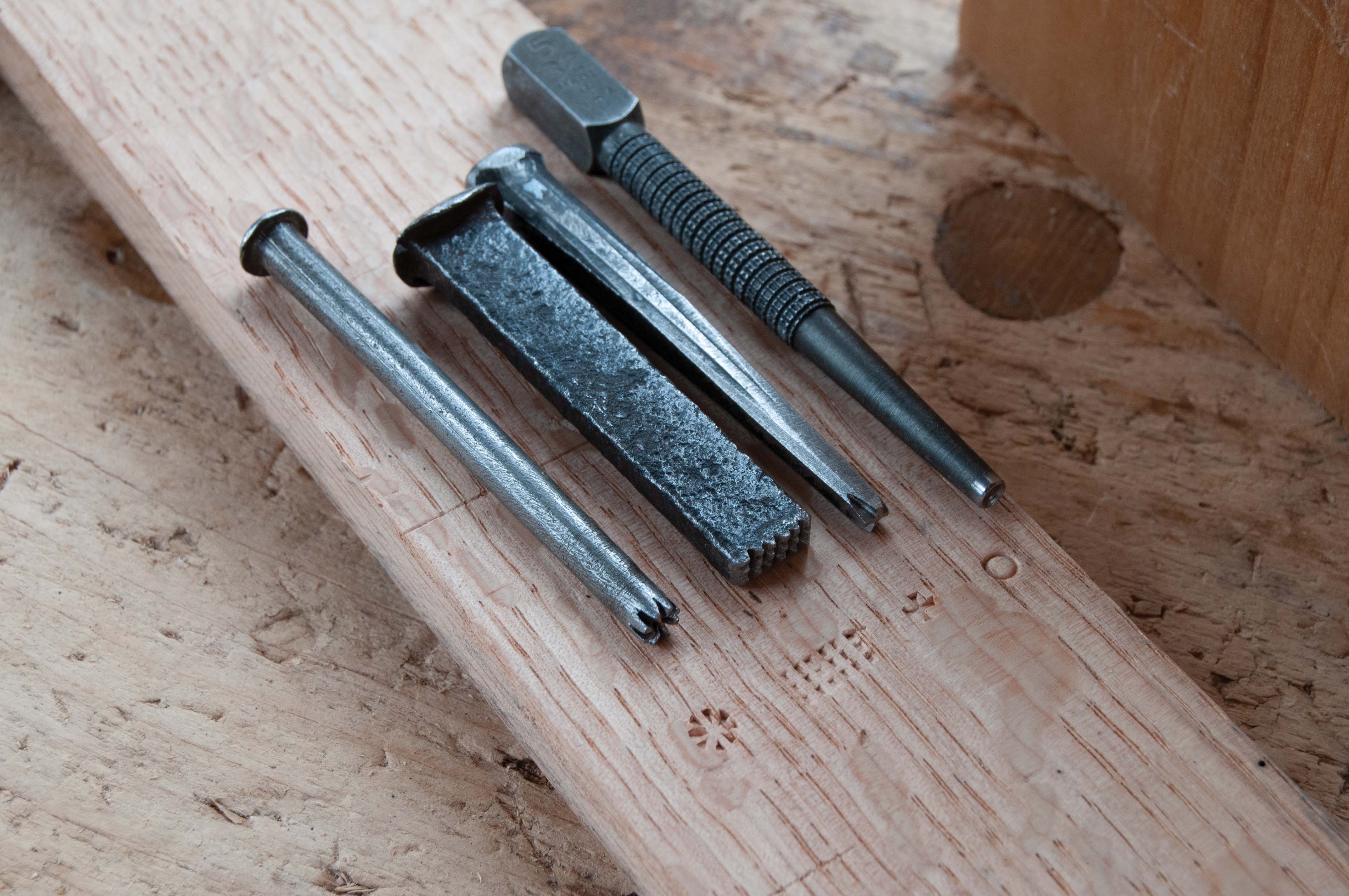
The following is excerpted from “Joiner’s Work,” by Peter Follansbee – in effect a doctoral thesis on processing furniture-shaped chunks of lumber from the tree using and axe, froe, hatchet and brake. Follansbee dives into deep detail on how he festoons his pieces with carvings that appear complex but are remarkably straightforward – plus lessons in 17th-century casework. His approach to the work, which is based on examining original pieces and endless shop experimentation, is a liberating and honest foil to the world of micrometers and precision routing.
The book features six projects, starting with a simple box with a hinged lid. Follansbee then shows how to add a drawer to the box, then a slanted lid for writing. He then plunges into the world of joined chests and their many variations, including those with a paneled lid and those with drawers below. And he finishes up with a fantastic little bookstand.
Punched accents often enhance carved decoration throughout the design. These punches are sometimes just a textured effect, often called “stippling,” in the background, or extended to include stars, crosses, floral patterns and other designs stamped onto the solid foreground of the carvings.
Here’s my main set of punches (Fig. 3.41). From right to left, a 5/32″ nail set, a Maltese cross filed from a large cut nail, a background punch, and a small flower design. All but the nail set are shop-made.
Working metal is one of my least-favorite shop tasks, but I can usually worry my way through making some punches. It only takes a few minutes. The stock is usually pretty soft; the hardest stuff I file is when I use an old cut nail. I have no hack saw, but one would be handy if you’re going to do much of this work. One place it would help would be trimming the length of something like the cut nails if their point is too small a cross-section for the intended design. Otherwise, a grinder of some sort, or some coarse filing brings the end down to a clean and finished blank.
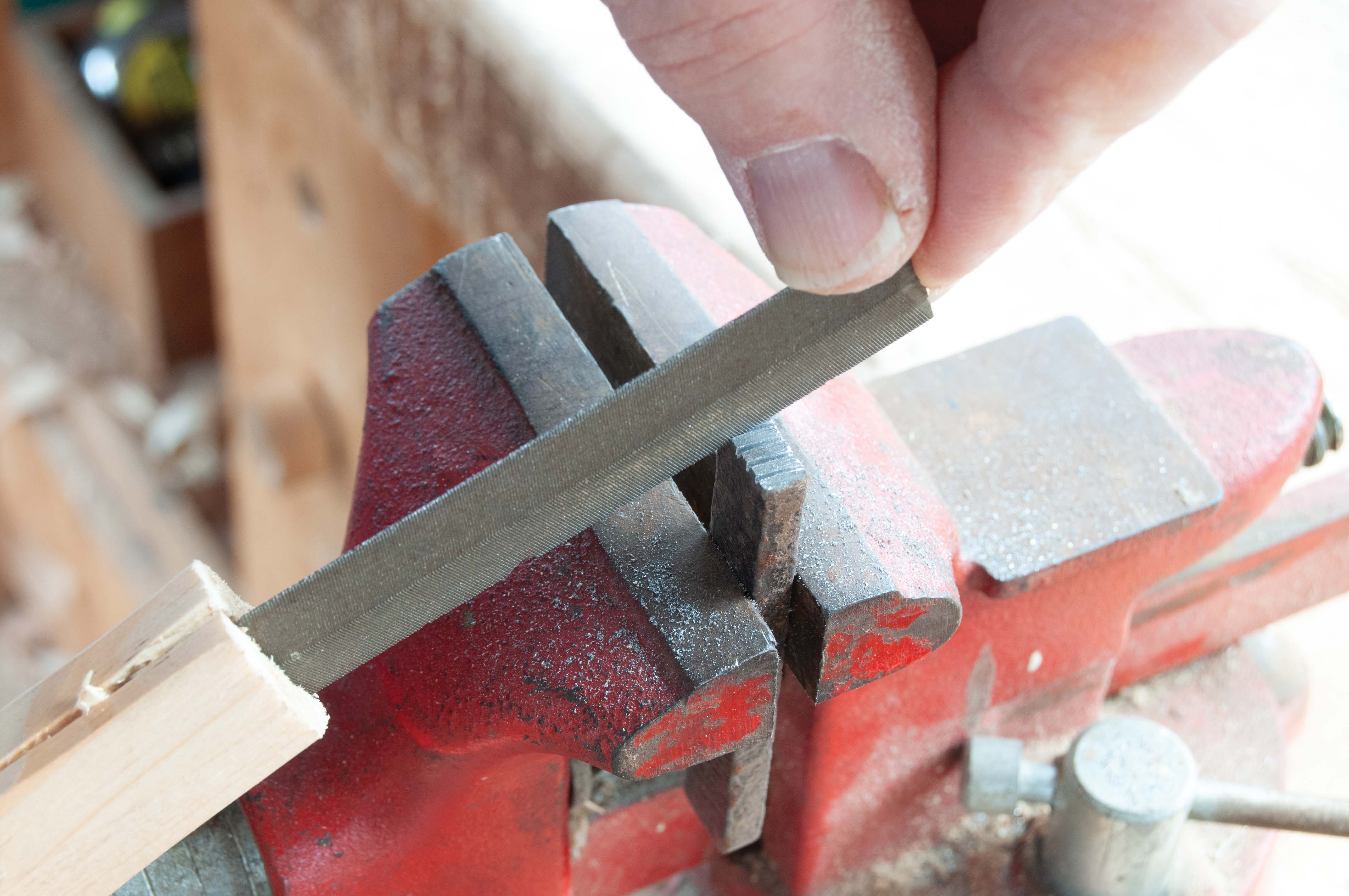
I start the background punch with a piece of stock about 1/4″ x 1/2″ x 3″ long. Make friends with a blacksmith; they have this stuff around. I file a row of lines dividing the punch across the wide dimension (Fig. 3.42). First in half, then half again etc. I use a feather-edge file to start these lines; you could use the hacksaw first.
I angle the feather-edge file by tilting the handle down to start this line. Then I gradually bring the handle up, lowering the file into the cut. I think of this as scoring the lines. I’ll finish them with a triangular file.
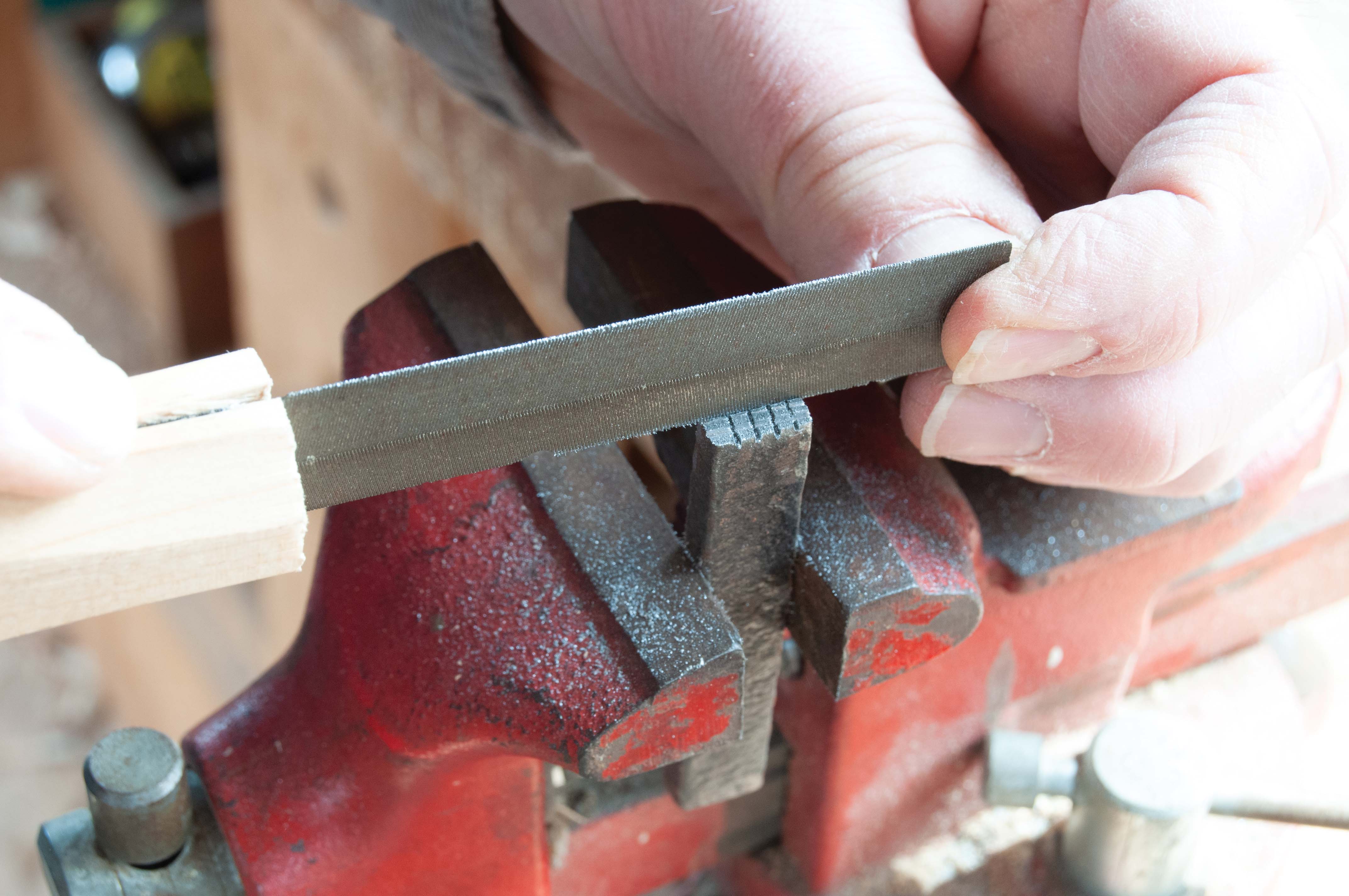
Then flip the piece in the vise, and file a couple of lines to define the other rows (Fig. 3.43). In this example, I filed two lines one way, and four the other, creating a punch with three rows of five teeth.
Don’t worry if your lines aren’t perfectly parallel. Get them close and then you’ll work on making things even out with the next filing.
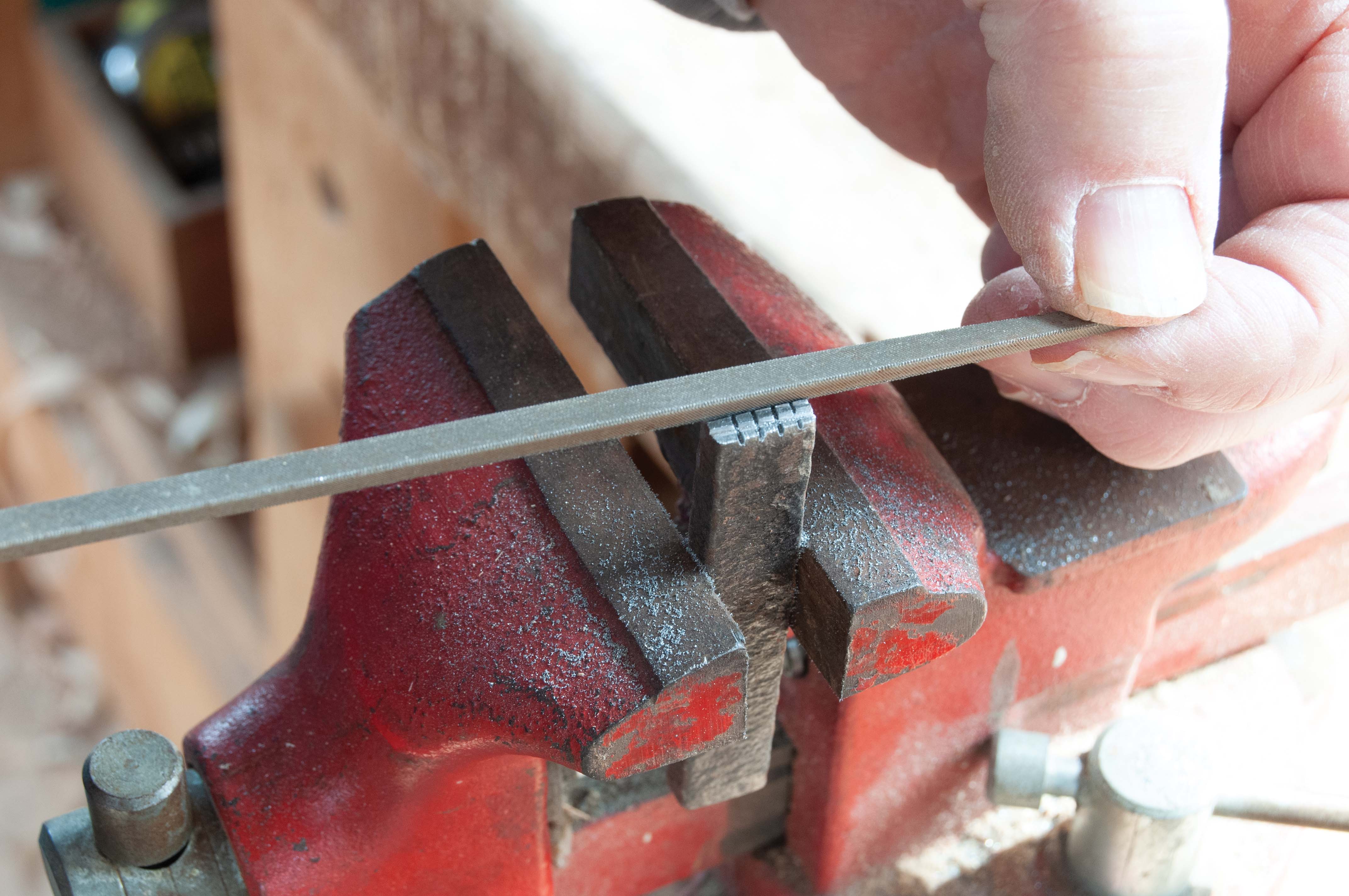
Once I’ve defined the layout with the feather-edge file, I switch to a triangular file to bring the teeth of the punch down to size (Fig. 3.44). Drop the triangular file into one of your slots you just made, and start to work it along. Check your progress frequently – things can change shape quickly. I find I have to tilt my point of view this way and that to catch the teeth in the right light. Aim for small “heads” to the punch’s teeth, evenly sized. Evenly spaced is good, but not as big a deal as size. If some teeth are too big, they won’t make as deep an impression.
The triangular file is easy to guide. Keep the top surface of the file level and the other two sides will be symmetrically aligned as they work mating sides of the row.
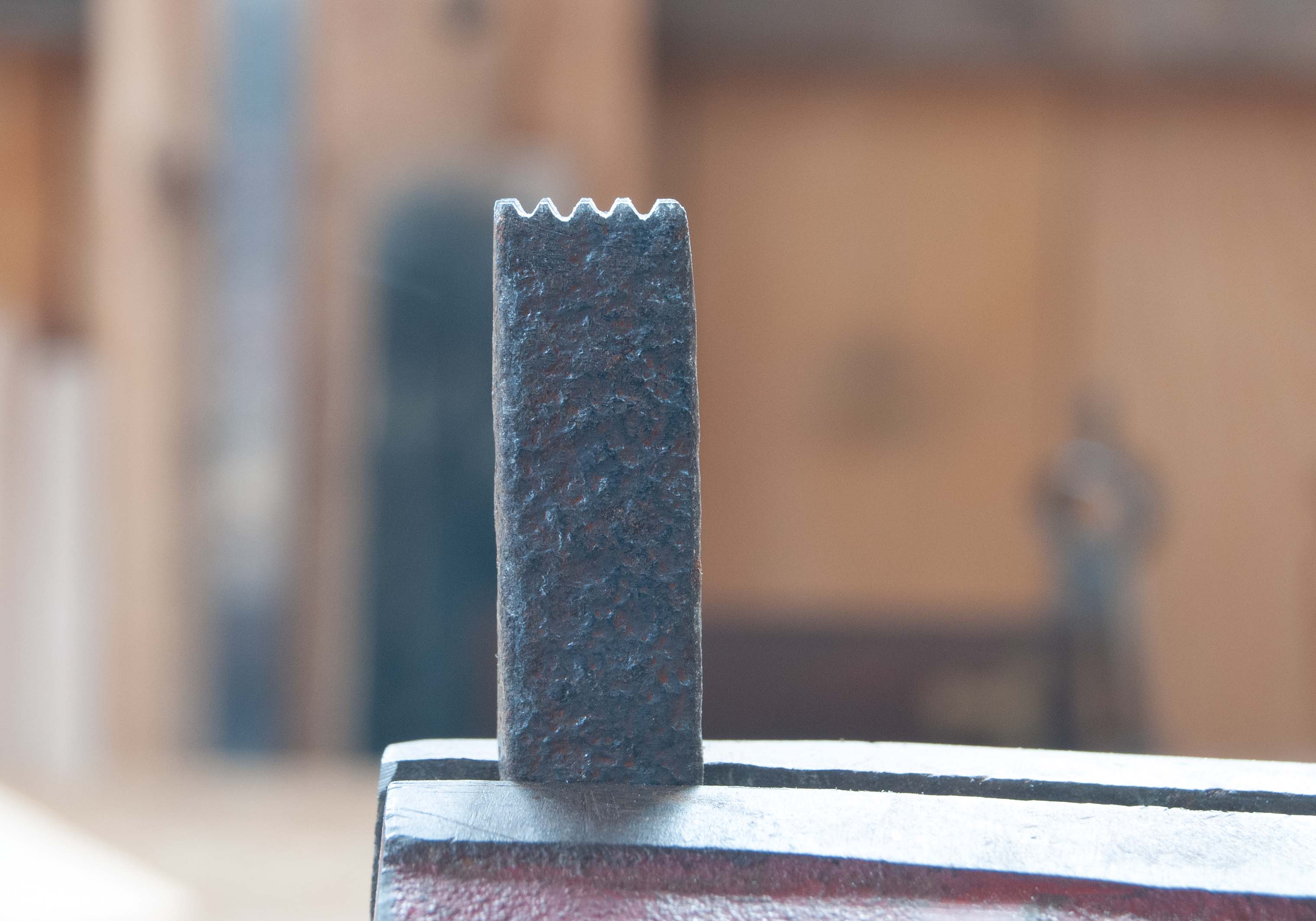
Variation in tooth size is expected, but teeth that are too big keep the punch from working well. The outer rows on this punch are both too big, especially the one on the right (Fig. 3.45). This is easy to fix. There wasn’t enough room to file another row, so I beveled off the outer corner of the punch, until I brought those teeth down to size.
Periodically take the punch from the vise and strike it in a piece of scrap wood. It’s good to be organized so you can keep track of your progress. I wish I were.
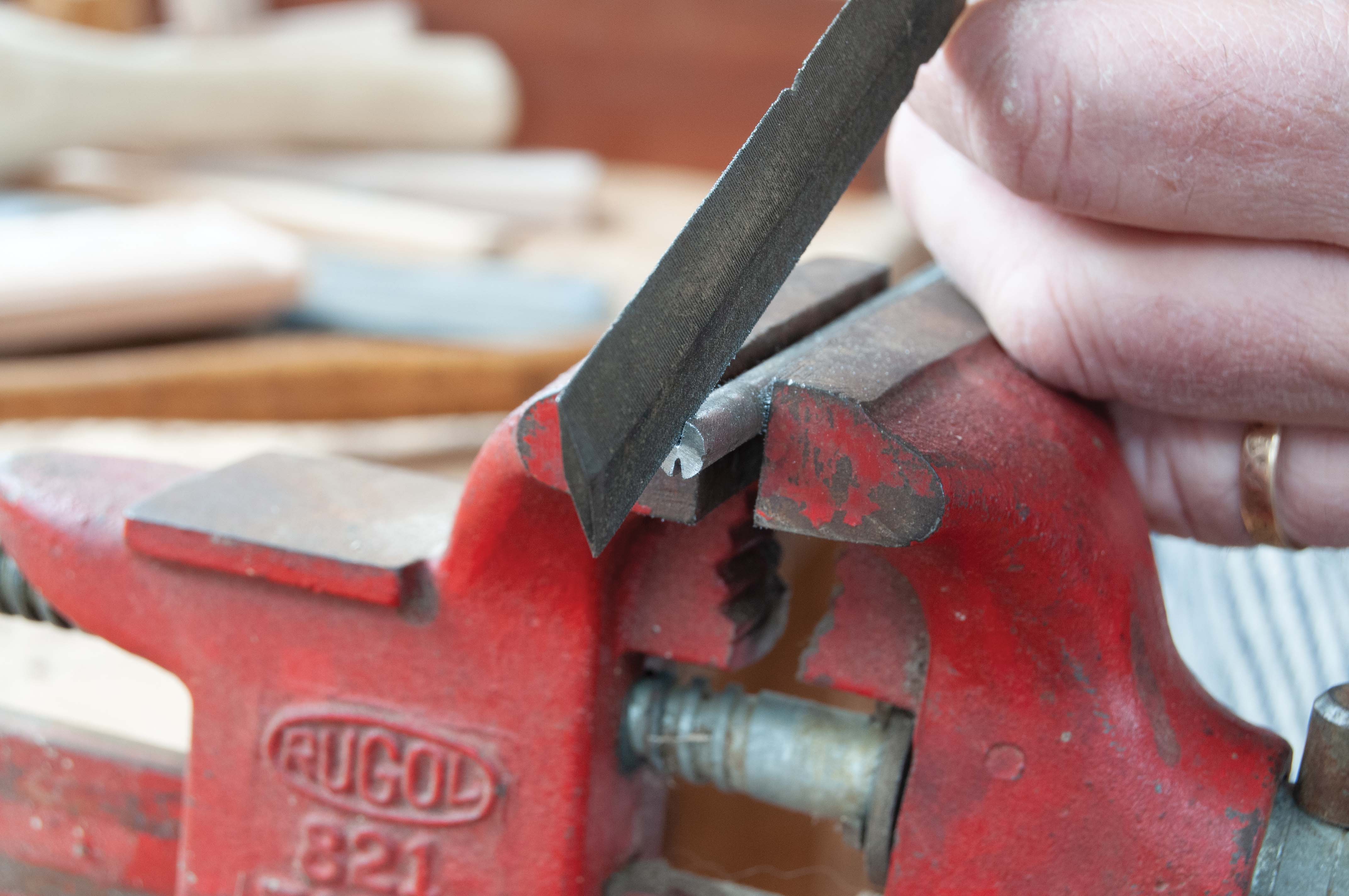
Make the accent punches in a similar manner. For the round flower punch I angle the feather-edge file so it’s just hitting at the corner of the punch’s end (Fig. 3.46). I file a notch from the outer edge to the middle, then turn the punch in the vise and file another notch across from the first.
Tilt the file to come across the end of the punch. Sometimes you have to then tilt your head so you can see where you’re going. File a little, look a lot.
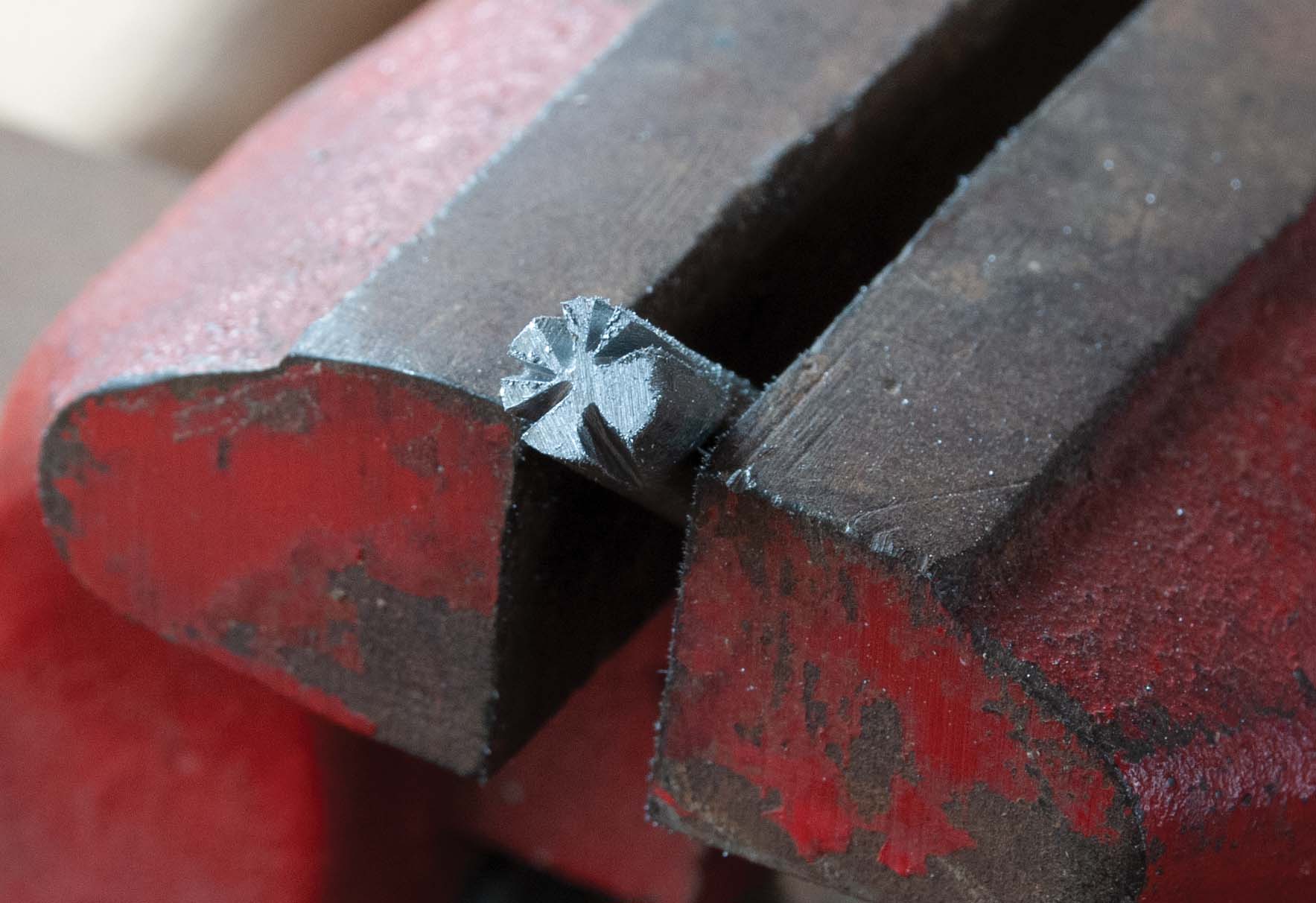
Keep splitting the spaces in half as best you can. If it gets off-kilter, split any thicker spaces in half again.
At this point, my pattern is out of whack (Fig. 3.47). What’s more important than symmetry is that the remaining “petals” are narrow. The wide parts in this view got filed to split them into smaller bits.
It’s surprising how small the remaining parts are to make the pattern work. It’s mostly negative spaces in the metal to create the impression in the wood.
Some find and use leather punches; I have no experience with them. If they are large enough they should work fine. If the business end of them is too fine, they might not make an actual impression in the wood. An easy way to see if a punch will work is to smack it on various pieces of scrap wood. Lightly on softer woods, harder on hard woods.
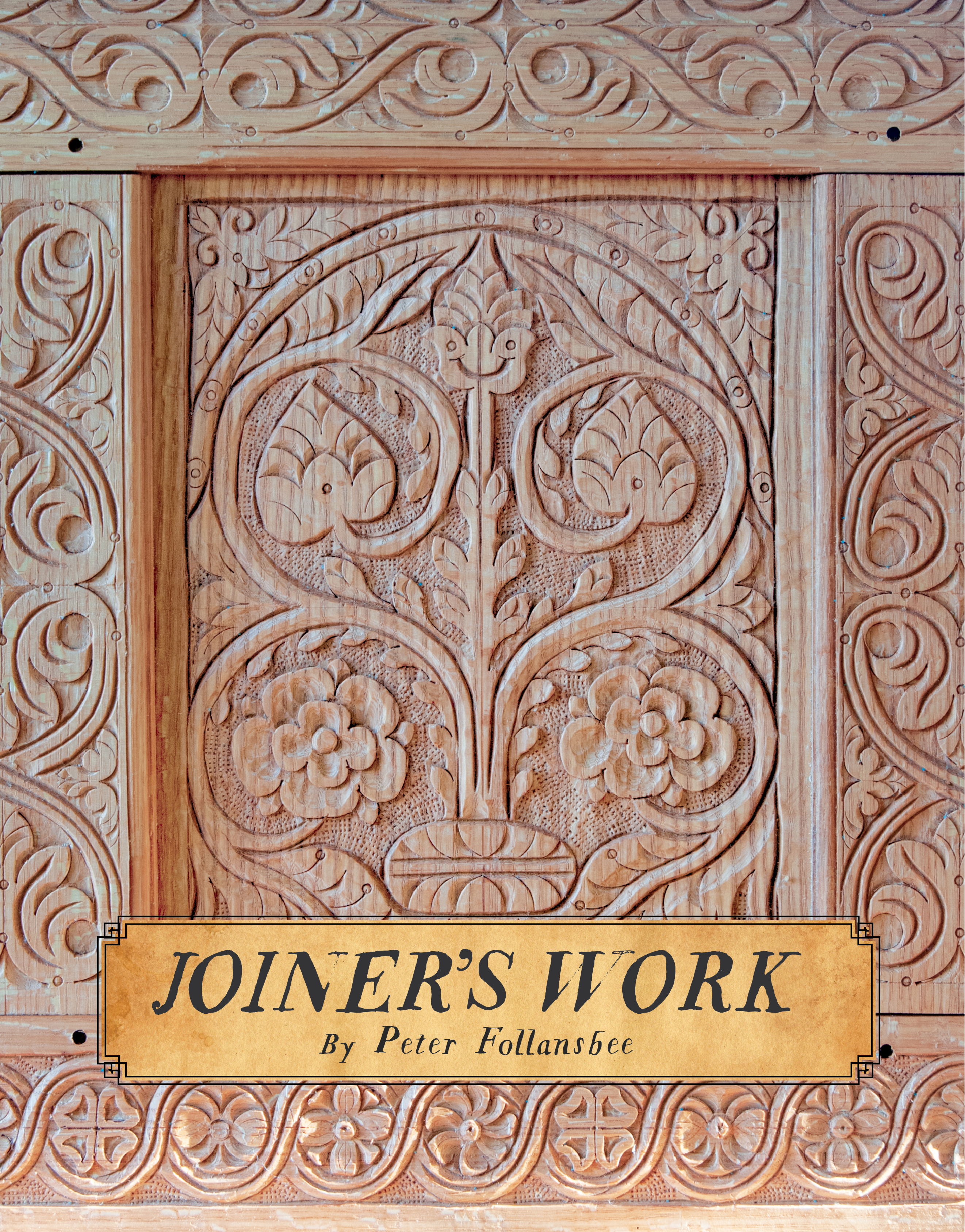