As some of you will recall, I last reported from Ecuador back in August, when I showed you the workbench that I had completed. Since then…nothing. What happened? Well, as it turned out, a variety of events and situations conspired to the extent that I ended up with virtually no time to do any actual woodworking. I did get started on a project, but wasn’t able to finish before we had to leave.
You will at least be happy to know that the bench found a good home in the workshop of the architect friend who earlier pointed me in the direction of wood merchants in my neighborhood.
And I did learn a few things along the way:
Lesson 1 – Colorado (aka Lyptus®, Eucalyptus grandis x urophylla) is not a hand tool-friendly wood.
Lyptus is very hard, about the same as hard maple or the very hardest of white oaks. And it has interlocked grain, which tears out readily no matter which direction you try to plane it in (even cross grain!). I eventually figured out how to plane it: with my plane set to a 60° cutting angle and taking extremely thin shavings, I was able to achieve a surface that could later be sanded smooth. But removing 1/16″ of tearout a thousandth at a time is not my idea of fun.
The wood reminds me of sapele, which is similarly hard and also has interlocked grain, although it’s more brittle and doesn’t tear out quite as much. Like sapele, it’s very difficult to get a decent finish without a considerable amount of sanding.
Lesson 2 – At some point, a baggage handler will drop your tool case very, very hard.
The damage shown here occurred when the lever cap knob of my Veritas low-angle jack plane punched through the bottom of the tray from below. Given that when the trays are stacked together there is at most 1/2″ of play before the knob contacts the tray bottom, I don’t want to think about how far the case must have fallen in order for this amount of destruction to occur. Fortunately, it appears that all of the tools are okay.
Lesson 3 – An outdoor woodworking shop in Tumbaco may not be the best idea.
This one was completely unexpected, and it’s the fault of these guys:
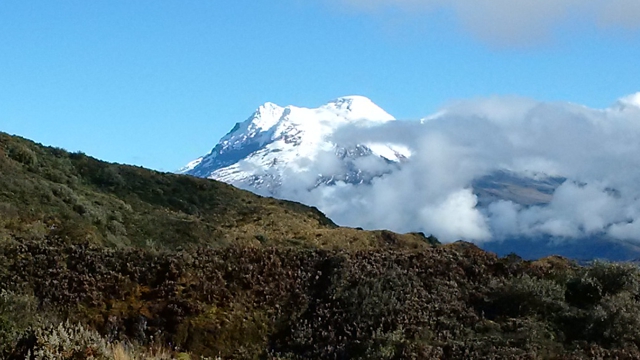
The soil in Ecuador is virtually all volcanic ash, in some places hundreds of feet deep. Very fine, very abrasive volcanic ash. Add to that the fact that the climate in Tumbaco is dry, and afternoons are usually windy, and you begin to see the problem. I would finish up one day and come back the next to find everything covered by a clearly visible layer of ash. Ash that wreaked havoc on my tool edges.
The ash ends up indoors, too. We had a housekeeper that came to clean every week, and still the pile-up of dust near windows and doors was impressive.
I’ll have more to write about our adventures in Ecuador (plus a couple of weeks in Peru) soon, so stay tuned. But for now, I have some pent-up woodworking to attend to.
– Steve Schafer