The first magazine article George Walker ever published appeared in Astronomy Magazine. At the time, he was working a lot of hours as the midnight shift supervisor at The Timken Company, a Canton, Ohio, factory that engineers and manufactures bearings and mechanical power transmission components.
“There was a hole in the middle of this building where they had a transformer that was open to the sky,” George says. “And I’d go out there at two in the morning, and I’d look up through these wires and cables and superstructure and watch Orion pass across the night sky. And I wrote this article about observing the stars amongst the smokestacks.”
No matter how ordinary the circumstances, George is regularly struck by the majesty and wonder of life, the way millions of colorful warblers gather at “a little spit of cottonwoods right on the edge of the lake” (Magee Marsh), as they have for millions of years, to rest and eat before their migration across Lake Erie. Or the way a medieval drawing found in an old monastery can inform his work through the understanding of geometry, even though he can’t read the text, as it’s written in Renaissance Italian or Spanish. Or the way he can now build a beautiful piece of furniture, without plans or a tape measure, using instead a stick, a piece of string and dividers.
George was born in western Iowa, his father, a farmer. His father left farming in the early 1960s and the family moved to northeast Ohio. George grew up in a small suburban neighborhood and spent much of his childhood outdoors, running around the woods, fishing, “being a little bit of a Tom Sawyer.” He had a good friend who lived on a property with a lake, a couple miles away, and the two often could be found in a boat trying to catch turtles. George enjoyed exploring and making things, which ranged from tree houses to electric motors. He enjoyed camping and scouting, and his interest in the outdoors led to lifelong loves of botany, astronomy and birding.
An avid reader ,George did pretty well in school, although he hated English. “My English teachers would flop over dead if they knew that I’ve become a writer,” he says. (His writing includes many magazine articles and two books co-authored with Jim Tolpin: “By Hand & Eye” and “By Hound & Eye,” both from Lost Art Press.)
“I had a high school English teacher who gave me a D just because she didn’t want to see me again,” George says. “She said, ‘I’d give you an F, but then I’d be stuck with you next year. I’ll give you a D so I don’t have to look at you.’ I should track her down and send her a book. It would blow her mind.”
English grades aside, George enjoyed historical fiction, “and like any kid I liked the kind of adventurous whatever, the swashbuckling stuff there was to read as I kid,” anything that had a little bit of truth to it mixed with adventure.
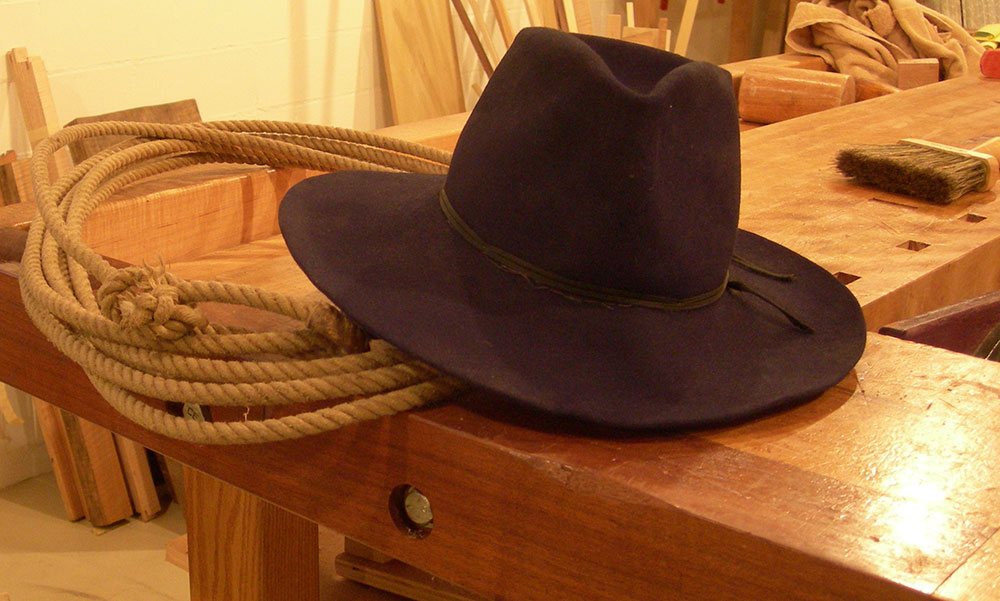
In 1975 George graduated from high school and decided that he couldn’t bear to live in Ohio another minute. So he headed out west to work as a cowboy on a 17,000-acre ranch near Phillipsburg, Montana. “Most of my time was spent on a tractor or driving around in a beat-up 1963 red Studebaker Lark station wagon,” he says. “I did learn how to ride and rope well enough to not embarrass myself.”
Although George had worked on farms while growing up, and he had an understanding of farm life, he was fairly unfamiliar with horses. And on his second day at the ranch he was put on a horse – all day. “That was pretty interesting,” he says. “But it was a quick learning curve.”
George had a brother who, after spending some time in Vietnam, decided he wanted to be a cowboy. “He kind of lived out that dream for a few years and he took me along with it for a little while,” George says. Two of George’s brothers live in Montana now, although neither are cowboys, rather “happy Montanans.” George enjoys visiting them and hiking in Glacier National Park. “I enjoy that country but I wouldn’t necessarily recommend the cowboy’s lifestyle,” he says. “It was for the rugged individual, looking at it now. It was fun for a time.”
While working in Montana as a cowboy George met a gun builder who made expensive rifles, and George decided that he wanted to learn the trade from him. The gun builder knew George was from Ohio and had had some vocational training in the machine trades. “But he said, ‘Kid, if you want to learn how to do this, go back to Ohio, get an apprenticeship, learn how to be a machinist and then come back and I’ll teach you something.’”
So, George did. But he never returned to the gun builder in Montana.
Instead he entered a traditional apprenticeship in Canton, Ohio. It was the mid-1970s and the experience, he says, affected his whole approach to craft.
“This was an old-school apprenticeship made up of a shop full of ethnic journeymen machinists, old-timers,” George says. “They were Jews, Greeks, Italians, Poles and Hungarians, a lot of them second-generation immigrants. This was before CNC, this was before OSHA. Everybody smoked a pipe or a cigar or a cigarette. They had a pecking order. If you were an apprentice, they would abuse you mercilessly.”
And then, after a while, after George had taken enough abuse, one of them called George over to his bench and handed him a cracker. On it was a little slice of onion, some sardines and Limburger cheese – it was clear he had to eat it. “And then,” he says, “they would take you under their wing and start showing you things. And these guys were really fantastic craftsmen, and could really do unbelievable work.”
George soon became aware of when he was being tested. “They’d watch you struggle, and they would give you a little tip, something as simple as, ‘Use a brass hammer on this, not a steel hammer, a brass hammer would work better for what you’re trying to do there.’ And if you listened to them, they’d offer you more tips, and if you’d ignore them, they would let you drown in your own suffering. You wouldn’t get any information from them.”
As a result, George says he grew great respect for experienced artisans who learned hard lessons. “Later on, while I was exploring old design literature, I would look for these little tips and instructions in old books, and whenever I would see them I would take them seriously,” he says.
George didn’t just read what they were saying, rather if given a piece of advice, he’d take it. “That’s what really started me on this learning curve of understanding design,” he says. “And that made all the difference.”
As an apprentice, George worked with “hundreds of different journeymen of all shapes and sizes and characters and quirks.” For the first four years, “basically they had you do all the dirty work and in the process, you learned. And then in the last two years of the apprenticeship they took you in the office and said, ‘OK, you learned the basics, now you have to learn to work fast.’” That mentality also has affected George’s approach to craft.
After six years George became a Class A Journeyman. He worked with 200 to 300 fellow machinists at The Timken Co., doing everything from repairing machinery to making tooling to scale. He worked on parts as small as a sunflower seed to gears 9′ in diameter.
George worked as a machinist for 10 years before transitioning to management. His years as a machinist heavily influenced his preference for hand tools. “As a machinist I’m running a lathe all day, it’s noisy and hot, chips are flying and there’s smoke,” he says. “When I got into woodworking I decided right away I wasn’t going to get a bunch of woodworking machines, because I did that all day. So I started woodworking with hand tools. This was back in the 70s, when that wasn’t that popular to do. Everybody who was in woodworking would go to Sears and get a router table and a table saw, and I started with hand tools mostly because I just didn’t want to spend all day bent over a machine, and then in my evenings be bent over [another] noisy and dusty machine.”
George initially began woodworking out of necessity. He and his wife, Barb, didn’t have much money, and they needed furniture. Barb’s father did some woodworking, and he had a neighbor, a WWI veteran, who was a great hand-tool woodworker. “I visited him and he loaded up a box of hand planes, saws and chisels, gave me a little bit of instruction and said, ‘You can do this.’”
George spent 33 years at The Timken Co. Like many professions he had a love/hate relationship with progressing to the role of manager. “It was a lot more fun being a machinist than being the boss,” he says.
But once in management, George’s woodworking took off. “It was a stress relieving thing and it was a creative outlet,” he says. “So I started really woodworking in earnest then, and also started writing somewhere around that time.”
With no formal training in writing George simply wrote about topics that interested him, including astronomy, backpacking and later, at Barb’s suggestion, woodworking (which landed him in Fine Woodworking and Popular Woodworking Magazine, among others). “I’d write articles and submit them to magazines,” he says. “I had a lot of rejections, but eventually I figured out how you can actually write for a magazine and get things accepted. It was a learning process. But if I was passionate about something, I just loved to write about it.”
After writing about half a dozen articles for several different woodworking magazines, the editor of Society of American Period Furniture Makers (SAPFM) asked George to write an article for its yearly journal. George asked what he should write about and the editor said, “Whatever you want to write about.”
At the time George had begun researching design. “I was real curious: How did these artisans back in the 18th century design stuff?” Not knowing the answer, he decided to research this question some more, and write about that, simply because he thought it would be a fun topic. “That research led to everything else that followed and it was like a really deep pool that I fell into that I’ve never felt the bottom of yet,” he says.
George wrote his article and then spoke to several groups about the topic. “Everywhere I spoke, people were like, ‘Wow, this is fantastic information.’ Nobody had ever heard this before, it hadn’t been presented like this.” He approached Lie-Nielsen Toolworks with a proposal to do a video series on the topic (they said yes) and around the same time Christopher Schwarz, then editor of Popular Woodworking Magazine, asked him to start writing a column (Design Matters).
And then, George met Jim Tolpin at a Woodworking in America conference in Chicago. “I was doing this keynote speech in an auditorium,” George says. “He was sitting down front and I didn’t know him from Adam. They had this question-and-answer session at the end and he raised his hand and asked me three different questions. I didn’t know the answer to any of them and I thought: Those are fantastic questions.”
Afterwards, George introduced himself and the next day he attended Jim’s session and realized immediately they were researching the same thing, but completely unaware of each other. “He was researching how the human body relates to proportions and design, and I was researching classical architecture, which uses the human body as a standard proportion,” George says. “I was looking at it more from an architectural standpoint than he was but still, we knew right away we were doing the same thing so that’s what started a pretty wonderful writing partnership.”
The economy had crashed some years earlier and George had left The Timken Co. in 2008. But he still needed a way to keep his family afloat. So he was serving as his own boss, working as a full-time consultant (something he still does to this day). His evenings, though, were (and are) dedicated to researching and writing.
When Jim and George first talked about writing a book together, Jim told George that the worst way to ruin a friendship is to write a book together. But oddly enough, George says, the partnership has only deepened their friendship.
“Our conversations can go all over the place because this exploration we’ve been doing has taken us into architecture, philosophy, history, theology – I mean, it’s something that’s embedded in Western civilization, and design and architecture was an expression of that, so there’s so much to explore and understand.”
Everything Jim and George are doing, George says, goes back to Euclid and his understanding of simple geometry.
So how has their relationship stayed intact after two books with a third, “From Truths to Tools,” forthcoming? “I don’t think either of us has much of an ego or an agenda,” George says. “We’re both interested in what is the truest thing we can learn. And both of us are able to correct the other one, and say, ‘You know what? I think you need to dig deeper on that, I think this could be better.’ And we actually can do that without feeling threatened. I know if he tells me something can be better he’s just trying to help me do better work and likewise, I can comment on something he does and he realizes that I’m just trying to help him do better work, and that’s a really, really rare thing. It’s really hard to find someone who you can be critical with, and positive with, and it still works.”
George spends three to four hours a night writing and researching, in addition to his full-time consultant work. And much of it boils down to simple Latin words that are part of our modern language, words no one ever thinks about.
“If you take a string and you attach a lead weight to it, it becomes a smart string, a 2.0 string because it does something,” he says. “And actually, the word we use for ‘plumb,’ to make something plumb, straight up and down, well that comes from the Latin word ‘plumbum,’ which is metal lead. So if you take a piece of lead and tie it to a string it becomes a plumb bob and with that you can find a vertical surface. So all the words that are involved in our craft and all the tools have all this ancient knowledge, ancient language tied to them. And that’s some of the work we’re doing right now. It’s pretty fun to cover.”
For George, research involves two things: reading and trying things out. While he can’t actually read many of the old Renaissance texts, which are written in different languages, he can study the old drawings and engravings, pulling out and considering the geometry behind them.
“But the other big piece of it is actually trying it out,” he says. “I’m not interested in just book knowledge. If they’re showing how to do a layout, how to figure out how to do something with what Jim and I call ‘artisan geometry,’ it’s not something [that involves] a bunch of formulas. It’s about practical knowledge, about how to lay out a foundation for a barn, or how to do any kind of layout in space. We’re taking these ideas from these old books and trying them. We put away our tape measures and our rulers and started using a stick and a string and a pair of dividers to figure stuff out. And that’s where you really learn. That’s a lot of the research: Actually trying it out at the workbench, finding out what works and what doesn’t work.”
There was a time, George says, when he thought building something without plans would have been really scary. These days, he builds things not only without plans, but also without a ruler, or a tape measure.
While George’s days are full, he values time with family. George and Barb married in the late 1970s and had one son. They now have a 6-year-old grandson who enjoys spending time in George’s shop, banging hammers and mallets, making messes and having fun. George’s son is just now getting interested in woodworking. Last year George helped him build a Nicholson bench and the two plan to attend Handworks together in May.
Barb enjoys plein air painting (you can see her work here). Together they’ll set up their workspaces outside, Barb standing and painting, George sitting next to her with his laptop. They’ll paint, research and write, go out for lunch and then go home.
Home is a two-story traditional suburban house filled with furniture George has built. George has an appreciation for stripped-down Early American furniture, typically walnut or cherry, without much ornamentation. While drawn to contemporary work he carries strong, traditional tendencies. For George, the hallmarks of good work are strength, functionality and beauty. He has a basement workshop filled with hand tools and a table saw primarily used as a place to eat lunch.
George and Barb enjoy hiking and birding. “If you’re a birder you understand the season by which birds are here now,” he says. “It starts in February with the swans coming in and the waterfowl and the sandhill cranes, and then you move into the redwing blackbirds and the white-crowned sparrows, and then, coming up on Mother’s Day, the neotropicals move in, those are warblers, little colorful birds that eat insects and they come in by the millions.”
He talks about Magee Marsh, just a couple hours away from Canton, Ohio, where thousands of birders congregate from all over the world to see the warbler spectacle. “The birds fly up the Mississippi Valley and they stop [at Magee Marsh] and they rest and they eat and they gain weight so they can fly across the lake,” he says. “Sometimes you hit it right and the trees look like Christmas trees, covered with colorful birds, red, blue, green and orange – it’s quite the spectacle.”
George’s ability to see beauty in stars, warblers and proportion, to even the most seemingly ordinary bits of life, allows him to “live out every moment.”
“I’m very thankful for the life I have,” he says. “I have a spiritual dimension to my life. I am a Christian so for that reason I’m thankful for every day, every part of living. And for that reason I believe God is part of every moment in my life, every breath. All the work that I do, waking, sleeping, everything is filled with his majesty. And life is about living out that wonder, being thankful for every moment that is. As humans we’re lousy at living out every moment. A lot of moments in life seem like drudgery. At my best I’m absorbing that wonder of creation and what it’s all about.”
George says through his journey with Jim, the two have tied together how the Greeks saw that wonder. They talk about quantum physics and how the universe got its start and everything, George says, is tied together. “Everything is an exploration of being alive.”
“If there are physical laws governing the universe, like gravity, and there’s a law governing the spiritual universe, I guess I’d call that the law of giving,” he says. “And if you live a life of giving, your life expands and grows. And if you live a life of trying to hold onto things, your life shrinks and becomes small and has less meaning. If life is about giving, it grows. And it’s more fun.”
It’s something George strives for, daily.
“I think there is so much more I’d like to learn,” he says. Both about design and giving, dimensions he hasn’t yet explored. “When I give, my life gets bigger.”
— Kara Gebhart Uhl