English oak coffer; 16th century. (Image from Wiki Commons, public domain.)
The once ubiquitous coffer (from the Greek “kophinos” – a basket; later from the French “coffre” – a chest) was also referred to as a “strong box” – because it was. (Later the term coffer would refer to an institution’s financial reserves.) This stout, often highly ornamented, chest reached its pinnacle of design and construction in the mid 1600s and was likely the first, and perhaps the only, piece of furniture that a commoner family might own. Likely used every day as a bench, its primary purpose was to keep the family’s valuables safe and private. Its thick oak walls and lid could often even keep its contents safe from a fire.
Accurate drawing of a similar 17th century English chest (by John Hurrell, published in 1903).
For George Walker and me, what is truly fascinating about these coffers is that they clearly demonstrate the traditional, artisan design process we have described in excruciating detail in “By Hand and Eye” (and decidedly less excruciatingly in “By Hound and Eye”).
For those unfamiliar with this process, here it is in a nutshell: Unlike modern builders who think primarily in terms of measurements to an external standard such as inches or centimeters, pre-industrial artisans took their cues from the builders of antiquity and thought more in terms of proportions. They would start by selecting a simple rectangle of harmonic proportions (literally from the audible harmonic musical scale) to govern the overall form. For example, the front elevation of height-to-length were commonly ratioed at 1:2 (an octave); 2:3 (a perfect fifth); 3:4 (a perfect fourth) or 3:5 (a perfect sixth). Within this rectangle they would select the span of some prominent element of the structure to act as a module (an internal index measurement often based on a element of the human body) and then tie all the other details proportionally to it.
The coffer is a perfect example of this ancient design process: a straightforward layout based on the geometry of a cuboid defined by simple whole number ratios of height, width and depth. Like the proportions embedded in the design of Grecian columns (which deeply influenced the design methodology of the joiners and cabinetmakers of the 17th and 18th centuries) the designer of this coffer clearly used the width of the chest’s leg in the front elevation as the “module” for the design. (The Greeks used the diameter of the base of a support column’s shaft, which happens to be the span of the human body, as the module for all the other elements of the temple.) We encourage you to print out the above drawing by Hurrell, take a sharp pair of dividers, set it to span the width of the leg (we label it “M”) and go exploring with us:
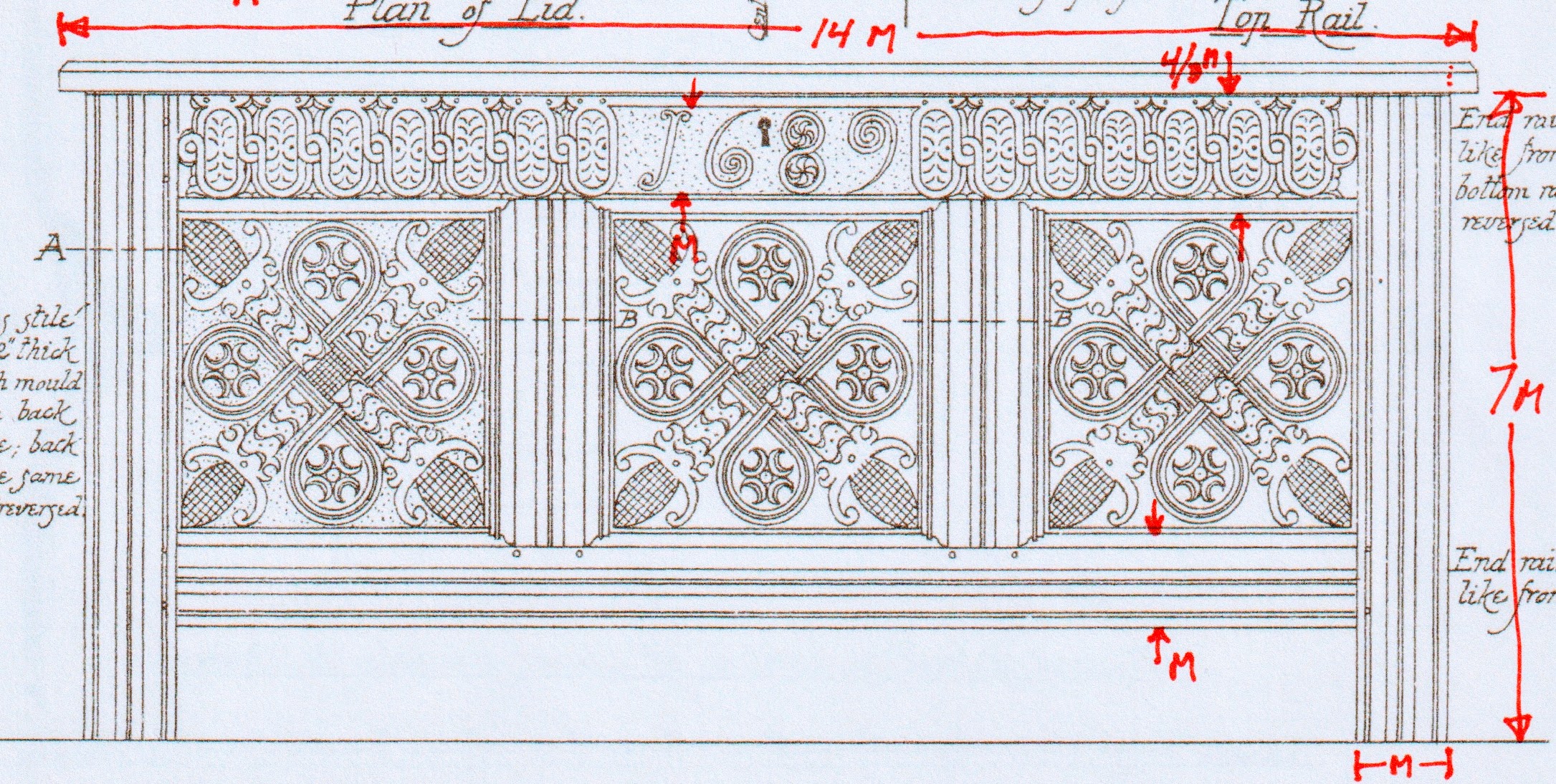
The first thing we’ll discover is that the height of the leg (to the underside of the lid) is exactly seven times its width (again, the module for this design). By eye, it looks like the length of the chest may be twice its height. When we step the module between the outside of the legs, however, we don’t come up with that nice whole-number ratio. On our second shot at it, we discover the lid from edge to edge is a precise 14 modules long. So there’s our 7:14 ratio – or to simplify 1:2. Which is a perfect octave harmonic, and a common choice for the coffers of this era (and later for highboys in their vertical extension).
Further exploration reveals that the mid-stiles and bottom rail are also a module wide, as is the height of the carved inscription of the date 1689. If you continue poking around, you’ll unearth all manner of modular-indexed relationships buried in the intricate geometric carvings. Be aware that the spans and radii, if not exactly a module-length, will be a whole number fraction above or below that length. For example, the module (plus a third of the module) serves as the spacing for the positioning of the lower rail from the baseline as well as the width of the top rail.
As in the ancient temples of Greece, every single element of this coffer enjoys a whole-number relationship with each other – and with the overall geometric form. As such, you can scale this piece of furniture up or down by simple changing the span of the module – no measuring to numerical dimensions is necessary – just an adherence to the ratios.
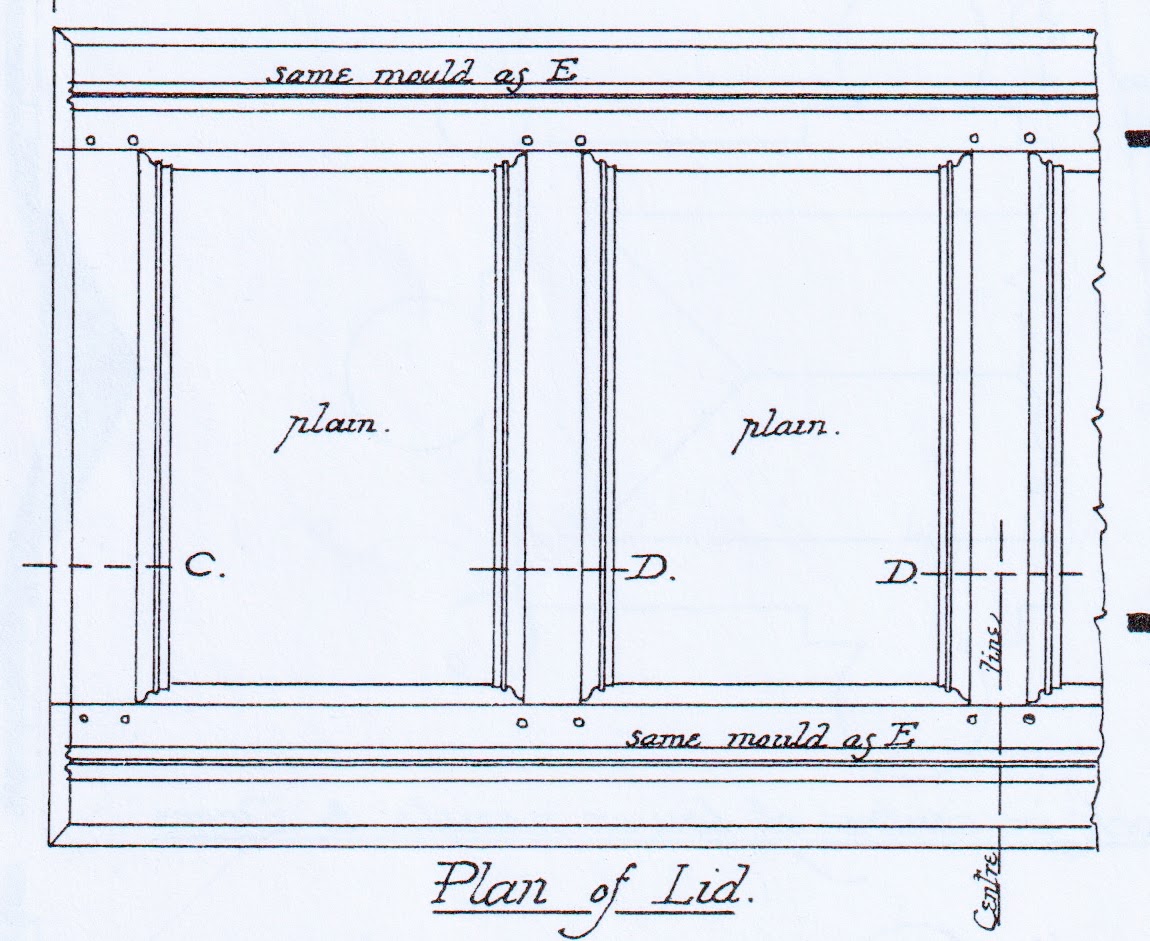
Now let’s explore the design of this coffer’s frame-and-panel lid. We were excited to discover how some anonymous 17th-century artisan made clever use of the module to add subtle, eye-pleasing asymmetry to the layout. Before you see how they did it (below), try to discover it for yourself. We find this sort of thing fun, and we bet you will too.
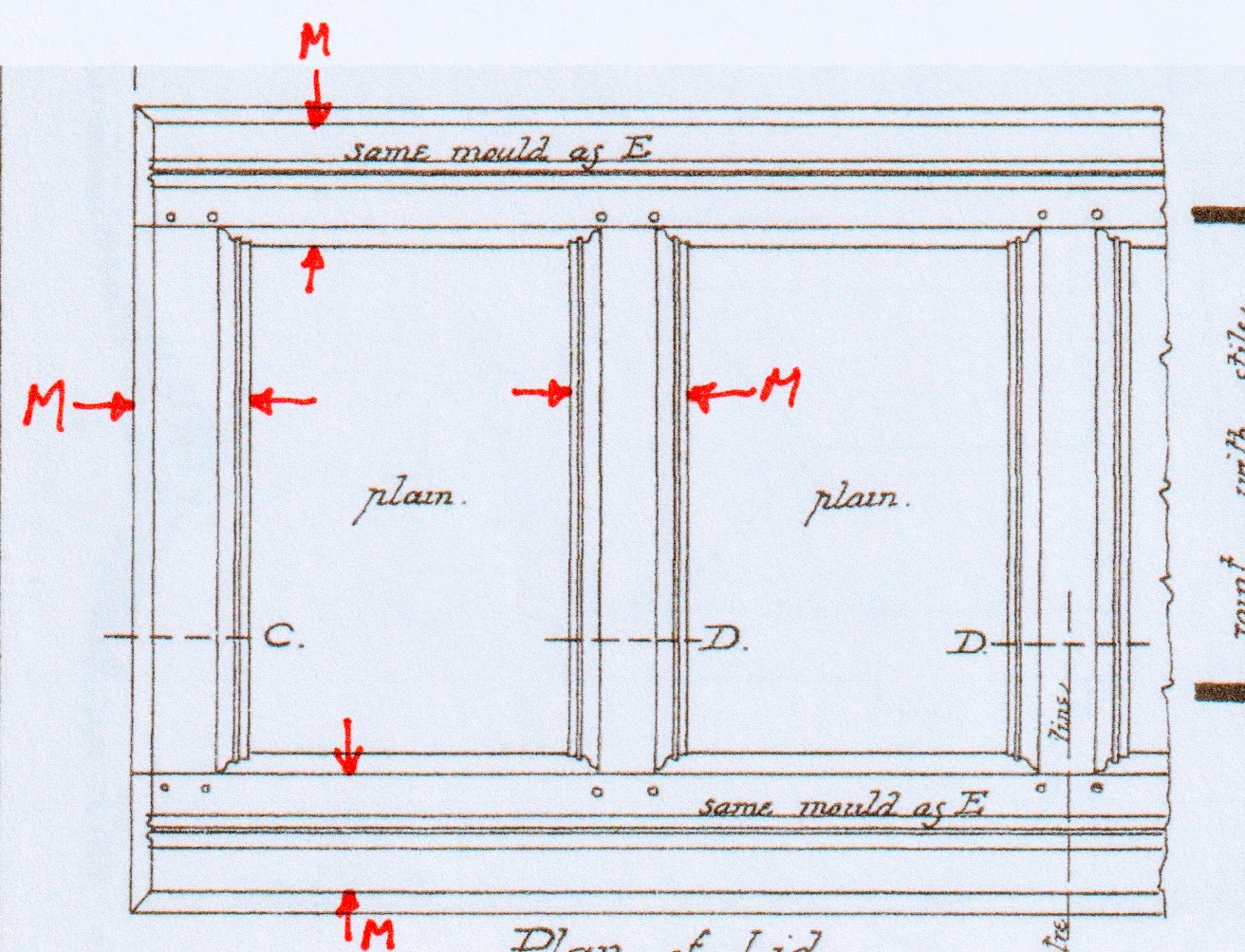
So here’s what we found: The module is utilized in four different ways: For the middle frames, it defines its overall width; for the hinge-side frame it defines its width, but it does not include the lid edging; for the end frame it does include the edging; and for the latch-side frame the module defines its width from the inside of the edging to the edge of the bevel next to the panel. Subtle, but just enough to make the design lively to the eye.
For your further entertainment, below are a couple more of Hurrell’s drawings of 17th-century English coffers for you to print out and explore. To see what we unpacked with our dividers, check out our blog at www.byhandandeye.com. One hint/reminder: The module for each of these designs is the width of the leg.
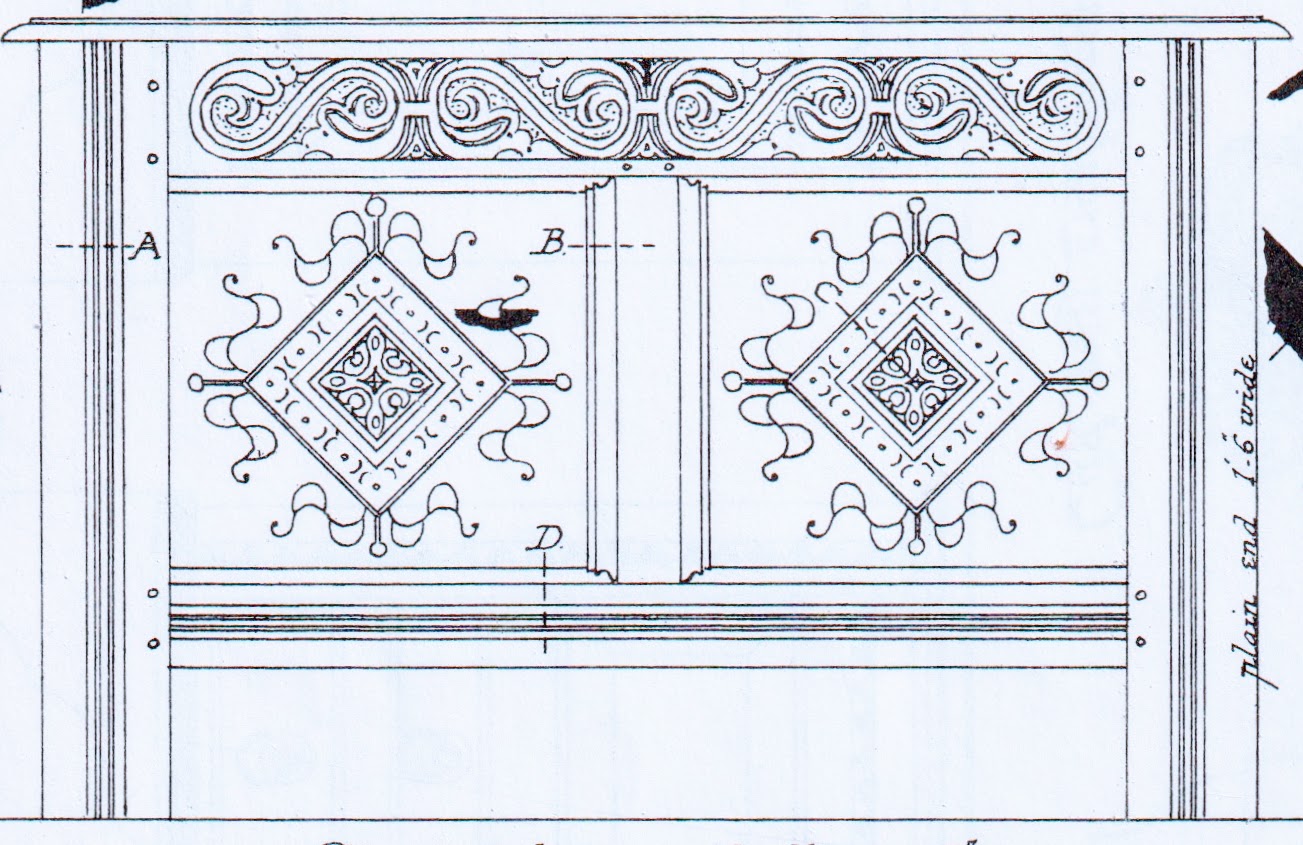
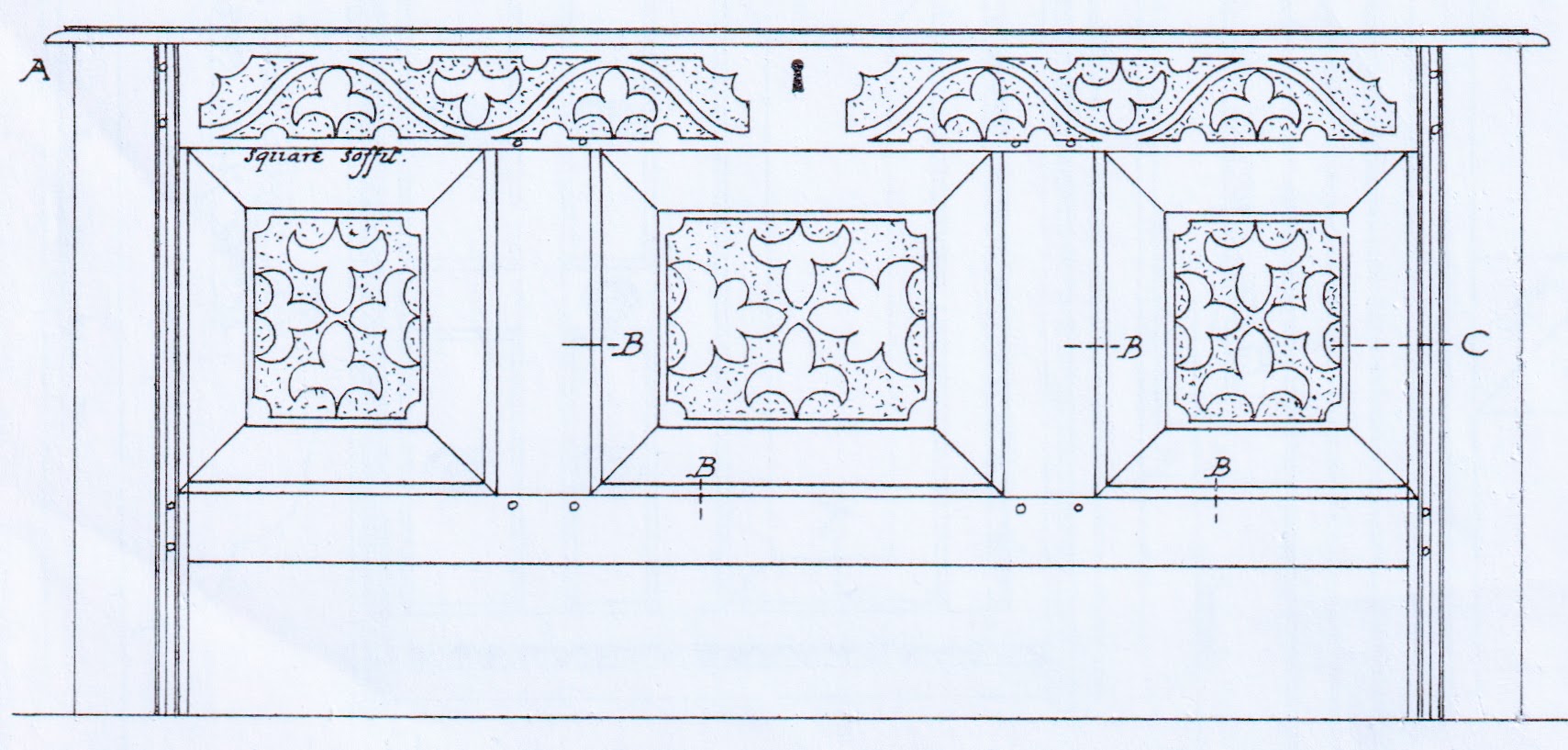
To learn more about the construction and carved ornamentation of these traditional coffers (also called a “joined chest” in America), you can do no better than to watch Peter Follensbee’s video “Joined Chest” available from Lie-Nielsen here or to read “The Artisan of Ipswich” by Robert Tarule, available from John Hopkins University Press here.
— Jim Tolpin
Like this:
Like Loading...