This is an excerpt from “The Anarchist’s Tool Chest” by Christopher Schwarz.
The funny thing is that it was my mad obsession with acquiring woodworking stuff that helped me find a balanced approach to the craft. You see, I became as obsessed with acquiring woodworking books as I was with the tools. I’ve always been a voracious reader, so consuming books on woodworking and tools was natural. (And add to that the fact that I was freelancing at the time as a contributing editor for the WoodWorkers’ Book Club newsletter. That job was a five-year-long force-fed diet of woodworking writing.)
Read enough modern woodworking books, and you might just want to gouge out your eyes with a melon baller. They are all so similar and shallow and filled with idiosyncratic information. I can’t tell you how many times I read the following phrase: “This might not be the right way to do this, but it works for me.”
Something inside my head made me wonder about that “right way” the author rejected.
It just so happened that at about that same time I had a short phone conversation with Graham Blackburn, one of my woodworking heroes. I had a few of Blackburn’s books from the 1970s, and I knew he had a command of woodworking history. So I interviewed him about the origin of the word “jack” in “jack plane” for a short piece I was writing for the magazine.
We then started talking about saws.
During the conversation, Blackburn said I could find the answer to one of my questions in the book “Grimshaw on Saws.”
Huh? I replied.
I’ll never forget what he said next: “You don’t have a copy of Grimshaw, and you’re an editor at a woodworking magazine? Hmmm.”
I was ashamed. So ashamed that I went down to Cincinnati’s public library that weekend to check out Robert Grimshaw’s 1882 treatise on saws. It was sitting on the shelf next to a bunch of other old woodworking books I’d never heard of. I wondered which of those books were also “required reading” in Blackburn’s world. I checked out as many of those cloth-bound books as the library would let me. I went home. I started reading, and I haven’t stopped.
The things I learned from the old books were different than what I expected to learn. I actually expected the shop practices to be different – you know, they had different ways of cutting a mortise, a tenon and a dovetail. But really, not much has changed in the way that steel (usually) defeats wood.
While there are a wide variety of ways to perform every standard operation, the pre-Industrial craftsman didn’t seem to have secret tricks as much as he had lots of opportunities to practice and become swift.
Instead, what surprised me was the small set of tools that were prescribed for a person who wanted to become a joiner or a cabinetmaker.
Joseph Moxon, the earliest English chronicler of woodworking, describes 44 kinds of tools necessary for joinery in “Mechanick Exercises” (1678). For some of these tools, you’d need several in different sizes (such as chisels), but for many of the tools that he described, a joiner would need only one (a workbench, axe, fore plane etc.).
Randle Holme’s “Academie of Armory” (Book III, 1688) has approximately 46 different joinery tools explained in his encyclopedia. An exact number is hard to pin down because some of the tools are discussed twice(for example, mallets, smoothing planes and hatchets) and some tools seem shared with the carpentry trade.
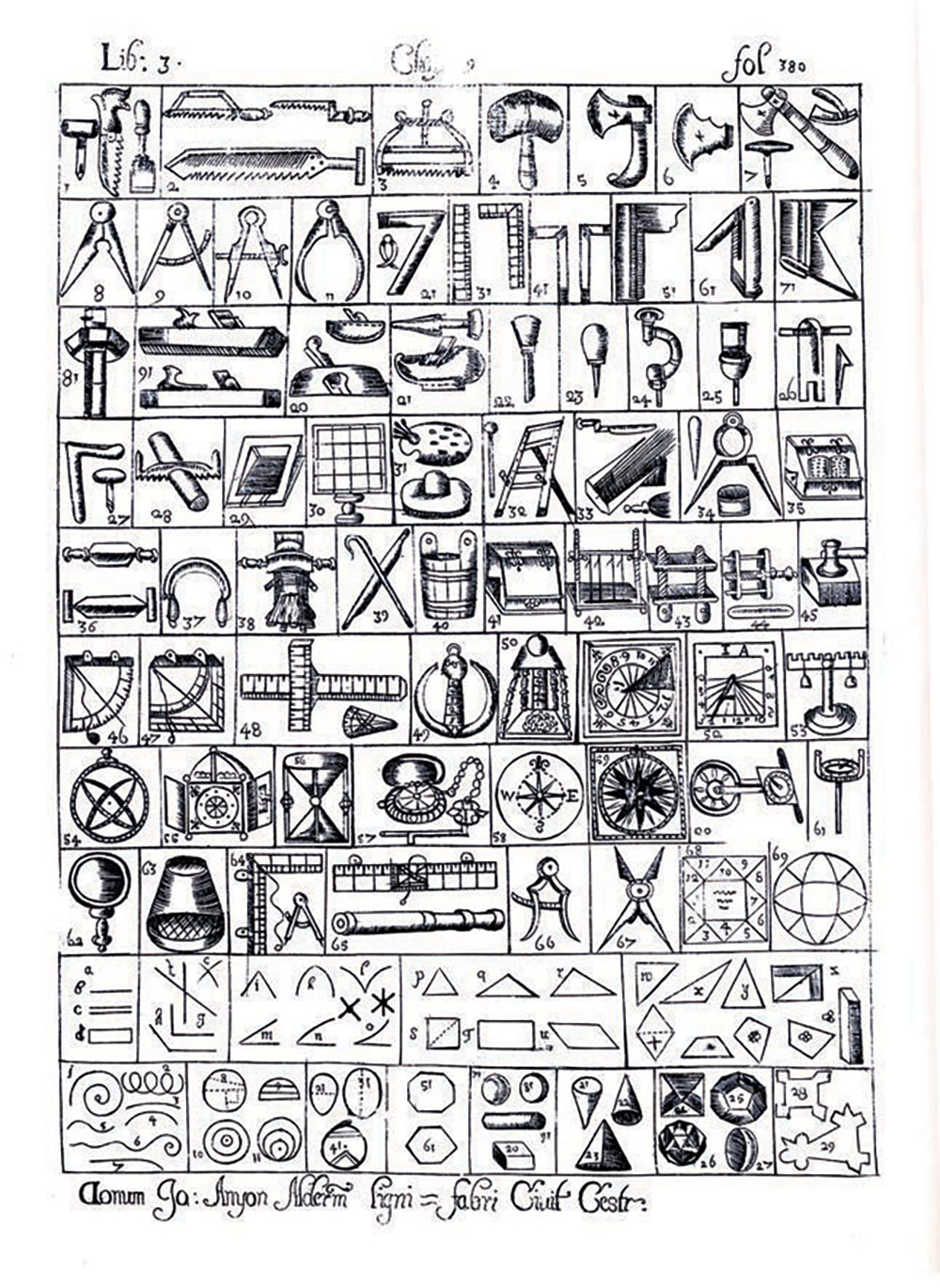
If we jump forward more than 150 years, not too much has changed. The list of tools required by the rural joiner in “The Joiner and Cabinet Maker” (1839) isn’t all that much different from the tool list described by Moxon and Holme. “The Joiner and Cabinet Maker” gives a significant description to about 40 tools used by a young apprentice during his climb to journeyman.
As the Industrial Revolution begins to crank out mass-manufactured tools, the basic list of tools recommended for basic joinery starts to expand. There are more kinds of boring bits available, new kinds of metallic planes (such as blocks, shoulders and routers), plus some new saws, including the coping saw.
By the 20th century, the basic list of tools for joiners stands at about 63, according to books by Charles Hayward, the traditionally trained dean of workshop writers. Still, when I looked at Hayward’s list it seemed rather paltry compared to what was in my shop. (See this book’s appendix for a comparison of these tool lists.)
At first, I attributed these short lists of essential tools to three things:
• Everything in the pre-Industrial age would have been more expensive because it was made by hand.
• The general level of economic prosperity was lower.
• Technological innovation had yet to produce the fantastic new tools shown in the modern catalogs.
But all that was just denial kicking in.
— MB