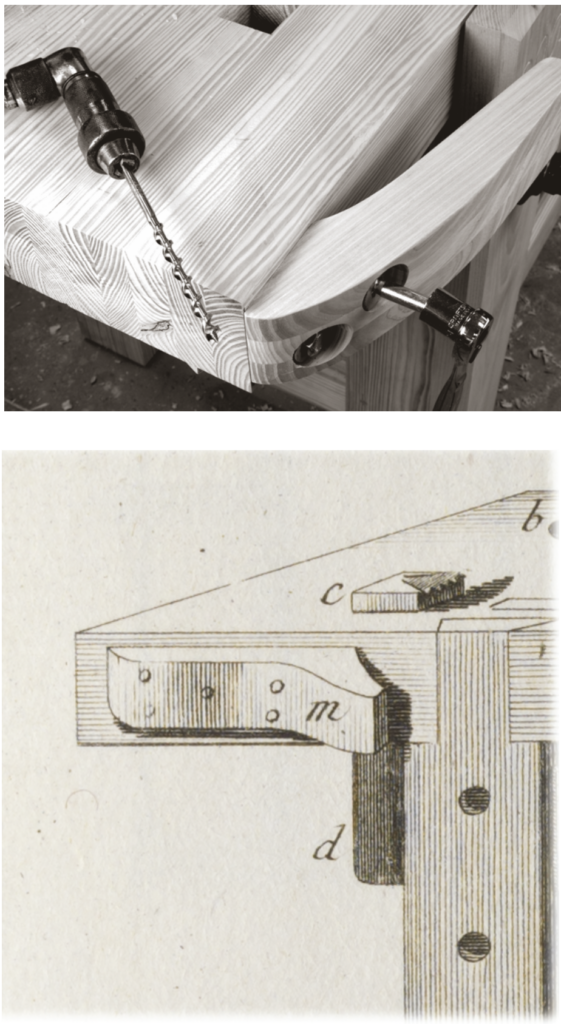
The following two early workholding methods are excerpted from “Ingenious Mechanicks,” by Christopher Schwarz.
Workbenches with screw-driven vises are a fairly modern invention. For more than 2,000 years, woodworkers built complex and beautiful pieces of furniture using simpler benches that relied on pegs, wedges and the human body to grip the work. While it’s easy to dismiss these ancient benches as obsolete, they are – at most – misunderstood.
Schwarz has been building these ancient workbenches and putting them to work in his shop to build all manner of furniture. Absent any surviving ancient instruction manuals for these benches, Schwarz relied on hundreds of historical paintings of these benches for clues as to how they worked. Then he replicated the devices and techniques shown in the paintings to see how (or if) they worked. This book is about this journey into the past and takes the reader from Pompeii, which features the oldest image of a Western bench, to a Roman fort in Germany to inspect the oldest surviving workbench and finally to his shop in Kentucky, where he recreated three historical workbenches and dozens of early jigs.
The crochet (French for “hook”) could be described as a planing stop attached to the edge of the workbench, but that doesn’t quite capture its full utility. A good crochet is also good for securing work for dovetailing and tenoning.
There are a couple kinds of crochets out there. Some of them are like wedges. You press the work into the opening and its V-shape helps hold the work (though you will still need a holdfast to complete the job). Old French ones, as shown in “l’Art du menuisier,” work more like a planing stop as opposed to a wedge. Their opening is square instead of V-shaped. Both forms of crochet work, but I prefer the V-shaped ones on my benches.
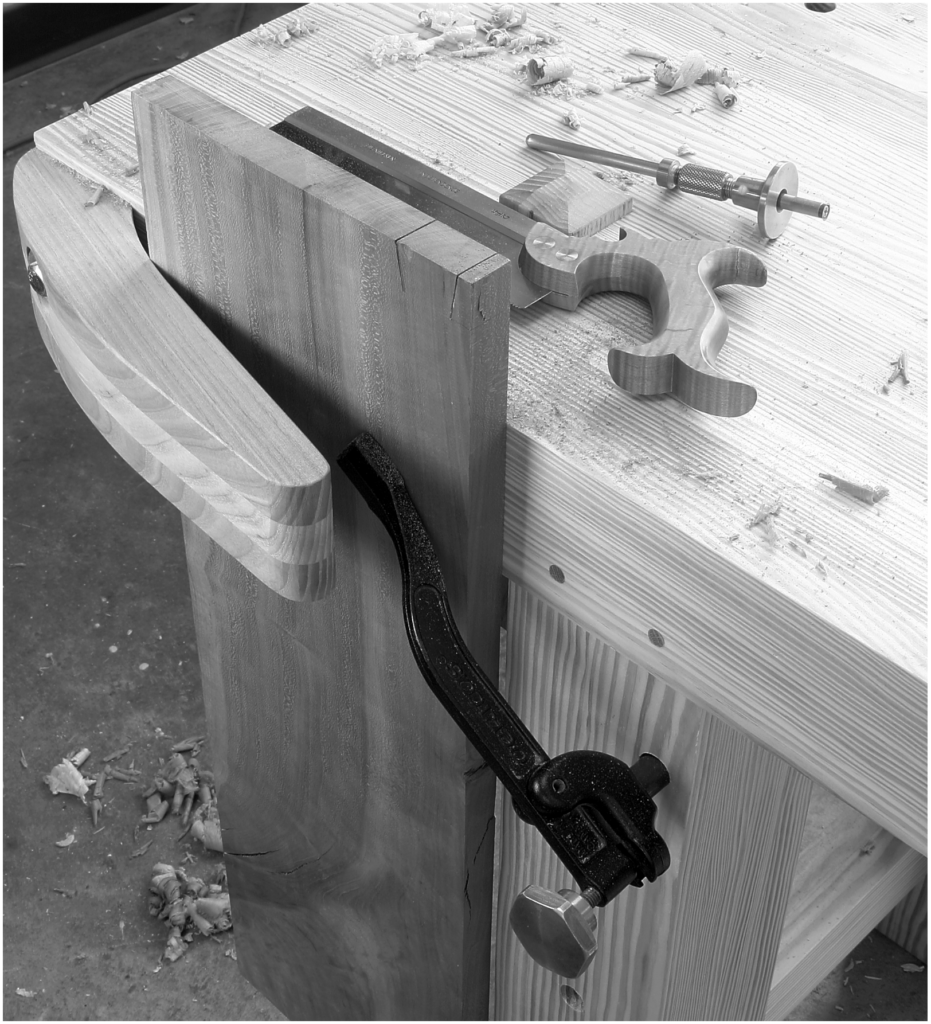
I make my crochets out of a tough and springy wood, such as oak or ash. I recommend you make the hook big enough so that it can handle 8/4 stock. So, the opening should be slightly larger than 2″. Many early crochets are shown attached with nails. I prefer 6″-long carriage bolts with washers.
Using the crochet for working on the edges of boards is straightforward. Typically, you secure the work to the front of the bench with one or two holdfasts (depending on the length of the work). Then you push the end of the board into the crochet to prevent the work from shifting as you plane it.
If I have a lot of boards of similar widths to work (say for a large tabletop) I take a different approach. I use holdfasts to secure a 2×4 to the front legs of the bench that will act as a platform for my boards. Then I press the end into the crochet. Gravity and the force of the plane immobilize the work.
Crochets can also be used to affix the work so you can cut dovetails or tenons. Put the edge of the work into the crochet and affix it to the front edge of the benchtop with a holdfast (or a bar clamp across the benchtop, if you are sadly holdfast-less).
Notches & Wedges
In many old paintings and drawings you’ll see benches that have no vises but instead have a large rectangular notch cut into the edge or end of the benchtop. In many cases, these notches are used as face vises. You put the work in the notch then use a wedge to immobilize it. I’ve had great – actually, quite spectacular – success using these notches for cutting tenons and shaping the work with chisels, rasps and files.
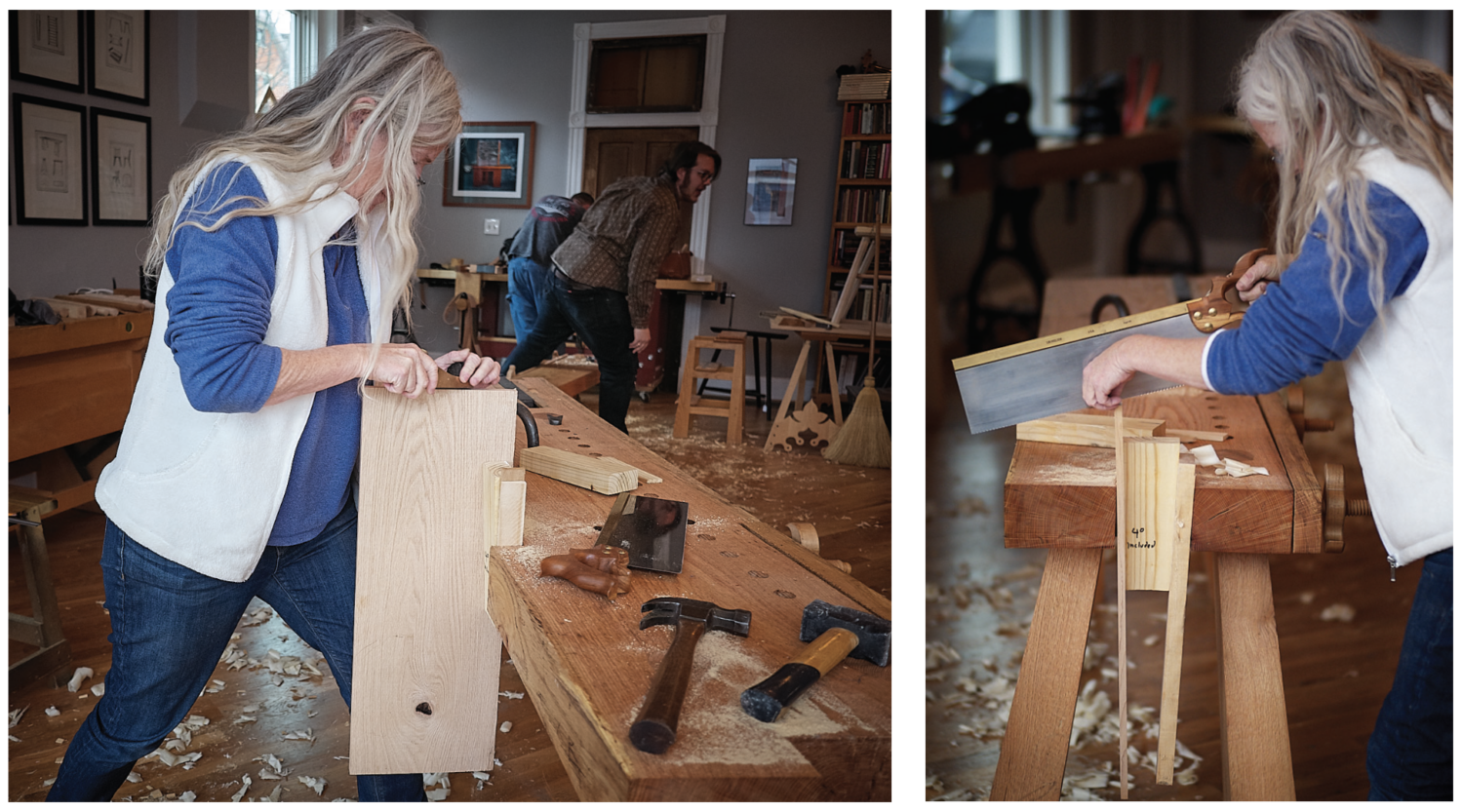
It took a little experimentation, however, to get the wedges right. As it turned out, I was making things too complicated. At first, I used oak wedges in the shape of a right triangle that I planed clean so they had an angle at the tip of about 15°. They held the work, but not reliably. So, I tried isosceles-shaped wedges with a variety of angles, looking for the magic number.
After several hours of messing with the oak wedges, I thought I was headed down the wrong path. So, I went to my scrap pile and grabbed a white pine 2×4. I sawed it to 12″ long and tapered one edge with a jack plane (I later measured the angle at 2°). Then I drove it into a notch.
It cinched down as hard as any screw-driven vise I’ve used. It worked so well I laughed out loud.
If you are interested in making these notches (what do you have to lose?), here are some details. In the old images, the notches have vertical walls. Some fellow woodworkers have suggested cutting them at an angle that is sympathetic to the wedge’s angle. I haven’t found that necessary.
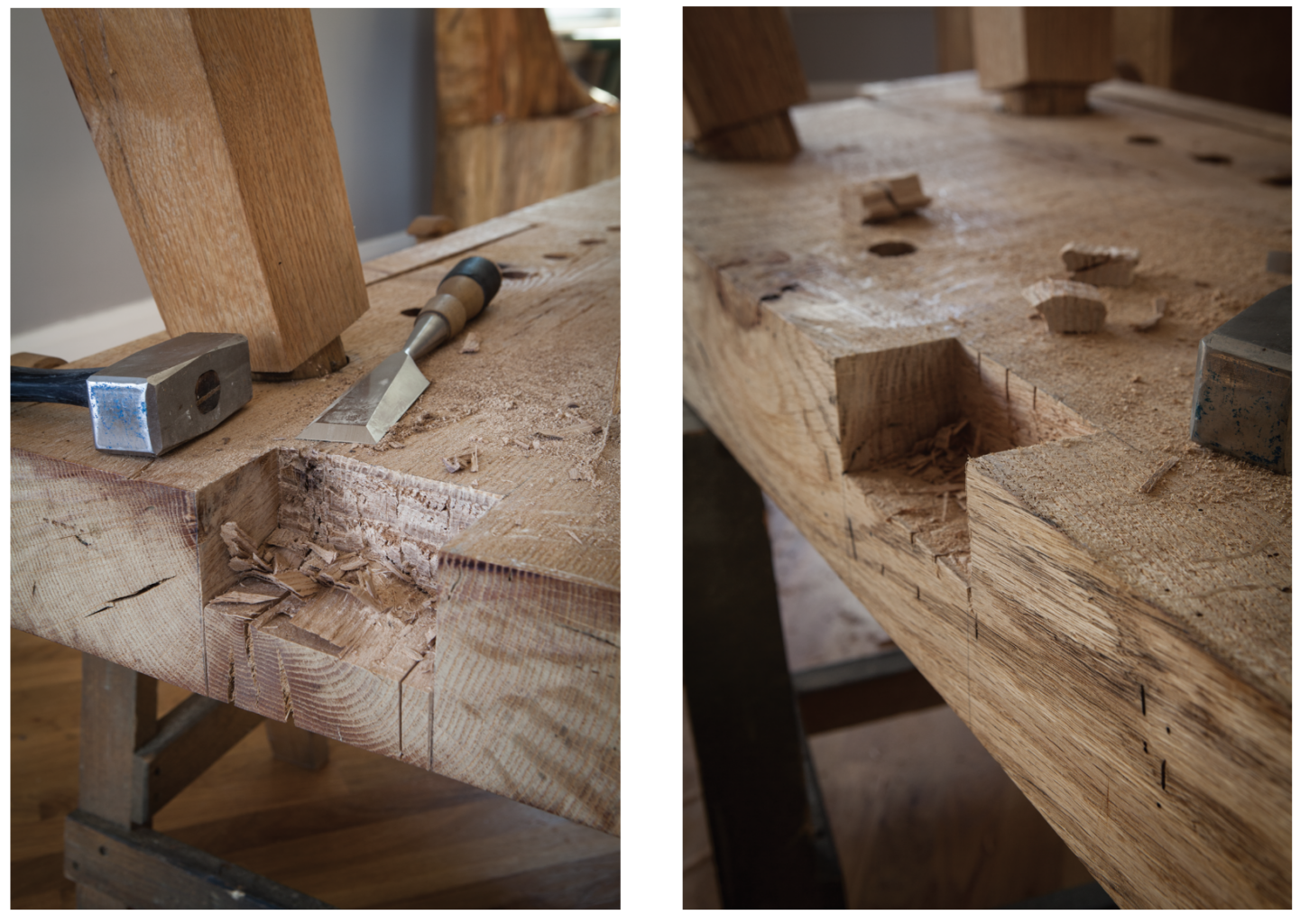
On some benches, the notches are in the end of the benchtop. In others, they are cut into the edges. I tried both. Functionally, I couldn’t tell any difference between them. They both held just fine. Making the two kinds of notches, however, is quite different. The end grain notches take about twice as long to make because the wood is fighting you the entire time. You have to rip saw the walls of the notch then chisel out the waste like cutting out a huge dovetail. There is a lot of chopping vertically then splitting out the waste. It’s not a horrible task, but it’s much more difficult than creating a notch in the edge of the benchtop.
There you crosscut the walls (crosscutting is always easier than ripping). Then you split the waste out with a few chisel chops. Splitting wood along the grain is always easier than chopping across it.
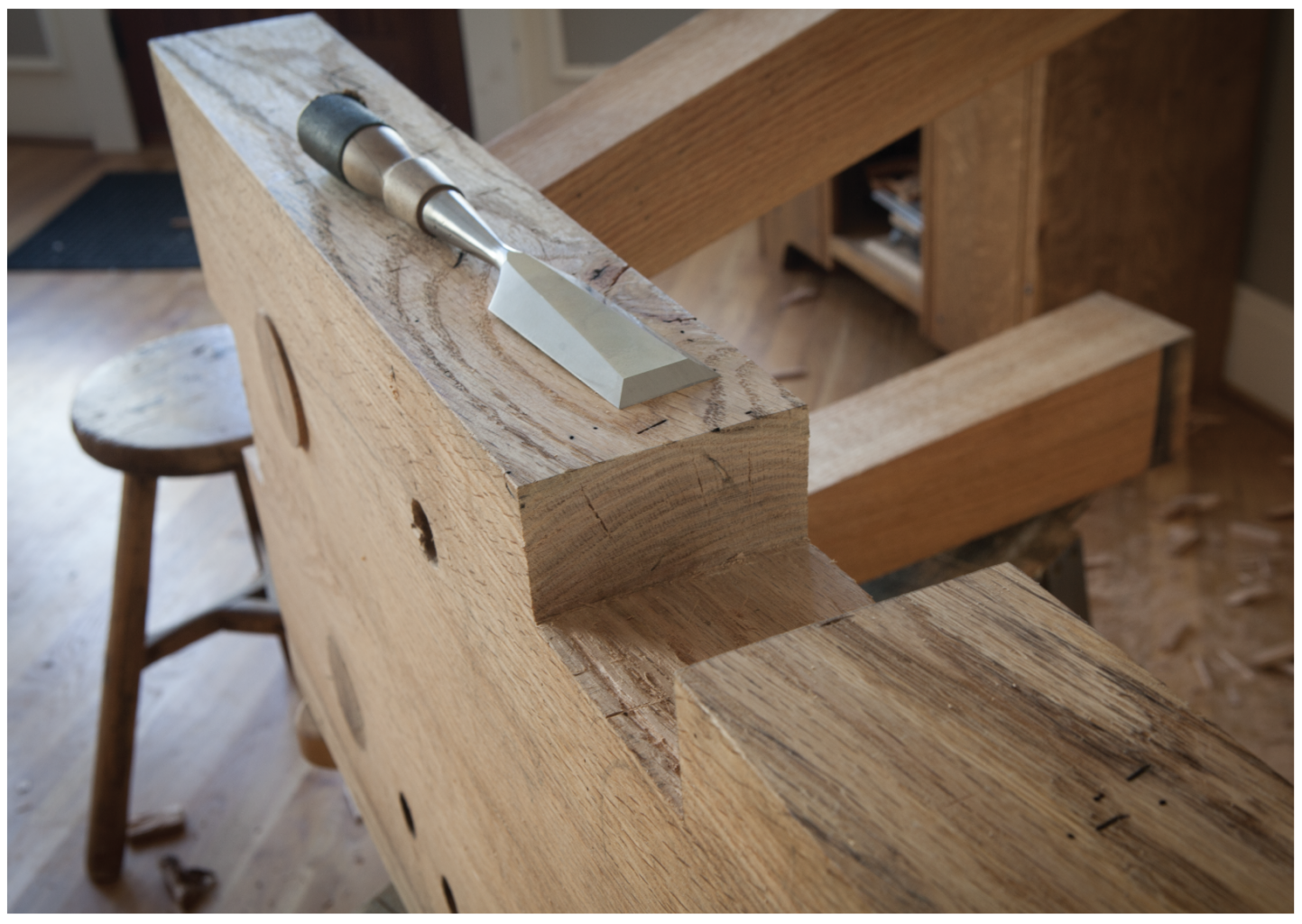
Here are the measurements for my notches. Don’t feel compelled to copy me, however. The end-grain notch is 4-1/2″ wide and 2-1/2″ long. The edge notch is 4-1/4″ long and 2″ wide. I have a variety of softwood wedges scattered about that can handle work from 1″ wide to 3″ wide.
One more nice use for the notch comes when cutting curves with a bowsaw or coping saw. Place your work over the notch while sawing and it will vibrate less.