
John Porritt, author of “The Belligerent Finisher,” has been designing and building furniture, restoring furniture and tools, as well as making chairs inspired by older Welsh stick chairs and English country Windsor chairs for more than four decades.
Born in 1953 in a military hospital in Aldershot, a town in Hampshire, England, John was the youngest child of John and Myra Porritt. At the time, his father was teaching at the Royal Military Academy Sandhurst. Growing up in an army family, John moved around a lot, eventually attending six different schools throughout his childhood.
“I’ve always felt slightly removed, not part of any group, an outsider through the years. And that’s OK. It opened my eyes to a lot of things, meeting different people and getting to know some of them. My mother was very supporting and accepting of my brother, sister and I. She was very creative. She understood line and form. My father’s credo was: ‘Be firm but fair’.”
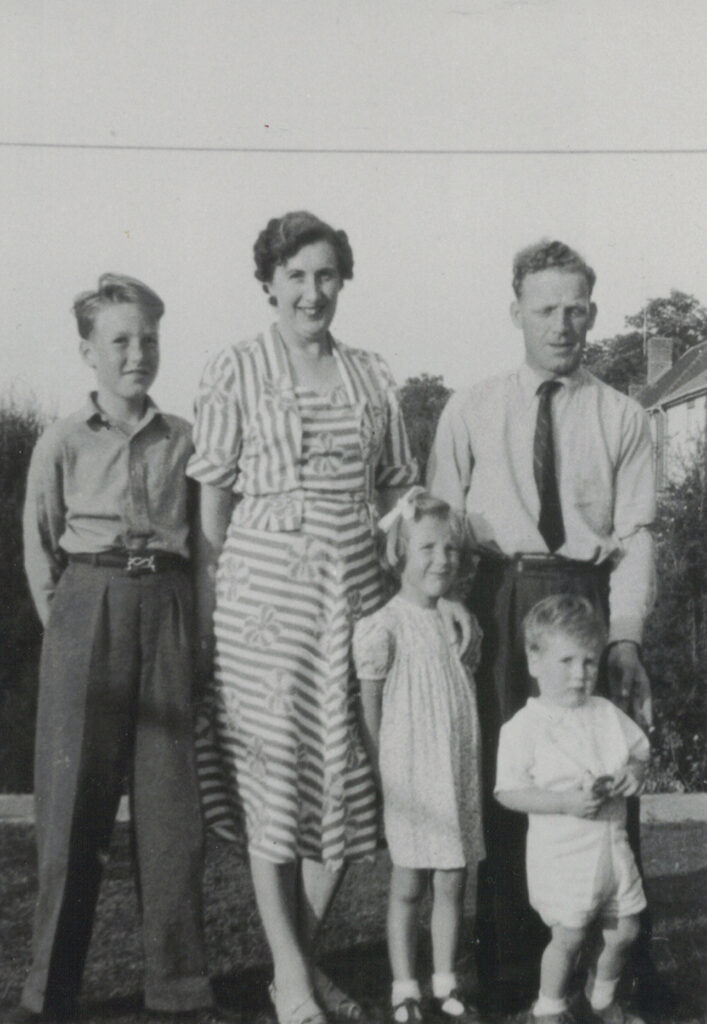
In 1957, the Gold Coast became Ghana, gaining independence from British rule. Prior to this, John’s father had been seconded from the British Army to help train the Ghanaian Army, so John’s family had moved to West Africa.
“Some of my earliest memories are from the village of Teshi, outside of the capital Accra,” John says. “Company Degarti, originally from Liberia, would watch out for me in the garden, pointing out lurking snakes, including a very thin poisonous black one that looked like a boot lace. I remember him picking me up to get bananas from the trees in the garden, cutting the pineapples growing down low, and us together digging up peanuts – which my mum would roast. Once, I saw Company sit down suddenly, take out his knife, cut into his heel, then quickly sucking at the wound and spitting out the poison from the snake bite. He did get better. What wonderful man with a great name – Company.
“I would see the Hausa men from the north, selling their beautiful carvings door to door, very tall and dark in their immaculate white robes. They moved so slowly, pacing themselves in the heat.
“I remember my family together on a golden, sandy beach, looking off in the distance to a beautiful white castle: Christiansborg Castle. My father wouldn’t take us there. Years later, I found out that it was a slavers’ castle, built for human beings to go directly into the boats to be sent to the slave markets.”
When John was 6 years old, they moved back to England. They lived on the 5th floor of a hotel in Portsmouth, Hampshire.
“I started to go bald,” John says. “It was something called alopecia. My mom would take me to a hospital to have this stuff rubbed into my hair. They worked out that I was so used to being on the ground in the bungalows that living up high was very stressful for me, or, at least, that’s what the theory was.”
So John and his family moved to Romsey, Hampshire. A quiet boy at the time, John attended church school. The head teacher “…was a bit of a sadist,” he says, “who used to cane certain children regularly.” At just 10 years old, John walked out of school one day, angry that he was about to be caned yet again for something he did not do. Through school, John spent a lot of time in Romsey Abbey, built in the 10th century.
“I remember, at 10, being impressed with the light coming through the windows of the stained glass onto the stone, that soft sunlight and the effects it would make on the building,” he says. “And I loved singing in the choir.”
Broadlands, Lord Louis Mountbatten’s estate, was nearby, so Queen Elizabeth II would come twice a year and attend services in the abbey. During those services, John, a choir boy, would steal glances at the Queen – the head of the Church of England – sitting alone in her pew by the high altar instead of his tucked-away Southampton football program, which was his usual go-to.
“I remember being completely impressed by the color of her coat,” he says. “Later, I found out that she was dressed by Hardy Amies, and he was known for the cut of his clothes. She had this beautiful blue that she would wear and it was just stunning. She looked wonderful.”
John attended three more schools before leaving at 15.
“My favorite subjects were history, geography, English and running. Running for me was a chance to get out on my own, with my own thoughts. I was the school cross-country champion. But it was a small school. I was glad to finish school and get out into the world of the late ’60s.
Although he was a skinny teen, John first found work as a builders’ laborer. In the mid-’70s, he was walking around West Kensington and got a job at Stokecroft Arts making simple pine beds – lots of sanding, gluing dowels and screws.
“It was run by a guy called Bernie,” John says. “Bernie was a great guy in that he gave a lot of people a chance. He had a lot of soul, a lot of heart. He came to England just before the war at the age of 10 on a Jewish Kindertransport from Germany. I remember he wouldn’t get pissed off, he’d be disappointed. ‘Come on, John, you can do better than this.’ He was a great guy. Bernie was a great guy.’”
John moved to Kent with his girlfriend at the time and took a six-month carpentry course at a government skill center in Sittingbourne, Kent.
“I learned a lot,” he says. “I learned how to handle tools. I learned how to sharpen. The instructor there was a man named Peter Dense and he was excellent. Very small, very quiet. Authoritative but quiet. And for the first two days he gave me chisels and plane irons and told me to sharpen them and I’d sharpen them and bring them back and he’d say, ‘Do it again,’ and I did that for two days.”
Halfway through the course, John split up with his girlfriend, leaving him without a home.
“I ended up living in somebody’s cupboard,” he says. “In hindsight, it was horrendous.”
“I remember my mum had said to me, ‘What are you going to do? Just find something you love doing. Find something that interests you. Find something to do and do it.’ And luckily, I did. I think about people like Bernie, Peter Dense and later John Price and I’m kind of humbled, really. Decent people who helped me out, great teachers.”
John also spent many of his younger years traveling. For a while, he worked in Germany as a shuttering carpenter, making forms for concrete.
“I remember Germany in the mid-’70s as quite a place,” John says. “The gaps between the generations, the intensity of it all. At one stage I was working in Nuremberg. One evening I went to the area where the rallies had been held in the 1930s, now completely deserted, listening to Joan Armatrading on my cassette player and enjoying the sight and calm of the willow trees there, wondering about what had passed and all that had happened there.”
At one point John and his crew were sent to Munich, but the directions were incorrect. They ended up at a beer festival and the carpenters from London John was with decided to take advantage of the situation and get absolutely drunk. John decided to take advantage of the situation and visit the state art museum.
“I was looking at the Blue Rider artists, which included Kandinsky, Franz Marc and August Macke,” he says. “In Germany, it’s Blaue Reiter. Before the first World War, they did a lot of pictures of animals in gorgeous colors and this guy, Franz Marc, did beautiful horses, stunning horses, which seemed to me to be symbolic of freedom and joy.”
John moved back to England and found a job with a company called A.J. Dunnings, working on an interesting site in Winchester complete with a stone barn from the 15th century. Early on John remembers the foreman asking him to rehang some sliding sash windows. John took the first window out, changed the cords, properly cleaned everything, sorted it all out and put it all back together.
“It’s tricky stuff,” John says. “You’ve got to stretch the rope and get the weights properly balanced.”
John showed the foreman his work.
“It’s a great job,” the foreman said. “Great job, you’ve done it really well. But there’s only one problem. You put the top sash inside, and the bottom one out. That will let the rain in.”
John is a wonderful storyteller and most of his life’s stories contain lessons learned, some subtle, some not.
“What I had done was I had gotten completely absorbed in the details,” John says, when telling his sash-window story. “I had forgotten the overall idea, which I think is something that a lot of woodworkers do from time to time. And I think that’s quite an important lesson there.”
A fellow carpenter, Joe, at this particular job called payday “Golden Wonder Day.”
“I didn’t get what that was about,” John says. “Turns out, Golden Wonder was a brand of peanuts so he was saying, we’d be getting paid peanuts. I like the banter you get with working people. I enjoy that a lot.”
John has worked all sorts of jobs in his life, with all sorts of people. He talks about working in a massive, cavernous room with high ceilings in, he thinks it was, Strasbourg, striking forms and then dodging them as they dropped, “an absolute nightmare,” he says. He talks about unloading a brick lorry where people would chuck bricks, five at a time. They were on the lorry and he was off it – he’d catch the bricks and stack them. One of the loaders once called him John and surprised, John asked him how he knew his name.
“We call everyone we don’t know John,” the loader said.
John laughs, remembering.
John had worked as a day laborer with Jack Dee, who, at 16 years old, had a deadpan humor that everyone loved. Jack Dee became a nationally known comedian with his own television show, using that same deadpan humor he used on the job site.
And John remembers digging clay for a German potter in West Cork, Ireland, “an unbelievably beautiful area,” he says. It was 1971 and he and friend were hitchhiking through at the time. A man picked them up who turned out to be astonishingly drunk. Chaos broke out when John, sitting behind the man, was trying to get him to stop the car while the man was trying to reach for his shotgun.
John has stories for days.
— Kara Gebhart Uhl
Read Part 2 next Sunday (March 12).