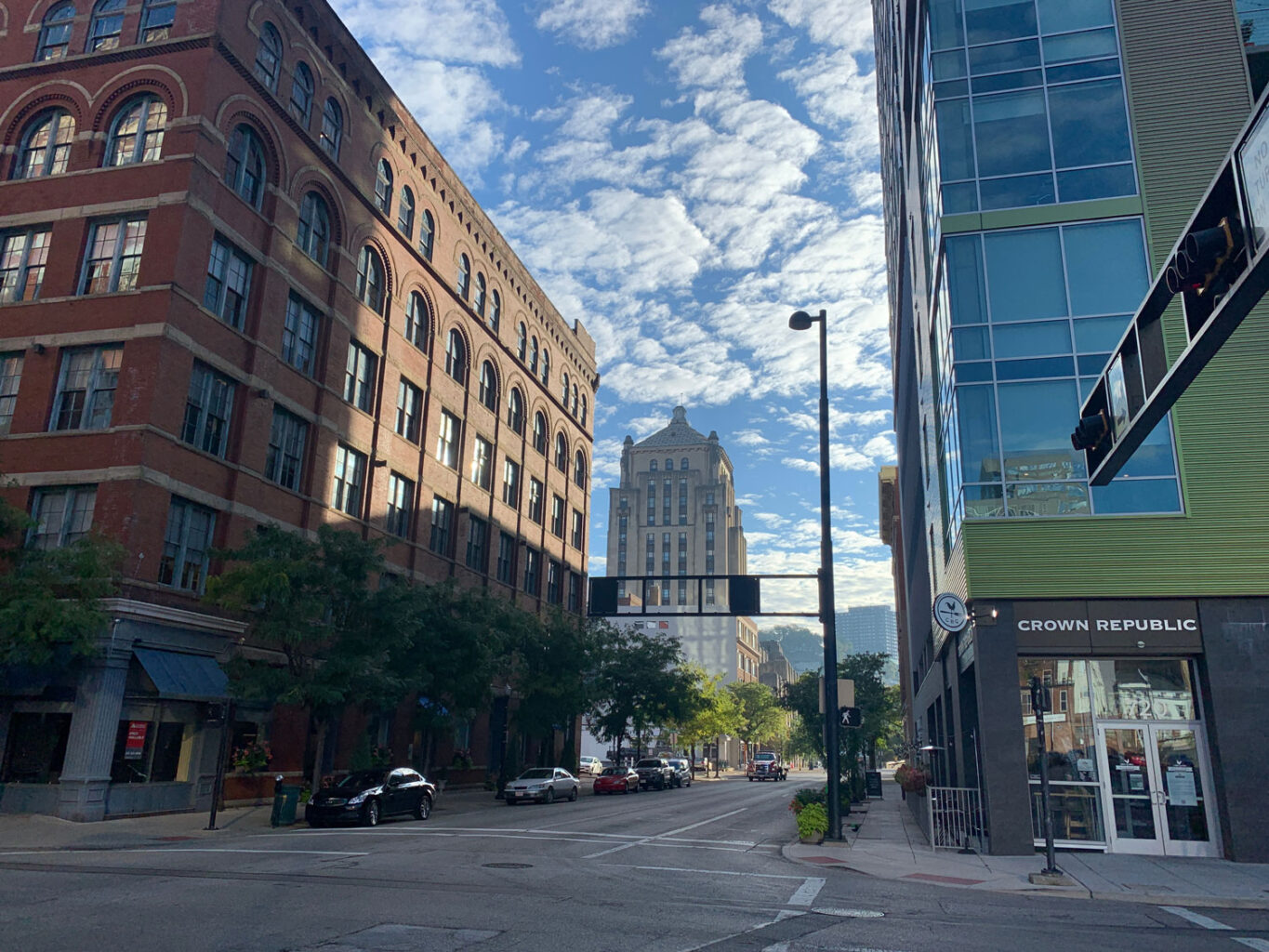
When Boyd went to work, he likely walked north up either Sycamore or Broadway streets to his factory at 8th and Broadway. This intersection is one of my favorites in town. After reading all Suzanne Ellison’s research on Boyd’s business it’s unclear exactly where his factory and other buildings were located, as it seems they were on both sides of Broadway. On one side of Broadway is my favorite building in the city, the Cincinnati Times Star Building. It’s an Art Deco masterpiece now used as a government building.
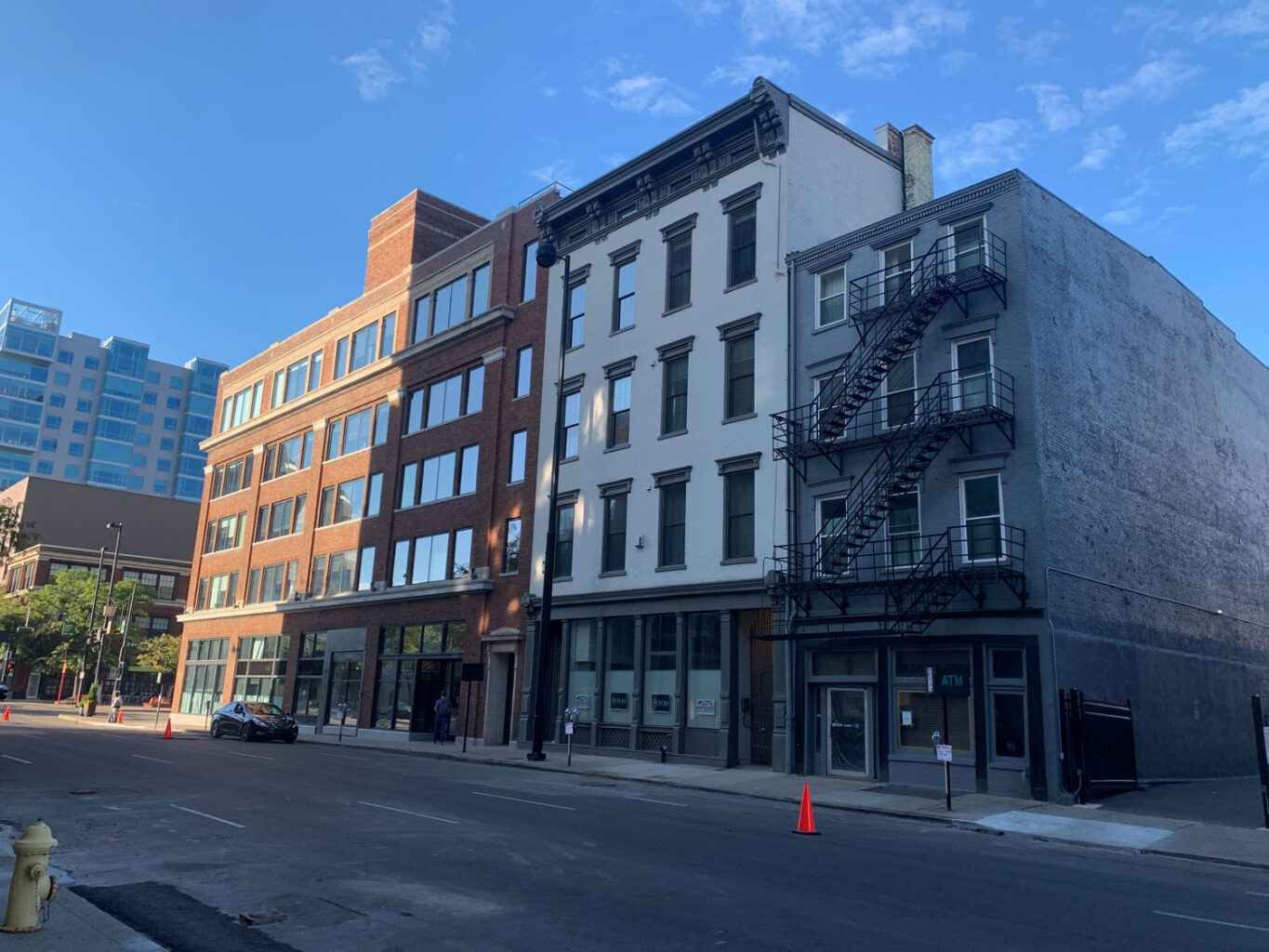
Across the street are a couple factory buildings that have been converted into trendy office buildings. One is from the early 20th century. The other is earlier, perhaps much earlier. Unlike New Street, this area has some very old buildings that Boyd might recognize if he were alive today. A stretch of buildings on Broadway look almost untouched from the early 19th century (you can tell by the lintels).
As I walk up and down these streets I always wonder if there was any business here he would have visited. And that always takes my mind to Arnold’s Bar & Grill. It’s at 210 8th Street East. It has been in operation since 1861. The buildings that make up Arnold’s date back to the 1830s and were a feed store and barbershop (and whorehouse).
Boyd most certainly would have walked by Arnold’s. It was only a block or so from his factory. But would he have been allowed in at the time? Unlikely. (Today Arnold’s is an inclusive gathering spot for people of all stripes and colors. We’ve had many beers there.)
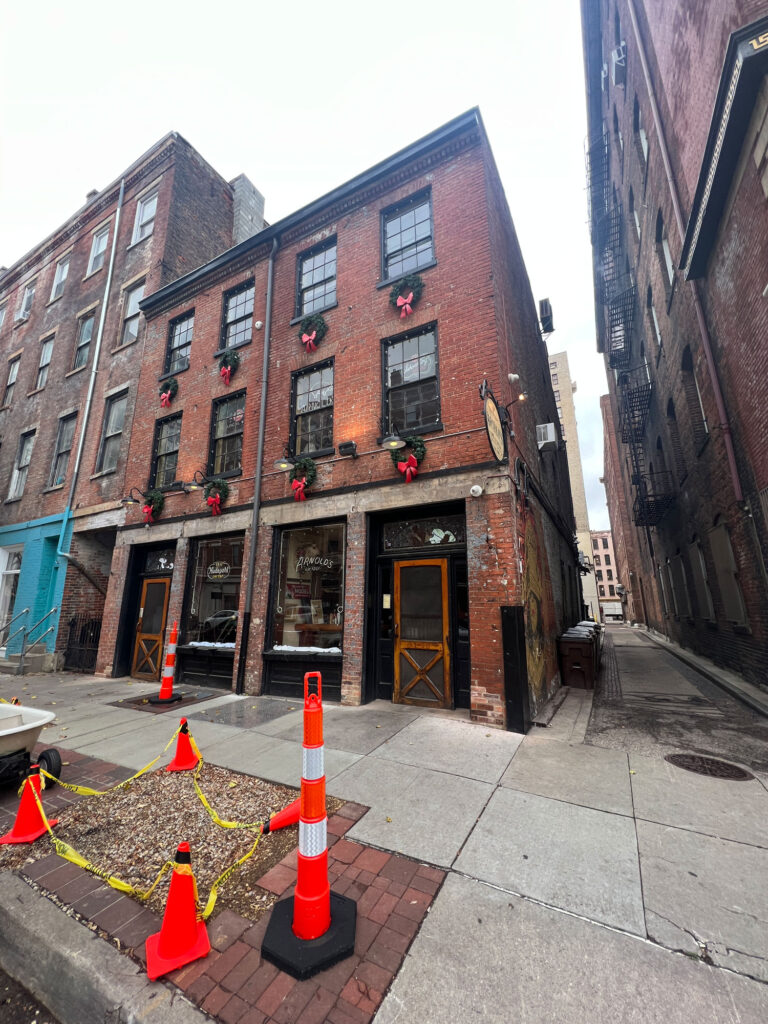
Most of Boyd’s neighborhood has been demolished to make way for an interstate, a casino and far too many surface parking lots that are virtually unused.
But I do take heart at times as I walk back to Covington and tread over Cincinnati’s public landing on the Ohio River. This area on the riverfront looks barren at times, but it has been the heart of the city’s riverfront since at least 1825. Boyd was here looking for work when he arrived as a free man in the city. And almost every day something still happens at the public landing. A steamboat arrives and disgorges passengers. A historic ship berths there for tours. The police launch a search for someone’s body. It’s an almost unchanged piece of flat land from the 19th century, sloping gently down into the Ohio River.
This is where Boyd began his life as a free man. And this is where I can close my eyes and really look for him.
— Christopher Schwarz
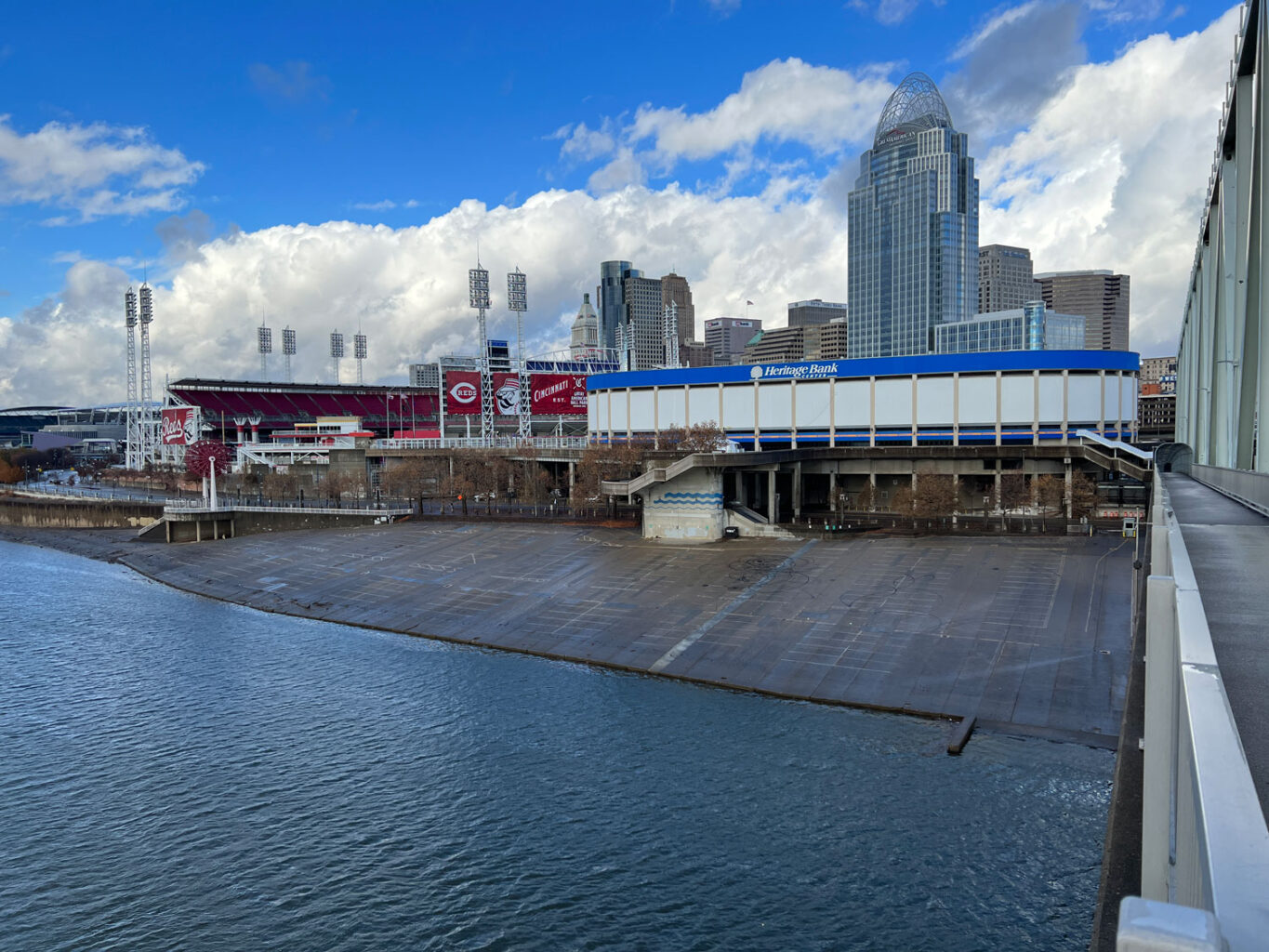