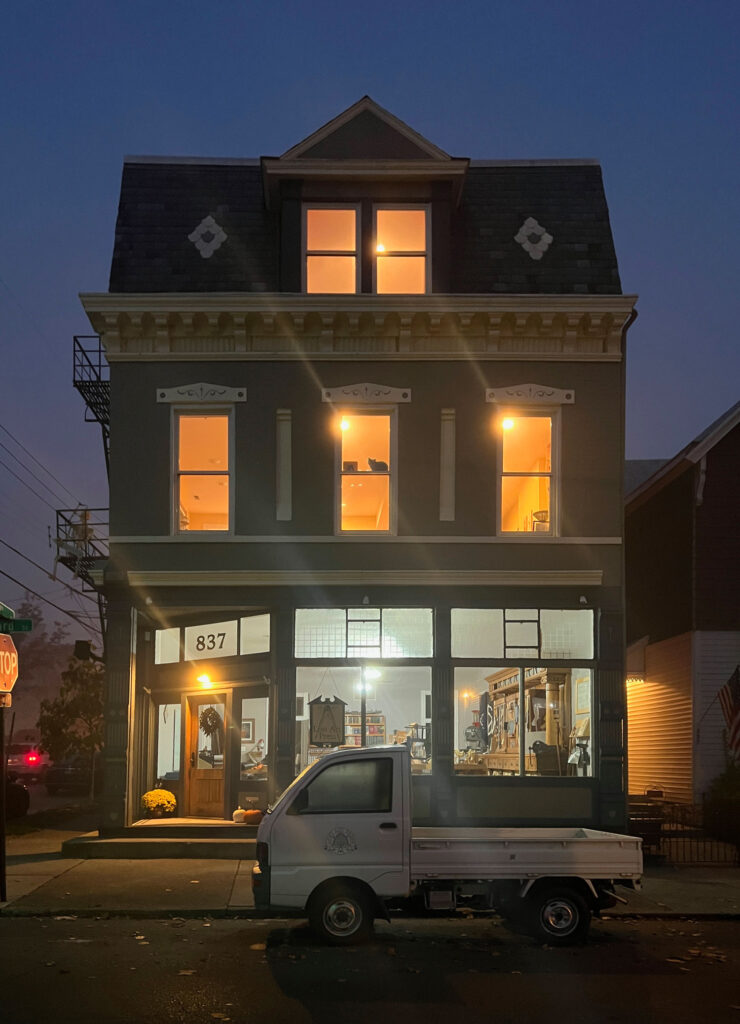
As Lost Art Press enters its 16th year of operations, I am amazed we are still here. We have made so many errors – some of them nearly fatal. Likely the reason we are still operating is that we are too dumb to quit. If I had to “make” every LAP book with a photocopier and a stapler, I’d probably do that before closing our doors.
If you run a small business (or hope to), some of our mistakes might serve as warning flags for you. Here’s a partial list. The complete list would be as long as a book.
- We trusted a FedEx salesman as to what our shipping costs would be when we signed up with the service. In less than two months, the company’s shipping costs almost drained our cash reserves. We now take a very granular approach to evaluating shipping costs and know exactly what we are paying for every shipment. Lesson: Don’t trust – *and* verify.
- We ordered too much inventory during the pandemic. Everyone made business mistakes during the last few years. We panicked when printing times went from five weeks to six months. And then we sank too much money into inventory. Good thing we’re not Lost Art Meat (books don’t spoil). We had our first “sale” over the summer to help correct the inventory problem. But it remains a drag on us.
- We listened to customers and produced “The Book of Plates” – a volume of all of the illustrations in A.J. Roubo’s “l’Art du menuisier.” The printing bill was more than $135,000, which was more money than we had in the bank at the time. Somehow we managed to pay the printing bill. And then the book’s sales were terrible. Plus the book was so huge (size-wise) that we were spending hundreds of dollars a month just to store the unsold books. We managed to eke out of that situation and break even.
- Every single poster we’ve made (except one) has been a loser. We would have been better off lighting the money on fire and using that for heat during the winter.
- Our lovely Ebbets Field Flannels hats. So many were returned with a single message: “That Brim!” The hat was too fashion-forward.
- Teaching too much. In 2012 I was teaching on the road for 18 weeks. I hadn’t yet learned to say “no.” I missed my daughter Katherine’s birthday four years in a row as a result of my teaching schedule. It almost made me crack.
- Public email. I had a public email address for about 15 years. A lot of things about it were good – I enjoy conversing with woodworkers. But a small percentage of people were what Roy Underhill calls “Time Thieves.” People who exist only to drain you. One night when I was teaching at Roy’s I received an email from a reader asking insanely detailed questions about moulding planes that would take me more than an hour of writing to respond. The next morning Roy remarked that he had received this awfully long email from a guy asking all about moulding planes. It was the same guy. At that moment I decided that not every email deserved a response. And within a year (at John’s urging), I shut down my public email address. Editor’s note: Please don’t send them to me instead. – Fitz
- Working for free. While I was an editor at Popular Woodworking, we often spoke to woodworker’s clubs for free to help get the word out about our magazine, and we were paid by the magazine to do it. After I left the magazine, the clubs kept calling. And kept asking/demanding free LAP books for Christmas give-aways and club picnics. I learned to say “no.”
- Every future poster that I will rationalize and print and try to sell.
- Taking our eyes off expenses for even a moment. Anytime we weren’t paying 100 percent attention to our expenses, we made a small (or large) error. We now have a company motto: Expenses are like fingernails. They always need to be trimmed.
OK back to making books and dreaming up a money-making poster. Hmmm, squirrels with tool belts? Who wouldn’t want that hanging on their shop wall?
— Christopher Schwarz