I found myself in need of a roughly cubical wooden frame the other day.
There are a lot of ways to fasten three sticks together to make a corner:
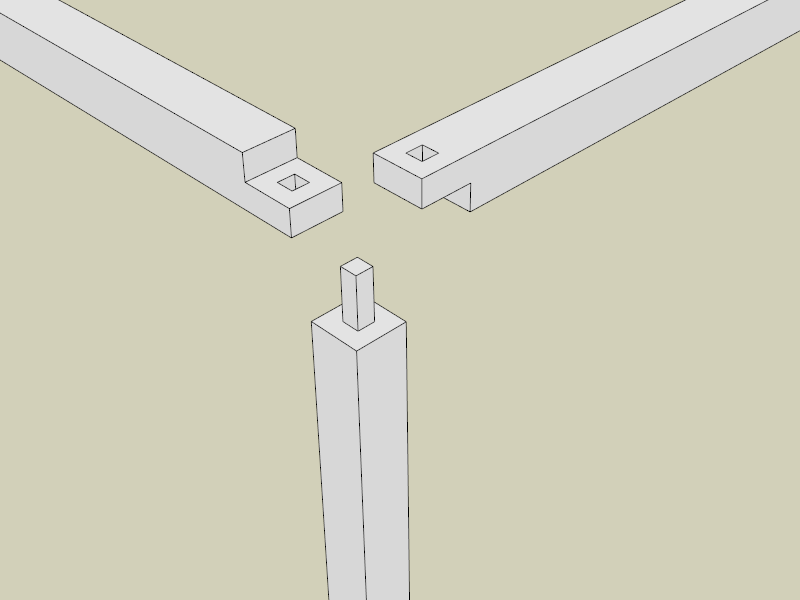
And in the end, I did end up using something like the above. But being the somewhat-obsessed-with-symmetry-and-patterns person that I am, I wondered if it would be possible to construct a corner joint where all three parts have exactly the same shape. The simplest “joint” of that kind is just three sticks:
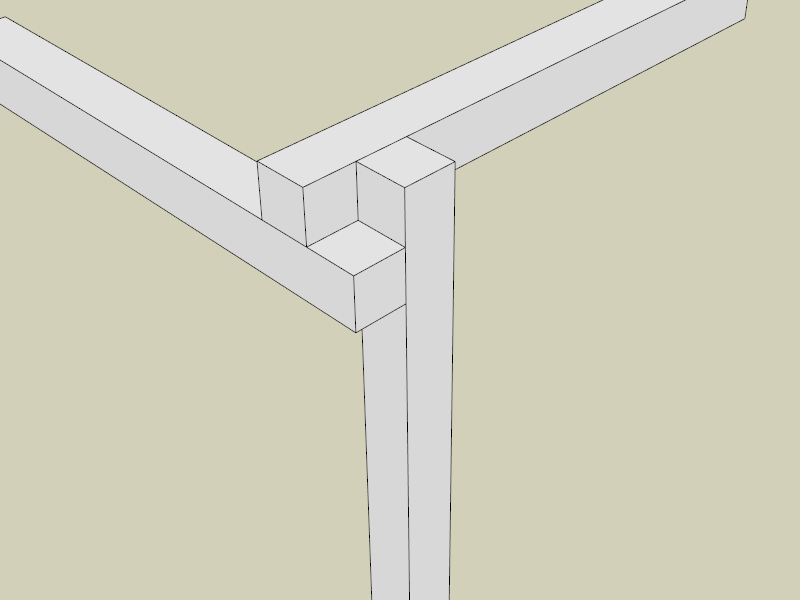
Obviously, this “joint” won’t stay together without help, but we’ll address that later on. In my case, I needed the frame to extend to the outside edges of the cube (so that I could fasten some sheet metal over the frame). That’s easy to do with this geometry; just widen the sticks and cut a notch for the joint:
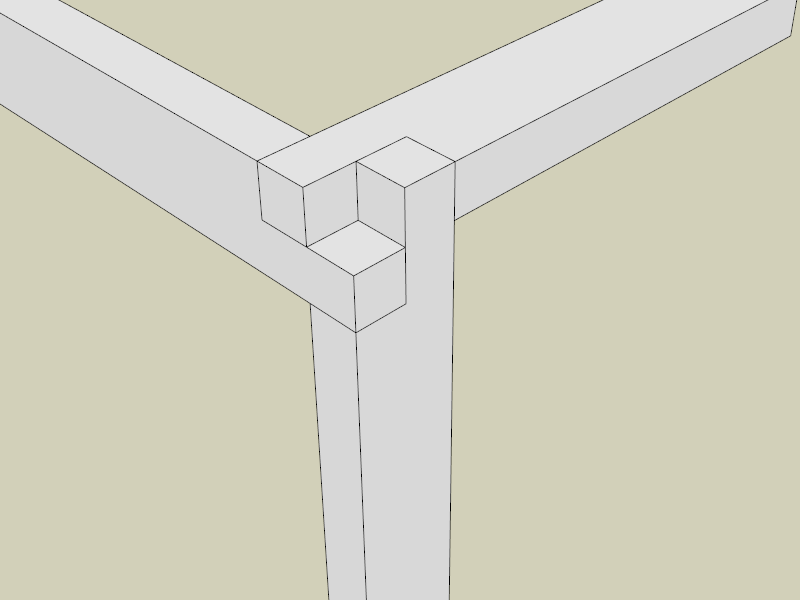
But there’s still that pesky empty cube in the corner. Is there a way to eliminate that without losing symmetry? It turns out that there is:
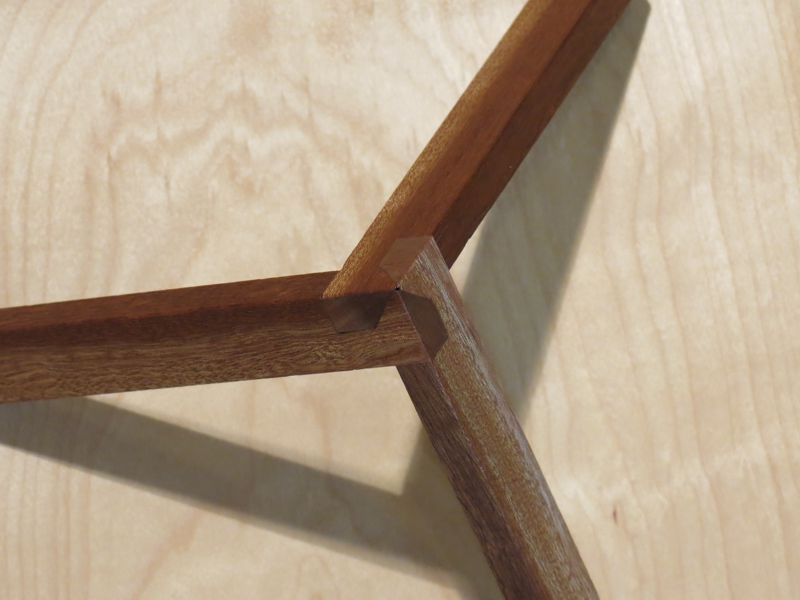
This isn’t a practical joint. It barely holds itself together, and it’s very fussy to cut and fit (and, if you look closely, you can see that it’s easy to break off one of the sharp triangular tips of the pieces). But it got me thinking: as impractical as it may be, it could nevertheless serve as an étude.
In music, an étude (French for study) is a composition whose purpose is to help build technical proficiency. Études are not meant to be performance pieces, although in a few exceptional cases, such as Frederic Chopin’s piano etudes, they have made their way into the performance repertoire.
Other fields of endeavor have similar practice pieces: chess players study standard openings, Japanese martial arts have their kata. The sequence of moves in tàijíquán can be thought of as a single long, extended étude.
Of course, woodworkers have…well, not much. There’s the Gottshall block, and Chris’s recently republished Dovetail a Day exercise. (Gary Rogowski has advocated something similar with his “5-minute Dovetail” regimen, although in his case it’s more of a warm-up stretch than an extended exercise.) And I’m looking forward to LAP’s new Charles Hayward book, as I suspect that it may contain some exercises along these lines.
But that’s about it. For whatever reason, the concept of standardized practice exercises doesn’t get much airplay in the modern woodworking world. One can argue that woodworkers want to make “real” things, and not just practice pieces, but the same argument applies to the other activities mentioned above: musicians want to perform for a real audience, chess players and martial artists want to face real opponents, etc.
So what’s the deal with woodworkers? Do we need a library of standard woodworking études? Would anyone do the exercises?
Appendix
In case you feel the urge to duplicate the joint in the photo above, here is a procedure that I’ve worked out.
You’ll need three sticks that are about twice as wide as they are thick, with the end in which you’re going to cut the joint nicely squared off. You will also need a thin shim, about 1/16″ thick. Set your marking gauge to the thickness of the sticks, and on each stick scribe a line up one face, across the end, and down the other:
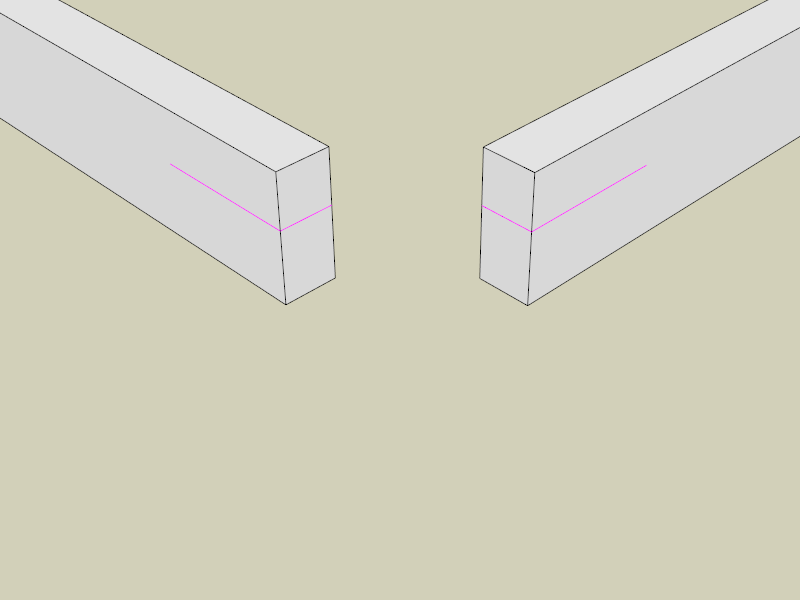
(I’m showing two views of the end of the stick, so that you can see both sides.) Make sure that you note which edge of the stick you’re referencing your measurement from; in this illustration, I’m referencing from the upper edge.
Now reset the gauge to the thickness of the shim, and scribe a line all the way around the end of the sticks.
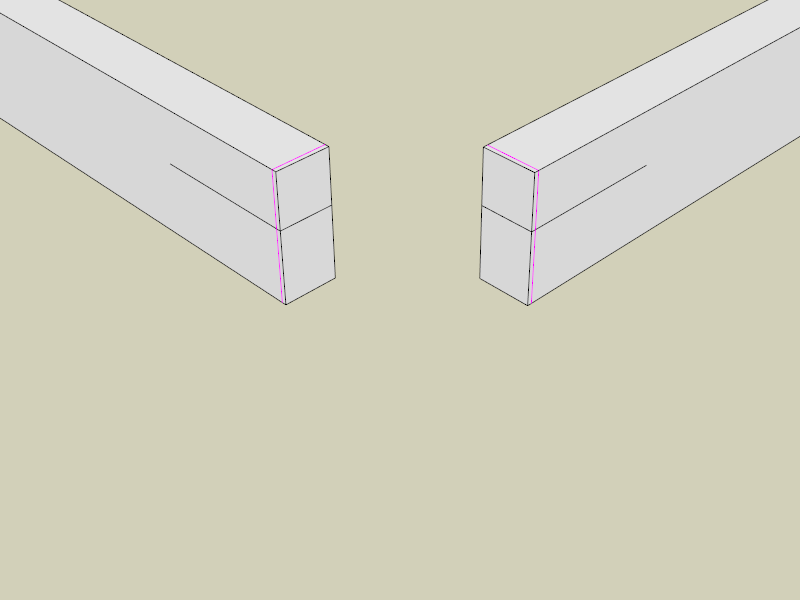
Repeat with the gauge set to the thickness of the shim plus the thickness of the stick:
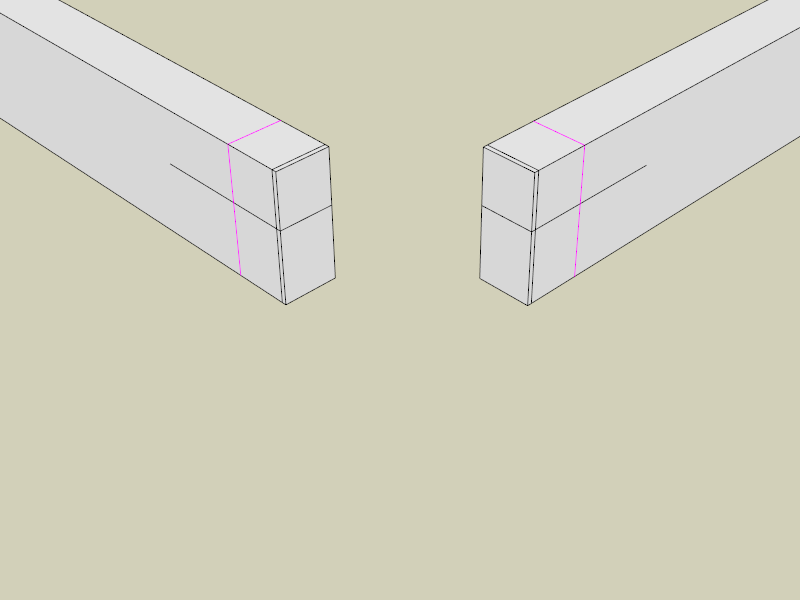
And finally, with the gauge set to the thickness of the shim plus the width of the stick:
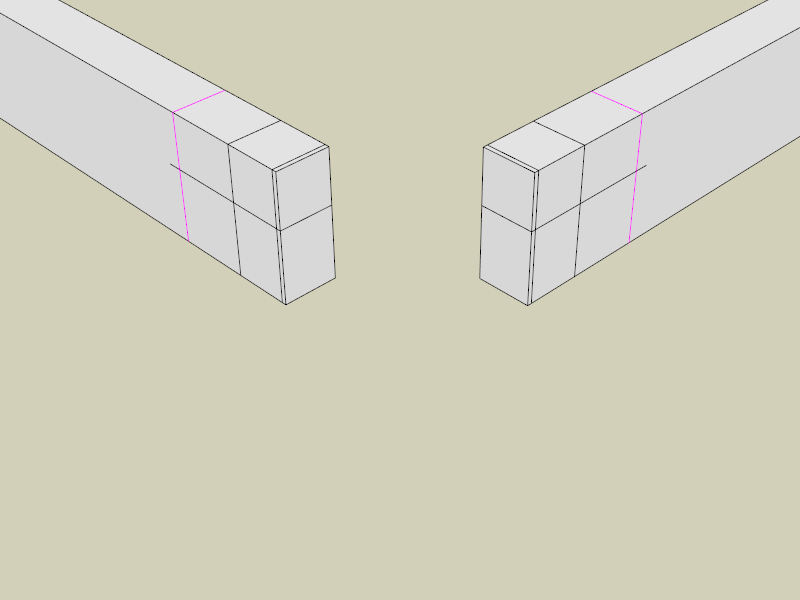
Scribe two 45° diagonal lines as shown:
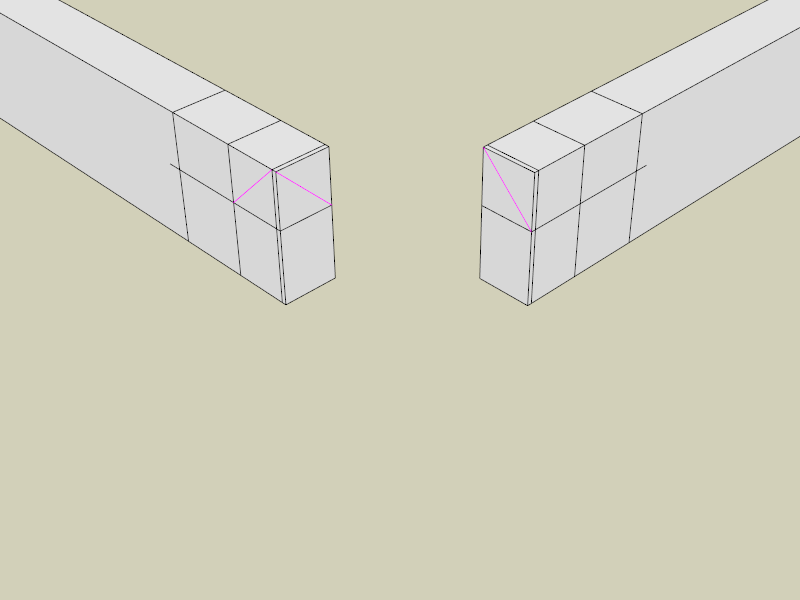
Note that if you’re ambitious and want to build an entire cube, the joints at each end of a stick have to be mirror images of each other, or else the cube won’t go together.
Use a saw and chisel(s) to cut a notch in each piece, from the edge that you referenced above, as if you were making a lap joint. You want this to be a good snug fit.
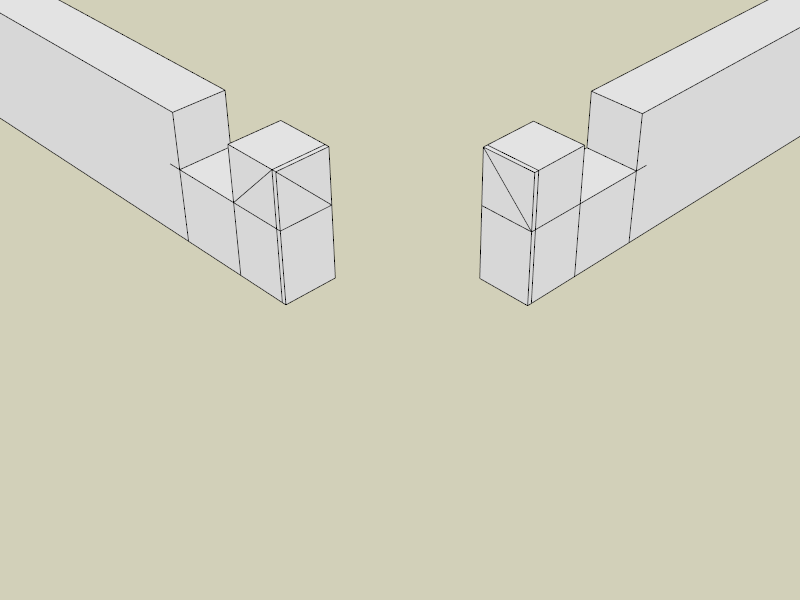
Remove the triangular waste adjacent to the notch:
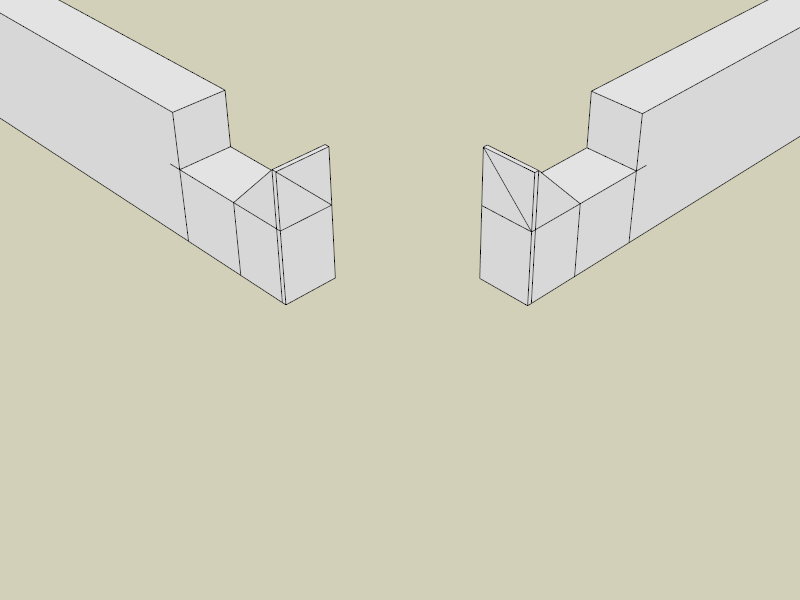
I find that the simplest way to do this is to lay the stick on its side and cut down with a chisel, removing a big chunk at first and then sneaking up to the line. Err on the side of caution here; you’ll be fitting this line against its mating piece later, so you’ll want a little extra meat to work with.
Now remove the other bit of triangular waste:
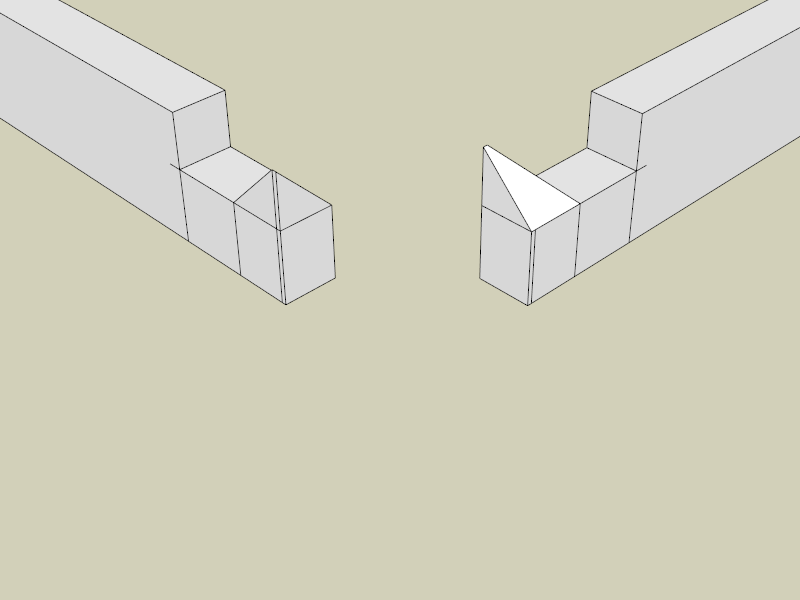
The easiest way to do this is to mount the piece in a vise, end up, and split the waste off with a chisel. Since the cut is along the grain, it splits off easily (maybe too easily). Again, leave a little bit of waste to remove later during fitting.
Mark the pieces on the side and end so that you can keep track of how they go together. I used a simple marking scheme:
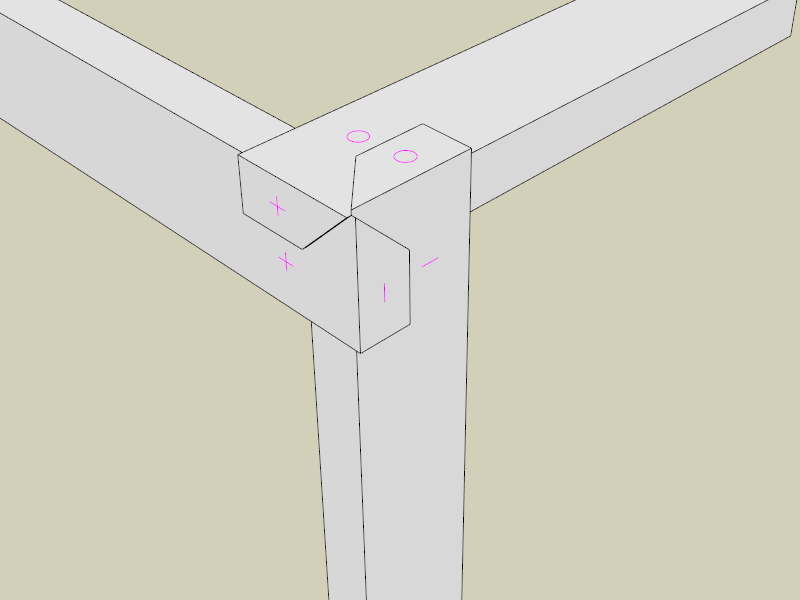
Finally, fit the pieces together in pairs, gradually paring away the remaining waste material until the pieces fit together closely. (You can cheat a little and make the fitting easier by slightly undercutting the two interior triangular faces.)
Once the pieces have been fit together to your satisfaction and you’ve assembled the joint for good, you can plane off the 1/16″ extensions, the purpose of which was to help prevent the unsupported triangular tips from breaking off, much like the “horn” on a mortise-and-tenon joint serves to keep the end of the mortise from blowing out.
This joint sort of holds together with friction, but it won’t stay together without glue (or pins). I’ve come up with a modified design that ought to interlock much more tightly:
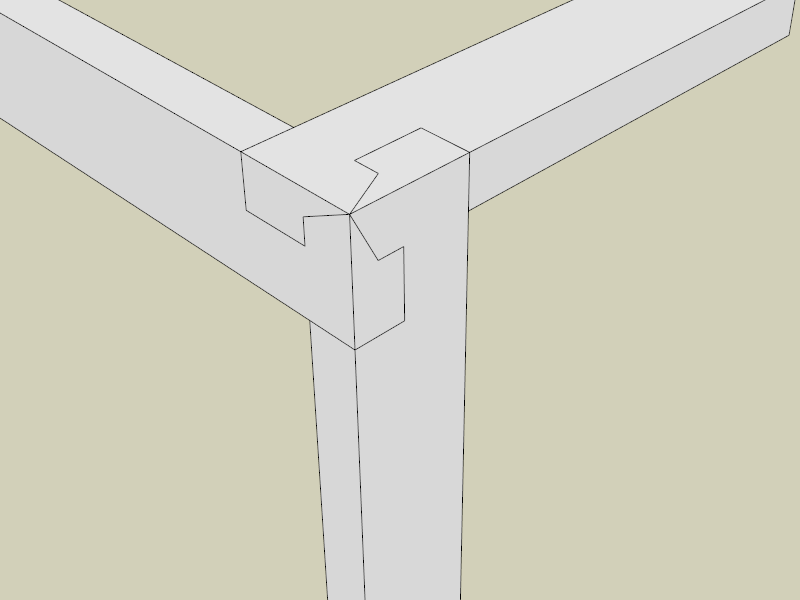
Unfortunately, I have yet to figure out a decent way to cut it (without resorting to a CNC mill). The experimental failures are currently littering my shop.
An étude for another day, perhaps.
EDIT: Bronzy935 asked about how to pin the joint; I’ve done something like this before (using screws), and it’s surprisingly sturdy:
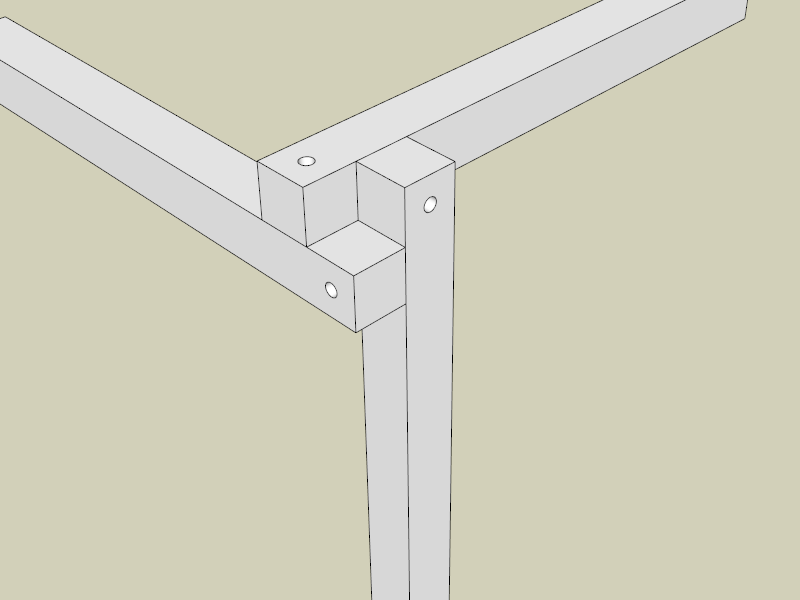
–Steve Schafer
Like this:
Like Loading...