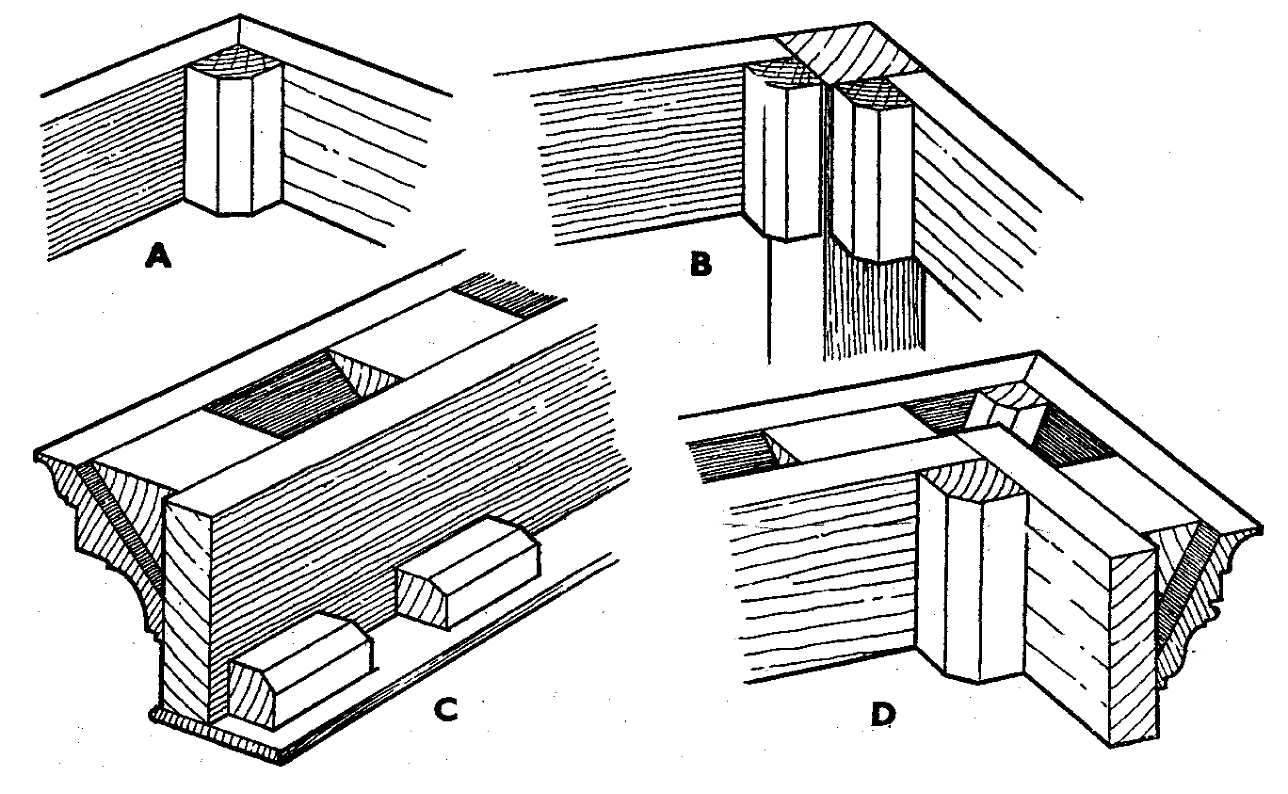
The following is excerpted from “The Woodworker: The Charles H. Hayward Years,” Vol. II – Techniques. This article was first published when “glue” was understood to be hot hide glue (or, as it’s called in The Woodworker, Scotch glue). Rub joints work with other glues, but in my experience, not nearly as quickly – hot hide glue has incredibly fast tack. I’ve used glue blocks on several pieces, and for them, I always heat up a little hot hide glue. It’s well worth the (minor) trouble.
– Fitz
Like most other things, glue blocking has its abuses as well as its uses. A typical example is when it is used to replace a properly cut joint in cheap work. If confined to its correct function, however, that of strengthening a joint, it can add very materially to the strength, and is a perfectly legitimate practice.
From the outset we should be clear that the glue block is a rather ugly thing to look upon. It is therefore suitable only for positions where it is not seen, for it does its work chiefly by virtue of its bulk and the extra gluing surface which it provides, and it necessarily leaves a smear of glue at each side (we shall see the reason for this presently). In concealed positions, however, it can increase the strength of a joint very considerably.
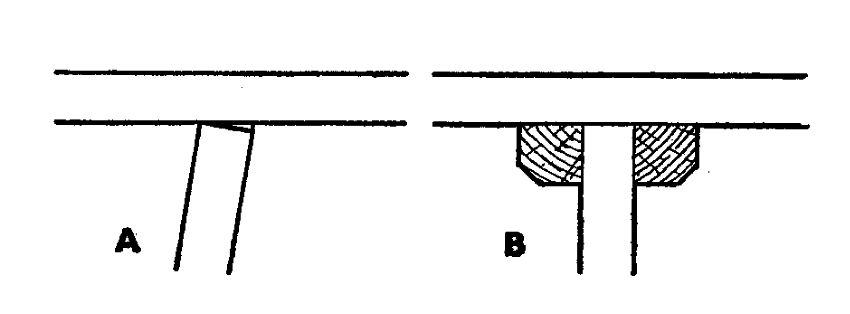
This shows how the blocks help to resist lateral movement by acting as angle struts. They also considerably increase the gluing area
As a simple example of its use take the T joint at A, Fig. 1. If the vertical member is subjected to much side pressure it is clear that, apart from the glue with which it is assembled, it has only the resistance of the wood in the joint to prevent movement. If the wood crushes or breaks, the member will give. At B, however, the glue blocks by their bulk offer considerable resistance, and in addition they have mechanical strength in that increased leverage is required to shift the joint. They are virtually like a short stay inserted at each side.
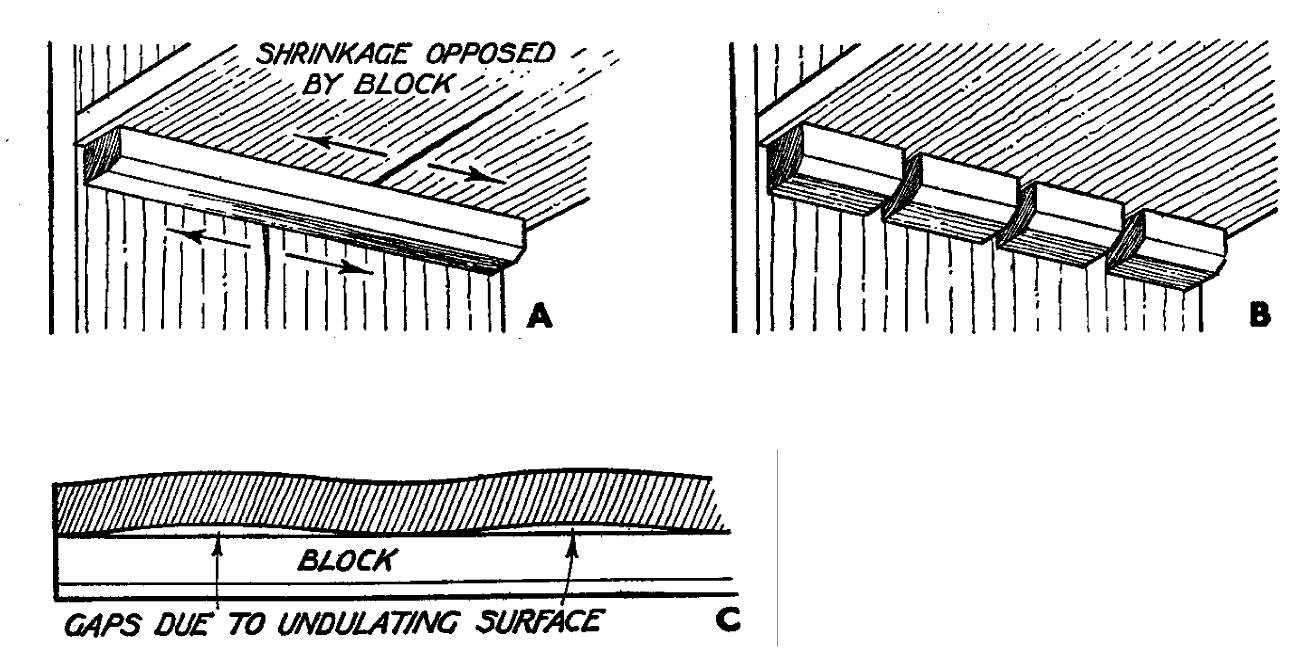
To be fully effective, a glue block should be comparatively short—say an average of about 3 in. One reason is shown at A and B, Fig. 2. At A there is one long block running the whole length of the joint, and its grain runs across that of the pieces that it joins. Consequently the block resists movement in the event of shrinkage, and a split is almost inevitable. If, however, there are several short blocks close together, as at B, the wood is free to contract without resistance from the blocks.
Of course, when the grain of all the parts runs in the same direction there is not so great an objection to the use of long blocks, but, even then, short blocks are generally stronger for another reason. If the wood that is being joined undulates slightly, as at C, Fig. 2, it is inevitable that there will be gaps in places with loss of strength. Clearly, short blocks would conform much more closely to the uneven surface.
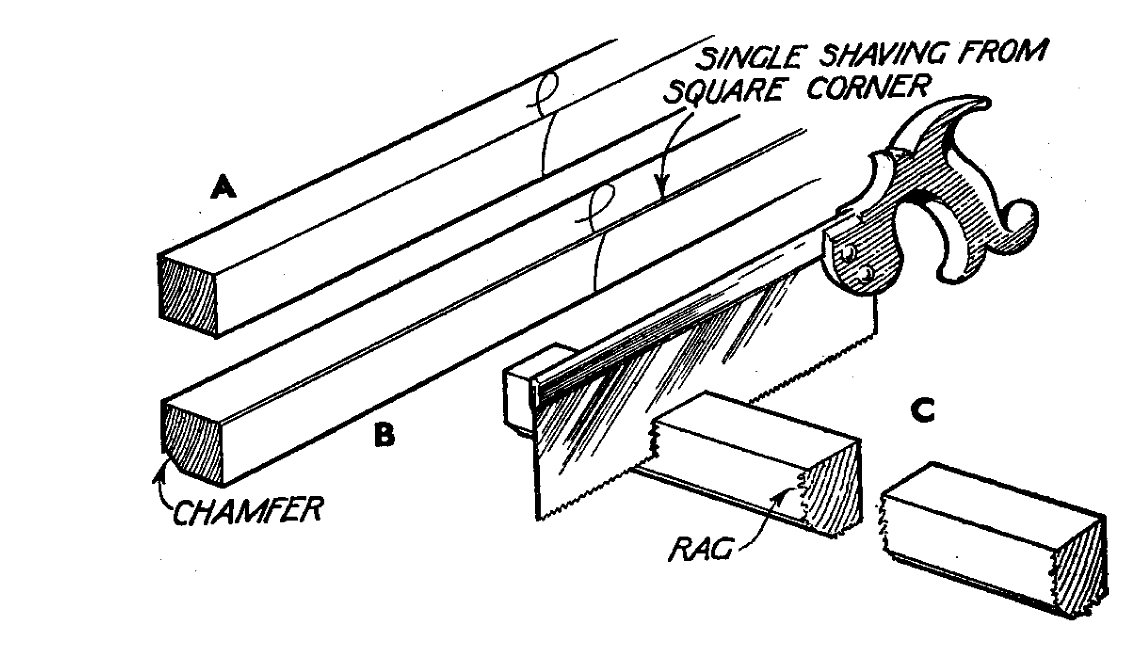
Preparation of blocks. The wood should be prepared in a length and cross-cut. Plane the first edge straight, and then make the other square with it, as at A, Fig. 3. Plane the remaining two surfaces (it does not matter if these are not exactly square), chamfer the outer corner, as at B, and take a single shaving from off the inner corner. There are two reasons for the large bevel. It lightens the block and takes off what is otherwise a heavy appearance; and it makes it obvious to the man who uses the block which is the square corner. The purpose of the single shaving from the latter is that sometimes a bead of glue is left in the corner into which the block is rubbed, and the removal of the corner enables the block to clear this.
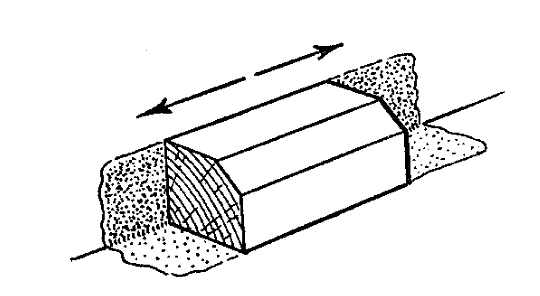
When cross-cutting the blocks keep the square corner pointing toward you, as at C, Fig. 3. In this way the saw always cuts into both square surfaces. Any rag occurs at the outer surfaces where it does no harm.
Gluing the Blocks. When gluing a block, glue the two square surfaces and rub the block back and forth in the angle a few times, as in Fig. 4. A few examples of the positions in which glue blocks are useful are given in Fig. 5 [at top].