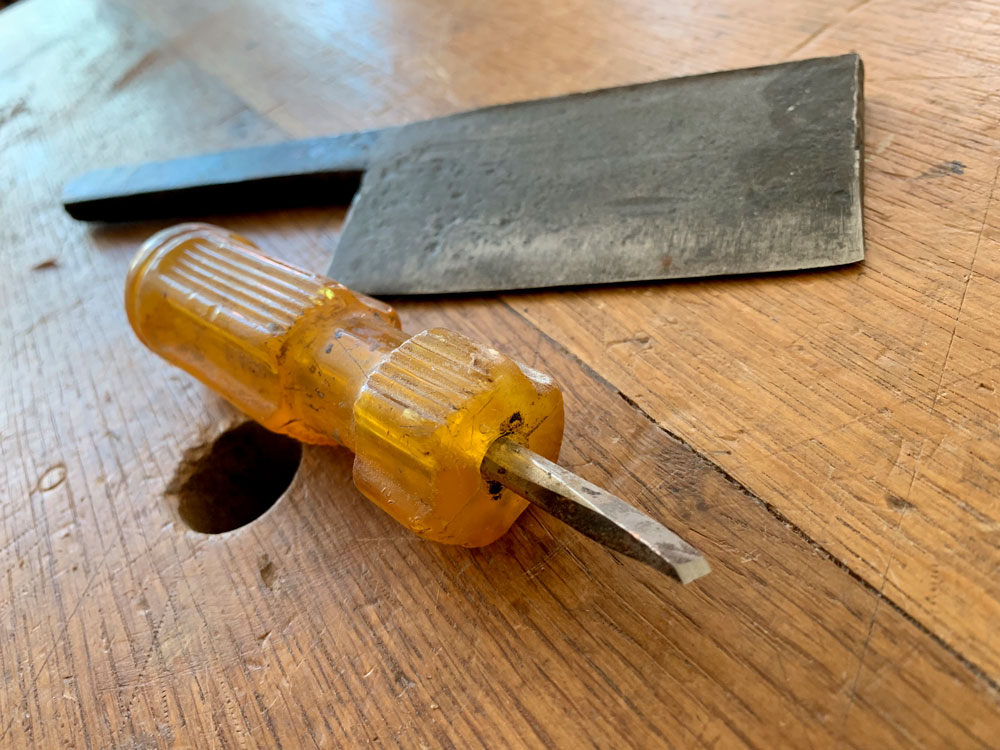
The day after the memorial service for Jennie Alexander, one of Jennie’s daughters, Harper Burke, posed an open question.
“Do you think Jennie was there?” she asked a small gathering of friends, family and woodworkers (who she calls the “woodpuckies”).
Now, I don’t think quickly on my feet, so I just smiled and kept my mouth shut. If I’d had a few minutes to think about her question, here’s what I would have said.
Of course Jennie (JA) was there. Jennie (and in her previous incarnation as John Alexander) had changed the lives of everyone who packed into that beautiful private Baltimore library last Saturday to remember her. There were chairs she had built. There were chairs that had been built as a result of her writing. There were people who had upended their entire lives to follow JA all over the world to teach the world about her beloved greenwoodworking.
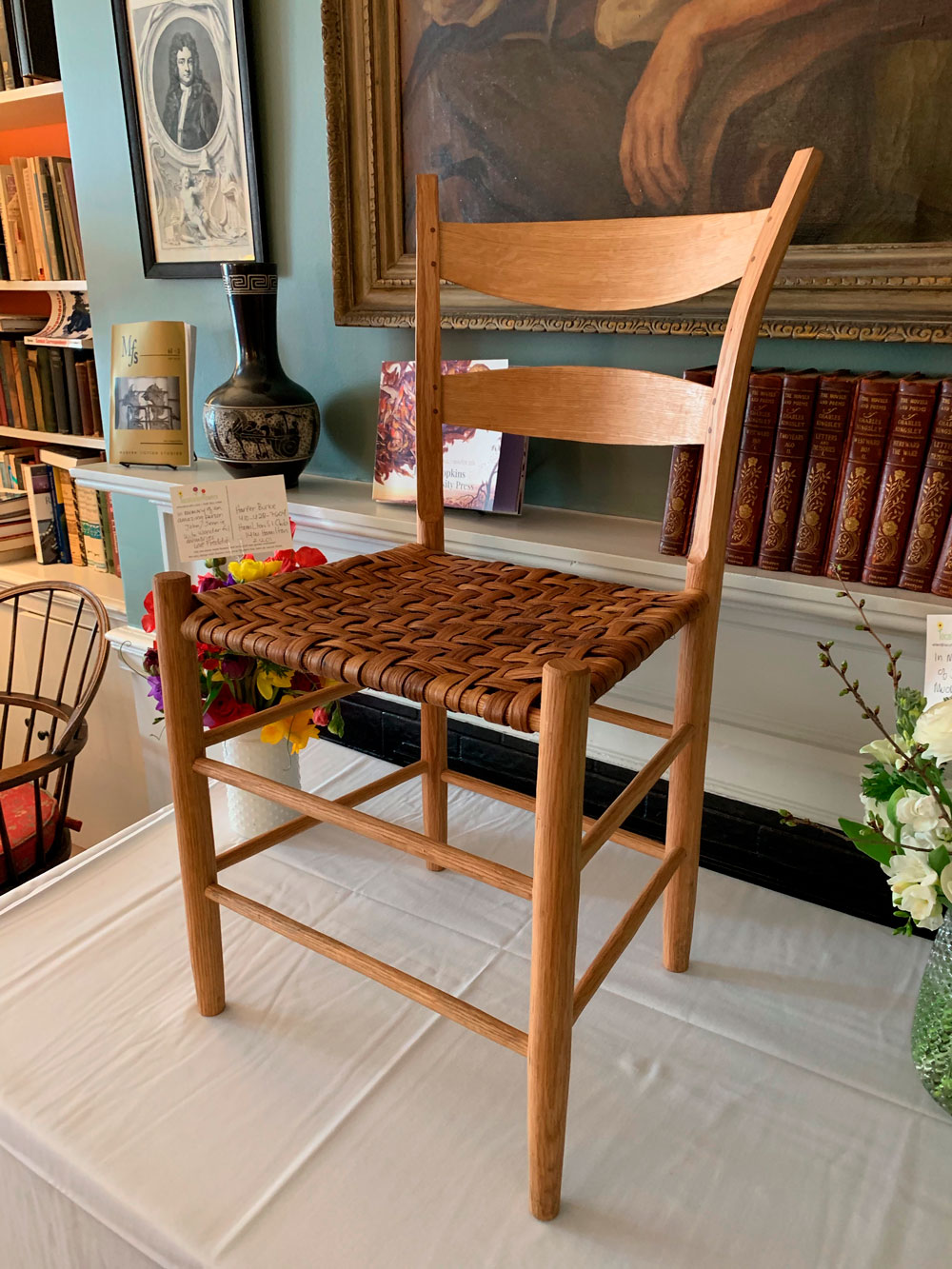
And Jennie wasn’t confined to that room on that day. When I returned home from the memorial service, I retrieved a few small artifacts I keep at the shop. One is a plastic-handled screwdriver that’s been ground into a chisel. This was the screwdriver that Brian Boggs had turned into a chisel so he could make the chair from JA’s “Make a Chair From a Tree.”
Yup. Brian Freaking Boggs, one of the world’s finest chairmakers and designers. He’d read “Make a Chair From a Tree,” and that set him on a course to who he is today, which (of course) took loads of hard work and talent on his part.
Peter Follansbee has often told the story about how he traveled to North Carolina as a young man to take a class from JA at Drew Langsner’s Country Workshops, and how their relationship transformed the arc of his life. In fact, Peter dedicated his latest book, “Joiner’s Work,” to JA and used language so kindly that it made me think: Did Peter really write this? (He did.)
JA’s death in 2018 came 40 years after the publication of “Make a Chair from a Tree,” the book that brought us together. Every day in my shop, JA is there – in the tools, techniques, books, ideas (both the ones that worked and those that didn’t). With all the love and respect I can muster, I dedicate this book to the unforgettable memory of John (Jennie) Alexander.
Hell, some days I feel like I have JA working to the left of me. Brendan Gaffney has watched the video of “Make a Chair From a Tree” more than I have, he’s nearly memorized the book and is now building chairs based on JA’s at an impressive pace.
In fact, in the woodworking world, it’s hard to find a place where JA isn’t. Her books, classes, articles, videos and letters – so many letters – have changed how woodworkers all over the world think about moisture content in the wood and caused us all to consider how it can be used to our advantage.
She gave the world a chair that is neither traditional nor contemporary. It is loved by people who treasure the past and those who are building only for the future. It charms and inspires almost everyone who sits in it.
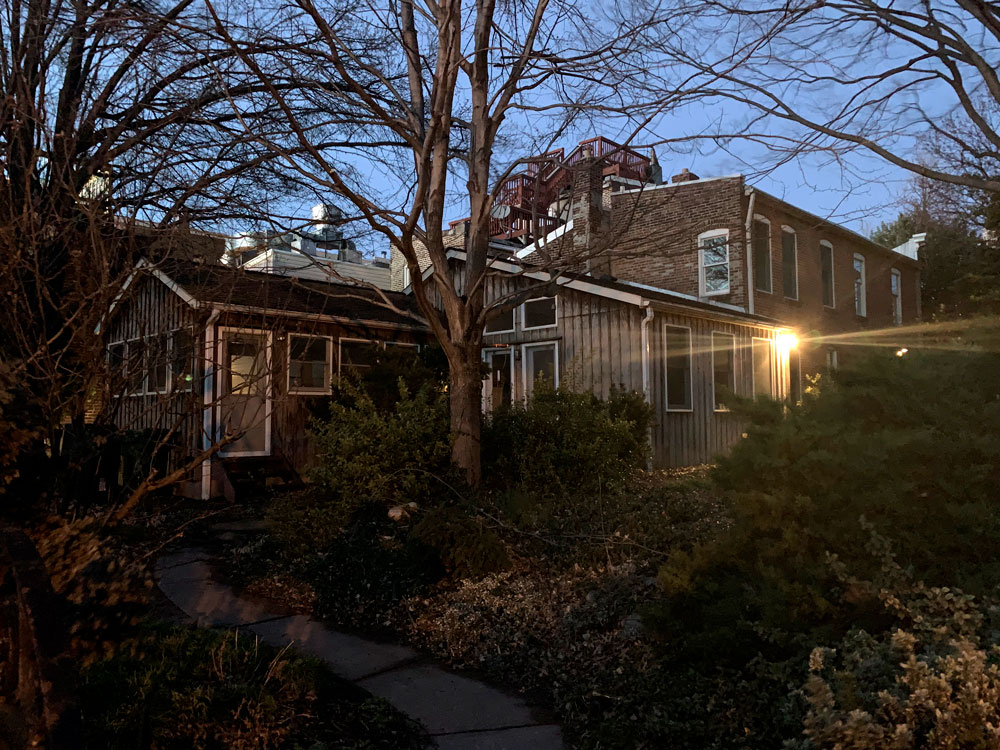
But there’s one place where Jennie isn’t, and that’s her Light Street home in Baltimore where she dwelled until she died last year. After the memorial service last week, Brendan and I wandered down to Light Street to take one last look at the place – it’s an amazing patch of green in the middle of a dense urban neighborhood.
JA’s tools, chairs, dinguses (jigs) and books are gone – all in the hands of loved ones and students. The trees and bushes of the 1400 block of Light Street – after being in service to JA and Joyce for decades – are now starting to take charge of the yard a bit.
I remember being stunned by the place the first time I saw it years ago. This is where so much incredible stuff had happened. On Saturday, I realized that the place itself had nothing to do with it.
Brendan and I then liberated one final memento – the last piece of pure JA that occupied Light Street – and headed back to our hotel, satisfied and happy we had known her.
— Christopher Schwarz
Like this:
Like Loading...