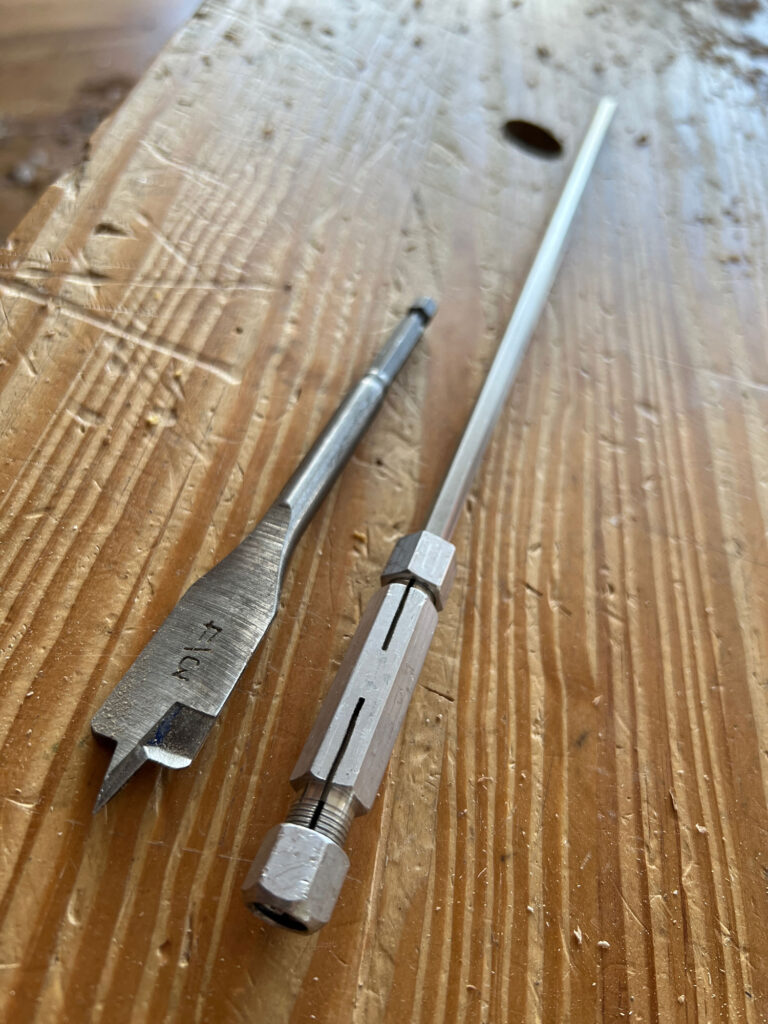
While some aspects of the U.S. economy have recovered, the printing industry is still on its heels. Because of labor and material shortages, we are still fighting lead times that are four times as long as normal. And we are the lucky ones. Many printing plants are simply turning away new business.
While we wait (patiently) for our books to make it through the long queue, we have been at work on new tools for Crucible. One of the tools I am working on with designer Josh Cook has been moving swiftly forward. Here’s a snapshot of our progress.
The GoDrilla Bit Extension
I use bit extenders almost every day, and I can tell you that every commercial one I’ve used is lacking. Many of them hold the bit with just a rare-earth magnet, which isn’t enough to keep the bit in place. Plus the fit is sloppy, so the holes you drill aren’t accurate.
Other bit extenders might hold the bit tightly, but it’s not concentric with the chuck of your drill or brace. So once again, your hole is going to be rough and larger than desired. To be fair, I think these bit extenders are designed for carpentry, so it doesn’t matter if the resulting hole is rough or a little oversized. But when it comes to making furniture, a little runout can ruin your day.
Finally, bit extenders don’t last long. They are easily bent and then become more difficult to use.
I wanted to make a bit extender that:
- Holds the bit fiercely and concentric with the chuck.
- Can be tightened by hand, but also can be cinched with a wrench when you need it to stay put.
- Is able to extend the reach of a bit from 6” to 24”.
- Is repairable if the shaft ever gets bent.
Josh and I fired a bunch of ideas back and forth, and we decided to build the GoDrilla around 1/4” steel hex bar. We will make the collet for the bit, but the user can use any length of steel hex bar to make the bit extender long or short. (The GoDrilla will come with a 12” length of hex bar, which is a common length required for chairmaking. You can order many sizes from McMaster-Carr.)
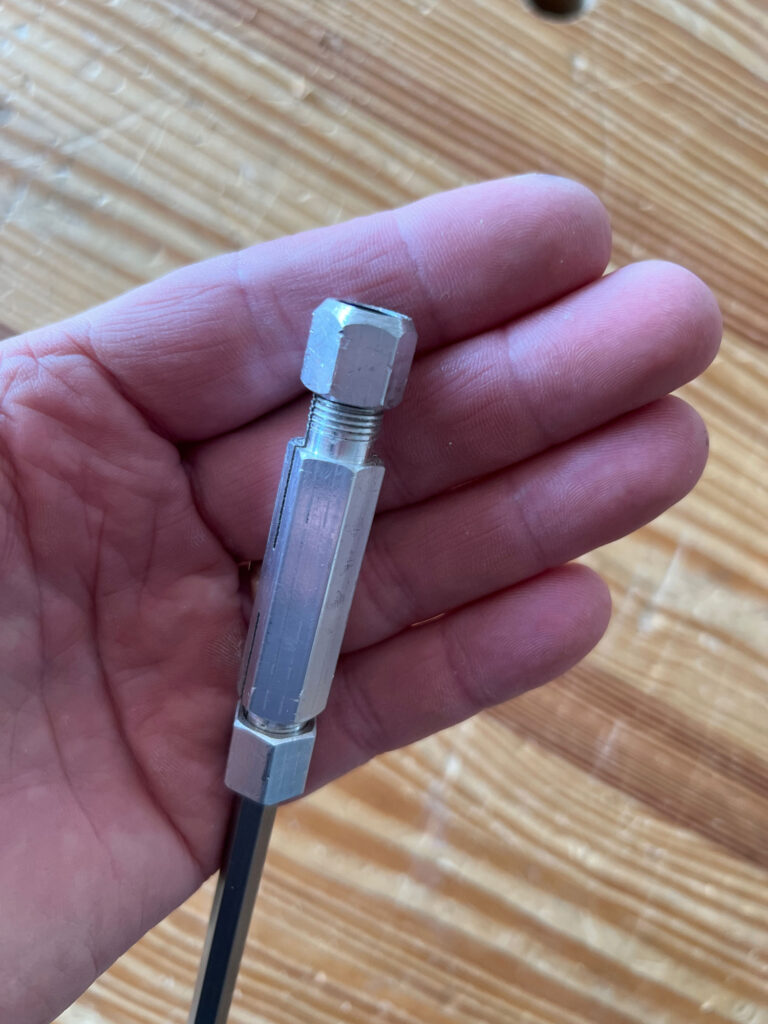
The collet works like a router collet (why did no one ever think of this before? It was Josh’s brainstorm). The collet has two ends: One grabs your hex bar (which gets chucked into a drill). The other end of the collet grabs 1/4”-shank drill bits. You can put anything you like in the collet, from a spade bit to a screwdriver bit to a countersink bit to anything with a 1/4″ hex shank.
It basically extends the reach of any of the thousands of tools that have a 1/4” hex shank.
The collet locks great with hand pressure. But you can make the bond unbreakable with a wrench.
The photos here show a rough working prototype in aluminum that has seen a ton of abuse. The real GoDrilla (gorilla not included) will have nice knurled nuts (with flats for a wrench), and the body will look a lot nicer.
We plan to make the tool in Tennessee – all our tools are made in the U.S. And we hope the GoDrilla will be about $43. While that is more expensive than other bit extenders on the market, this one works really well, and does things that no other extender does. Plus, it should last you a lifetime (instead of for about 10 chairs before it gets bent).
We hope for a summer release.
— Christopher Schwarz
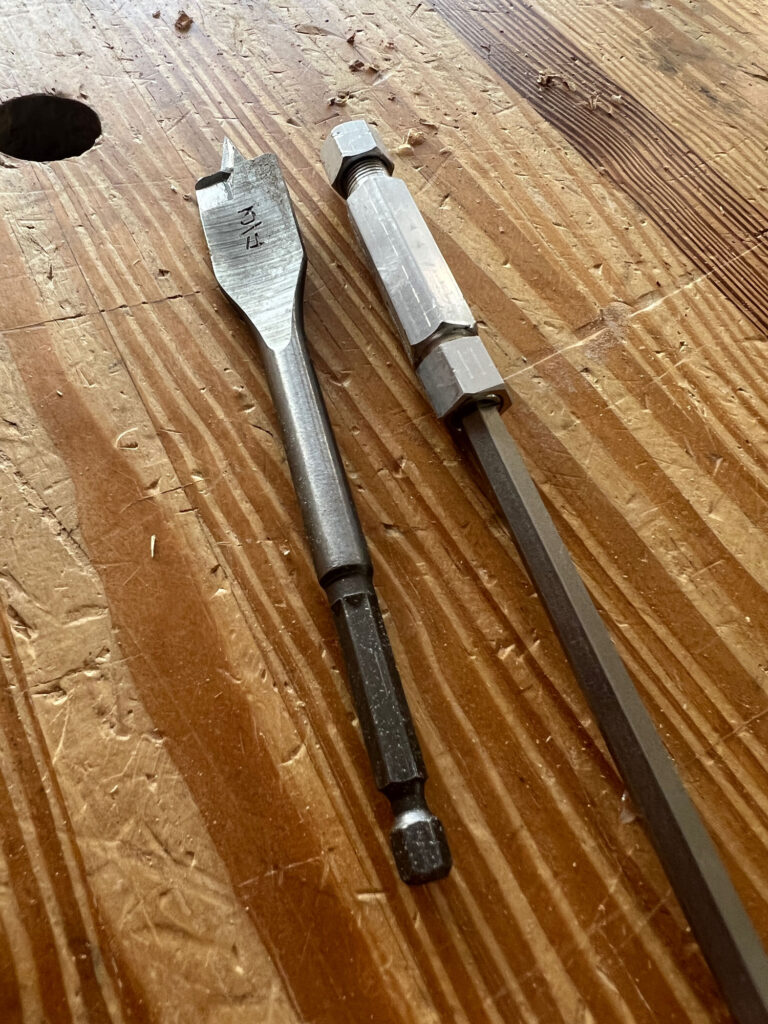