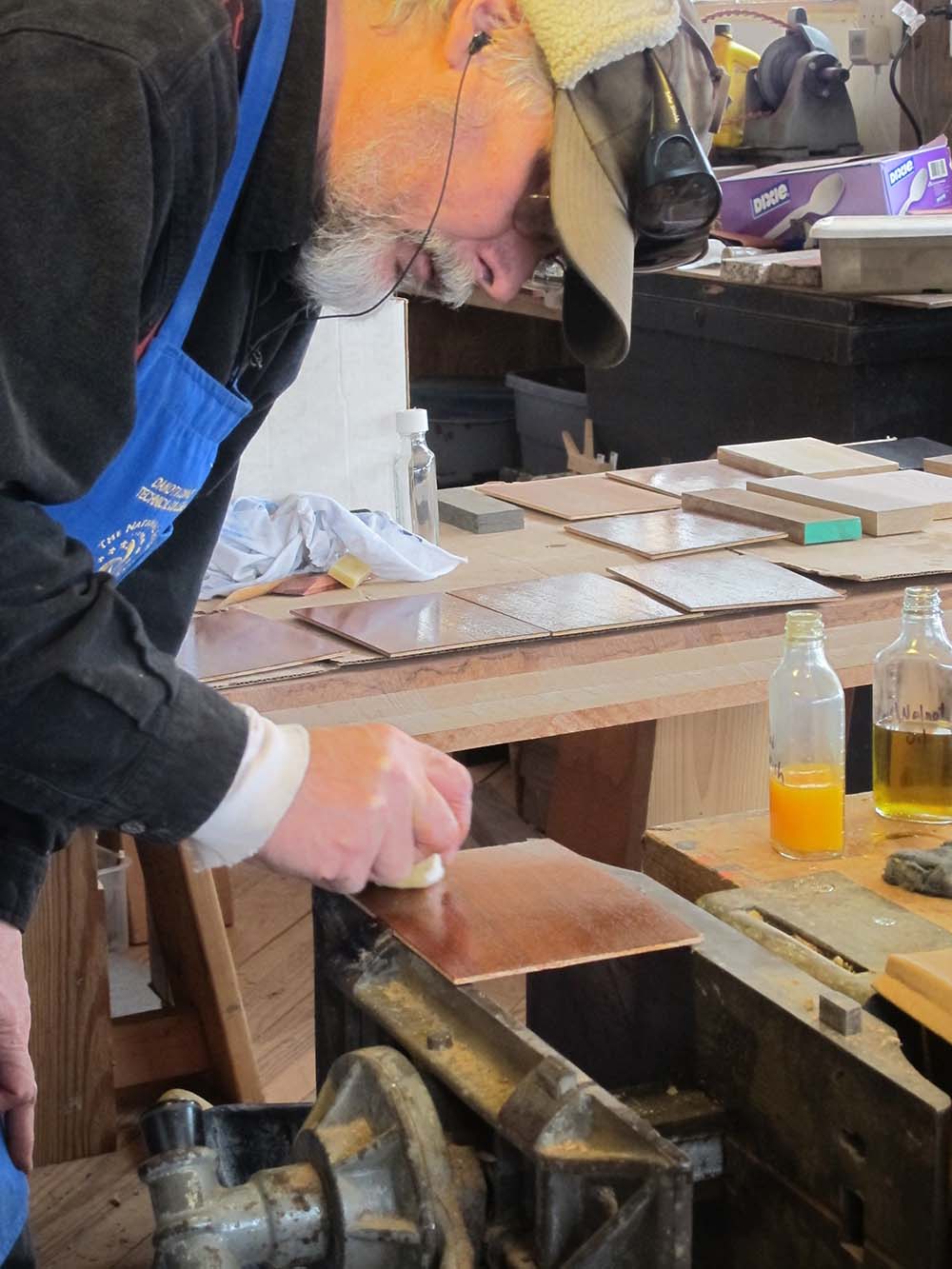
Editor’s note: As we wrote about in August, longtime LAP author Don Williams is writing a new book, “A Period Finisher’s Manual.” Don is a conservator, craftsman and author of many articles and several Lost Art Press books, and the maker of Mel’s Wax, a patented archival furniture care product. This post has been adapted from his new book’s introduction. Don is currently editing the manuscript and taking lots of pictures at the finishing bench.
It’s probably not the best marketing approach but now that the first draft of “A Period Finisher’s Manual” (APFM) is in the compewder it is probably time to scribe a few words about what it is not. That’s right, what it is not.
Even the title gives a clue; it is not “The Period Finisher’s Manual,” not “The Complete Finisher’s Manual” nor “The Ultimate Guide To Finishing.” Regardless of the subject or context those kinds of book titles almost always make me roll my eyes audibly. Epistemologically they strike me as pretentious and implicitly fraudulent; even The Bible confirms there was a lot more going on than there was time and space to record it all. I am personally not burdened with undue humility, but any book I write is by definition incomplete. To quote the punchline to an old joke, “An expert is a guy with a briefcase a long way from home.” I’m at home so my work can only include a portion of knowledge. So my title is “A Period Finisher’s Manual.”
Another thing APFM is not is a slavish catechism of pre-industrial finishing practices. No, you will not need to don knee breeches and replace your electric lights with tallow lanterns or wax candles in order to comply with the thrust of its message. You do not need to be strictly limited to the materials and tools available to the 18th-century workshops of London, Paris or Williamsburg. Certainly these form the conceptual and practical foundations but are instead the guides to thinking about finishing compatible with the technologies and aesthetics of the past. It’s sorta like the tag line for Don’s Barn: “Where modern craft meets the past.” APFM is about a way of working at the woodfinishing bench that transcends the limitations of orbital sanders and catalytic spray lacquers. Hint: You are probably not astonished when I suggest that old-timey hand-worked surfaces and their finishes are the more beautiful option. Just my opinion, of course (but I am right).
Were I forced to describe APFM briefly, it would be “The What, Why, and How approach to traditional woodfinishing.”
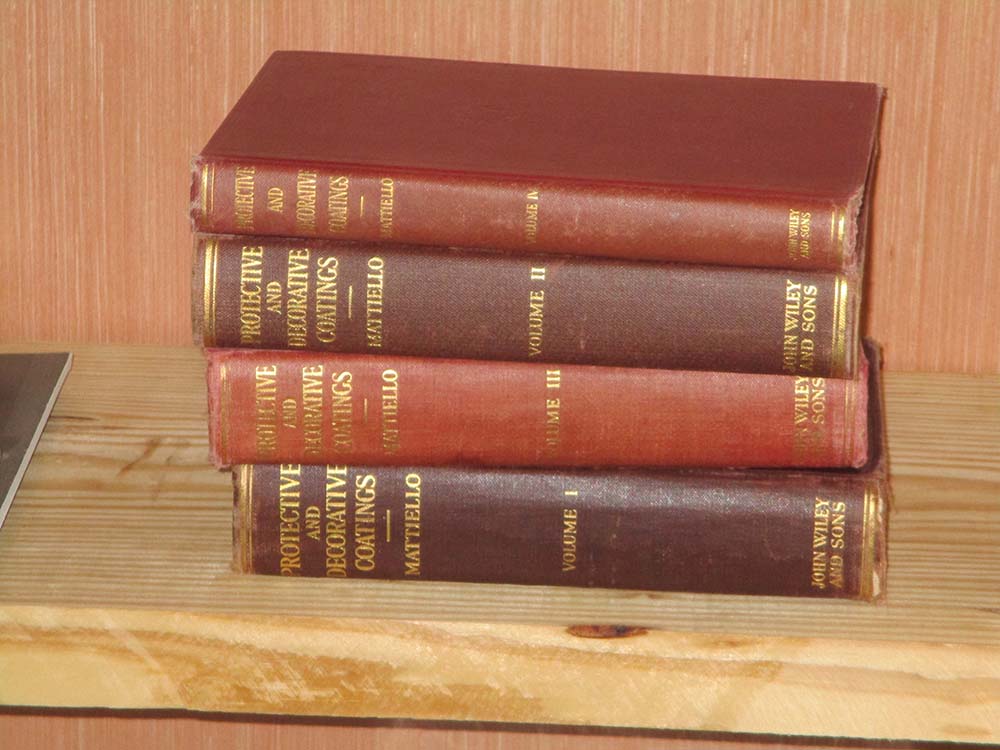
What?
“A Period Finisher’s Manual” is not any sort of definitive survey of finishing materials and processes. It is a selective review of just a few materials and practices predating the Age of Synthetic Chemistry: a few waxes, a few varnish resins, and a few oils, applied (or not) with elegantly simple tools. The greatest attempt to recount a complete inventory of materials and processes available to the finishing enterprise was the magnificent WWII-era undertaking “Protective and Decorative Coatings” by Joseph J. Mattiello, consuming multiple volumes and almost 4,000 pages. Yes, I own and have scoured the set, along with its 1970s-era successor “Treatise on Coatings” by Myers and Long, and the most recent “Organic Coatings” by Pappas, Jones and Wick.
I could enter into writing APFM with the expectation that the reader would undertake a thorough study of these tomes beforehand, but that would likely be an unfulfilled expectation. So necessarily APFM will be restricted to materials and information the reader is most likely to actually use.
Why?
Recently I was corresponding with my friend John, a former seminarian, about the meaning of a particular passage in the New Testament. At one point in the discussion John said something to the effect of, “You can only get so far in this without reading Greek.” What does that have to do with woodfinishing (other than the possible implicit divinity of the craft)? Well, in the very same exchange John reminded me of my exhortation to students that, “In woodfinishing you can only get so far without learning some chemistry.” That said, “A Period Finisher’s Manual” is not a chemistry textbook. Rather than bombarding you with such exquisite knowledge, even though it would no doubt thrill a small cohort of readers, APFM integrates chemistry and its parent, materials science, as I believe necessary for the finisher to understand why things happen as they do on the surface of the wood. Solvent theory, molecular weight, adhesion, rheology, film formation, gloss, diffractive index, surface tension and many other components of successful finishing are essentially manifestations of molecular properties.
So too is color, even though I spend almost no time or words on the subject. APFM is not a color technology book, at least in the context of historic dyes and stains on bare wood. I find little use for ancient recipes for chemical wood stains in my own work so the topic is not addressed in any meaningful depth here beyond japanning and interlaminar glazing.
The need for understanding materials science in the finishing room is a constant theme running through the art form. One vignette from my own past is a fairly omnipresent reminder to me. Forty-five years ago, while working as a “scratch and dent man” for a furniture store, I was charged with touching up a set of bilious French Pretentious bedroom furniture. (Pop Quiz – Q. What’s the difference between a furniture repairman’s “touching up” and a conservator’s “inpainting?” A. About $75/hour.) Though I have a pretty good eye for color and layered finishes it was a struggle to get to an acceptable appearance, in the end involving the forcible integration of powder pigments with a concoction of spirit varnish, oil paint and latex. With these three totally incompatible materials I got it to work through the sheer application of energy, in this case the forced agitation with a brush. I was so pleased with the result that I bragged about it to my friends. Hey, I was 19.
Knowing what I now know about material properties, I have to wonder if at some point later the touched-up areas simply exploded off the surface. As my late friend and colleague Mel Wachowiak used to say, “With enough force you can pull the tail off a living cow.” I guess the same is true for incompatible woodfinishing materials. I got them to work together under the whiplash of vigorous mixing, but some understanding of the chemistry involved sure would have helped me then and it will help you in your future projects.
Which leads directly into another descriptor of what APFM is not – a stuffy academic book. I won’t say that Chris put his foot down, but he did suggest in a most emphatic manner that any book with hundreds of footnotes was unlikely to be appearing in the LAP catalog. Any technical citations will simply be folded into the folksy banter of the text. If you have read my other books or follow my blog you will know what to expect – big words when necessary, good humor always.
How?
“A Period Finisher’s Manual” is not a book of “how-to” tricks. Pets and circus animals do tricks, craftsmen have skills and techniques. (I’ve literally warned editors if the word “tricks” ever appeared in concert with one of my articles our working relationship was terminated.)
Instead, APFM is my attempt to describe a systematic approach to woodfinishing, complete with several dozen detailed verbal and visual descriptions – basically the How? culminating the What? and Why? considerations I mentioned above. By walking through a variety of finishing projects, complete with conceptual rationales and step-by-step visual representations, I hope to instill you with the confidence to embrace finishing as something to be anticipated with a delight rather than be feared and loathed, and ultimately, shortchanged. I have seen far too many examples of wonderfully designed and skillfully crafted woodworking projects that were betrayed by their makers’ puking some polyurinate on the surface with little understanding and less care.
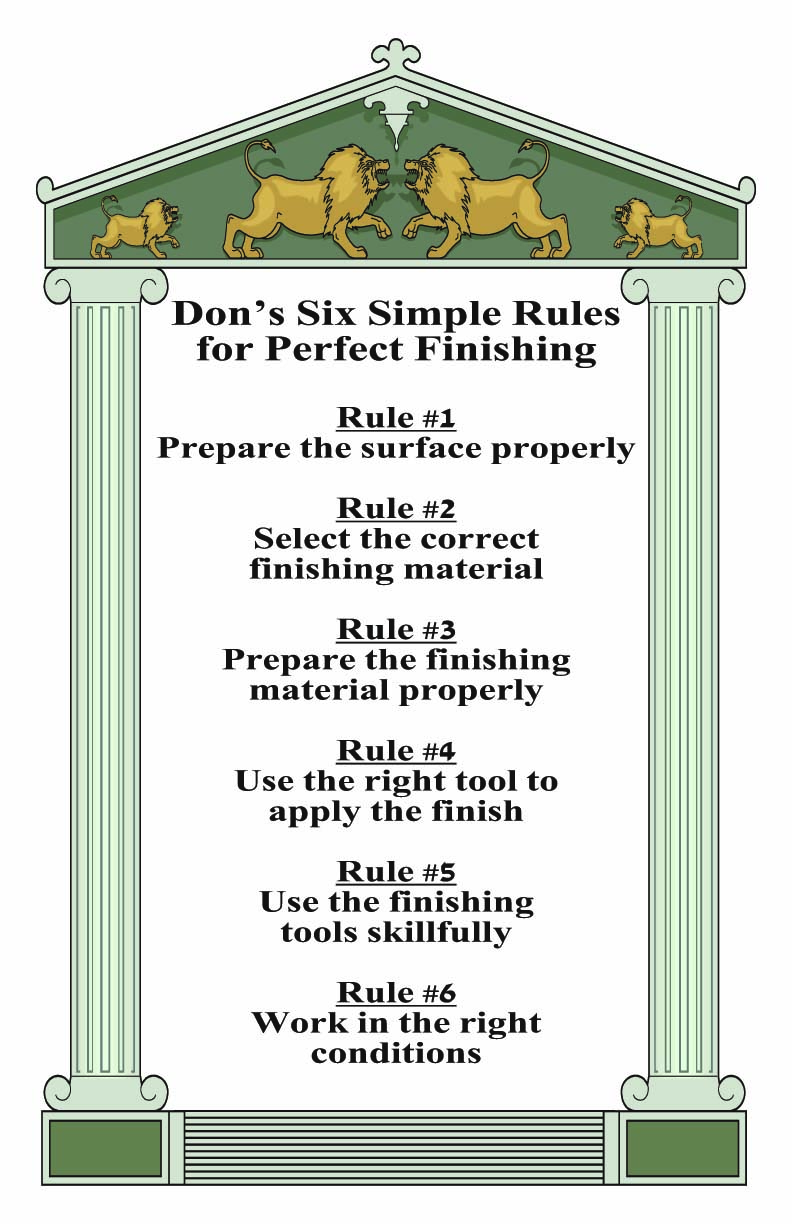
Decades of woodfinishing (and teaching same) confirm that despite its vagaries it can be a predictable step-by-step process built on a foundation of technical and artistic understanding. So, I’m organizing the book’s contents the same way I organize the concepts and practices for my own woodfinishing, resulting in predictably good results.
Perhaps I should have titled it “A Predictable Finisher’s Manual,” or even “A Contented Finisher’s Manual.”
Because in the end, it is also not unpredictable and definitely not intimidating. It is in essence the very reason we make stuff.
— Don Williams