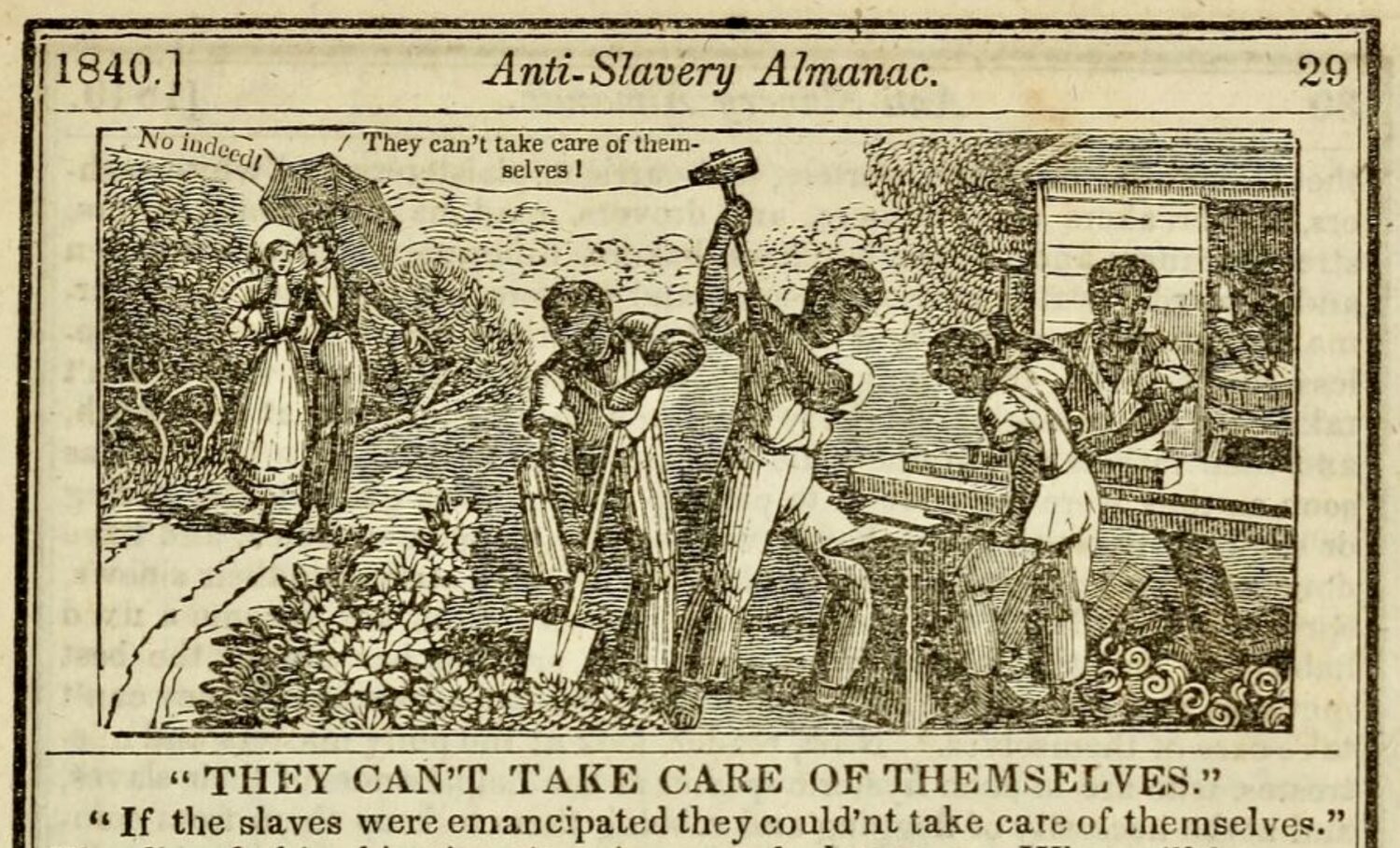
One of the arguments used by pro-slavery groups was the idea if enslaved people were granted their freedom they would not be able to take care of themselves. Abolitionists like to point out exactly who was doing the work in the states where slavery thrived. A portion of the counter argument is below.
After gaining his freedom Henry Boyd headed on foot to Cincinnati. He arrived in 1825 or 1826 ready to work. From a young age he had worked on a farm, sometime in his teens he was hired out to work at the Kanawha saltworks and he had learned carpentry (likely from an apprenticeship). He could also read and write, which was allowed under Kentucky laws.
The Initial Years Navigating a Hostile City
In a city growing as rapidly as Cincinnati in the mid-1820s there was plenty of carpentry work available, unless you were a Black man. When Boyd arrived in the city the Black population was just under 700 (4.5 percent), compared to a total population of 15,540. He was refused work and white men would not work beside him. Skilled or not, Boyd and other recently freed Black workers were left to seek lower-paying jobs. There was also direct competition with newly arrived immigrants from Europe.
Boyd eventually worked as a laborer along the riverfront. The “Proceedings of the Ohio Anti-Slavery Convention of April 1835” provide this detail:
By 1829 the Black population of the city was 2,258, approximately 9.4 percent of the total, an alarming number to much of the white residents. In June of that year the decision was made to “rigidly enforce” the requirement of a $500 surety bond, one of the Black Laws of 1807. Black residents were given 30 days to comply. Rigid enforcement was taken to mean violence would be used. Previous to this announcement Black leaders had been working to help residents establish their own communities outside of Cincinnati and others were negotiating land purchases in Canada. They asked for more time. By August the city was restive and some residents evacuated.
The attacks began on August 15 and continued until the 22nd. Mobs of white, mostly working-class men, moved through the Fourth Ward attacking Black residents and burning houses and businesses. The police did not intervene and city officials and business leaders stayed quiet. The newspapers of Cincinnati did not publish accounts of the riots, but the newspapers outside the city did. The number of people killed, white or Black is unknown.
Between 1,100 and 1,500 Black residents left Cincinnati. The city lost a large labor pool, entrepreneurs, businesses and taxes. Between the years 1830-1860 the Black population was never more than 4.8 percent of the total population.
Henry Boyd stayed in Cincinnati. By 1829 he was likely married to Keziah and was supporting her and Sarah Jane, his stepdaughter. He had work and was saving to buy the freedom of his sister and brother. At age 27 he probably had a very good idea of the obstacles he would continue to encounter in Cincinnati.
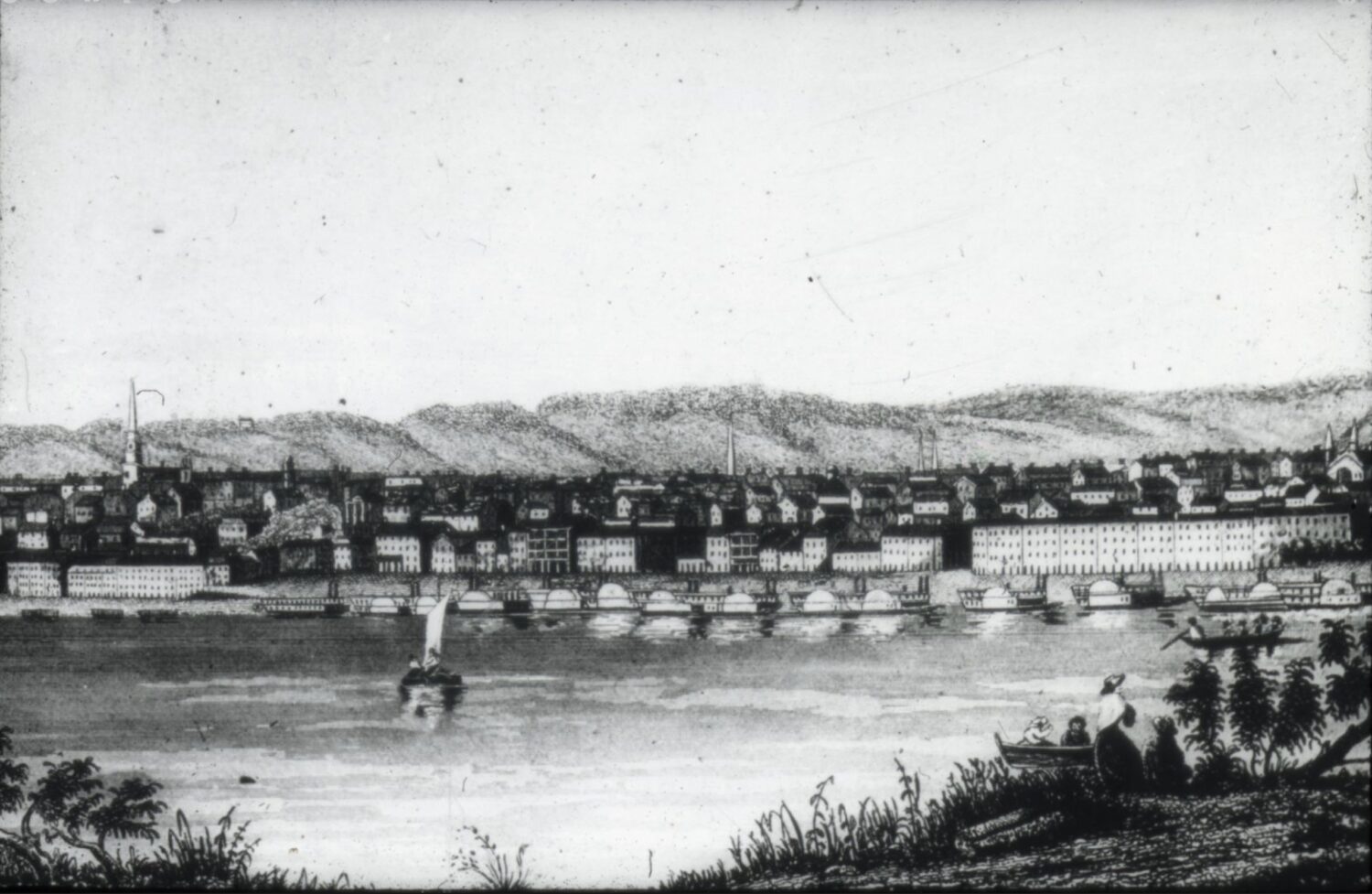
A variety of documents from the 1830s provide some good detail on Boyd activies during his first full decade in Cincinnati. It was a decade of intense labor and consequent reward for Henry Boyd.
Boyd is not listed in the 1829 city directory (the earliest available) and a directory is not available for 1830. His first listing is in 1831.
He is living and working from New Street, between Sycamore and Broadway (“do” is an abbreviation for ditto). His city directory listings remain the same until 1839.
The Cholera Epidemic
In the summer of 1832 newspapers reported the outbreak of cholera in New York and other cities. With its location on the Ohio River, it was not of matter of if, but when, cholera would reach Cincinnati. The epidemic began in the city in October.
Medical authorities of the time were correct that cholera was not transmitted from person to person, instead it was thought to be airborne. The air in the poorest sections of the city, the miasma, was suspected to be a cause. It was true the communities most affected by cholera outbreaks were those in lower-lying and crowded areas populated by they poor, but sanitation was lacking throughout the city. One thing the epidemic revealed in Cincinnati and other prosperous cities was a misery that had mostly been hidden.
Henry Boyd may not have been the only Cincinnati resident that thought cholera was spread through water, but he took the extraordinary step of communicate his idea to the editor of one of the city’s newspapers. From the Liberty Hall and Cincinnati Gazette of October, 1832:
We don’t know how many people followed this simple life-saving solution. His solution was certainly undercut by how it was introduced. It would be another 22 years before it was definitively proven that cholera was contracted in contaminated water.
George Porter and the Bedstead Fastener Patent
The patent for his bedstead fastener was likely submitted sometime in 1831 or 1832 and was granted on December 30, 1833. The listing can be found in the List of Patents for Inventions and Designs Issued by the United States from 1790 – 1847.
The patent is No. 7911X and a copy of the patent application with drawings is unavailable. A fire in December 1836 destroyed almost all of the records at the U.S. Patent Office. A request was made to all patentees to send patent documents to the Patent Office for copying. It doesn’t seem George Porter or Henry Boyd complied with this request.
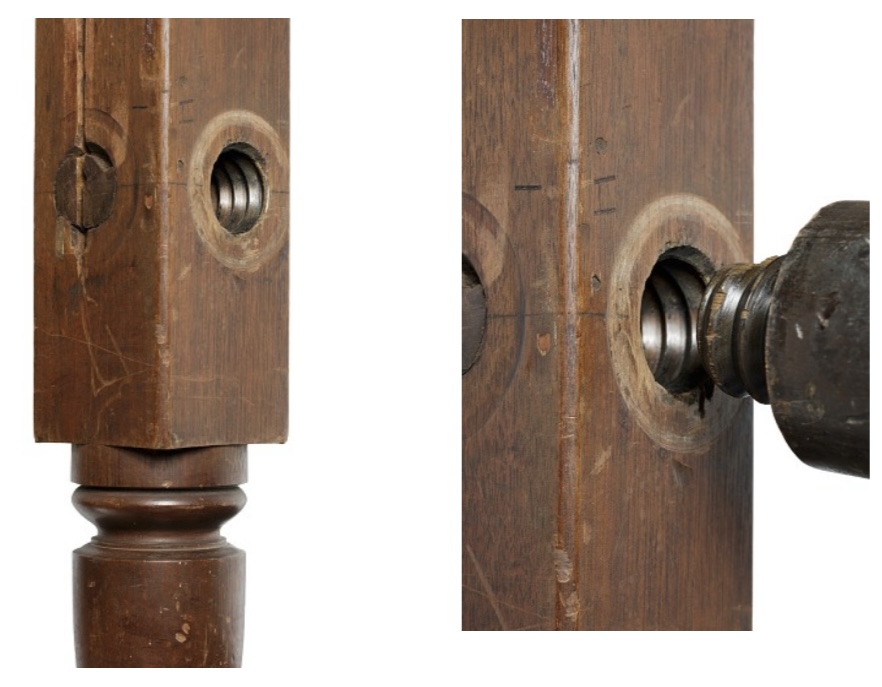
George Porter was a Massachusetts cabinetmaker, active from 1817-1849. He arrived in Cincinnati around 1823 and by 1826 was operating a his own furniture shop at the “Sign of the Golden Eagle” at the corner of Main and Seventh Streets. Porter’s shop was just a hop, skip and jump from Boyd’s house on New Street.
Why isn’t the patent under Henry Boyd’s name? Although Henry Boyd was legally able to apply for a patent, as could any Black inventor, enslaved or free, he may not have known this. He may have been denied help from a patent lawyer and/or been given false information about the process. Porter, a trained cabinetmaker with an established business, seems to be the logical person to ask for help. It is apparent they knew each other and Porter may have sent work Boyd’s way. The two may also have had a financial agreement.
An English Abolitionist Visits
E.S. Abdy visited the United States between April 1833 and October 1834. He met with several men from Lane Seminary (later, the abolitionist Lane Rebels) and was taken to visit Henry Boyd at his home in New Street. From Abdy’s Journal of a Residence and Tour in the United States of North America from April 1833 to October 1834, Vol. 2 we have this description:
This passage verifies when Henry Boyd purchased is own freedom, “about eight years before” and that he had also freed his sister and brother. It is also the first description we have that verifies Boyd is running his own shop and is employing both white and Black men.
Henry Boyd, House Builder
Tax assesment records for 1835-1838 show Henry Boyd paying taxes in an area named Burrows Smith. Was this his home location or where he had a separate shop? Fortunately, the Cincinnati History Library and Archives sent me a copy of a law suit filed by Henry Boyd and the Burrows Smith mystery was solved.
Boyd built a frame house for James Carr on the north side of New Street in the subdivision (or plats) of Burrows Smith. The house was finished on May 14, 1836, and other than receiving $6.34 from Carr, Boyd was owed $334.76. Boyd filed the suit for payment on May 22, 1836 and a full account of materials, labor and costs are listed.
The wood frame house was built on the east half of plat 11. The front footage of the lot was 15 feet and the depth 90 feet. The house had two stories with upper and lower porches. The exterior had weatherboarding applied and the roof had wood shingles. The house builders among you can revel in the rest of the details.
The suit against James Carr verified the kind of work done by Henry Boyd prior to opening his bedstead factory and that he was working from a shop at his home on New Street and not at a separate location. The detailed list of the cost of materials and labor demonstrate he had the necessary accounting skills for a self-employed mechanic.
Towards the end of my research on Henry Boyd I found an article that provided more background on how he became a house builder.
In 1877, the Cincinnati Commercial newspaper published a biography of the now-retired Boyd.
House Builder No More
In the city directory for 1839-1840 Henry Boyd had two listings.
In the main section was his residence:
The publisher of this directory included a Colored Section and here is Boyd’s second listing:
Henry Boyd had opened his bedstead factory at the corner of Broadway and Eighth.
This map from the Library of Congress is dated 1838. The color dots show the location of George Porter’s shop at the corner of Main and Seventh (green dot), Henry Boyd’s home on New Street between Sycamore and Broadway (blue dot) and the bedstead factory at the corner of Broadway and Eighth (red dot). Plat 11 on New Street is where Boyd built the house listed in the 1836 suit. You can also see where Henry lived and worked in relation to the Public Landing on the Ohio River. Click on the map for a closer look.
Within a span of 13 to 14 years Henry Boyd gained his freedom, found steady work and a home, married, freed his sister and brother from slavery, patented a bedstead fastener and opened his bedstead factory.
It is safe to say Henry Boyd could take care of himself.
— Suzanne Ellison