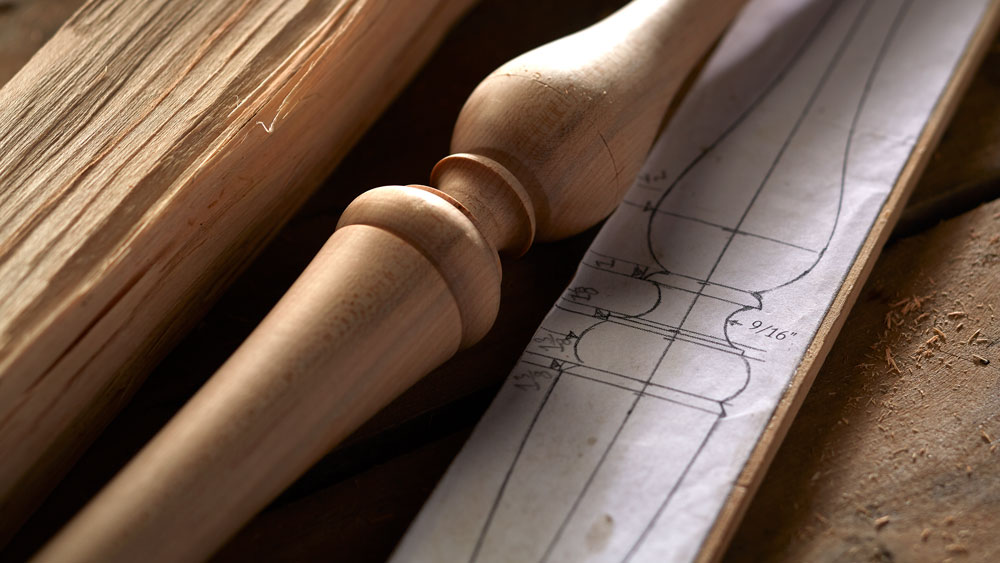
Turning spindles for chairs, settees or staircases requires a small set of tools and a focused group of techniques. Most furniture makers have little need for the tools and techniques of turners who make bowls, platters and art pieces.
That’s why chairmaker Peter Galbert designed this new video “Spindle Turning for Furniture,” which focuses entirely on the needs the furniture maker. Peter has taught hundreds of people to make chairs and has honed his turning instructions for people who have had little or no experience on the lathe.
Much like his book, “Chairmaker’s Notebook,” Galbert has managed to distill a seemingly complex endeavor – learning to turn from scratch – into a series of understandable skills and simple shapes that you create on the lathe.
Once you understand how to make these shapes – coves, beads and flats – Peter shows you how to combine these shapes. You’ll be shocked at how these simple shapes can be combined into beautiful and complex finished pieces.
One of the unique aspects of this video is that Peter spends a significant amount of time showing you how things go wrong during a cut and how to get out the trouble spot with minimum damage. He demonstrates these troublesome cuts, shows you the warning signs and then offers an escape route.
The video clocks in at almost four hours and covers everything you need to get turning spindles. Customers who buy “Spindle Turning for Furniture” will be able to stream the video on demand with an internet connection at any time, and can download the entire video to watch it on virtually any device (the video is 4gb). The video is free of Digital Rights Management (DRM) and costs $47.
Spindle Turning for Furniture from Christopher Schwarz on Vimeo.
Here are the major chapters covered in this video:
Materials
How to select stock for straight grain, how air-dried and kiln-dried woods behave differently, how wet wood and dry wood turn differently, what you need to know about moisture content.
The Lathe and Tool Rest
How to set up your lathe for spindle turning, choose the right centers, reduce vibration, select the correct speed.
Cutting Tools
How to select the tools for spindle turning: parting tool, large roughing gouge, 1” roughing gouge, skew, fingernail spindle gouge, bedan tool.
Tuning and Sharpening
How to get the proper shape on a grinder and then hone with diamonds.
The Concepts in Cutting
Scraping v. shearing, understanding relief angles.
The Major Skills
Cutting long grain v. end grain, learning to combine these two skills to cut coves and beads.
Tool and Body Movement
Learn to move the tool and body to end up in a place of stability.
Putting it all Together
How to combine these basic skills to make a baluster leg, armpost stretcher and stile.
Design
How to combine shapes of different sizes to produce a pleasing result.
— Christopher Schwarz
Like this:
Like Loading...