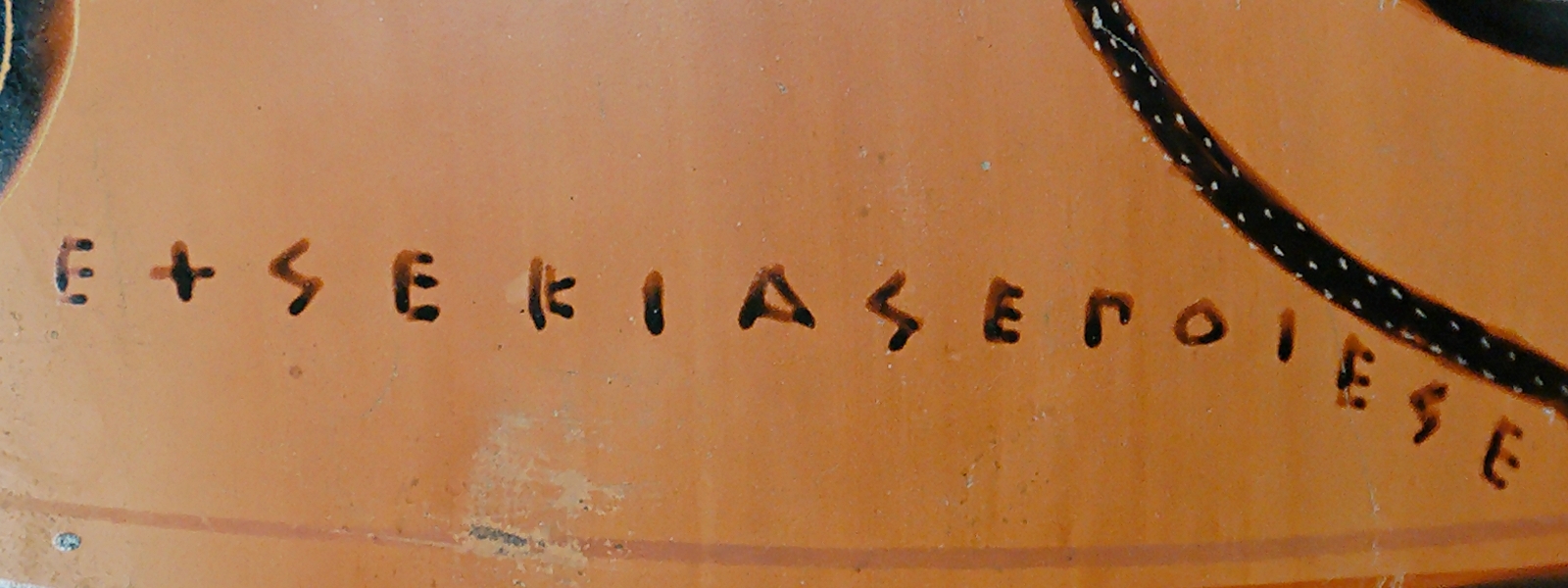
I have often wondered what period of time must elapse before a good craftsman becomes an outstanding one. Was he born that way, needing only the requisite skill to develop his genius? Or did he evolve stage by stage like other men, but having the courage to take his work a stage further, perhaps many more stages than other men will venture.
Yet that may only imply the virtue of persistence, not that he is outstandingly gifted. What is the secret? We can add together the small perfections which make up the quality of a first-class man but, even so, something eludes us, something in the very essence of his work which defies analysis.
There is an old Breton proverb which says: “Qui aime son métier, son métier l’aime.” It may be this puts a finger right on the spot. That there has to be love between a man and his work, something which each gives to the other, which acts and interacts upon his skill before craftsmanship becomes the superlative thing that is created beauty.
Probably many more men than we can possibly estimate, working at the handicraft they enjoy, are producing work of this kind today, to be seen by few people, but to some of those few communicating that little thrill of pleasure which only superlative work can give. When we think of the amount of wastage there has always been right down through the ages by reason of material change and decay, the destructiveness of wars, accidents, sheer stupidity and thoughtlessness, the marvel is the amount of creative beauty which must have been produced by unknown men in every age for so much to have survived into our own, infinitesimal in comparison with what has been lost.
Furniture, of its nature, cannot date back many centuries, as much, perhaps more, through neglect due to changing fashion than from the perishability of wood. But ancient records and wall paintings have yielded up a great deal of information about the furnishing of kings’ palaces and the like, and many ancient craftsmen’s masterpiece has been described in meticulous detail, which still seems to retain the sense of wonder of those who had seen the work and the proud sense of possession of the monarch who had owned it. Very occasionally, by one of the freakish chances of history, the name of the craftsman will have survived while that of his noble patron is forgotten. A strange reversal in values.
In some cases, conscious that this work of his was good, the craftsman has inscribed his name on some obscure corner, to be discovered years afterwards by men who came to admire. It is not often the craftsman inscribes a friend’s name as well as his own, yet this is what happened when, between two to three thousand years ago, a Grecian artist wrote his signature in tiny, crabbed Greek script: “Exekias made it,” on the lovely vase he had made and painted, and then in a burst of pride and affection: “Handsome Onetorides.” And so the name of his handsome friend has been passed down through the ages in somewhat unsual confirmation of Keats’ “A thing of beauty is a joy for ever.”
Had the maker instinct of immortality when he inscribed his friend’s name on the lovely thing he had just completed? Exekias himself was known as the finest Athenian vase painter of his day, and the vase is the famous one painted with a panel in which with consummate skill he shows the two Homeric warriors, Ajax and Achilles, seated at an improvised table playing a dice game. The two figures, painted and incised in black upon a red ground, are bearded and every line of their bodies as they bend forward shows a kind of eager intensity, but there is nothing to suggest that the handsome Onetorides was a model for either. No, the inscription seems to have come out of the fullness of the artist’s creative joy, knowing this work of his hands to be good and wishing to associate with it the name of the friend he admired. Rarely has a dedication been made with such simplicty and rarely has any dedication lasted so long.
Probably when we come to the word “dedication” we come to the crux of the whole matter. The man who is going to do outstanding work in any craft has himself to be a dedicated man. He must be sensitive to beauty wherever he sees it and in whatever form and have the instinct to turn to beautiful accomplishment the handicraft he has made his own. He has to have skill so sure and informed that it will carry him faithfully through his undertakings, enabling him to tackle new kinds of work with the confidence of experience.
But all this the really good craftsman can have. If he wants to go further still, it can only be for the love of it, something which will bring an element into his work which no school can teach, a heightened degree of skill, a suavity, a finish, which can only happen when, as the Bretons say, the work loves him back.
—Charles Hayward, The Woodworker, February 1963