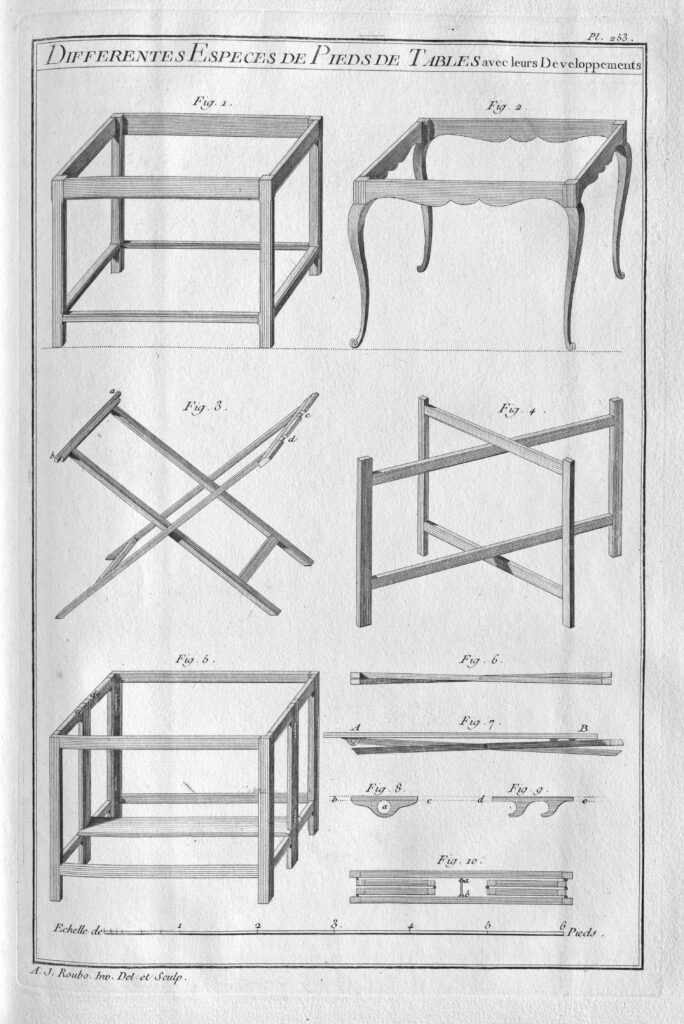
The following is excerpted from “With All the Precision Possible: Roubo on Furniture,” by André-Jacob Roubo, translated by Donald C. Williams, Michele Pietryka-Pagán & Philippe Lafargue.
Representing a decade of work by an international team, this book is the first English translation of the 18th-century masterpiece: “l’art du Menuisier” by André-Jacob Roubo. This, our second volume, covers Roubo’s writing on woodworking tools, the workshop, joinery and building furniture.
In addition to the translated text and images from the original, “With All the Precision Possible: Roubo on Furniture” also includes five contemporary essays on Roubo’s writing by craftsmen Christopher Schwarz, Don Williams, Michael Mascelli, Philippe Lafargue and Jonathan Thornton.
“Roubo on Furniture” is filled with insights into working wood and building furniture that are difficult or impossible to find in both old and modern woodworking books. Unlike many woodworking writers of the 18th century Roubo was a traditionally trained and practicing joiner. He interviewed fellow craftsmen from other trades to gain a deep and nuanced view of their practices. He learned to draw, so almost all of the illustrations in this book came from his hand.
After Beds and Seats, Tables are the most ancient pieces of furniture, or at least the most useful. The number of Tables currently is considerable. There are Tables for the kitchen, Tables for eating, game Tables, Tables for writing, dressing Tables, night Tables, Bed stands, etc. which are composed of a top and of several legs, and which do not differ except in their size and the shape of their top or in their legs. That is why, before entering into any detail on the subject of these different Tables (which you can consider as being three different types, namely dining Tables, game Tables and writing Tables), I am going to address the different legs of these same Tables in general, so as not to repeat it when I come to their particular detail later.
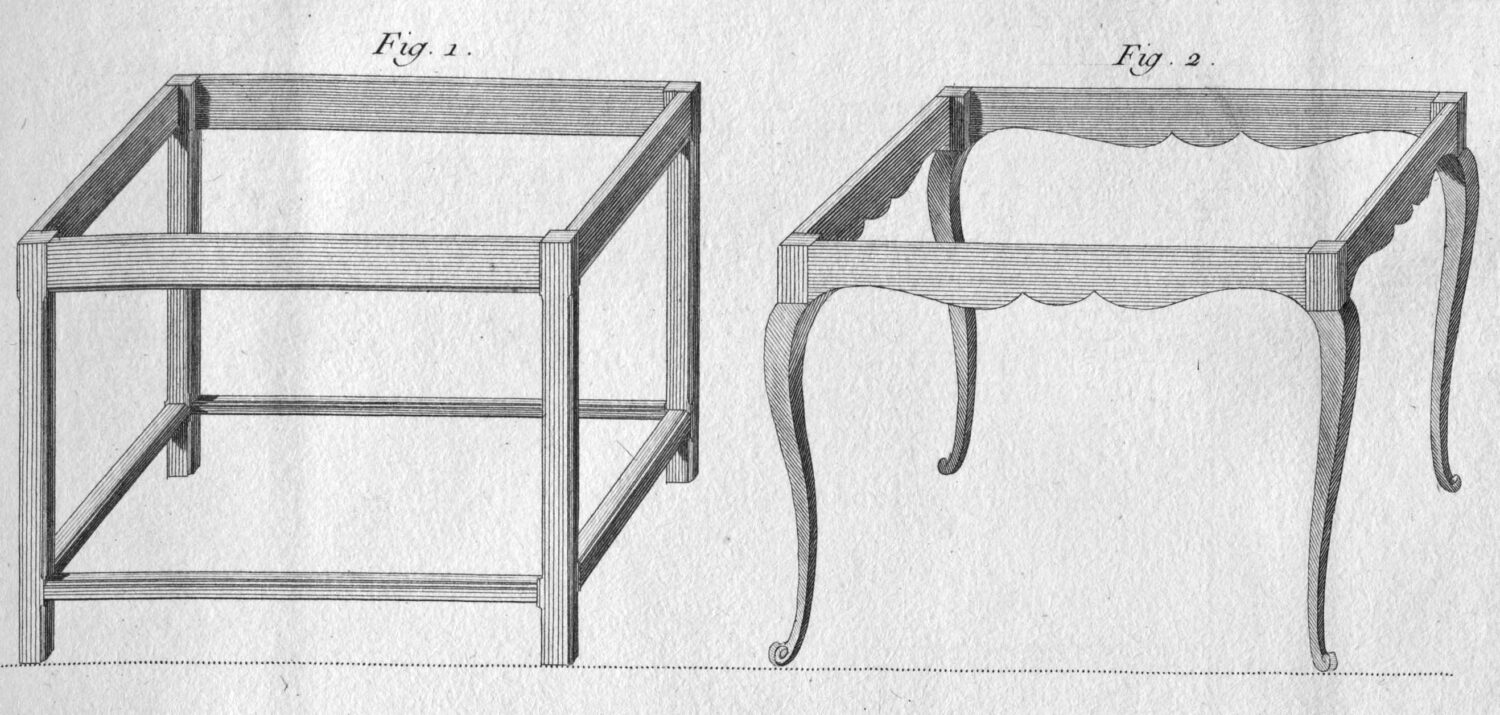
The legs of Tables are of two types, namely those which are immobile, as in Figs. 1 & 2, and those that fold, like those in 3, 4 & 5. In the first case, the bases are composed of four uprights, of four cross-pieces [aprons] at the top and of four others [stretchers] lower down, as in Fig. 1, which is the most solid way to make legs for Tables. Sometimes you put there only two cross-pieces [stretchers] at the ends with a brace in the middle. Or even two stretchers at the ends and one on its rear side, such that there is one side free for providing access for the user’s legs, which is necessary for writing Tables and dressing Tables.
These sorts of legs are, as you can see, very solid. However, we often prefer those of the serpentine leg, represented in Fig. 2, which, although less solid than the first, have the advantage of being less heavily decorated and not to bother in any way those who are seated around it, whether for playing or writing; [this] is to be highly considered, especially when there is no need for much strength or they are not subject to changing place frequently. Because in the latter case, you would need legs like in Fig. 1, unless the Tables being very light, like little writing Tables, game Tables and others of this type.
The legs of folding Tables are of two sorts: namely those in x, whether in elevation, as in Fig. 3; whether in x in plan, like Fig. 4; and those of a folding frame, like Fig. 5.
In the first case, Fig. 3, these feet are composed of two frames assembled with a cap at the end, which would be about 2–and-a-half feet in length each, with a width equal to that of the table, less 2 to 3 thumbs, according to the greater or less width of the latter.
The width of the legs that I speak of should not be taken from outside of the uprights, but from the ends of the cross-pieces at the cap, at the end of one of which you make some dowels, a, b, which move in the hinges attached to the top of the table, which I will speak of next.
The frame that holds the dowels should be the narrowest so that in rounding off the latter, some shoulder remains in the mortise that receives the upright. One could not do this to the other frame, unless by moving it back a lot and consequently to reduce/narrow the frame on the interior as much as the exterior, and diminish at the same time the seating of the leg, of which it never has too much in the case being questioned here.
The two frames of the legs of the Tables that I just described are held together in the middle of their length by an iron pin which enters into each of the uprights at about the middle of their width, which requires that one not peg the wider frame after having placed the [iron] pins, which at 2 to 3 lines in diameter [will] suffice for giving all the firmness suitable.
I just said that you place the pins in the middle of the length of the frame. However, if you wish to give more spread to the leg, you could place them a little bit higher, which you do with no other change than to augment the length of the uprights a little. That is why when you make these sorts of legs, you [will] do very well to draw them in elevation in order to have the exact length of the uprights, the place of the hinges, Fig. 8, [& some racks] Fig. 9, which are attached under the table, as you can see in Fig. 7, which represents the leg folded under the table AB, which extends by about 5 to 6 thumbs at the end, at least normally.
The hinges, Fig. 8, (which Joiners improperly call pins), are made of beech, about a thumb’s thickness and from 5 to 6 thumbs in length; in the middle of which, and about 6 lines from the bottom, that is to say, from the straight edge, you drill a round hole a of about a thumb in diameter into which enters the pins of the crossbar of the leg. These hinges are attached under the table with some nails, which is the most normal way. However, it is much better to make them enter into a notch [that is] the thickness of their cheek in the underside of the table, [as] indicated by line b–c. This is not only more solid, but makes the top of the cross-piece of the frame support equally along the entire width of the table.
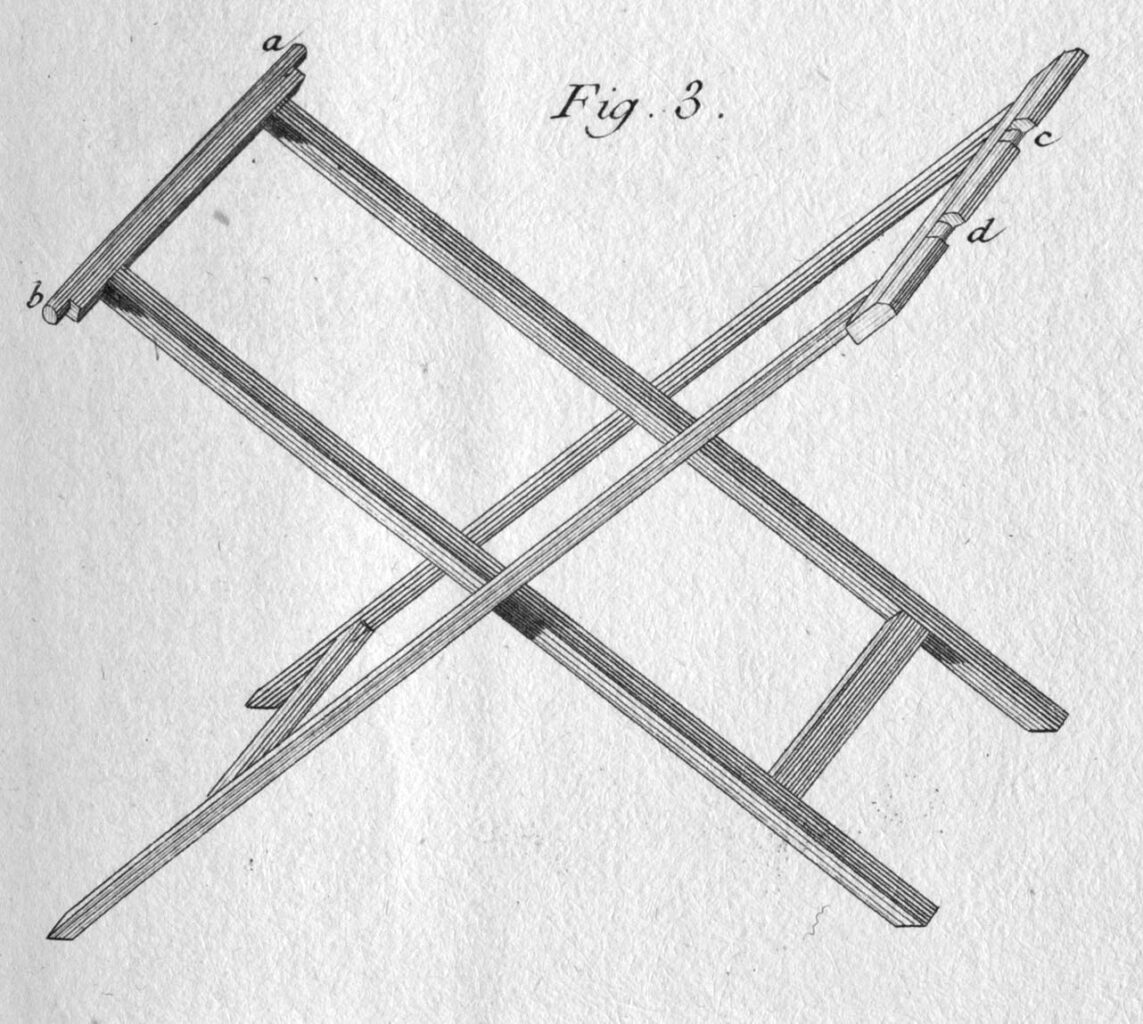
The racks represented in Fig. 9 are made of the same wood and of the same thickness as the hinges and are attached under the table with some nails, as with the latter. One is required to make some notches c–d, Fig. 3, into which enter the cheek of the rack. It would be good to make this enter into the notch in the tabletop of this same thickness, so that it attaches more firmly, and you are not obliged to make a notch in the crossbar of the leg frame, which conserves all its strength. However, as these notches serve to hold the leg in place, or at least to prevent it from varying, you can let the rack project by about 2 lines from the edge of the tabletop, [as] indicated by line d–e, which removes less of the strength of the crossbar and is sufficient to prevent the foot from varying. The racks normally have two notches, f & g, [NB: these elements are not present in the plate] to allow you to raise and lower the table as you judge appropriately, which you do by moving the cross-piece of the frame from one notch to the other, noting that the notch farther away is positioned such that the leg be at its normal height, which is for all dining Tables (where these legs are normally used) from 25 to 26 thumbs on the bottom of the table.
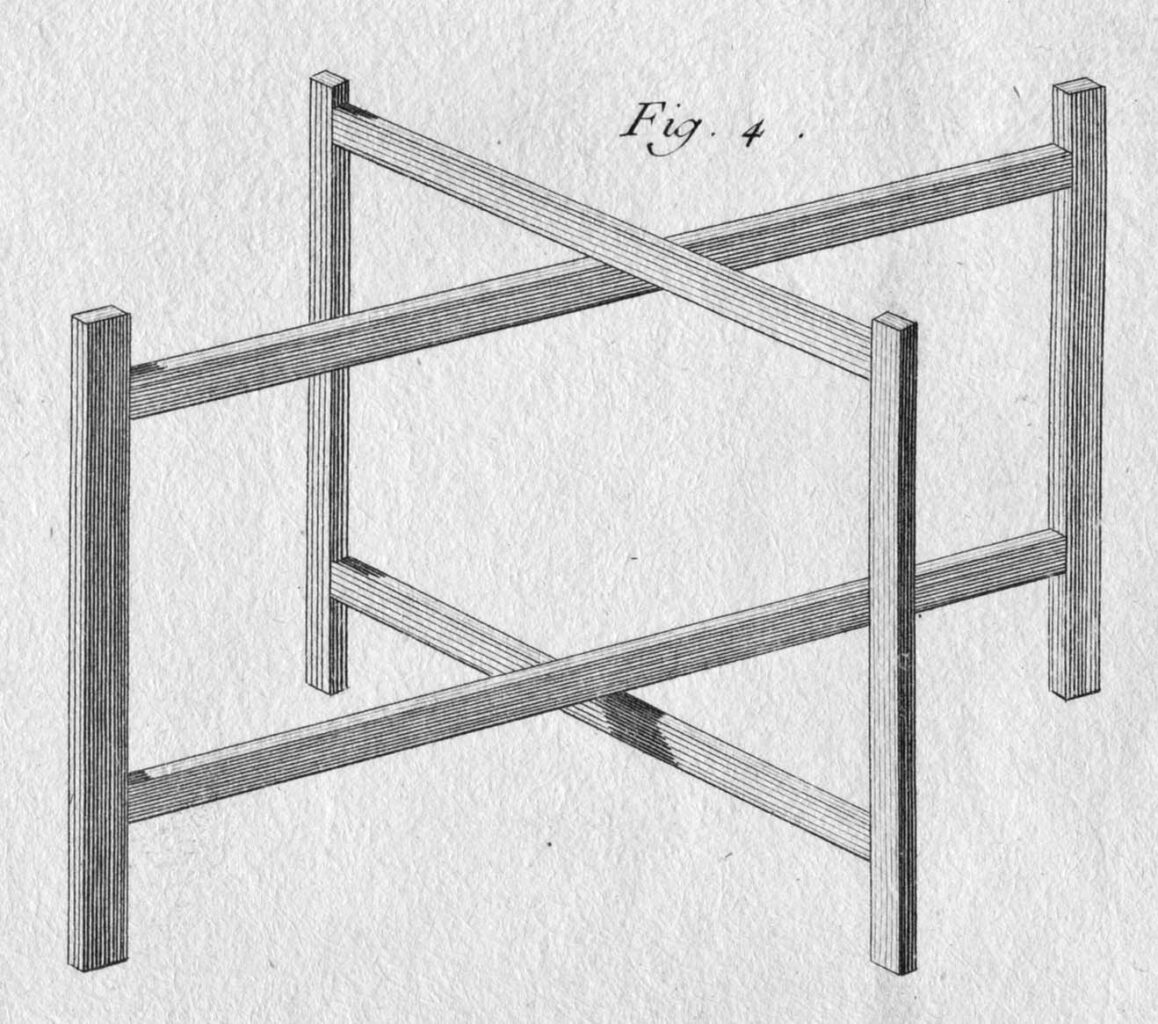
These sorts of legs are not used except for dining Tables of average size and are otherwise inconvenient and less solid, [with] their legs interfering with those who are placed around it. That is why one should prefer them in [an] X on the plan represented [as] in Fig. 4, which are the most solid, less awkward and less complicated, although constructed rather in the same manner, as you can see in this figure, of which inspection alone is sufficient.
The top of the uprights of this sort of leg should project past the crossbar by about 9 lines or 1 thumb, which is necessary to preserve the shoulder. This projection is necessary for entering into the notches that you put on the underside of the tabletop, so as to hold the leg in place. Sometimes you do not put a notch on the underside of the table, but you use some cleats into which enter the end of the uprights.

These sorts of table legs are very convenient for a dining table of a certain size because they do not interfere in any way with those who are seated around it and they take little space when folded, as you can see in Fig. 6, which represents this leg completely folded and viewed from above. This is preferred to all others for dining Tables of average size. What’s more, these feet are normally of a very simple construction and are consequently less costly, which is one more reason to prefer them.

Other folding legs are required, much more complicated than those that I just spoke of, but which are at the same time more solid. The leg represented in Fig. 5 is composed of six frame sections, or better said, of four – two on the side and two at the ends – which each break into two parts in the middle of their width. These frames are closed by pinned hinges on the inside on the frame and in the middle of the two outside. When you wish to fold them, you make them move toward the inside of each side, which make these fold thus, hardly 5 thumbs of thickness, as you can see in Fig. 10, which represents this folded foot held in place by a hook of iron ab, which you can remove when you wish to open it.
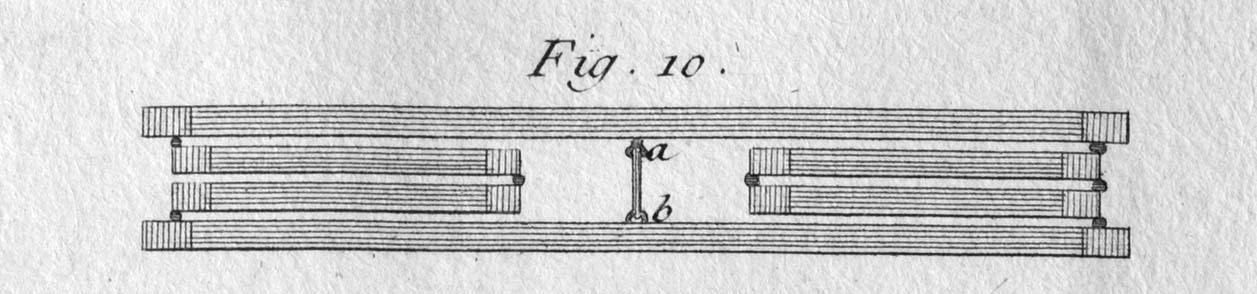
When this foot is open, you hold it in place with a flat iron hook, c–d, Fig. 5, which is placed behind the break in the middle. We also have the custom of placing there a movable brace, which is nothing other than a board of a length equal to that of the leg, and large enough so that it can hold the two uprights in the middle which enter into the notch in the ends of this spacer, which sometimes you make of assembled braces to make it lighter, like the campaign Tables represented in Fig. 6, Plate 251.
These sorts of legs are very solid and greatly in use for dining Tables of a medium size, of which the large projection over the leg [is] made such that it cannot harm those seated around the table.
There are serpentine legs, like Fig. 2, which fold in the same way as those that I just spoke about; that is to say, they fold in the middle of the cross-pieces of the ends, which instead of a tenon, have only a tongue-ending [like a wooden key], which enters into the serpentine leg on which they are tightened.
We also make a tongue at the fold in the middle of these crossbars and you note to make there a shoulder above and below so that they are more solid. These types of legs are frequently used, however they are less solid, no matter the care that you take when closing them. One should prefer the legs with a folding frame, Fig. 5, for large Tables or even that represented in Fig. 4 for small ones.
The size of the leg of Tables’ frames varies from 3 feet in length by 2–feet-3–thumbs in width up to 6 feet by 4–feet-6 thumbs by a height of 25 to 26 thumbs, which is general for all dining Tables. This cannot be otherwise since this height is determined by that of the person seated there, below the elbows of which the top of the Tables must be flush, at least for those of a normal size, which ordinarily is 26 to 27 thumbs in height from the top of the Tables. As to the size of the wood of these legs, 10 lines or 1 thumb thickness suffices, by one–thumb-and-a-half or 2 thumbs, and sometimes 2–thumbs-and-a-half for the width of the uprights, according to the size of the legs. Their crossbars should [proportionally] be a bit larger than the uprights, especially those that meet at the end of the latter so as to conserve the strength of the assemblage.
There you have in general the detail of all the different types of table legs in use for both dining Tables and Tables for games and writing, which, with some small changes, are always of the same form.