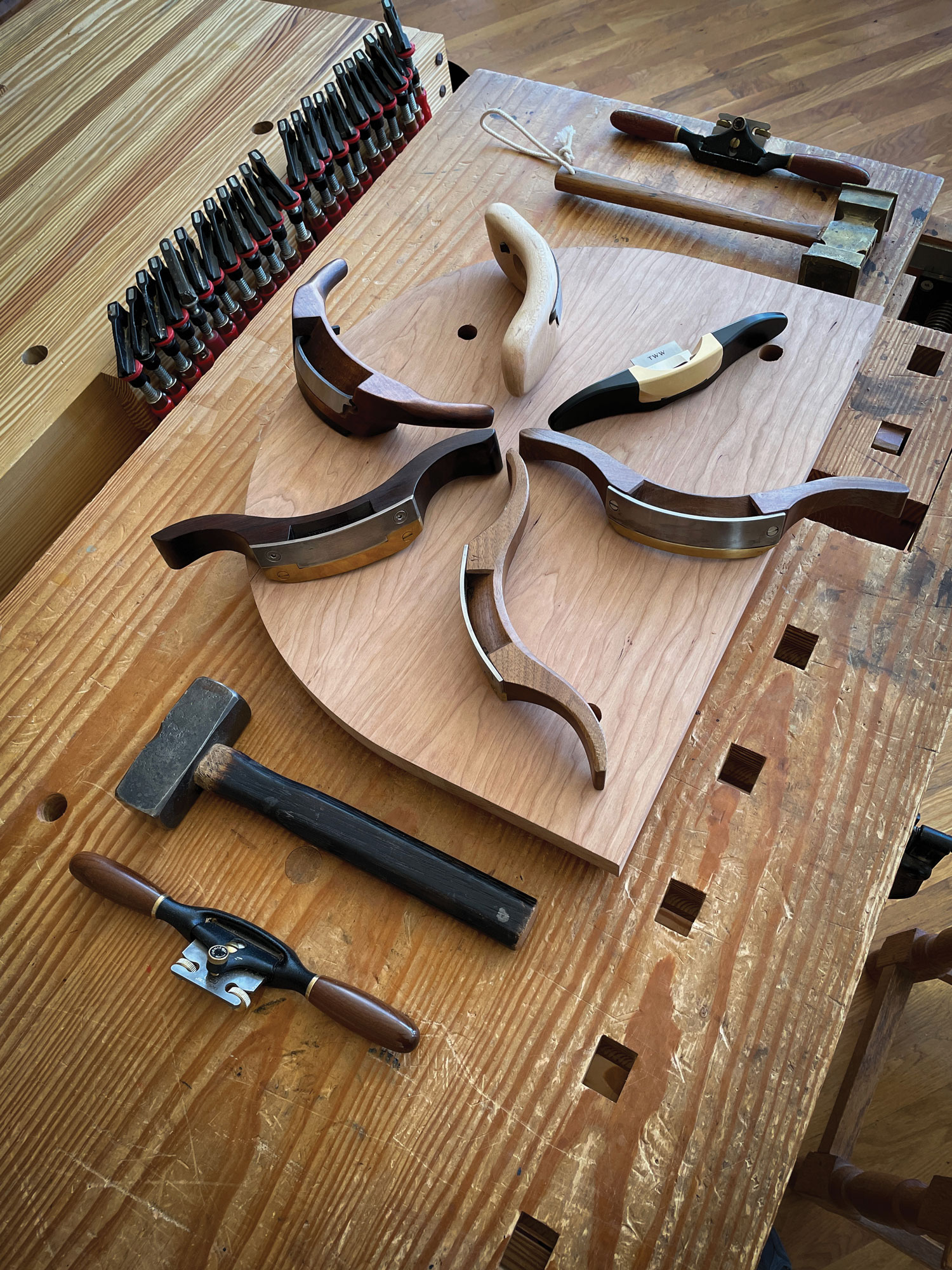
When I started making chairs, I wanted someone to hand me a list of tools and say: “Here. Buy these, and you’ll be on your way.”
The longer I made chairs, the more I understood why a list like that isn’t a good idea. There are too many tools out there and too many variables in how people like to work.
For example: I’m not a big drawknife guy. Ask me to recommend a drawknife, and I’ll give you a bewildered look. Ask Peter Galbert or Curtis Buchanan about drawknives, however, and you will get a master’s thesis on the tool.
Another problem is that suppliers are constantly changing. If I told you to buy a Harris Tools travisher, you’d spend months trying to hunt one up and spend some stupid money. Toolmakers come and go. Plus, they go through management changes – both good and bad.
The easy way out of this problem is to say: “Sorry, I can’t help. Do your own homework on tools.” But as someone who bought a lot of crappy chairmaking tools back in the day, I can’t do that to another person.
The following list is, I hope, a helpful medium. It’s a list of the suppliers I use and trust – plus the tools and supplies that I buy from them. These are the tools and supplies that I think are important to my success. If a type of tool isn’t listed – say, a scratch awl – that’s because I don’t think it really matters what kind of scratch awl you buy.
And because the marketplace is constantly changing, I didn’t want to print this list in “The Stick Chair Book.” Instead, I’ll issue a new list if new suppliers emerge or go out of business. This one is current as of June 2021.
Cold-bend Hardwood
Pure Timber LLC http://www.puretimber.com/cold-bend-hardwood-1/
Liquid Hide Glue
Old Brown Glue https://www.oldbrownglue.com/
Beeswax
Bulk Apothecary https://www.bulkapothecary.com
Soap Flakes
Pure Soap Flakes https://puresoapflakes.com/
Limonene (Citrus Solvent)
Real Milk Paint Co. https://www.realmilkpaint.com
Tapered-tenon Cutters (12.8°)
Hollow Augers/Straight Tenon Cutters
Reamers (12.8°)
WoodOwl Augers
Universal Sharpener
Spokeshaves
Auriou Rasps
Earlex Steam Generator
Veritas Dowel Maker
Felt Wheel for Grinder
Honing Compound
Lee Valley Tools https://www.leevalley.com/
Froe
Lie-Nielsen Toolworks https://www.lie-nielsen.com/
Dozuki
Gyokucho Razorsaw https://hardwickandsons.com
Sliding Bevel
Vesper Tools https://www.vespertools.com.au
Blue Spruce Toolworks https://bluesprucetoolworks.com/
Reamers and Tenon Cutters (6°)
Elia Bizzarri https://handtoolwoodworking.com/travishers/
Star-M Japanese F-Type Auger Bit
Workshop Heaven https://www.workshopheaven.com
WoodOwl OverDrive Bits
Taylor Toolworks https://taytools.com/
Bedan Sizing Tool
Highland Woodworking https://www.highlandwoodworking.com
Travishers
Claire Minihan Woodworks https://cminihanwoodworks.blogspot.com/
Elia Bizzarri https://handtoolwoodworking.com/travishers/
Windsor Workshop https://thewindsorworkshop.co.uk/
Scorp/Inshave
Lucian Avery, blacksmith https://www.lucianaveryblacksmith.com/
Barr Specialty Tools https://barrtools.com/
Soft-jaw Pliers
Tamiya Non-scratch Pliers https://www.tamiyausa.com
Hi-Vise
Benchcrafted https://www.benchcrafted.com/
Band Saw Blades
Woodslicer from Highland Woodworking https://www.highlandwoodworking.com
Abrasives
Mirka Abranet https://www.mirka.com/abranet/
Moisture Meter
Lignomat https://www.lignomatusa.com/
— Christopher Schwarz