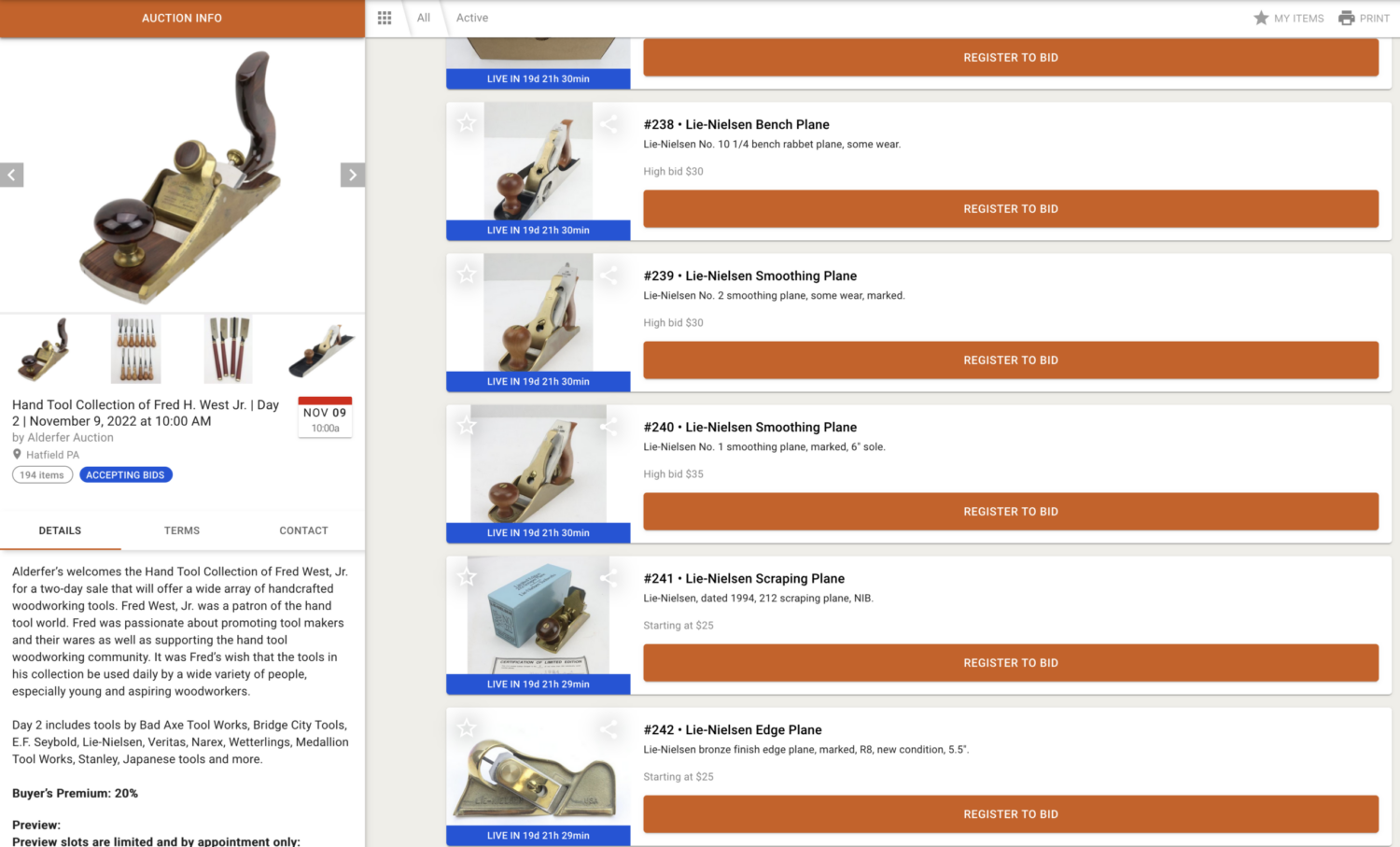
The catalog for Day 2 of the Fred West Tool Collection Auction is available; bids are accepted for Day 2 items through 10 a.m. on Nov. 9. (You can read a bit about Fred in this post, for the Day 1 catalog.)
— Fitz
The catalog for Day 2 of the Fred West Tool Collection Auction is available; bids are accepted for Day 2 items through 10 a.m. on Nov. 9. (You can read a bit about Fred in this post, for the Day 1 catalog.)
— Fitz
I am so happy to announce our latest book “Henry Boyd’s Freedom Bed” by Whitney L.B. Miller. This illustrated children’s book is about the life of Henry Boyd, one of the unsung furniture geniuses of the 19th century.
The book traces Boyd’s life from his birth on a Kentucky plantation, where he was enslaved, to the deadly Kanawha salt works in what is now West Virginia. After Boyd purchased his freedom, he moved to Cincinnati and – after much tribulation – set up his own furniture business that employed both white and Black woodworkers.
Boyd specialized in building beds. And perhaps his greatest contribution to the craft was the invention of an ingenious way to join the bed rails to the headboard and footboard. It involved using a traditional threaded screw at one end of the rail and a reverse-threaded screw at the other end.
The design was so successful it was widely known as “The Boyd Bed” and others began copying it. The invention was eventually patented.
Boyd’s woodworking cleverness also served him well during his work on the Underground Railroad.
This book has been years in the making, beginning with extensive original historical research. Boyd’s story was brought to life by Miller, who wrote and illustrated the tale. Miller is a local television reporter, woodworker and maker, and her lightly fictionalized account of Boyd is suitable for children ages 3-8 (though even adults will learn something).
In addition to Miller’s lovely telling of Boyd’s life, “Henry Boyd’s Freedom Bed” also features an extensive historical timeline of Boyd’s life. The timeline was created by researcher Suzanne Ellison, and it dispels many of the myths about Boyd that have been circulating in newspaper accounts for more than a century.
“Henry Boyd’s Freedom Bed” will be available for purchase in early November. In addition to the book itself, there will be a deluxe edition available (more details on this coming soon). You can sign up to be notified of the book’s release here.
This book, though slim, was a monumental effort for so many people. Miller developed a new illustration style for the book, and taking a person’s entire life and boiling it down into a story for children was no small feat. Ellison’s research on Boyd can be described as nothing less than relentless. We have shared it freely with local museums, and it was the foundation upon which the Cincinnati History Museum created its exhibit on Boyd (now a permanent exhibit). And then there was our own Kara Gebhart Uhl, who helped Miller with the mechanics and storyboarding to create the book.
This book is the first to examine Boyd’s life, but we hope it’s not the last.
— Christopher Schwarz
I admit, I’ve chosen an easy bay for this Covington Mechanical Library post (it’s been a frantic – and slightly under the weather – week). Today, it’s the Foxfire series, volumes 1-12 (which is an almost complete set – I believe there are two additional anniversary editions).
For those of you unfamiliar with the series, it’s a compendium – assembled from a quarterly magazine of the same name – of the crafts, culture and heritage of Southern Appalachia. The first was published in the early 1970s; Chris doesn’t remember a time when there wasn’t a Foxfire book in his home.
Also in the bay are “Trades and Occupations: A Pictorial Archive from Early Sources,” selected and arranged by Carol Belanger Grafton, and “2000 Early Advertising Cuts,” edited by Clarence P. Hornung. Chris has had these two since the early 1990s, when he was editor of “The Kentucky Gazette,” a weekly political newspaper in Frankfort, Kentucky. This was before digital photography, and Chris used these to illustrate articles when they didn’t have any appropriate photography – it was either use old clip art or he had to draw Skippy the Turtle.
To the far right are seat models, one with wire to bend the legs into position for new chair designs, along with a cutaway showing how staked joints work (from “The Anarchist’s Design Book.”)
— Fitz
Click here for week 1
Click here for week 2
Katherine “the Wax Princess” Schwarz has a fresh batch of Soft Wax 2.0 now now available in her Etsy store. It’s my favorite finish for Shaker trays and tool chest tills, and Chris uses it on just about every not-painted chair. It looks great, smells great, is easy to apply, is non-toxic – and it makes my hands softer.
Instructions for Soft Wax 2.0
Soft Wax 2.0 is a safe finish for bare wood that is incredibly easy to apply and imparts a beautiful low luster to the wood.
The finish is made by cooking raw, organic linseed oil (from the flax plant) and combining it with cosmetics-grade beeswax and a small amount of a citrus-based solvent. The result is that this finish can be applied without special safety equipment, such as a respirator. The only safety caution is to dry the rags out flat you used to apply before throwing them away. (All linseed oil generates heat as it cures, and there is a small but real chance of the rags catching fire if they are bunched up while wet.)
Soft Wax 2.0 is an ideal finish for pieces that will be touched a lot, such as chairs, turned objects and spoons. The finish does not build a film, so the wood feels like wood – not plastic. Because of this, the wax does not provide a strong barrier against water or alcohol. If you use it on countertops or a kitchen table, you will need to touch it up every once in a while. Simply add a little more Soft Wax to a deteriorated finish and the repair is done – no stripping or additional chemicals needed.
Soft Wax 2.0 is not intended to be used over a film finish (such as lacquer, shellac or varnish). It is best used on bare wood. However, you can apply it over a porous finish, such as milk paint.
APPLICATION INSTRUCTIONS (VERY IMPORTANT): Applying Soft Wax 2.0 is so easy if you follow the simple instructions. On bare wood, apply a thin coat of soft wax using a rag, applicator pad, 3M gray pad or steel wool. Allow the finish to soak in about 15 minutes. Then, with a clean rag or towel, wipe the entire surface until it feels dry. Do not leave any excess finish on the surface. If you do leave some behind, the wood will get gummy and sticky.
The finish will be dry enough to use in a couple hours. After a couple weeks, the oil will be fully cured. After that, you can add a second coat (or not). A second coat will add more sheen and a little more protection to the wood.
Soft Wax 2.0 is made in small batches in Kentucky. Each glass jar contains 8 oz. of soft wax, enough for at least two chairs.
Sure, we all know to keep our handplanes sharp, clean and lubed. But when was the last time you did maintenance on the tool’s mouth and the edges of its sole?
These areas are fragile and take a heap of abuse. Yet little is written about how to regularly maintain them.
Let’s start with the mouth of the tool. The area of the sole right in front of the mouth gets worn away from use. Not decades of use. Usually just a few months of heavy use will cause noticeable wear.
Why do we care? If the sole in front of the mouth isn’t pressing down the wood fibers, then the cut will happen ahead of the tool’s cutting edge. And that’s tear-out.
If the wear is shallow, you can remove it by rubbing the sole on some #220-grit sandpaper affixed to a flat floor tile. (If the wear is deep, you will need to file the front of the mouth, which I will cover in a future entry).
To flatten the sole, paint some red marker on the sole surrounding the mouth. Then rub the sole on the sandpaper until all the color is gone. I usually dress my plane sole every six months, and the dressing can require 5-10 minutes of work.
Once the sole is done, you should bevel the edges of the sole – with sandpaper or a file. Why? The edges of the sole are fragile when they are a sharp corner. They are stronger when they are rounded over. So if your tool has a sole with rounded edges it is much less likely to develop a burr when the plane collides with a fellow tool or a knot. These burrs look like plane tracks on the work and frustrate beginners.
To round over the edges, I tilt the plane 45° and round over the plane’s long edges on the sandpaper (see the photo at the beginning of this entry). Then I file the front and rear of the sole with a fine needle file – these areas of the sole take the most damage – to create a bevel. Then I round over that bevel with some fine sandpaper.
These small efforts make a huge difference. Your plane will produce less tear-out. And it is much more likely to leave a flawless surface behind.
— Christopher Schwarz