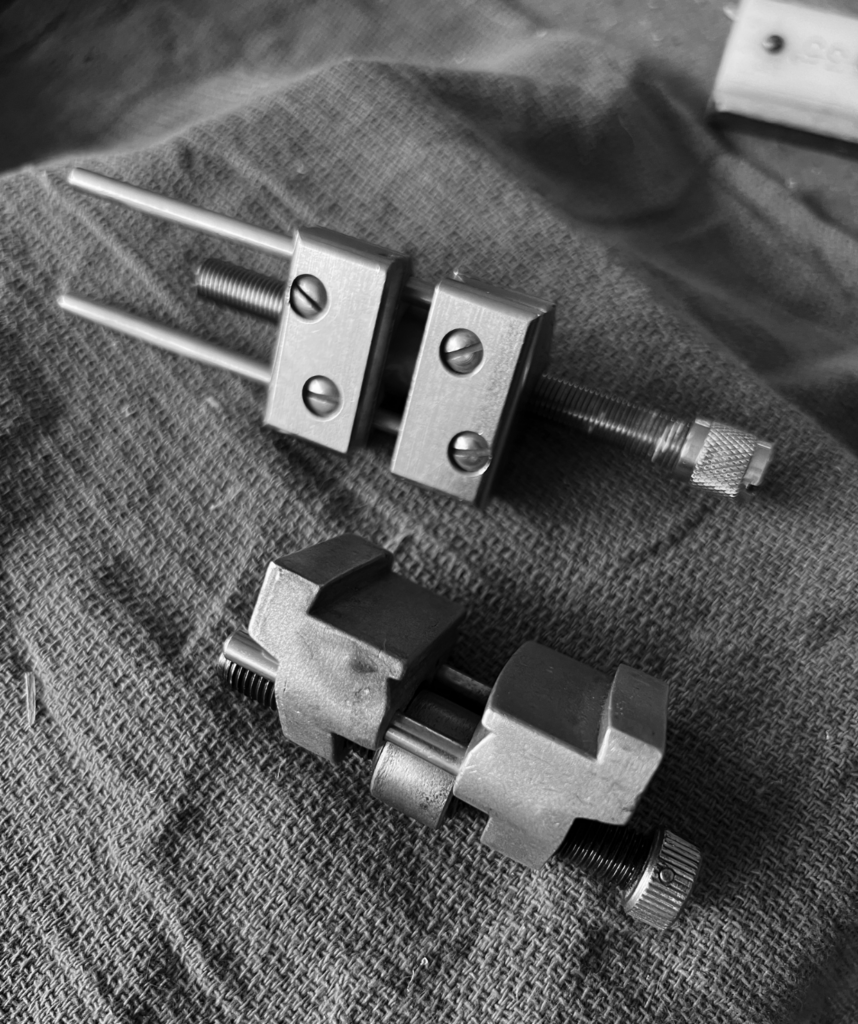
The following short excerpt is from Christopher Schwarz’s “Sharpen This” – a 120-page pocket book on how to get great edges, regardless of the sharpening system you choose. It is about what is important: Creating a sharp edge quickly with a minimum amount of equipment.
Simple side-clamp honing guides are a godsend for quick and repeatable work when it comes to chisels and plane irons. I do sharpen freehand a lot of unusually shaped tools, but when it comes to plane blades and straight chisels, I am happy to let the honing guide do the work.
Side-clamp honing guides can be had for a song – inexpensive ones cost less than $20.2 And I have found no valid downside to using them.
Critics of honing guides deride them as “training wheels” or as a crutch that slows you down. I have regularly challenged these people to sharpening contests for speed and fineness of edge – the winner determined by a judge who doesn’t know whose blade is whose. I have never lost – not because I’m a great sharpener but because the honing guide is an enormous asset.
While I do love my honing guide, my love has limits. I don’t use the endless attachments that allow honing guides to be used for oddball tools or skewed tools or short tools or extra thick tools. For those tools, the honing guide and its accessories slow me down. So I stick with the base model, which works well for chisels and plane blades.
So if you stick with the base-model honing guide, you are five minutes away from being a speedy sharpener. All you need is a simple block of wood that sets the blade at the proper angle in the guide so the steel at the tip of the blade immediately touches the sharpening media perfectly. Which brings us to a discussion of sharpening angles.
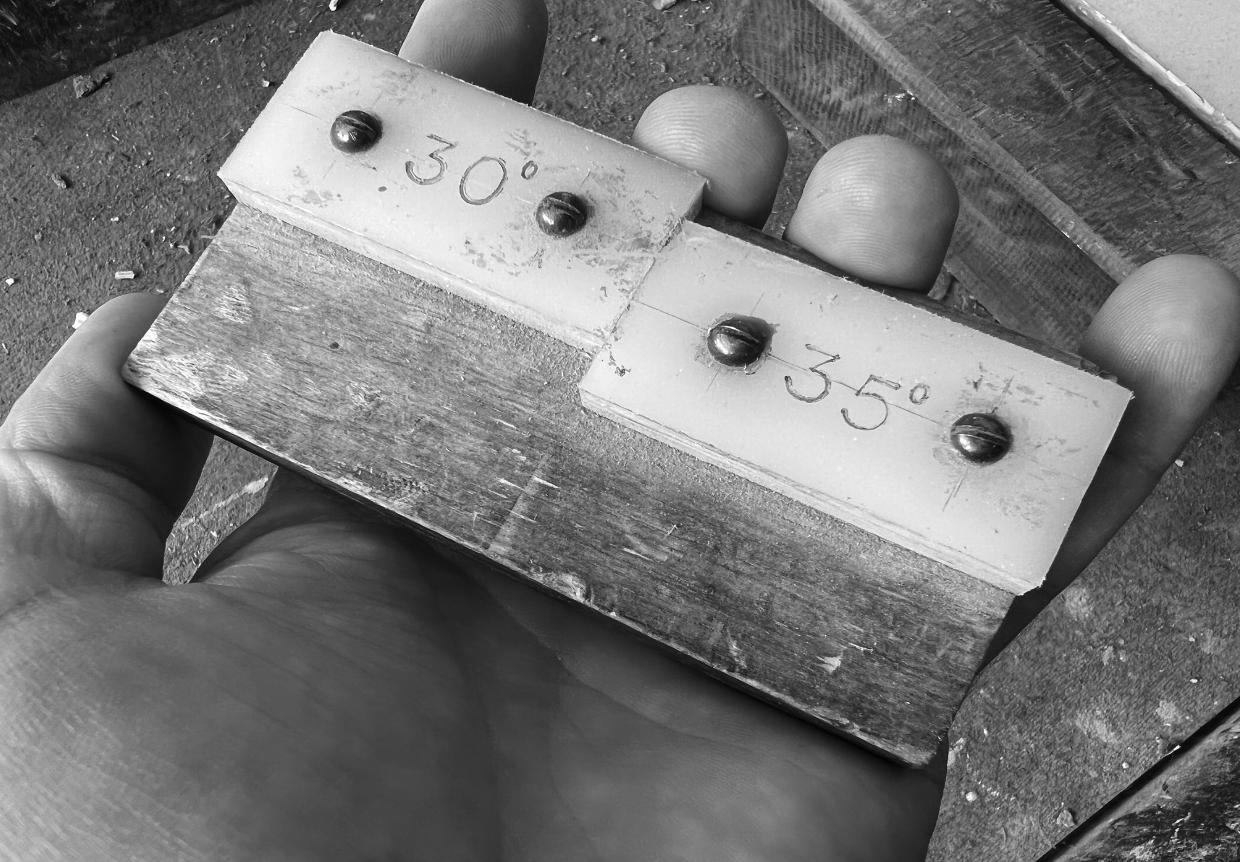
Honing Angles – the Argument for Fewer (or One)
Most sharpening experts steer you toward using a wide variety of angles for different jobs in the workshop. Lower angles for paring tools. Higher angles for chopping tools. And soon you are engraving all the sharpening angles on all your tools and doing more sharpening than woodworking.3
In my experience, the sharpness of the edge is more important than the angle (within reason). A 25° paring chisel and a 35° paring chisel will both do a fine job when really sharp.
When I realized this, I decided to see if I could hone and polish all my tools at 35° and be happy. That was about 10 years ago, and I remain committed to this simple approach. I am sure there are tools out there on the fringes that won’t work with a 35° hone and polish, but I have yet to encounter them.
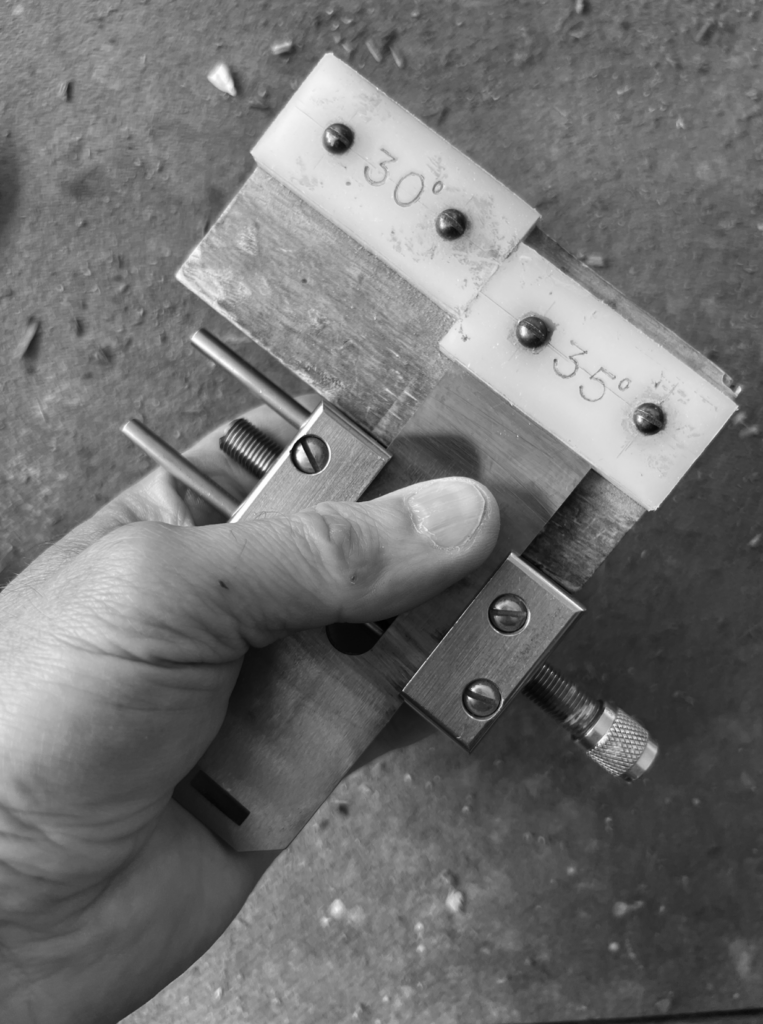
So I have a block of wood with a stop on it. I put the tool in my honing guide, I press the guide and blade against the stop block, then I tighten the guide. I am ready to sharpen. (Making a setting block is simple. Use a school protractor to set the blade to the correct angle in your honing guide. Then screw a stop to a block of wood that matches that projection.)