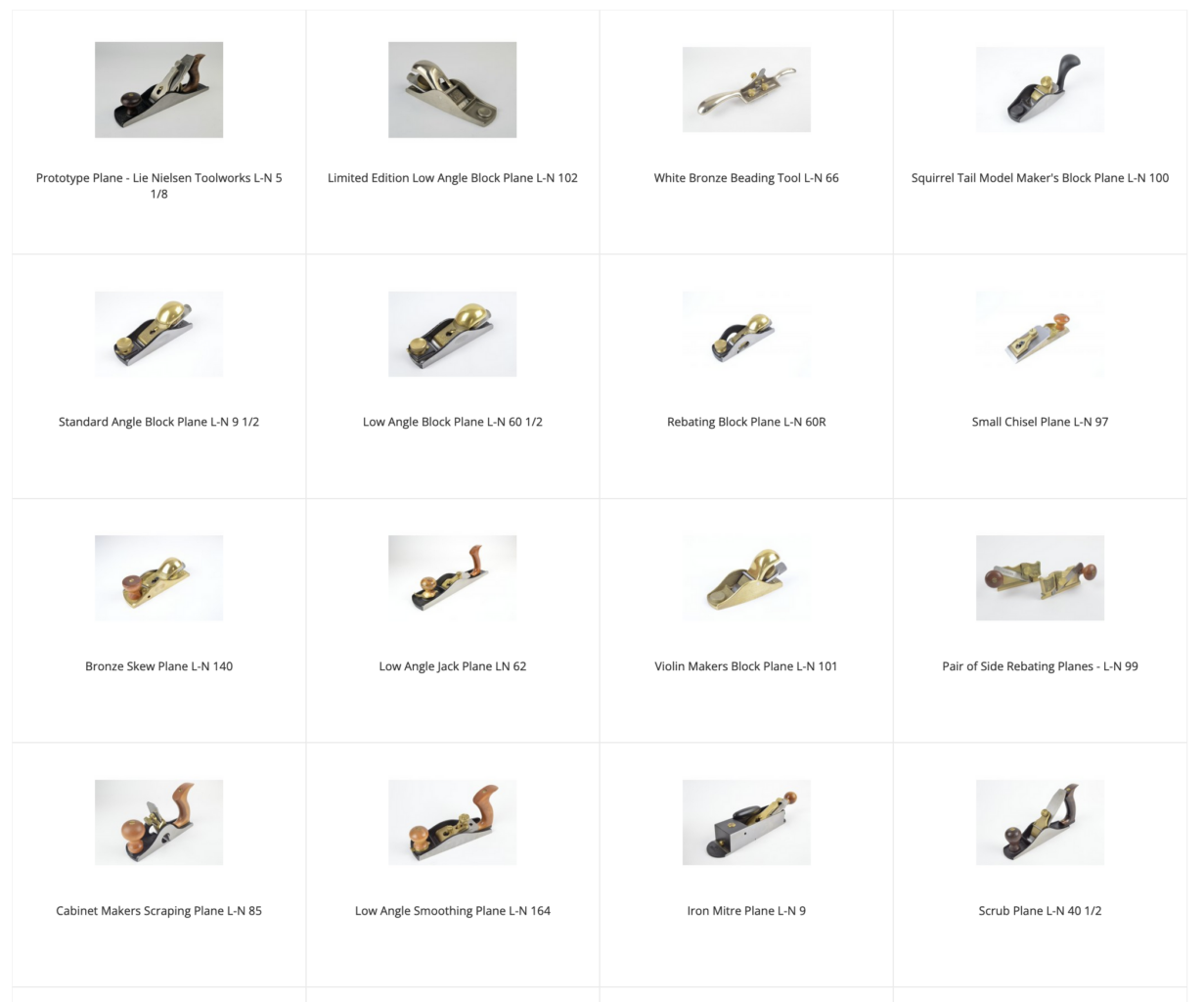
The U.K.’s Classic Hand Tools (CHT) has organized an auction of David Charlesworth’s hand tools – 100 of the best tools he amassed and used in his storied and half-century woodworking and teaching career. The auction proceeds will benefit David’s wife, Pat.
The tools – each professionally photographed and properly described – are available for preview viewing now, and are arranged by tool type – planes, saws, chisels etc. CHT notes that more information about each tool, and a price guide, will be added as/if that information becomes available. Online bidding begins on November 24 and ends on December 1 at 4 p.m. GMT. These are tools that David actually used, and as such are in excellent condition and ready to put to work.
This is a “best offer” sale – the person who submits the highest bid in the closed auction will be the winner. CHT will ship the items at cost. For more on how to bid and how it works, take a look at any of the items on the CHT pages – at the bottom of each is a link for bidding information. Here again is the link for the main auction page.
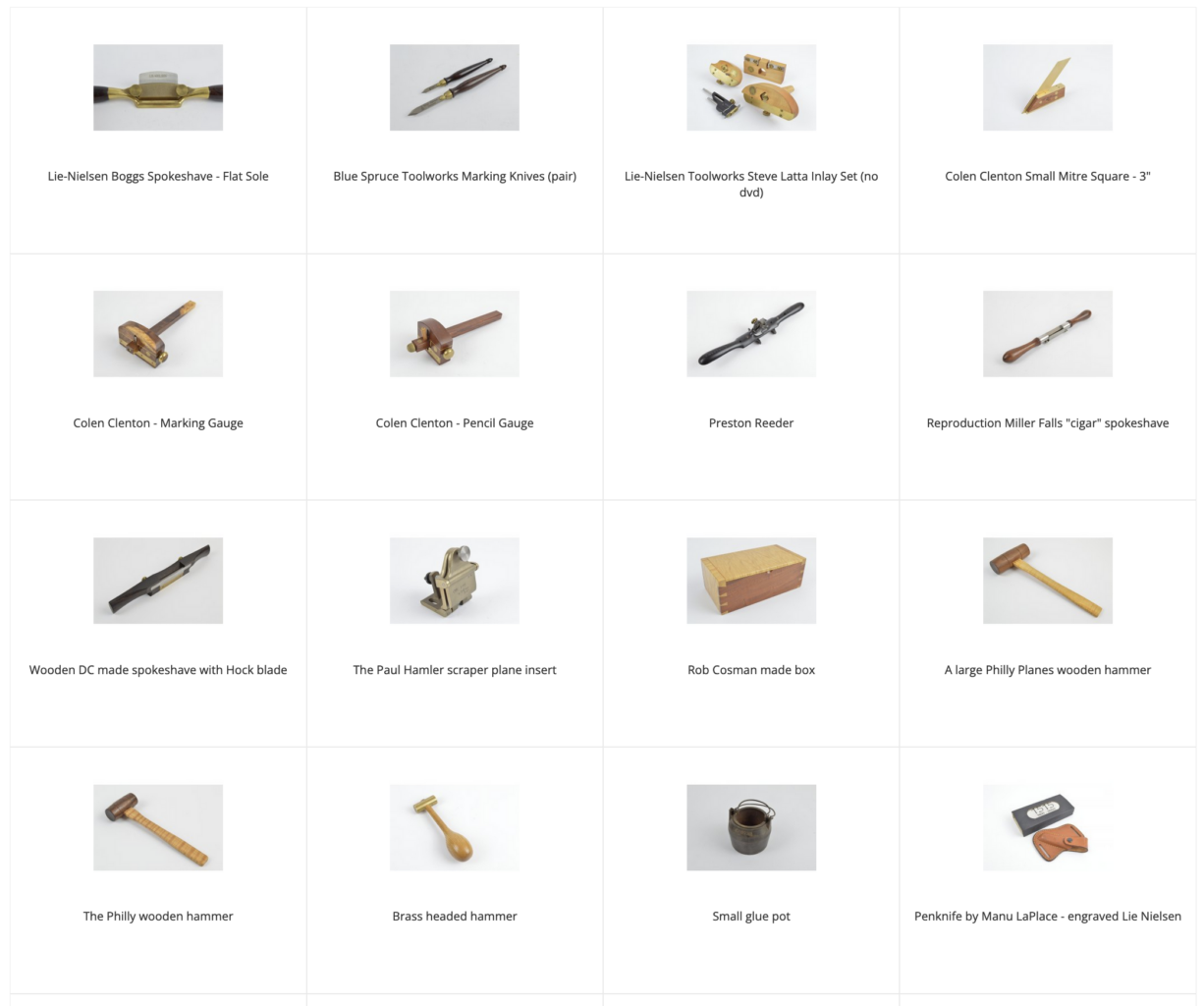
– Fitz
p.s. You can read more about David in this post by Christopher Schwarz. Or by simply Googling him. He was a woodworking giant, and is greatly missed.