While I’ve known about the surviving Roman workbenches at Saalburg Museum since reading W.L. Goodman’s classic “The History of Woodworking Tools” (1964) many years ago, I never thought I’d get to examine the benches in detail.
On Thursday, archaeologist Rüdiger Schwarz unlocked the warren of climate-controlled chambers under one of the buildings of the reconstructed Roman fort and led me, Görge Jonuschat and Bengt Nilsson past thousands of Roman artifacts organized on shelves, in drawers and in boxes.
And then there they were. Black from their time buried in well No. 49 outside the walls of the fort. Distorted from their return to the atmosphere after they were excavated in 1901. But solid oak workbenches, nonetheless. (We should all look so good after 1,839 years, give or take.)
Rüdiger, a trained furniture maker, graciously allowed us as much time as we needed to examine the benches, take photographs and write down measurements. For me, what was most shocking is how completely familiar the low benches seemed, especially now that I have a low bench in my shop. The legs were exactly where I would put them. The mortise for the planing stop – ditto. And the width (varying from 11” to 12”) was just right for me to straddle.
Both of the benches had split across the middle of their lengths – perhaps from their time in the well or when they were put down the well. One bench has been repaired since recovery; the other left as-is. The legs on both of the benches were added sometime after they were recovered from the well.
There is a lot that we don’t know about the benches. Why were they put in the well in the first place? There are a few theories – perhaps to protect them during an attack. Perhaps to hide them so they were not cut up and used to build defenses during the decline and eventual abandonment of the fort about 260.
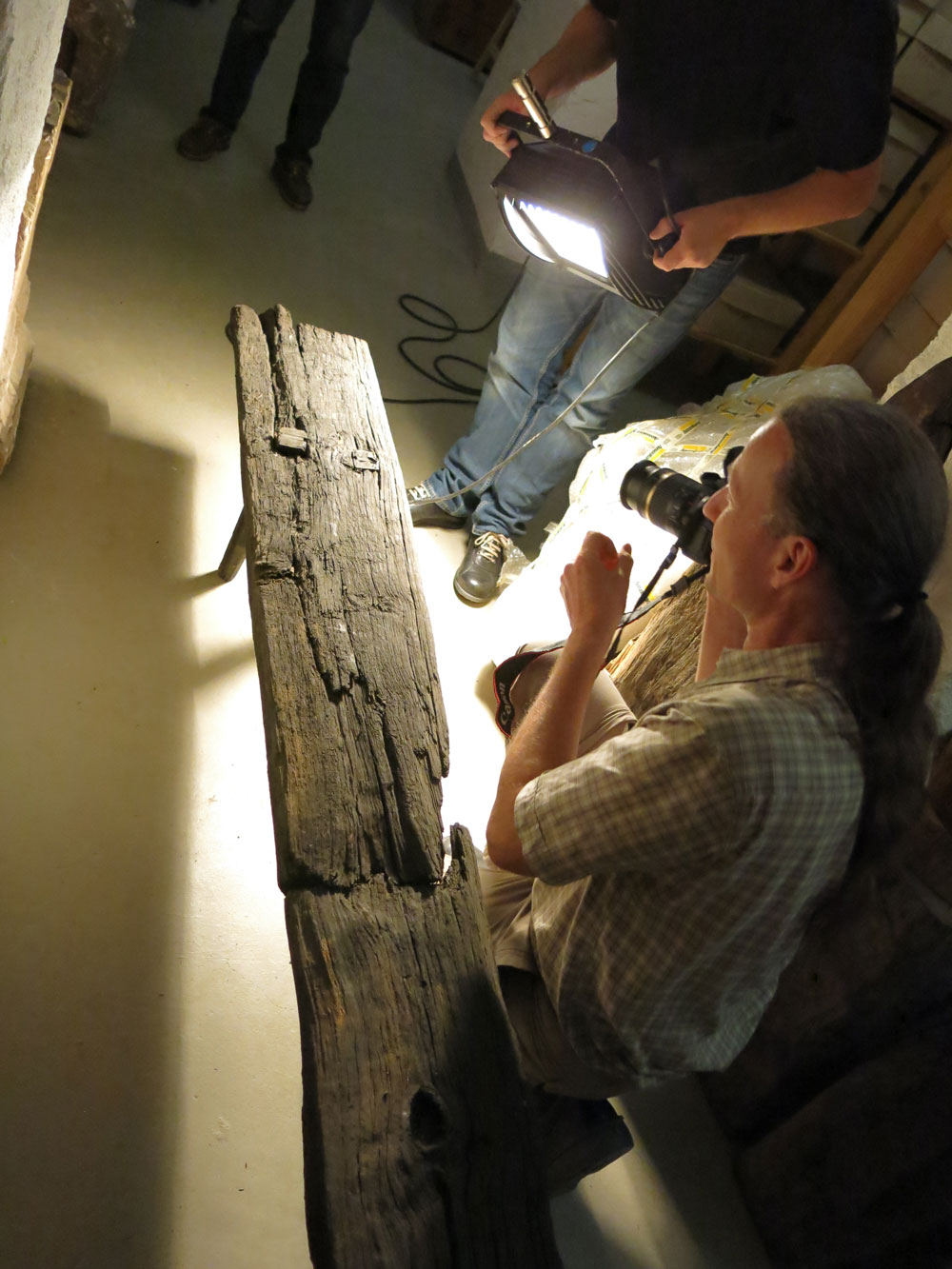
What were the odd notches on one edge of one of the benches used for – if anything? What did the planing stop look like? Exactly how long were the legs?
These questions (and more) are going to be addressed in detail in my forthcoming book on Roman workbenches. I took enough measurements that I’ll be able to build a fairly close reproduction – copying the leg placement, plus the overall size and shape of the top.
I doubt that a reproduction will give us a lot of definite answers. But it should confirm again that this style of bench is part of a long and still-living woodworking tradition.
— Christopher Schwarz