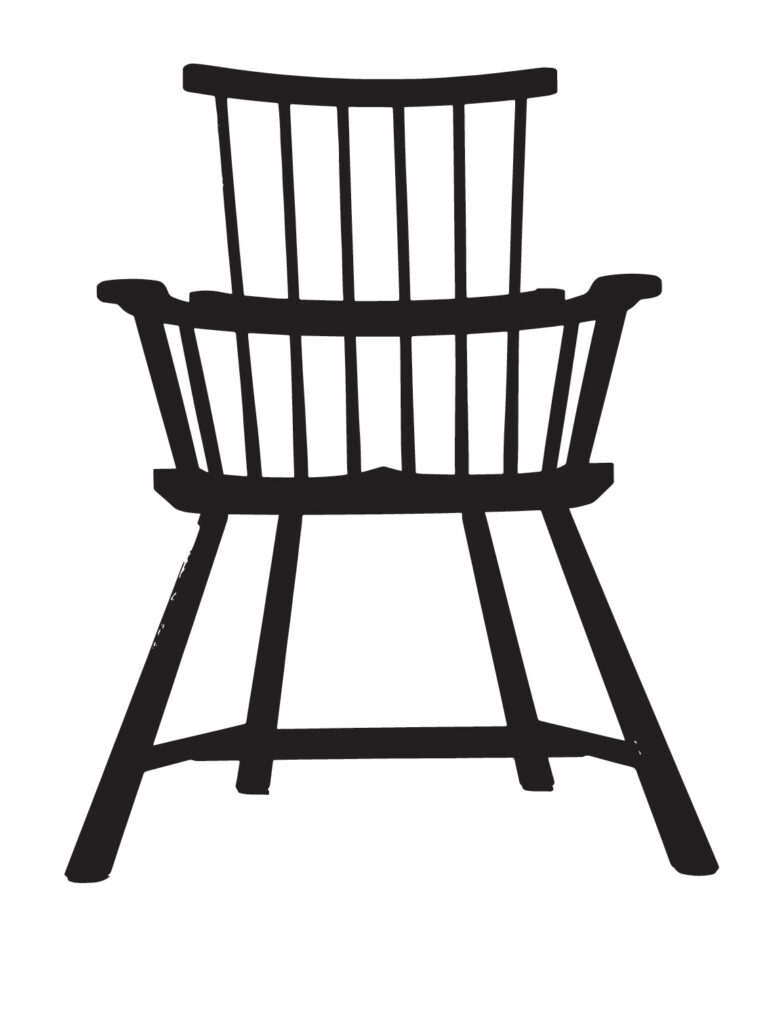
Publisher’s note: The following is the essay I wrote at the beginning of The Stick Chair Journal that explains what it’s about and what is coming in the future. This is the only excerpt we’ll be publishing on the blog.
The world does not need any more chairs. Or magazines, for that matter. And yet I am compelled to create both.
When I left my corporate publishing job in 2011, I was determined to stay away from magazine writing. And for years I turned down a half-dozen friendly offers from former competitors to write tool reviews, a column or long-form feature articles.
It turns out, however, that what I hated about corporate publishing was just the corporate part. The endless fleecing of customers (why does the cost of a yearly subscription go up for loyal subscribers?). The pressure to grow revenue 20 percent every year (without additional resources). The constant cheapening of the printed product (if there’s a thinner, crappier paper out there, they’ll find it and use it). The pandering to advertisers at the expense of the readers. The non-stop pressure to write articles for the lowest-common denominator.
It took me 11 years to recover from that toxic diet. Then one day while taking a shower I realized I could start a publication on my own terms. No advertising. Beautiful paper. No pressure for growth. And the magazine/journal/zine could be filled with the minutiae that I obsess about.
And that’s how The Stick Chair Journal was born.
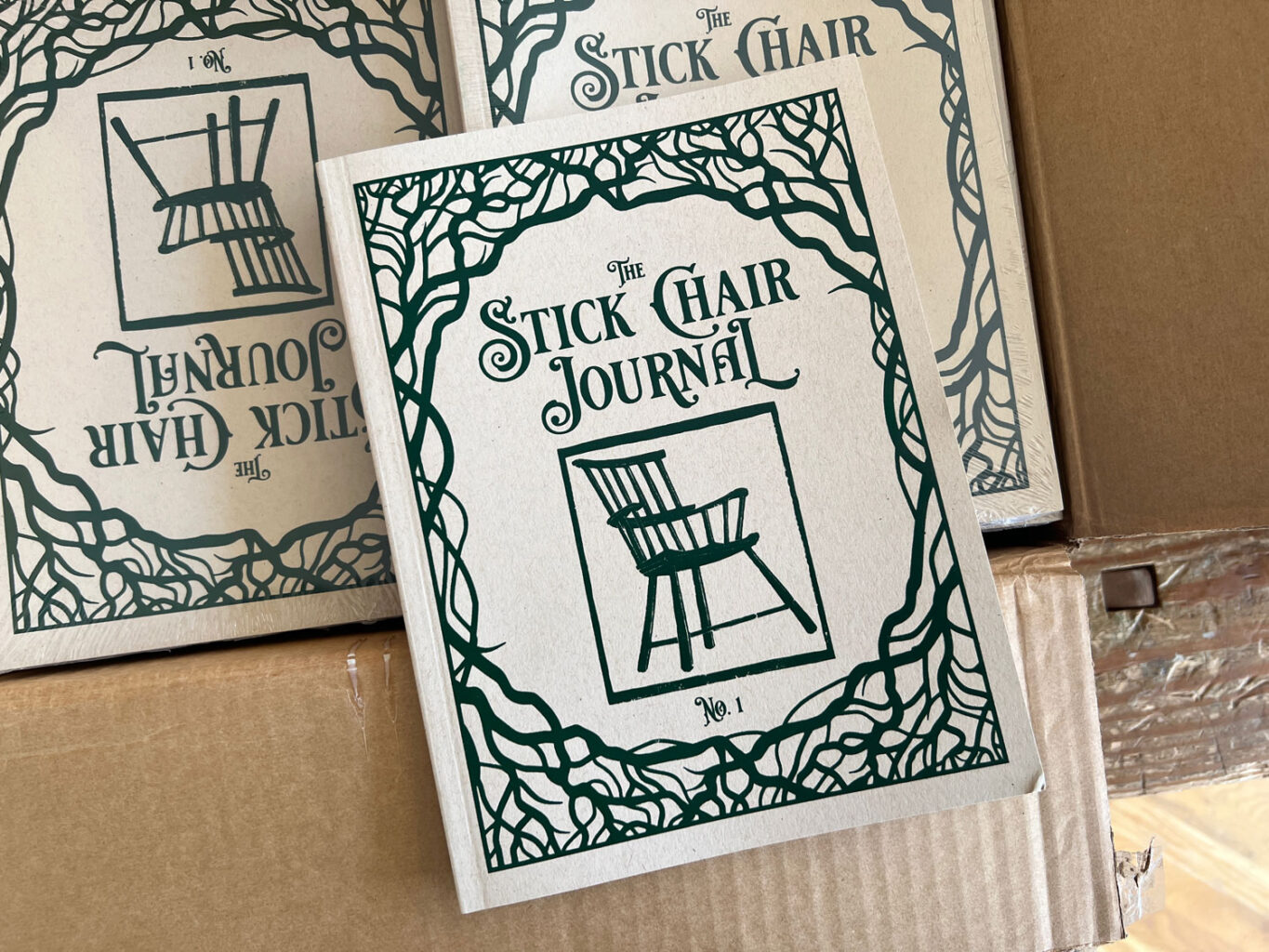
What’s it about? Chairs that look like they are made from sticks. While the first issues will surely be about the chairs that I love and build, the world of “stick chairs” is much wider. I consider Windsor/Forest chairs to be stick chairs. In the hills of Kentucky, Tennessee and West Virginia, ladderbacks are often called stick chairs. All these chairs share one central feature: They are built from very slender, roundish components (sticks!) that are joined to create a lightweight and comfortable place to sit.
Unlike frame chairs, which are rooted in the cabinetmaking tradition of square mortises and tenons, stick chairs use different technology. The joints are circles instead of squares. And instead of deriving strength from bulk, stick chairs survive thanks to the exploitation of wood at the cellular level.
In each issue, we hope to highlight techniques that you might find helpful. Discuss tools that fly under the radar of mass-market magazines. Offer plans for one chair per issue that you are free to build for yourself and even sell to customers. And I want to explore the cultural aspects of stick chairs. What does that mean? Read “A Vampire Chair” in this issue for a taste.
I consider The Stick Chair Journal to be a supplement to “The Stick Chair Book.” That means that my plans use the techniques already discussed in that book. If you are an experienced chairmaker, you probably will be able to follow the plans here without any help. But if you are new to chairmaking, you might want to pick up a copy of “The Stick Chair Book” to get grounded in the basics first.
For future issues, we hope to convince other makers of stick chairs to share their methods and designs. But first, we have to get a few issues under our belts to establish a rhythm for the editing, production and printing of the Journal.
Oh, one more thing: We don’t plan to offer subscriptions. We don’t have the staff or infrastructure to manage a subscription/renewal database. In any case, most magazines are trying to trick you into renewing (sometimes for several years). And I don’t have the stomach for that game any more.
The Journal will be printed annually and will be released in the fall – stick chair season. If you want a copy, you’ll be able to buy it from Lost Art Press, plus (I hope) the outlets where we sell our books. Purchase only the issues you want. Skip the ones you don’t. If you don’t like an issue, send it back for a refund.
If all this sounds like a lousy way to run a railroad, you are probably right.
But let’s find out anyway.
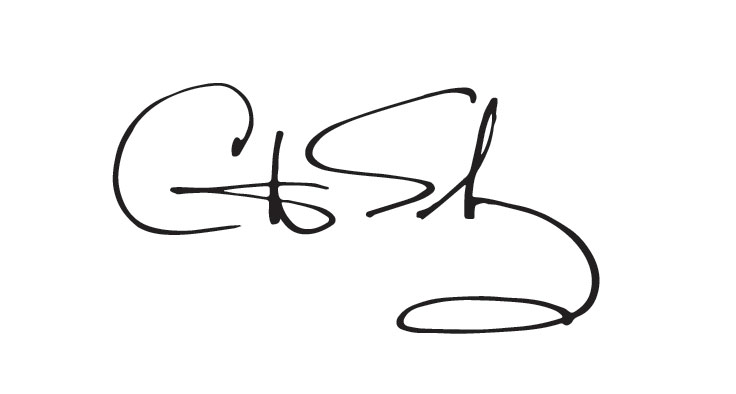
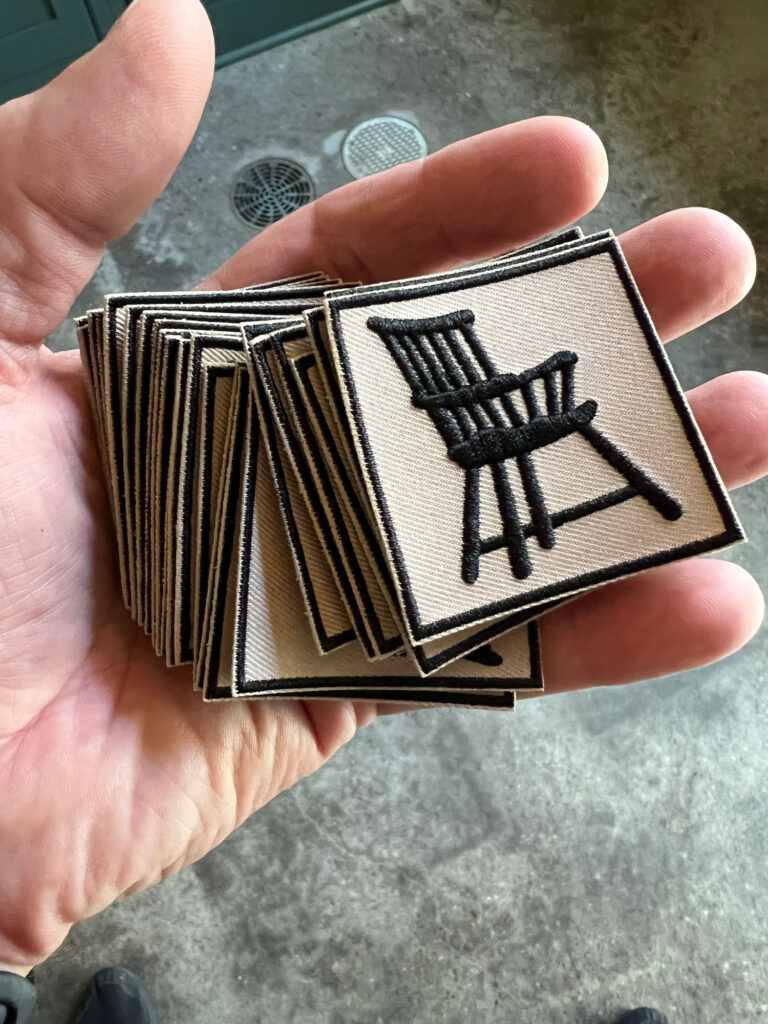
P.S. We still have PLENTY of Stick Chair Merit Badges to give away. Here‘s how to get one!