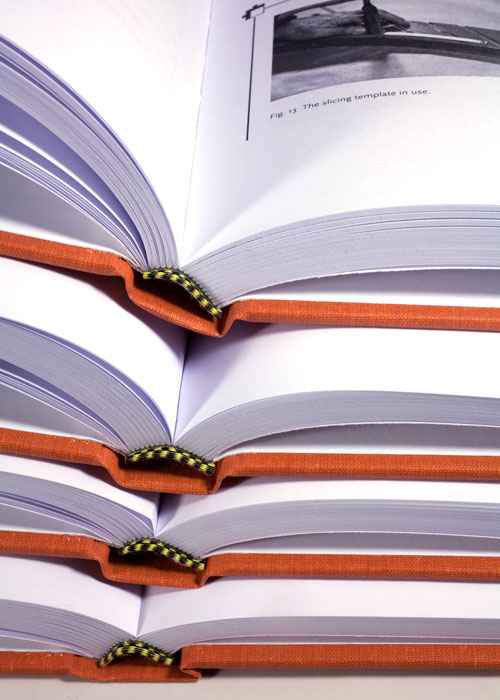
When I left the corporate publishing world, I stopped wearing a wristwatch everyday. In fact, I don’t think I’ve worn one this year. This is, of course, a symbolic gesture. We won’t release a book until we are happy with it.
So I can’t ever say when a certain title will be released. However, here are the projects we are working on now and in the coming months.
“Windsor Foundations” (a tentative title) by Peter Galbert
I’m about halfway through editing this book. As a woodworker who loves chairmaking, I can say that this is the best book I have read on the topic. Peter is able to explain complex subjects with clarity and just a few words. Plus, he is drawing all of the illustrations for the book (and there are a ton of them).
“Princips de l’Architecture” by André Félibien, translation by Brian Anderson
This important French book pre-dated Joseph Moxon and explains processes and tools not shown in Moxon’s “Mechanick Exercises.” Brian is finishing the translation, which should be in my hands in a few weeks. Read more on this book here.
“Roubo on Furniture” by Donald C. Williams, Michele Pietryka-Pagán & Philippe Lafargue
The translation of this book is complete and the edited sections are now flowing to me. The scope of this book is remarkable. I think you will find it was worth the wait. We will again publish a standard edition and a limited deluxe edition of this book. I don’t have any more details on pricing or availability.
“Calvin Cobb: Radio Woodworker!” by Roy Underhill
The text is complete and Megan Fitzpatrick is finishing her first edit. We are on the verge of selecting an illustrator. Right, Megan? This book is on track for release in the fall.
“Furniture of Necessity” by Christopher Schwarz
I’m taking the first load of furniture up to the engraver on Saturday. So look for an update on this title in the next week or so.
“The Woodworker: The Charles Hayward Years” by Charles Hayward
This project has been going on for as long as our Roubo translation. We have acquired the rights to publish about 500 magazine articles written and illustrated by Charles Hayward when he was editor of The Woodworker magazine in England. The book will cover joinery, tools, casework, carving, turning and traditional design. The goal is to have this massive tome released by the end of 2014, but you’ve heard that line before.
“Virtuoso: The Tool Chest and Workbench of H.O. Studley” (tentative title) by Don Williams
This book will be out this time next year. That is all.
We also have three other titles that I haven’t announced yet but we have completed contract negotiations with the authors. One of these books is a do-it-before-you-die project for me. So our 2015 is booked up and we are already working on the lineup for 2016.
— Christopher Schwarz
Like this:
Like Loading...