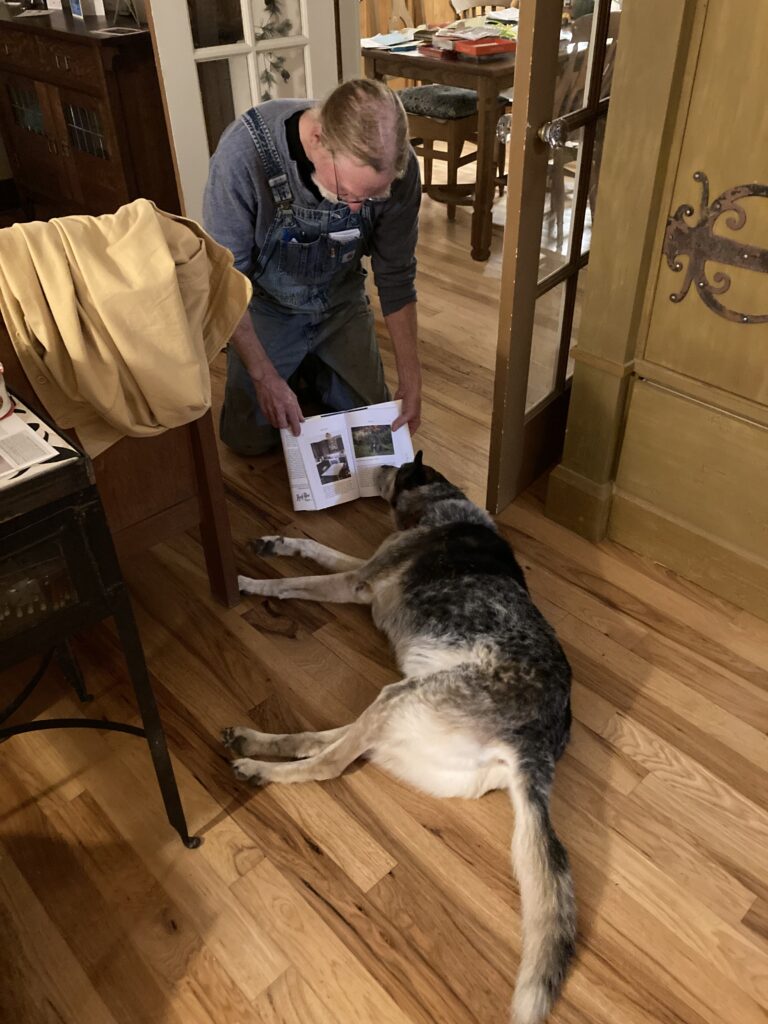
Lost Art Press had an early visit from St. Nicholas in the form of a comment on “Shop Tails” from Nick Offerman. It’s not every day that you find a gem in your inbox from Ron Swanson this thespian, author, singer-songwriter, lover of sheep and shepherds, all-around good guy and builder of canoes and ukuleles, among other wooden artifacts.
“It was only a matter of time before Lost Art Press found itself publishing a beautiful book that is not about woodworking,” he wrote.
“I have long admired Nancy Hiller as a craftsperson and a writer” – the admiration is mutual – “so I am thrilled to the marrow at this examination of her life through the lens of relationships with animals she has known. Here you hold the richly penned, fantastic memoir of a plucky and clever woodworker, kitchen designer and writer, who honestly describes her ascension on the path of wisdom, with a special focus on the stumbles. Among the signposts and guides she has been lucky enough to encounter, she counts a parade of charismatic creatures and the charming directions they lent to her life’s decisions.”
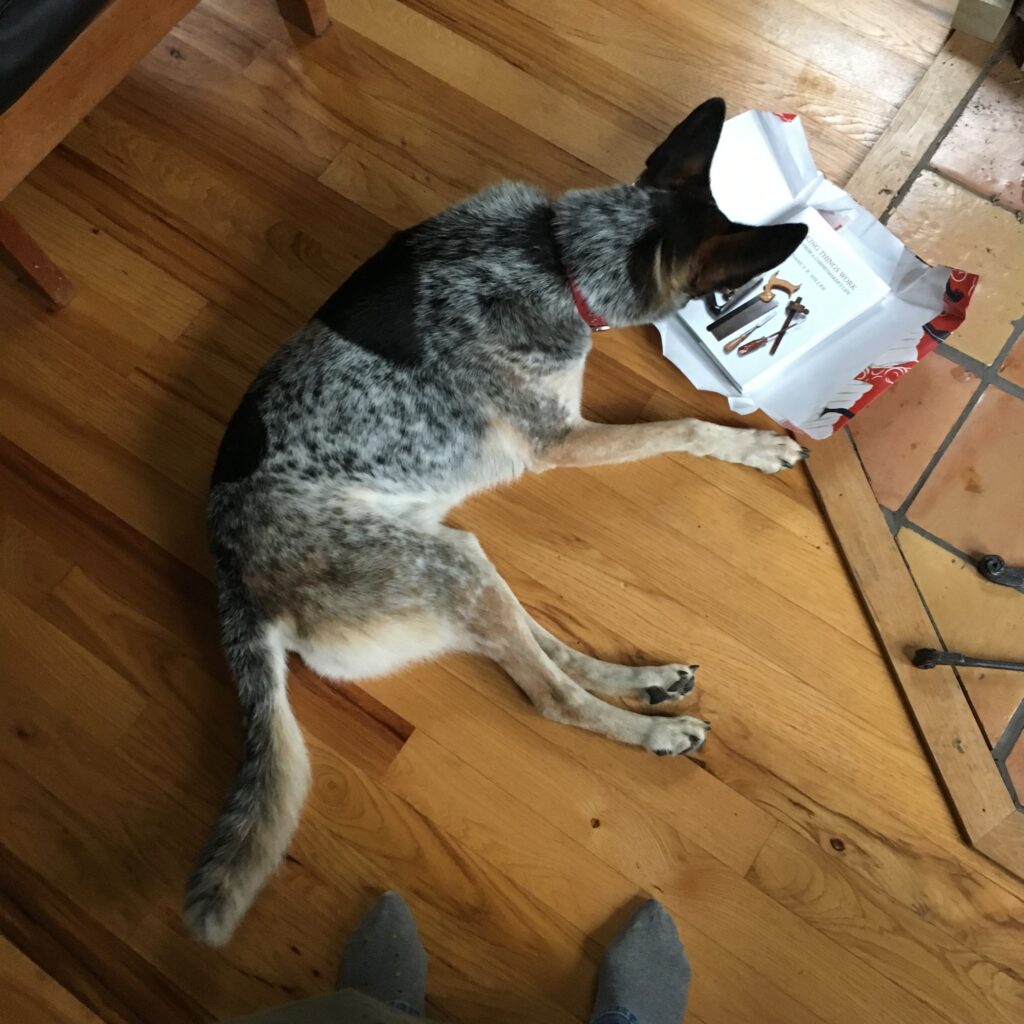
While I personally make no claim to wisdom, I have learned a lot from the animals who have shared my household at different times, as well as from wildlife, stray domestic animals (including a goat) and a select few (among them, buffalo) raised on farms. These and more fill the tales in this volume, the entirety of which is true.*
But while the book honors animals who have been my companions, teachers, entertainers and occasional bêtes noirs, it is at heart, as with all books published by Lost Art Press, about learning and teaching. In this case, the learning isn’t about how to sharpen tools or build a chest, but about finding ways to survive devastating loss, or realizing that most of us are capable of facing far scarier slang for fecal matter turns of events than we might otherwise imagine. In the same vein, the teaching is not about how to build a chair or harvest hickory bark, but about the reality that bad things don’t just happen to “other people,” and few, if any of us, live the kind of picture-perfect life that sells everything from refrigerators to potato chips. It also seeks to raise awareness of at least one dangerous common practice and a challenging-to-diagnose cause of canine paralysis.
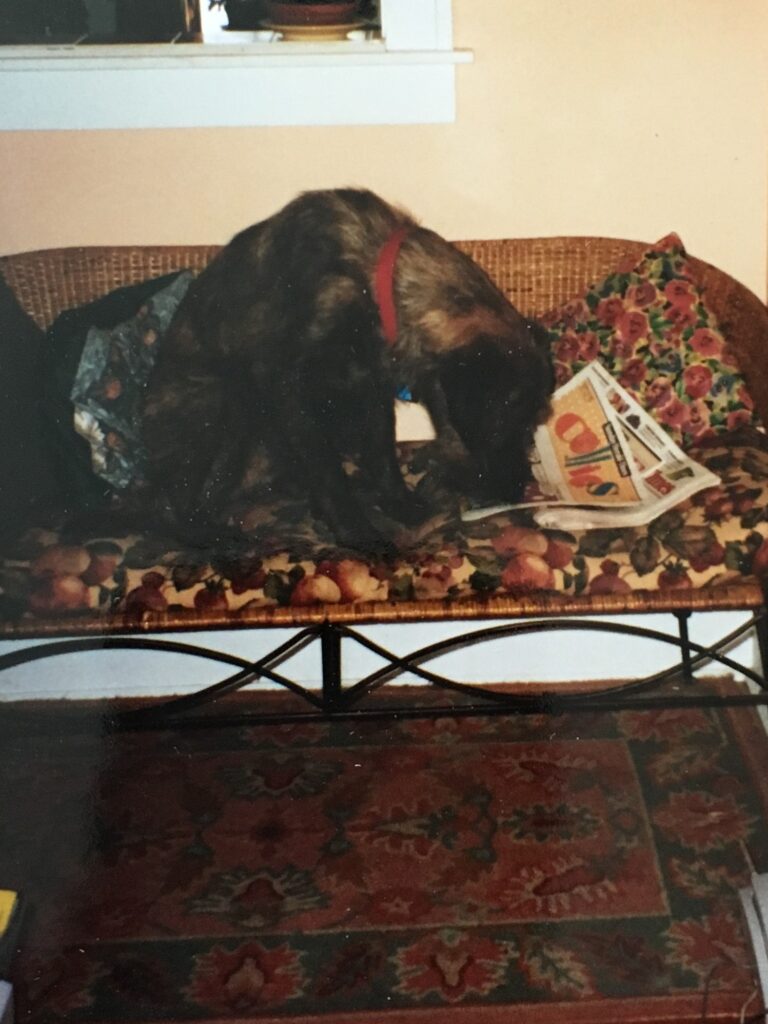
If there is any wisdom in this book, it’s consistent with many exhortations from Mr. Offerman himself, as those who have attended his performances in person will know: Be kind. Think of others, as well as yourself. Open your eyes; don’t let the years slide by while you wait for just the right moment to live. This earth is a place of wonders; savor them in ways that will leave them in good shape – ideally, better shape – for those who come after us. And it’s OK to have the occasional belch or fart among friends.
Big thanks to Nick Offerman for even cracking the cover of “Shop Tails,” let alone reading, and for sending this supportive fistbump.
– Nancy Hiller, author of Shop Tails, Kitchen Think and Making Things Work
*Some names and other identifying information are altered, and in one case only part of the story is included out of respect for other parties.