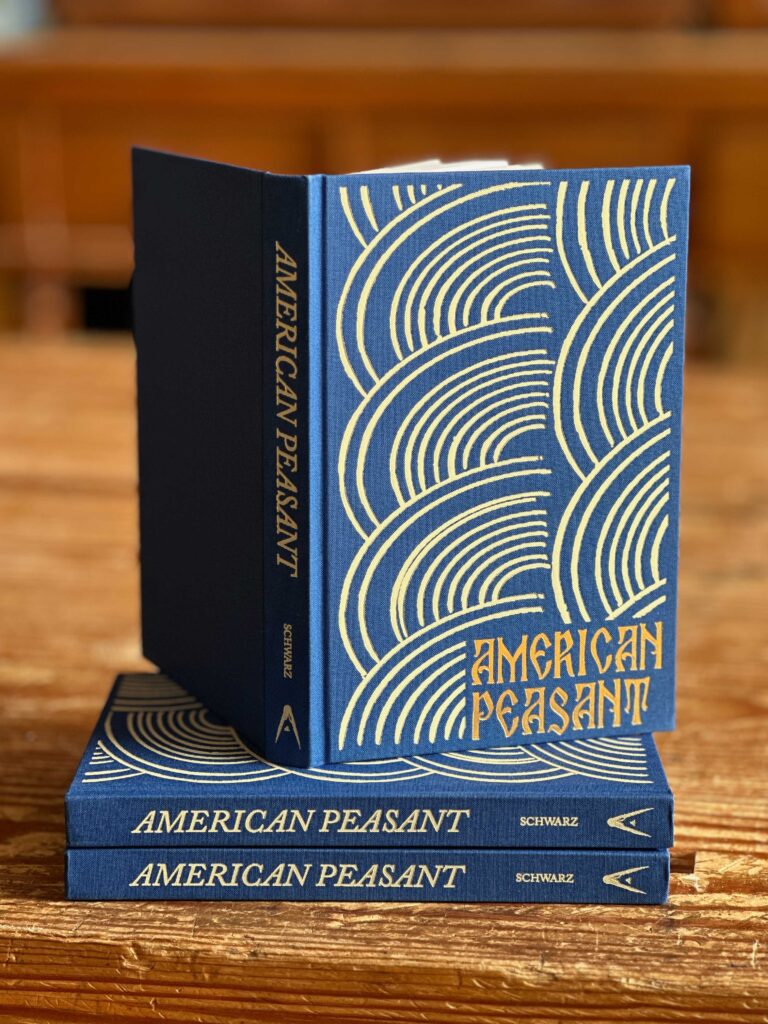
My latest book, “American Peasant,” is now shipping from our Covington warehouse. The price is $37 plus shipping. All copies purchased from us are autographed.
If you can’t afford the book, or aren’t sure it’s for you, the pdf of the complete book is free. You can download it by clicking this link. This is not a trap. You don’t have to register or give up your email. Just click this, and the pdf will download to your device. No strings attached.
The pdf is free now and for always. Tell your friends.
A quick note for those who bought merchandise to support our renovation of the Anthe Warehouse, your book is on the way. Check the bottom of this entry for details.
What’s the Book About?
“American Peasant” is an introduction to a style of peasant furniture and decoration that is almost unheard of in the Americas. Built primarily with tongues, grooves and pegs, the furniture is frequently engraved with geometric symbols that beautify the piece and protect its owner.
With this book, you will learn to build 10 simple pieces using common tools and whatever lumber is on hand. And you’ll learn to engrave the pieces using nothing more than a cheap craft knife and a vinyl flooring cutter. (We were so thrilled with this tool that we now make a commercial version of it.)
In addition to furniture making, “American Peasant” delves into other areas of the craft that will make you a more independent woodworker. Learn to make your own commercial-grade glue using only three ingredients (food-grade gelatin, salt and water), all of which you can find at the grocery store. The glue is strong, reversible and non-toxic (it’s edible, though we don’t recommend eating it).
You can make your own finish using beeswax, linseed oil and citrus solvent. This non-toxic finish is easy to apply and to repair. Plus, it looks better with age and use.
Finally, you’ll learn the language of the engravings, which come from Scandinavia, Eastern Europe and the U.K. These geometric engravings can protect a loved one from sickness, guard your valuables and grant good fortune to others (there are no negative engravings or spells in this book).
It’s the most beautiful book I have written, designed and printed. The cover is our first two-color diestamp, and the plant did a beautiful job of stamping it extra-deep so the cloth has a fantastic texture (“…with the look and feel of hand-tooled leather.”).I hope you enjoy it.
Anthe Supporters – Read This!
If you were one of the 445 people who purchased a special class, a spell panel, lump hammer or book that supported our effort to fix up our Covington warehouse, this section is for you.
Last month I sent out a couple emails to all of you. If you didn’t get one, check your junk folder. I have signed all your books, personalized them to you and they are shipping now (I labeled a bunch of them this morning). If you think or know you are entitled to a book but you haven’t received an email, don’t leave a comment here. Instead, reach out to help@lostartpress.com. They will help sort it out.
Customer service stuff aside, thank you – all of you. Your purchases raised about $120,000 that was beyond helpful.
And Hats!
We also have a batch of new hats in the store. These are navy blue with our dividers embroidered in white. These are unstructured, soft and have a metal clasp to adjust them. We got a special deal on them and were able to lower the price by $5.