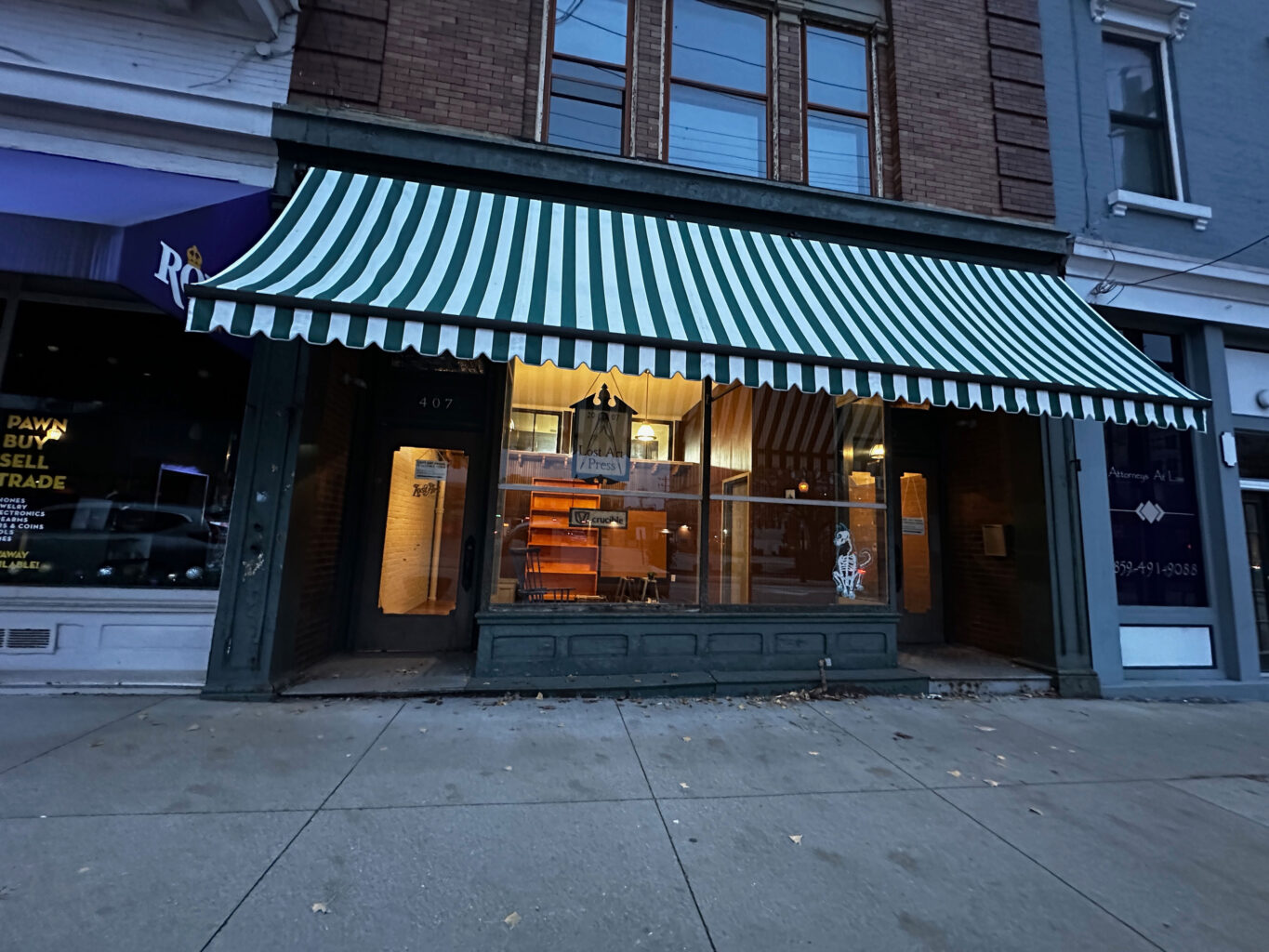
It’s been a while since I wrote about our work on the Anthe Building, the old factory where our fulfillment center is located. This fall we’ve been working on the storefront of the building, which faces Madison Avenue in downtown Covington. And on some offices upstairs for the editorial staff. Here’s the latest.
The Storefront
This will be operational by the end of the year. The entire facade of the Anthe Building is one of the last remaining completely original storefronts in Covington. So every repair here is aimed at conservation of the original materials and altering as little as possible.
The plate-glass windows are trimmed in ornamental steel and were originally painted a bright green. We’ve removed some of the old paint on the trim and will repaint it in the original color. Likewise, all the woodwork surrounding the windows and doors is original. Some of it is in rough shape, but we will keep it all. But that’s a project for later. Most of the work has been to the interior space.
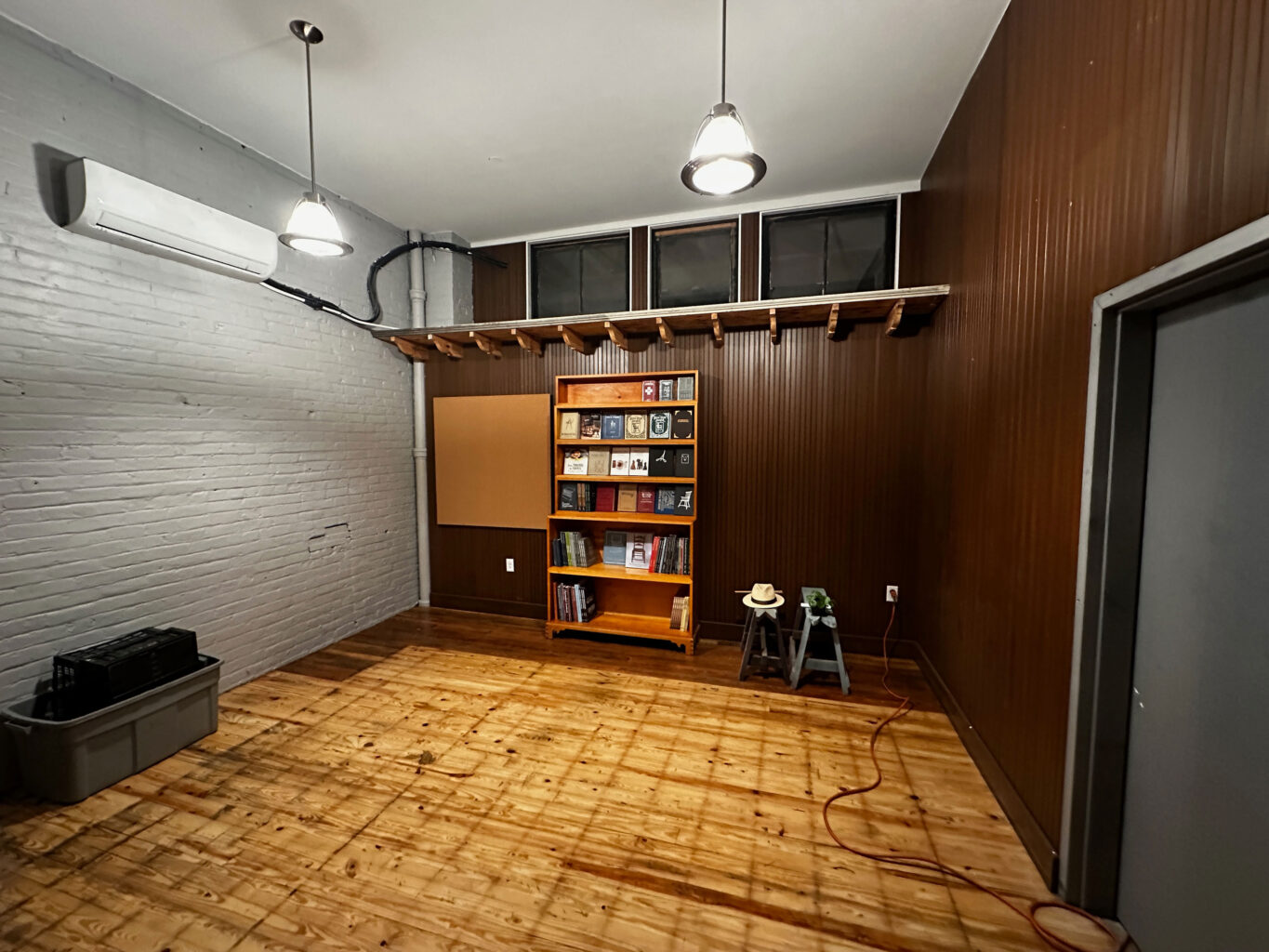
We have tidied up the original pine floors – removing some mastic left from some late 20th-century flooring – and adding some varnish to preserve them. The back wall of the storefront and its gallery are now complete and await some final painting.
We’ve moved the storefront’s main bookcase into the storefront, hung a cork board to display apparel and not much else. This month I’ll build some freestanding displays for books and other fun window displays. The goal is to look like a 19th-century storefront, because that’s what it is.
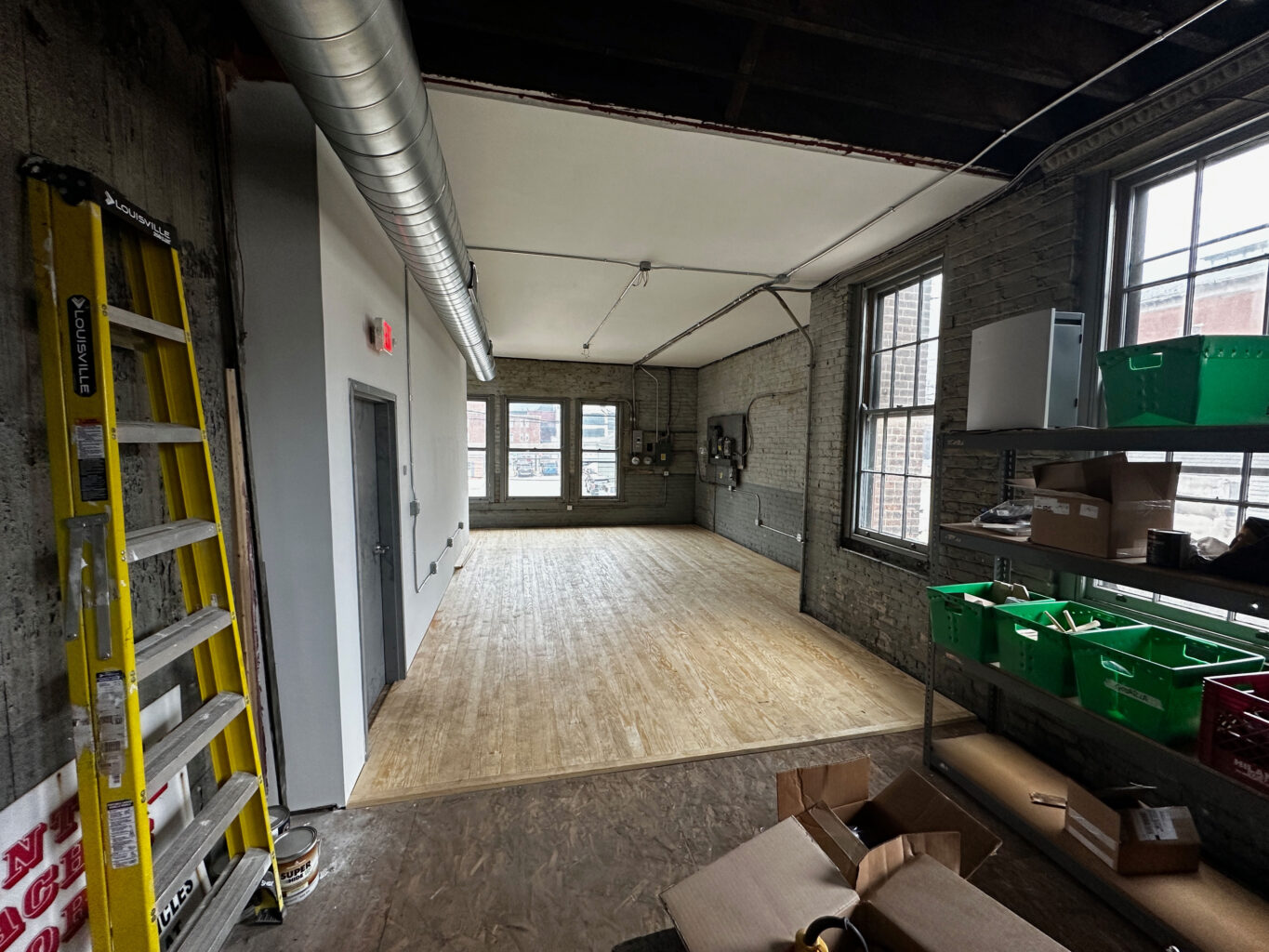
Offices
Upstairs, we’ve carved out 370 square feet for offices, with another 200 square feet for tool assembly. The area was drywalled during the first phase of the project, so we’ve been trying to make it habitable. That meant adding a heat pump system for the second floor, plus a nice floor (the original floor is too worn out to use, so we preserved it under felt and OSB). Our offices have yellow-pine floors to match the rest of the building.
We should move some desks in there by the end of the week. And we’ll be working there every day by the end of the year.
What Does This Mean for You?
Our Willard Street storefront, which is below our living quarters, will remain basically unchanged. We’ll use it for classes, furniture construction and photography. But it won’t be home base anymore.
All retail sales will move to the nearby Anthe Building at 407 Madison Ave. The good news is we will have regular storefront hours for people to visit – 10 a.m. to 5 p.m. weekdays. The bad news is we won’t be open for weekends just yet. We don’t yet have the staff to cover those shifts.
When we embarked on this project, we held a fundraiser where we sold special products (classes, hammers, books) with the proceeds going to building repairs. We also had plans for an opening day party for everyone who contributed. We keep putting that party off because Anthe is still an active construction zone.
I can’t say exactly when we might have the party. But we will have it. Maybe February 2025.
— Christopher Schwarz