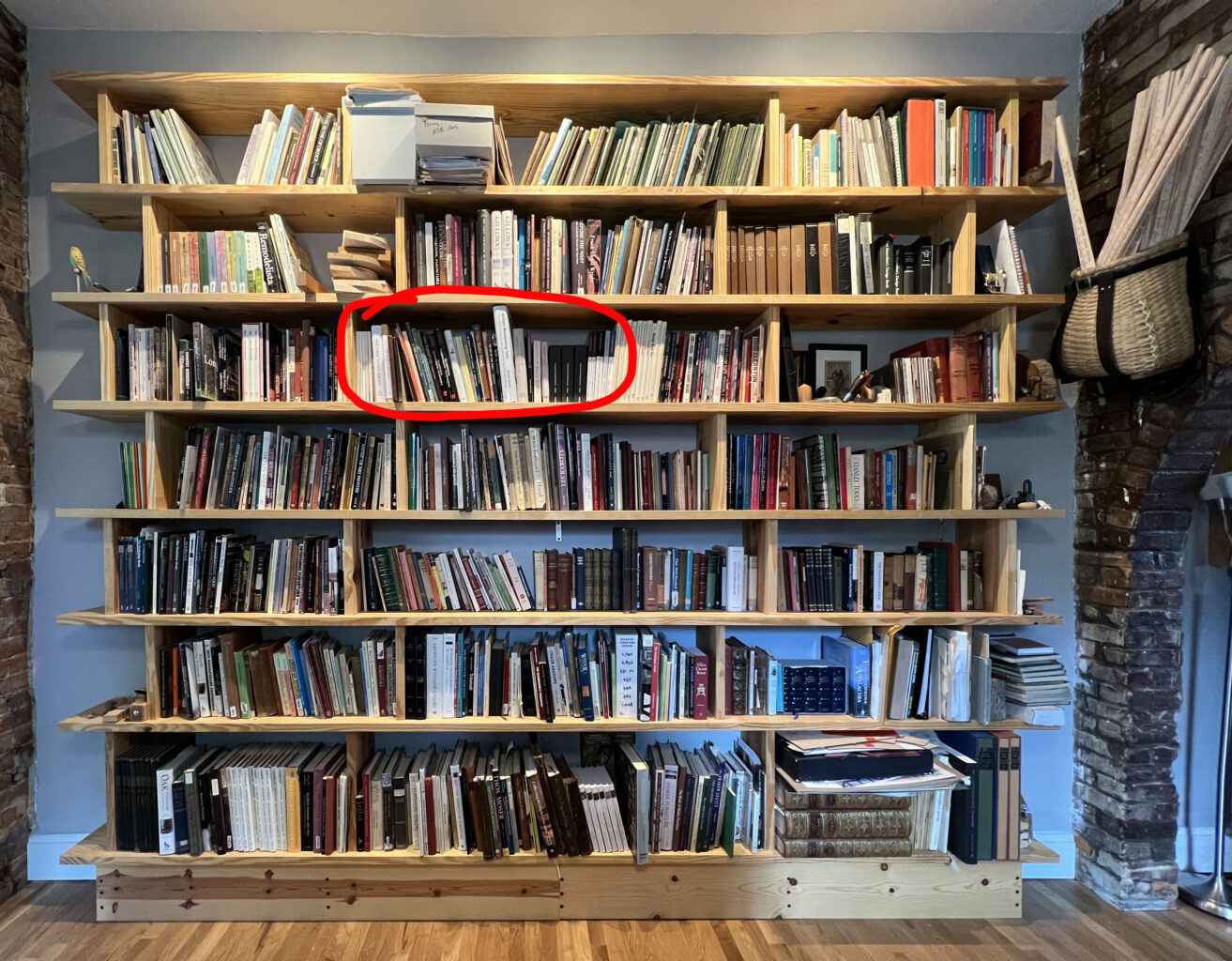
We sure have a lot of sundry/miscellaneous/mixed/jumble shelves. Could be worse; at least we don’t shelve books by color. (We do, however, shelve a few by size; we’ll visit that lower-right corner soon).
On the far left of this bay is most of our “Mortise & Tenon Collection,” both some issues of the magazine and the two books M&T has published (between us, we have all the issues, just FYI). When Joshua Klein first mentioned to us he was thinking of starting a magazine both Chris and I independently told him not to do it, then shared with him everything we could think of about doing it right. Good thing he didn’t listen to us (about not doing it; he’s certainly doing it right).
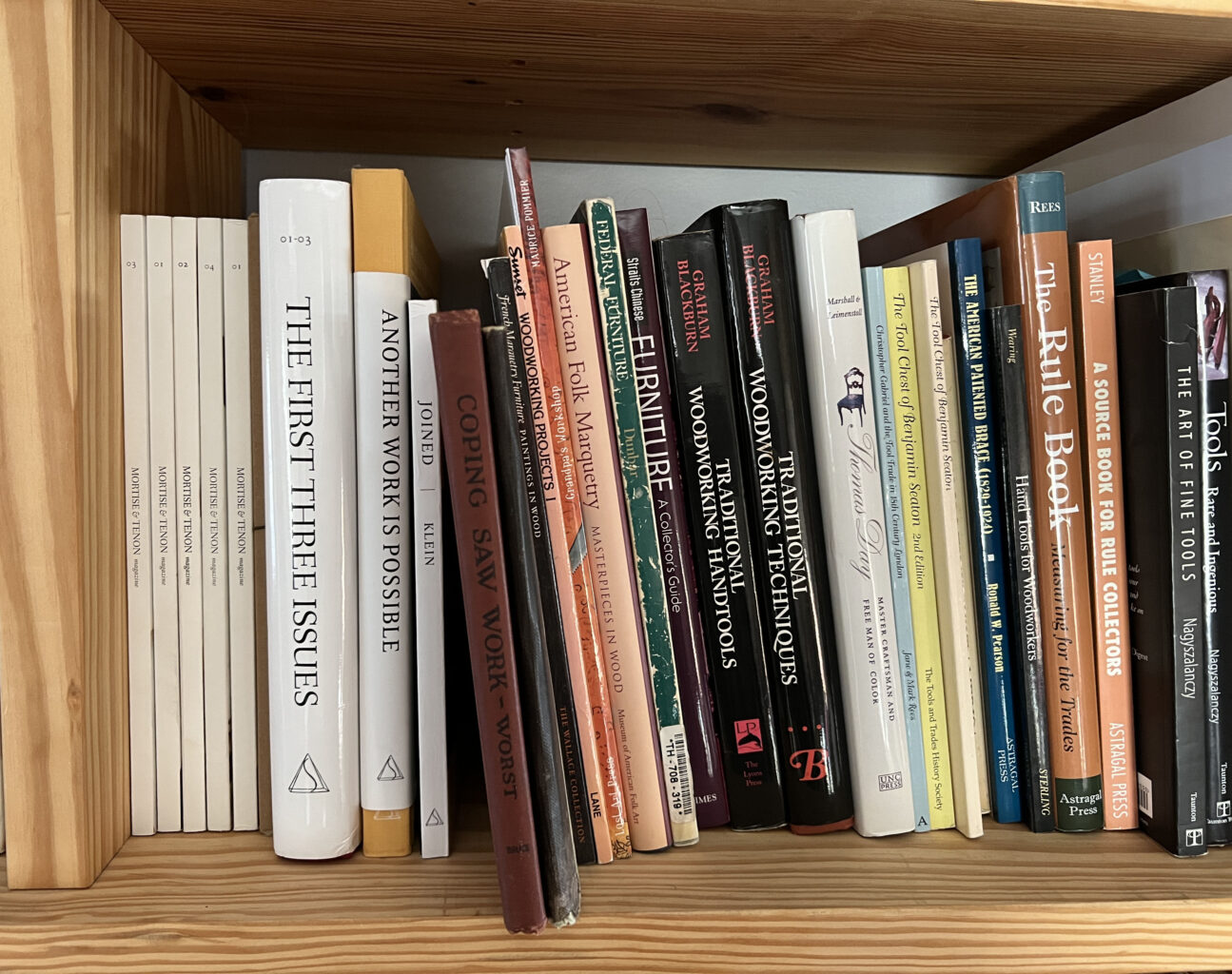
And then comes the jumble. We have two copies of Edward F. Worst’s “Coping Saw Work” (First published in 1927 by Bruce Publishing). This book is, according to Chris, a “cool representation of the humidor or turned pens or epoxy river table of the early 20th century.” I other words, it’s a slice of a small point in history when coping saws were the hottest thing. And I gotta say – the Minecraft-looking animal patterns are pretty cute.
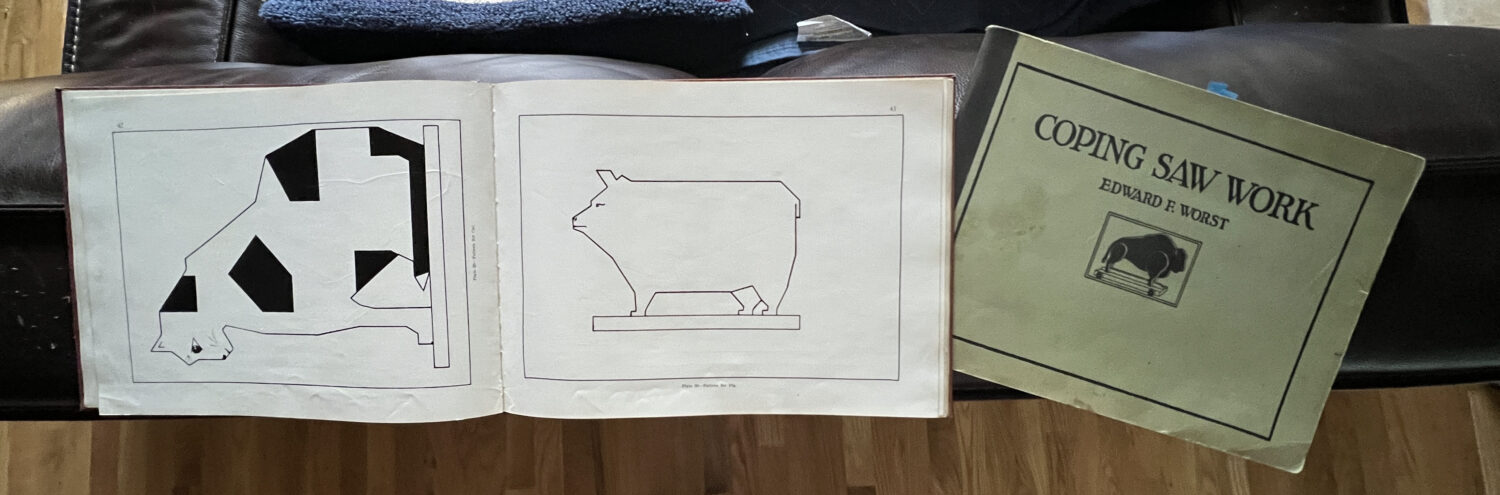
But if it’s toys you’re looking for, the compilation book “Sunset Woodworking Projects 1” (Lane Publishing, 1987 – first published in 1975) is chock-full of pre-computer-chip offerings for the little ones and simple projects for around the house. Chris has it not for the contents so much as for the layout – it is easily identifiable as of a certain period in book design history, which is always useful when thinking about how things should/could/shouldn’t look.
Next to that is Yannick Chastang’s “French Marquetry Furniture: Paintings in Wood” (Wallace Collection, 2001). Chris met Chastang in London (he thinks it was London) and was impressed with a talk he gave, so of course he bought the book. In between that and another marquetry book is a “hidden” copy of “Grandpa’s Workshop” (I think it’s our last copy, and we don’t want it at easy grabbing level). The other marquetry book is Richard Mühlberger’s “American Folk Marquetry” (Museum of American Folk Art, 1998); it reminds us of a lot of Kentucky furniture (for which both Chris and I have a great fondness).
Michael Dunbar’s “Federal Furniture” (Taunton, 1986) is an ex-library copy and was too good a buy to pass up (and though neither of us are huge fans of the style, it does deserve representation in any woodworking library). Then we’ve a gifted copy of “Strait’s Chinese Furniture: A Collector’s Guide,” by Ho Wing Meng (Times Media, 1994).
Then we’ve Graham Blackburn‘s “Traditional Woodworking Hand Tools” (Lyons, 1998) and “Traditional Woodworking Techniques” (re-published by Blackburn Books in 1994). These are “must-haves” for the hand tool woodworker; Graham was writing about hand tools and teaching their use when just about no one else was. (An aside: Graham is among the nicest guys I’ve met in woodworking, and is also an excellent musician and dancer!)
Thomas Day: Master Craftsman and Free Man of Color,” by Patricia Phillips Marhsall and Jo Ramsay Leimenstoll (North Carolina Museum of History/UNC Press, 2010) is a landmark book. It’s the first significant book on a Black furniture maker and his contributions to the craft, the first to acknowledge that Black people didn’t historically just work in menial positions in the United States, but were skilled tradespeople with important jobs.
From there, we move into the tool section of our collection (for the most part) – and it continues on several other shelves still to be covered. First up is a trio of books edited by Jane and Mark Rees: “Christopher Gabriel and the Tool Trade in 18th Century London” (Astragal, 1998) and both editions of “The Tool Chest of Benjamin Seaton” (Tools and Trades History Society 1994 and 2012).
Then we have “The Tools that Built America,” by Alex W. Bealer (Bonanza, 1976). “Someone told me I had to have it and gave it to me,” says Chris. “I flipped through it and was like, meh.” (But not so “meh” that we’ve passed it on to someone else, yet.) Alongside it is “The American Patented Brace, 1829-1924: An Illustrated Directory of Patents,” by Ronald W. Pearson, D.O. (Astragal, 1994) and “The Rule Book: Measuring for the Trades” by Jane Rees and Mark Rees (Astragal 2010). I dipped into these books that are ostensibly for collectors quite a lot when I was editor of The Chronicle, Chris loves them not only for the history of toolmaking, but because “they show things that are missing from the written record – it’s written in tools, not in words.” And that holds true for the rest of the tool-related tomes in this bay.
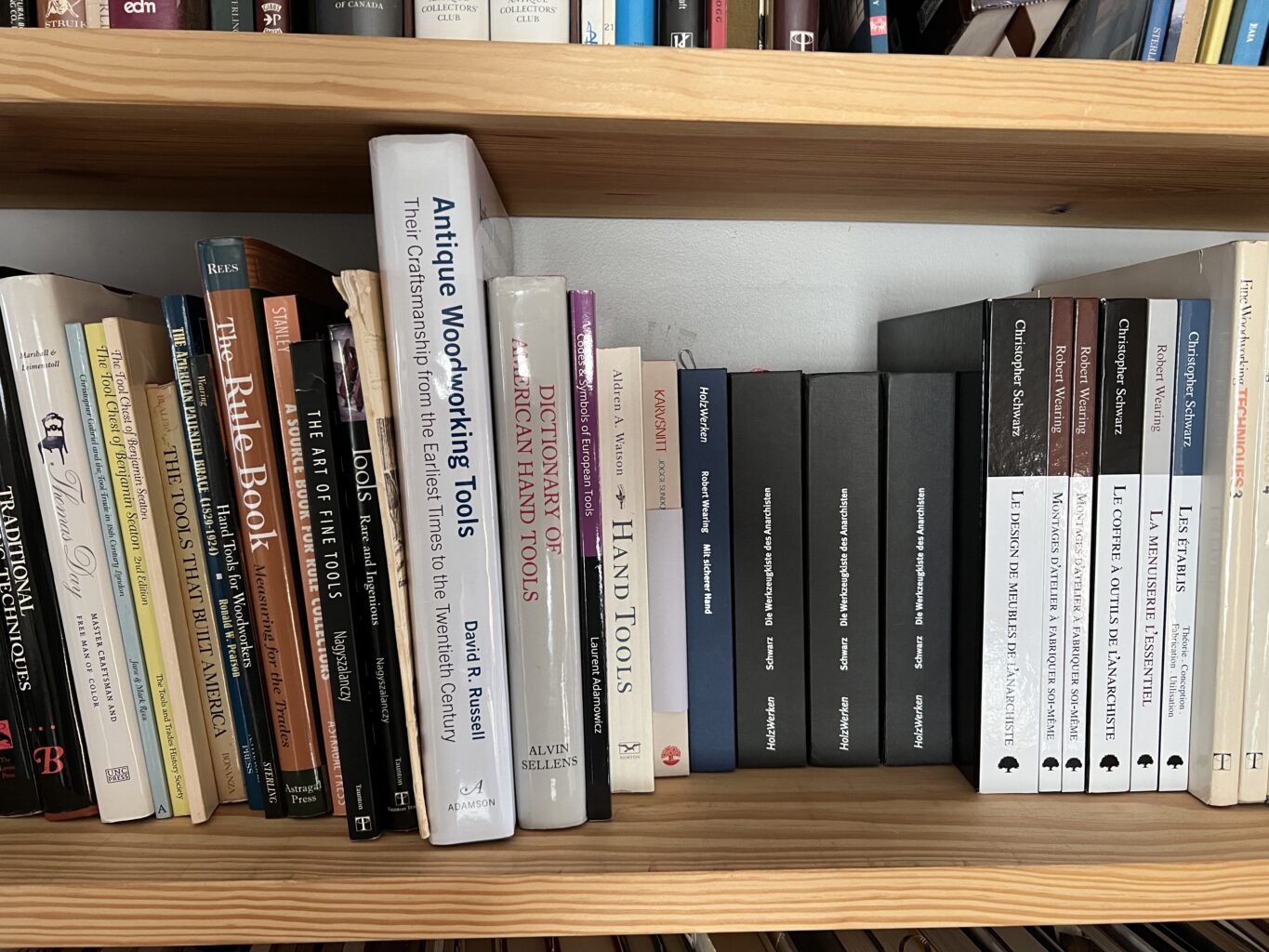
Tucked into those is Robert Wearing‘s “Hand Tools for Woodworkers” (Sterling, 1996). That should probably be with Wearing’s other books. Then it’s “Source Book for Rule Collectors,” by Philip E. Stanley (Astragal, 2003), “The Art of Fine Tools” (Taunton, 2000) and “Tools Rare and Ingenious (Taunton, 2004), both by Sandor Nagyszalanczy. If you like nice-looking tools, these are must-haves. Peter C. Welsh’s thin but invaluable “Woodworking Tools 1600-1900” (Smithsonian, 1966) is a must for the tool-history lover.
David R. Russell’s “Antique Woodworking Tools” (Conti, 2010) documents an insanely good collection (in a well-made wrapping), and serves as inspiration for our own tool and book making. It’s just gorgeous to look at. “A Dictionary of American Hand Tools,” By Alvin Sellens (Sellens, 1990) is among our many tool dictionaries – books that we as teachers and toolmakers count as must-haves. The same holds true for Aldren A. Watson’s “Hand Tools: Their Ways and Workings” – but with a grain of salt, as he recommends everyone have a jack rabbit plane. Huh. But he’s masterful illustrator; the drawings are an excellent look at the way tools go together. “Codes & Symbols of European Tools,” by Laurent Adamowicz was too intriguing to pass up. “I’m always interested in tools, and that was an aspect that I’ve never seen covered. But it didn’t quite live up to the title,” says Chris.
And finally, we have the German and French editions of several of our books, and one of Chris’s earlier books for Popular Woodworking. (The right side of this bay was covered in an earlier installment.)
– Fitz
This is the eighth post in the Covington Mechanical Library tour. To see the earlier ones, click on “Categories” on the right rail, and drop down to “Mechanical Library.” Or click here.