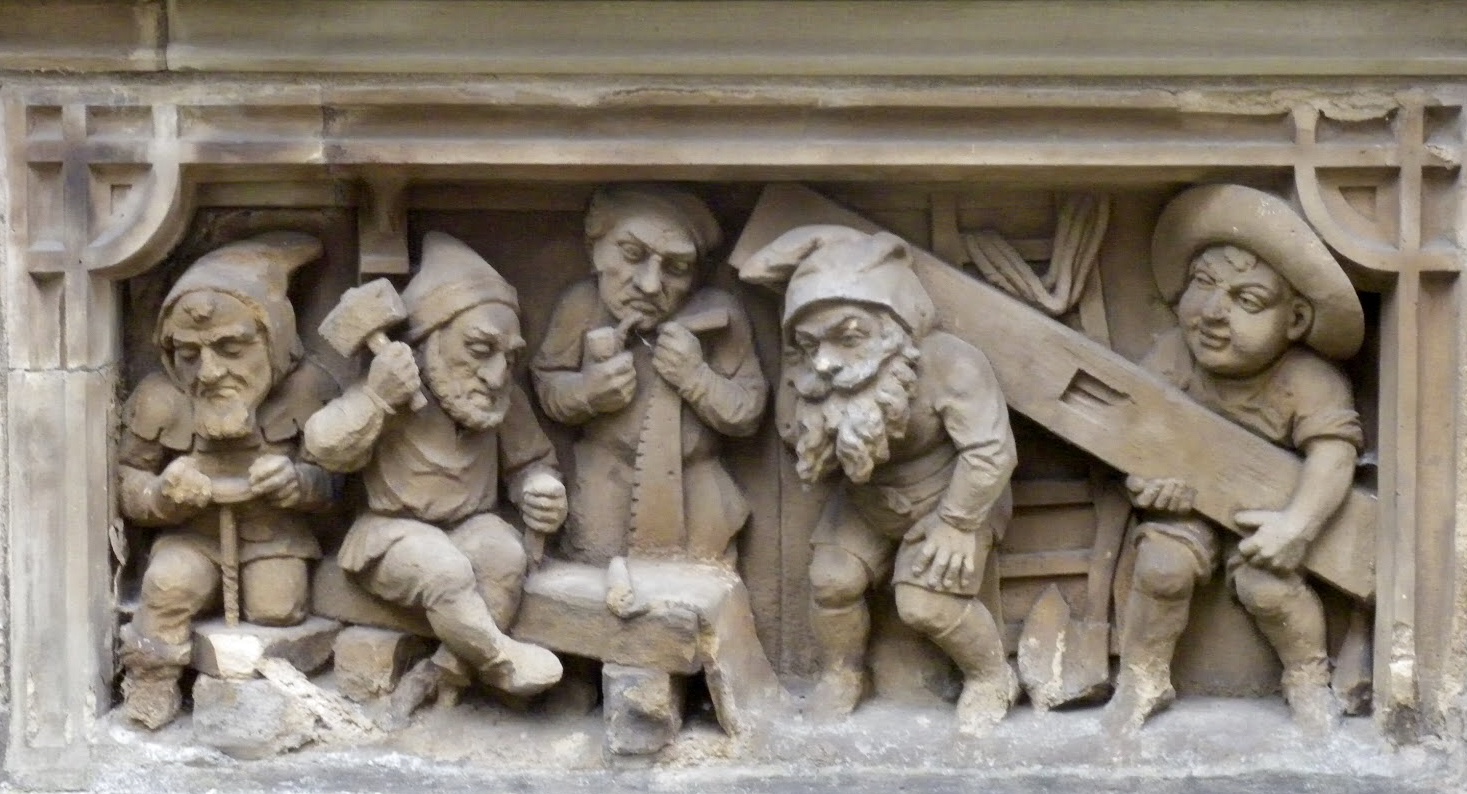
While you work feverishly to finish a commission for a customer or gifts for family and friends do you sometimes find yourself giving the side eye to those acquiring gifts with the mere click of a button? Perhaps you are feeling a bit Heinzelmännchen-ish? Let me explain.
Although the full history of the Heinzelmännchen is lost in the mystery and mists of time the modern story of these gnome-like spirits was written almost 200 years ago. A popular version of the story is August Kopisch’s 1836 poem “Die Heinzelmännchen” with scheerenschnitt (scissor cuts) by Regina Gebhard.
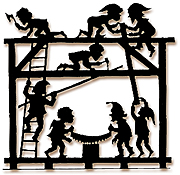
As the story goes, the citizens of Cölln did not work. While they slept each night the little gnome-like Heinzelmännchen were the workers of the town. They cooked, baked, brewed and sewed. They were the butchers, sausage makers, masons and carpenters.
The townspeople woke each morning to clean homes and another day of leisure – some would say laziness.
Here is an English translation of Kopisch’s verse about the carpenters:
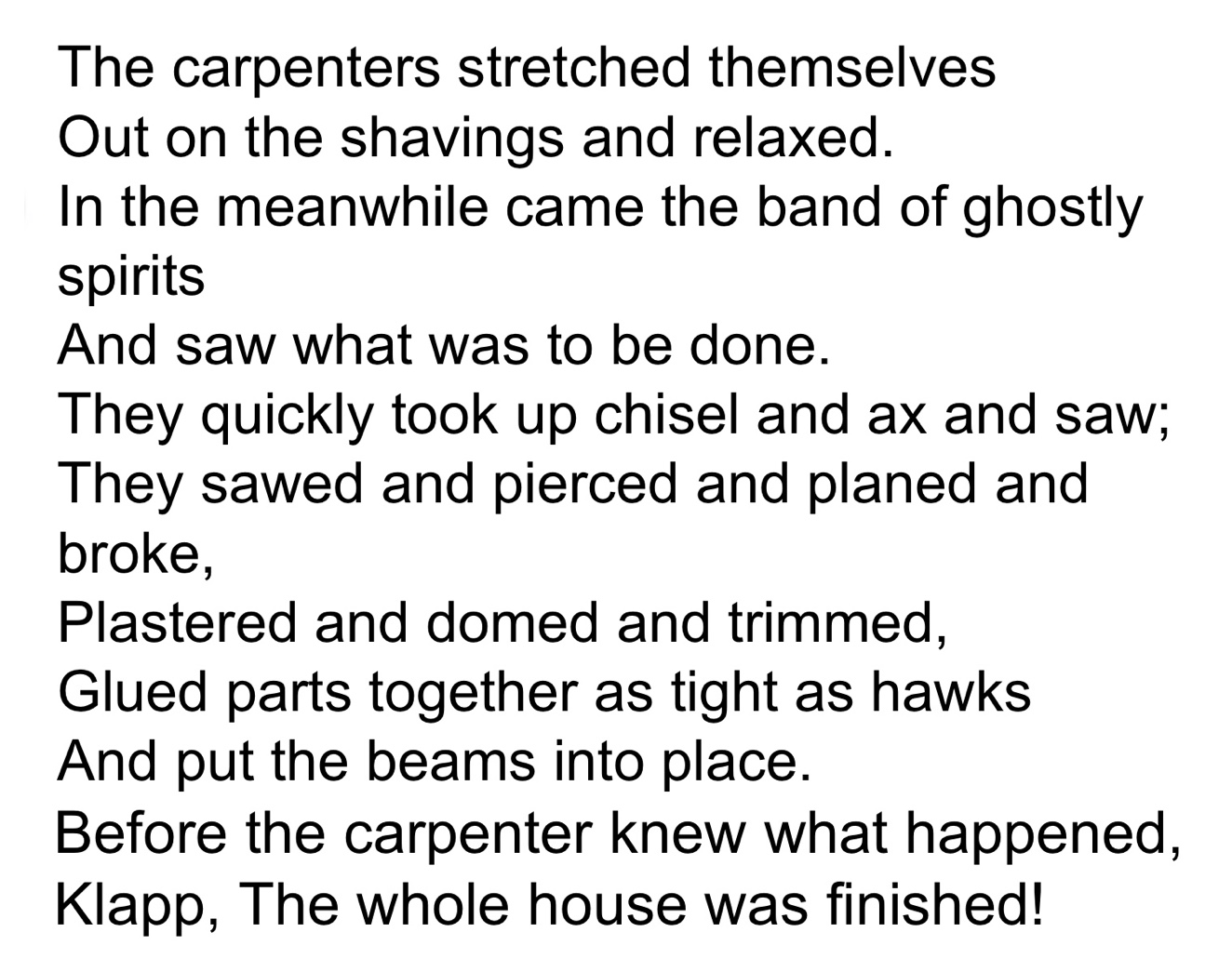
The easy life of the carpenters and other residents of the town did not last, and you can blame that on the tailor’s nosy wife. She could not contain her curiosity and was determined to see who was making the wonderful garments for the tailor’s shop.
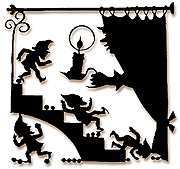
Her plan was to throw peas over the floor to cause the Heinzelmännchen to slip and fall, and in the morning she would be she be able to see the little spirits sprawled about the floor. Let’s assume she threw dried peas on the floor and not proper British mushy peas.
As with most malfeasance her plan did not go well. Yes, the Heinzelmännchen did trip and fall and land in vats. They also became enraged, yelled and cursed and…they left!
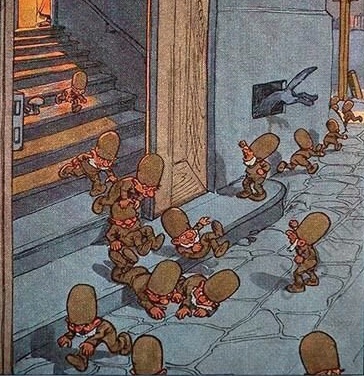
The Heinzelmännchen disappeared and were not seen again. And you know what happened next: the townspeople had to work for themselves and their dream-like existence was over.
Fairy tales are supposed to scare us and convince us to always check under the bed before going to sleep (and don’t forget to make sure the closet door is closed). So, what do we learn from the Heinzelmännchen? In Thomas Keighley’s “The Fairy Mythology” from 1833 he concludes his telling of the Heinzelmännchen with:
”…and since that time the Heinzelmännchen have totally disappeared, as has been every where the case, owing to the curiosity of people, which has at all times been the destruction of so much of what was beautiful in the world.”
Carry on woodworkers! Although you may not see it, your efforts to carve a spoon, turn a bowl, make a chair or a heart-shaped box will be rewarded! The handle of the spoon will fit perfectly in the hand stirring the soup, the bowl will hold apples picked from an orchard, the chair will be passed down to great-grandchildren and the heart-shaped box will hold the small treasures of a loved one.
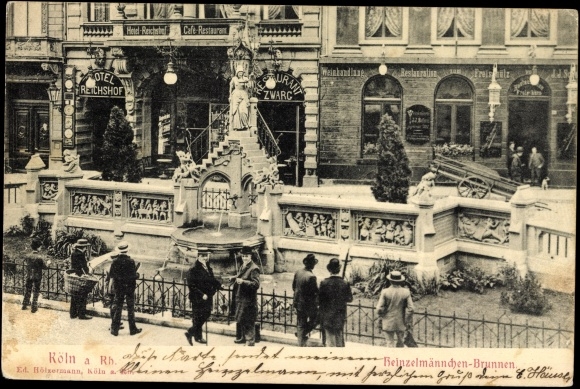
One last note on the Heinzelmännchen concerns the town of their origin. There is some back-and-forth on Cölln on the Spree River (now part of Berlin) or Köln (Cologne) on the Rhine. The good people of Köln built a fountain for the Heinzelmännchen, and I think that might settle the question.
You can read “Die Heinzelmännchen” (in German) here. English versions are available, and because I’m not your fairy godmother you can be a Heinzelmännchenn and look it up for yourself.
— Suzanne Ellison