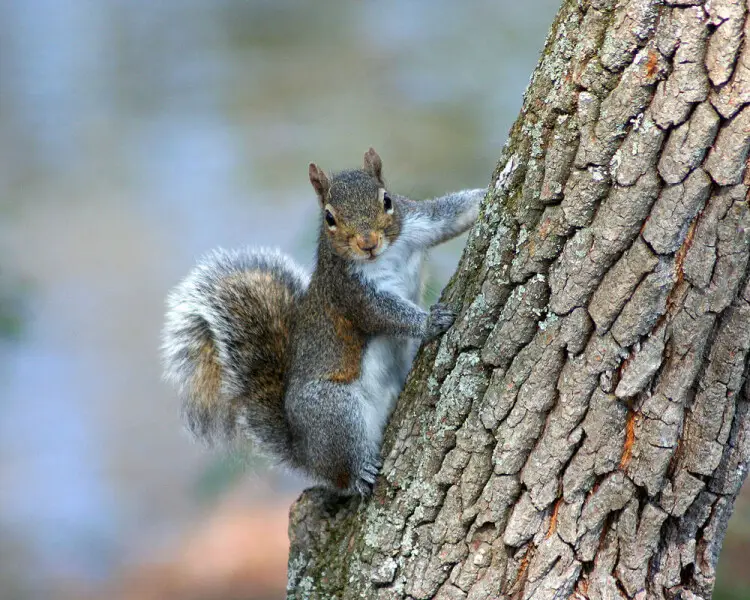
Right after breakfast, Amelia helped Amos, her grandfather, bring in enough firewood to last for several days. Snow was expected in a day or two and he wanted to be prepared. Amelia loaded baskets into her grandfather’s old garden wagon and helped him unload and stack the wood inside the cabin. After several trips her grandfather said, “That’s good. Now, sit and rest and get your feet back under you.”
Just about mid-morning, Amelia was at the table with a book propped up before her. “How commited are you to that book? asked her grandfather. “Not much, “ she answered. “How about you go out and find me some crooks for spoons. Take the big path into the woods. After about a 10 minute walk you should see a patch where some branches came down a while ago. You know what to look for. When you get back we’ll go into town for lunch at the Thursday Market.” “Sounds good to me,” answered Amelia. She got her backpack and a big canvas tote. She grabbed a small axe and headed for the back door. “Have you got the axe?” he called. “Yep, got it,” she answered.
Amelia crossed the open field behind the cabin and stepped into the big path. Within a few minutes the woods were thicker and the light dimmer. Deep in these woods there were old-growth sections with enormous trees that were protected by law. She had not yet found the patch her grandfather mentioned, instead, she was at a point where the path forked, something she didn’t remember from previous walks in the woods. She took the right fork. The trees loomed above her and the wind came up. Amelia pulled up the hood of her jacket but the wind caught it. With her hand shielding her eyes she leaned forward and kept moving. The wind grew stronger and the light dimmer. The air was filled with debris. Tree branches creaked and squeaked as they moved with the wind. She stopped and the wind lessened as did the creaking. The squeaking, however, was louder than ever. She looked up and saw a gray squirrel scrambling down a giant white oak tree. It was doing the squeaking and it looked angry.
When the squirrel was almost at Amelia’s head height it stopped. It half squinted it’s eyes, pointed at her and yelled, “Drup that ass!” Puzzled, Amelia answered, “Drup my ass? Who are you to tell me to drup my ass? Wait, what does that even mean?” The squirrel dropped from the tree and bounded over to the top of a nearby boulder. It took a deep breath and said, “No asses! No asses!” Amelia also took a deep breath and, as she smacked one side of her butt, asked, “Well, squirrel, how am I supposed to walk without my ass?” The squirrel chipped and chucked and almost fell off the boulder. “Are you laughing at me?” demanded Amelia. “Yez!” came the answer between more chips and chucks.
The squirrel regained its feet, pointed at Amelia then pointed to his eye. “OK, you want me to watch, go ahead,” she answered. The squirrel put its paws together and moved its little arms up and down in a chopping motion. This was followed by it crossing its arms to form an X. Amelia watched closely and guessed, “No chopping? No chopping the trees?” The squirrel repeated the motions and finished this second try by pointing at Amelia’s right hand. She tried again, “No chopping, no,” she looked at her right hand and the light turned on, “no axes! No asses! No axes!” She bent over laughing and looked over to see the squirrel jumping up and down squeaking, “Yez!” Amelia put the axe in her backpack and as she did noticed the wind had stopped and the trees were still.
Looking at the squirrel, Amelia explained, “I came looking for wood for spoon carving. “Spoons?” questioned the squirrel. “Yes, wood for spoons,” replied Amelia. “Crooks. Come with me, Dummy,” instructed the squirrel. “Hey, my name is not Dummy! It’s Amelia!” she complained.
The squirrel led Amelia to an area where there were plenty of fallen branches. She was able to find several good crooks and some larger pieces that might work for carving bowls. After loading them into a big canvas tote she looked up to where the squirrel perched on a branch and said, “Thank you for showing me the way. I apologize for bringing the axe into the forest.” The squirrel nodded and pointed towards the path, “Time to go.” “Do you have a name?” she asked. The squirrel nodded. “What is it?” The squirrel tilted his head one way and then the other as though he was contemplating her question. Finally, he made a zipping motion across his mouth and took off up a tree. “You little devil!” Amelia yelled, followed by, “Oh!” as a large spray of pine needles landed on her head.
Amelia wasn’t sure what had just happened or if it had happened. She didn’t quite trust herself and her reactions to new things. She had been in a bad car accident in the spring and had a slow recovery. Her grandfather had invited her to spend a couple months with him to, as he put it, get her feet back under her. She was feeling stronger and more balanced since arriving at his cabin, but it was her head injury that caused her to doubt what she had experienced in the woods. She decided not to tell her grandfather about the squirrel.
As promised, her grandfather took her into town for their lunch and to visit the farmer’s market. After lunch, Amos went in search of some vegetables, while she headed to see Sarah, the basket maker. She found Sarah at her usual spot in the market and greeted her with, “I’ve got some sassafras for you, Sarah.” “You must have been reading my mind, Amelia girl!” exclaimed Sarah. “Just in time! A couple of people have been asking for my sassy baskets to give as Christmas and New Year gifts.” Sarah added the fragrant sassafras around the rim of baskets to make make them sassy and spicey, which happened to be a good description of Sarah herself. “Can you sit with me for a while?” asked Sarah. “Yes, of course and I want to hear all the gossip!” answered Amelia. They were close to the same age and Amelia had learned the rudiments of basket making from her new friend. Amos found the two of them with heads together giggling over something Sarah had just said. As Amelia and Amos left, he turned back and called to Sarah, “We’ll see you at Christmas dinner!”
By the time they arrived back to the cabin it was almost dark. “I can’t get used to it getting dark before 5 o’clock,” said Amelia. “It creeps up on you, doesn’t? Come on, let’s have an early supper. I’m thinking pancakes,” answered her grandfather. Over supper, her grandfather told her they had one more thing to do that evening. They were going into the woods. “Why? It’s dark and cold!” exclaimed Amelia. After the episode with the squirrel she wasn’t eager to go into the woods. “It the long night, the winter solstice, and it’s a tradition of mine,” answered her grandfather. “And, I think it will be good for you. So, dress warmly, we won’t be back until late.”
They left a couple of hours later. Amos pulled his garden wagon loaded with bags he had pulled from the root cellar. Her grandfather shrugged off her question about the bags with, “Amelia, sometimes you just have to go with the flow and see what happens.” As they crossed the field behind the house and were well away from any lights, Amelia looked up and exclaimed, “The stars are so clear tonight! There’s Orion and the Pleiades and Aldebaran!” “Wait until we come out of the woods later tonight. It will be even more spectacular,” answered Amos. “Come along, hold the lantern up. We’re almost at the path into the woods.”
Amelia held the lantern higher as they entered the woods. It was quiet and dark, very dark and she said so. “Amelia,” her grandfather started to say and she cut him off with, “I know, I know, go with the flow, I’m flowing, I’m flowing.” Amelia thought they were going to walk the entire network of paths until Amos stopped at a small clearing. Taking some wood from the wagon he lit a small fire in a pit. “Grandpa, is that allowed?” she asked. “There is no wind, it will be fine,” he answered. “Take the bags out of the wagon and put them near the sitting boulders. Then, grab one of the cushions, have a seat and get comfortable,” he directed. She did as she was told and waited for him to also take a seat before asking, “Now what?” He answered with, “Shhhh.”
Amelia waited. The quiet was broken by a scrabbling sound coming from a nearby tree. A few seconds later a squeaky little voice spoke from the boulder closest to her grandfather. “Good evening Amos, you brought Dummy with you.” Before her grandfather could say a word, Amelia jumped to her feet, pointed at the newcomer and exclaimed, “You! I wasn’t imagining you!” Then she turned to her grandfather, “You sent me into the woods this morning knowing I would meet him, didn’t you?” “Only if you entered the old part of the forest and were carrying an axe,” Amos replied. He was sitting on his boulder, arms crossed with a self-satisfied smile on his face. “Amelia, please meet Wipunk, guardian of the old forest and my companion for our annual meeting on the long night. Wipunk, Amelia is my granddaughter.” Wipunk was dancing from foot to foot. “Amos, I made a mistake with the words today. I told Amelia no asses, I meant no axes. She thought I was nuts!” Amelia told Amos the details of the squirrel’s pantomime and Amos and Wipunk burst out laughing. She added, “I thought I was nuts.” Wipunk considered her for a moment and said, “It is okay to sometimes be nuts.”
Still looking at Amelia, Wipunk explained, “This is the long night and on this night we have a fire and we share food. Amos, what did you bring for the long night?” Amos started to open the canvas bags. “Acorns from white and red oak, hickory nuts, late-harvest apples and pears, a few berries, Catawba grapes and cabbage leaves,” he answered. “Cabbage?” queried Wipunk. “Rabbits and deer eat cabbage. Try some,” Amos answered and handed Wipunk a small piece. Wipunk took the cabbage and sniffed it, gave it a lick and took a small bite. “Not bad,” he announced. Amos handed a small bag of almonds to the squirrel. “I didn’t forget your almonds for the long night.” While Wipunk started on his almonds, Amos and Amelia spread the acorns and other goods outside the circle of boulders. As they did so, Amos explained, “By morning, all of this will be eaten or stored away.”
When they sat back down, Wipunk looked at Amelia. “The long night is also when we tell stories. Amos, Amelia should hear the the story of how you met my ancestor.” Amos had a strained look. He rubbed his face with one hand as though he was removing a protective mask. He looked at Amelia, his eyes sad. “I suppose I must,” he said. “Yez, Amos, you must,”replied Wipunk. Amos began, “It was twelve years ago, not long after your grandmother died. I was in a bad way.”
~~~~~~~~~~~~~ * ~~~~~~~~~~~~~ * ~~~~~~~~~~~~~
Amos was struggling. His dear Anna had died several months before and he was bereft. The funeral, the visits by friends and neighbors, the memorials and the legal paperwork were finally done. He was alone and without her for the first time in over fifty years. His grief descended and held him for days.
Late one afternoon, he was sitting in his favorite chair looking across at her old chair and thought Anna would have told him to get outside and walk away his bad mood. “That’s what I’ll do!” he announced to the empty house. He got his backpack ready, grabbed his hiking stick and again announced, “I’m going outside!” Going out the back door, he walked through the garden and was about to started across the field when he stopped. A white-throated sparrow was under the laurel bush searching under some leaves. “When did you get here?” he asked. He looked around and realized he had not only lost his wife, he had lost the autumn. Although it had happened around him, he had not noticed the leaves turning colors then dropping, or the October arrival of the little sparrow from Canada. Normally, he paid close attention to the natural world and kept a journal filled with notes on animal life, what was eating which vegetable in the garden and the weather. “I have to get myself together. Anna would expect me to do better,” he said as he shook his head and started across the field heading towards the woods.
Walking through the woods always lightened his mood, but that afternoon felt different. Well, I haven’t been here in a few months, he thought. It seemed darker than it should be and he couldn’t find familiar landmarks or pathways. The further he walked, the more disoriented he felt. “Why is it so dark so soon?” he asked aloud. Further along the path he came upon a clearing. There was a small fire pit surrounded by a half-circle of small boulders. Amos sat down on a boulder, checked his watch and saw it was only half-past four. Looking around, he could still see the trees, but the light was closing fast and it was getting colder. Not knowing where he was made him think he might have to stay the night right where he was. The air was still and he thought it would be safe to have a small fire in the pit. He got to his feet and started gathering a supply of wood to keep a fire going.
The light and warmth from the small fire helped him feel a bit easier with his situation. He could relax a little, but not too much. Sitting cross-legged on a cushion of pine needles, he leaned back against the boulder. His growling stomach reminded him he had energy bars, nuts and water in his backpack. He opened a package of almonds and popped a couple in his mouth. As he started to take a few more from the bag he heard a small voice say, “What are you eating?” Without thinking, he answered, “Raw almonds, no salt.” The voice came again, “May I, please?” Amos snapped to. He wasn’t alone! In a panic he jumped to his feet and called, “Who are you? Where are you?” “I am over here, on the other boulder. May I have the almond?” came the answer.
Amos looked over and saw a gray squirrel perched on the furthest boulder. The squirrel had one paw extended waiting to be given an almond. “Did you just talk to me?” Amos demanded, then caught himself, “I’m hallucinating! Yes, I am hallucinating.” He plopped back on the pile of pine needles and started laughing at his situation. “I don’t know about that. May I have the almond?” asked the squirrel as he jumped to the next boulder in the circle. Thinking he would just go with the flow, Amos said, “Sure you can try an almond. Here, take a few.” He put several almonds on the boulder closest to the squirrel. The squirrel picked up one almond, sniffed it, licked it and then took a small bite. His little jaws working fast, he took another bite. Amos counted eight bites to eat the whole almond. “This is good,” said the squirrel as he took up a second almond. After eating a third almond, the squirrel turned to look directly at Amos and asked, “Are you here for the long night?” “Yes, it looks like I am here for the whole, long night,” replied Amos. The squirrel tipped his head to the side and replied, “This is the long night, are you here for long night?” Amos was about to repeat his previous answer when he stopped and said instead, “What do you mean the long night?” The squirrel explained, “This is the long night of the year that follows the short day of the year. On this day I can talk to you. On this night we have the fire and share food. It has been a long time since Old Joe came here for the long night.” By the time the squirrel finished his explanation Amos was wide-eyed and his mouth was hanging open in disbelief. Deep down, he really wanted, no, he needed, this squirrel to reassure him and asked, “So, I’m not seeing things and I’m not crazy?” he asked. The squirrel jumped to the boulder closest to Amos, leaned forward and with one little paw tapped Amos right on the nose, “You are not crazy, just a dummy!”
Amos laughed so hard he cried, then he sobbed until he was laughing again. The squirrel watched and helped himself to the bag of almonds. After Amos recovered, he introduced himself and asked the squirrel if he had a name. “I am Wipunk. The squirrel that can talk is named Wipunk. After we have more to eat and more talk I will show you the way out of the forest.”
~~~~~~~~~~~~~ * ~~~~~~~~~~~~~ * ~~~~~~~~~~~~~
“And that is what he did,” explained Amos. “He showed me the way out. I would see him every time I went into the forest and he would acknowledge me by tossing an acorn or pine cone my way. I asked around and was able tracked down Old Joe, a former ranger. He was well into his 80s and in a nursing home. He spent about a quarter-century of long nights with several generations of Wipunks and he learned the word Wipunk is from the Lenape language and means gray. So, probably, the Lenape word for gray squirrel was somehow shortened to just gray. Old Joe thought there must be some kind of winter magic on long night, magic that made the barrier between humans and nature permeable.”
“Wipunk did one more thing for me that night. I was about to put another piece of wood on the fire when he stopped me. “No, keep that one for spoons,” instructed Wipunk. Old Joe was a spoon carver and Wipunk had learned how to choose a good crook. When I found Old Joe he was still carving spoons and he taught me the craft. The first spoon I made was from the crook Wipunk told me to save. It’s hanging above the stove.”
When Amos finished his story Amelia was very quiet. “I didn’t know you had such a bad time after Grandma Anna died,” she said. “You couldn’t have known, you were a young child,” replied Amos. He continued, “Now you know why the long night and Wipunk have such great meaning for me. It brought me back to myself and helped me become closer to the great healer, the natural world.” Amos reached into his backpack and took out two sandwiches. He handed one to Amelia and unwrapped one for himself. Sniffing the air, Wipunk pointed towards Amelia and asked, “Is that one peanut butter?” She tore off a corner off her sandwich and offered it to the squirrel, “Yes, peanut butter with grape jelly.” Wipunk tasted and then devoured the small piece of sandwich. “Oh, very good! Please bring some next long night, Amelia.” He added, “You will come the next long night?” “I wouldn’t miss long night here with you and Grandpa for the world!” she answered.
Soon it was time to go. They packed the bags into the garden wagon, put out the fire and started homewards. Wipunk rode in the wagon until they reached the edge of the woods. He jumped out and sprang up to the trunk of the nearest tree. Continuing up the tree he called out, “Good Night, Amos and Amelia!” “Good night, Wipunk!” they answered. As they cleared the tree line the sky opened up and they stood still, dazzled by the winter constellations.
“I proposed to your grandmother under a winter sky like this,” said Amos. “With Yeats,” he added. “You quoted Yeats to propose to Grandma!” laughed Amelia, “How did that go over?” “Well, it was the third time I proposed to her. I had to make it extra special,” he said. “When was the first proposal?” asked Amelia. “The last day of ninth grade. She threw her chewing gum at me and ran away,” he said laughing. “It took me a month to memorize the Yeats poem. Do you want to hear it?” he asked. “I sure do. Fire away!” she answered. Amos looked up to the sky and began:
“Had I the heavens’ embroidered cloths,
Enwrought with golden and silver light,
The blue and the dim and the dark cloths
Of night and light and the half light,
I would spread the cloths under your feet:
But I, being poor, have only my dreams;
I have spread my dreams under your feet;
Tread softly because you tread on my dreams.”
Amelia looked at her grandfather and saw he was deep in his memories of his Anna and she waited. Finally, he shook himself and said, “It’s cold! Let’s get home and warm up.”
The next morning a light snow was falling. Tired from the long night, Amos and Amelia took their time over their coffee. Looking out at the snow, Amos said, “One night, a couple of months before my Anna died she told me she had been talking with the angels. It made me worry that she was starting to lose her mind. Now, I don’t think so.” “What changed your mind?” asked Amelia. Amos turned to look at her and had a big grin on his face. “I have been talking to a squirrel and so have you!”

Like this:
Like Loading...