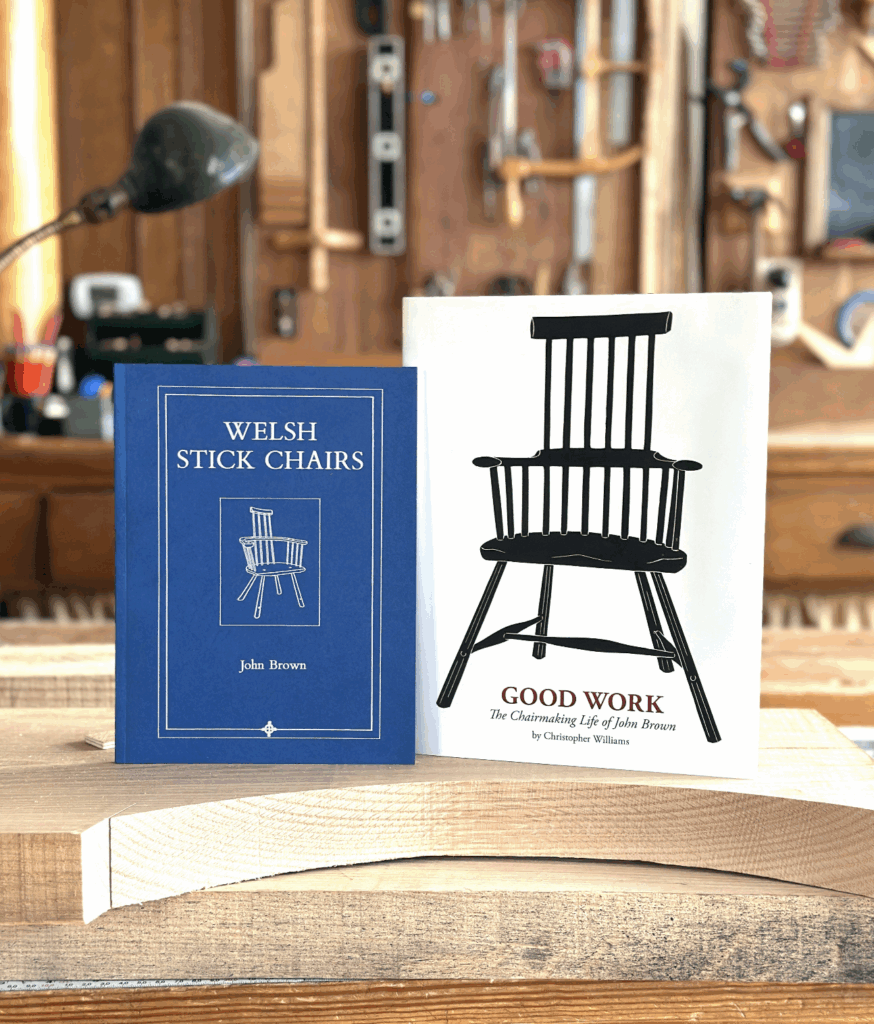
Get two classic chairmaking books – “Welsh Stick Chairs” and “Good Work” – for one special price. Together, they’re just $ 49 – but only through August 7. The regular price for both is $87 – you save 44 percent.
If you’re wondering where stick chairs came from, these two books will tell you the whole amazing story – and get you started in building them.
Stick chairs have been around for centuries – but they’ve mostly been ignored by museums. In the 1990s, Welshman John Brown wrote and published the landmark book “Welsh Stick Chairs.” This book inspired hundreds of people all over the world to begin researching and making these vernacular chairs.
One of those people who was inspired by “Welsh Stick Chairs” was Welshman Chris Williams. He worked with John Brown for more than a decade making these chairs. Through the years, John Brown’s chairs became more wild and true to the old Welsh character, and Chris was there the whole time.
After John Brown died, Chris wrote the book “Good Work” about his mentor. This biography explores John Brown’s creative genius and his tumultuous character. And it explains how John and Chris built these chairs almost entirely by hand.
There is no better place to learn about the spirit of these chairs and how they were made than with these two books. So we are offering them at a special price until August 7.
Technical Details
“Welsh Stick Chairs”: Using first-edition examples of “Welsh Stick Chairs,” we reset the entire book in the original font to ensure the text was crisp. We rescanned and processed the photos and drawings and cleaned them up. And we spent weeks researching the paper stock of the original to capture the same earthiness and perfection of the first edition. We also made a small but invisible improvement – we sewed the signatures together to ensure the book will last for lifetimes. The book is a softcover, covered in heavy card stock like the original. The book measures 7-1/4″ x 9-5/8″. Our version includes John Brown’s original introduction to the book, plus the additional introduction he wrote for the third edition and an updated essay on John Brown by Nick Gibbs.
“Good Work”: The 208-page full-color book is also filled with historical photographs (many never published before) and beautiful linocut illustrations by Molly Brown, one of JB’s daughters. The book is printed on heavy coated paper with a matte finish to make it easy to read. The book’s pages are sewn, glued and taped – then covered in heavy boards and cotton cloth – to create a book that will last for generations. And the whole package is wrapped in a durable tear-resistant laminated dust jacket, which features linocut illustrations by Molly Brown.
Both books are produced and printed in the United States.