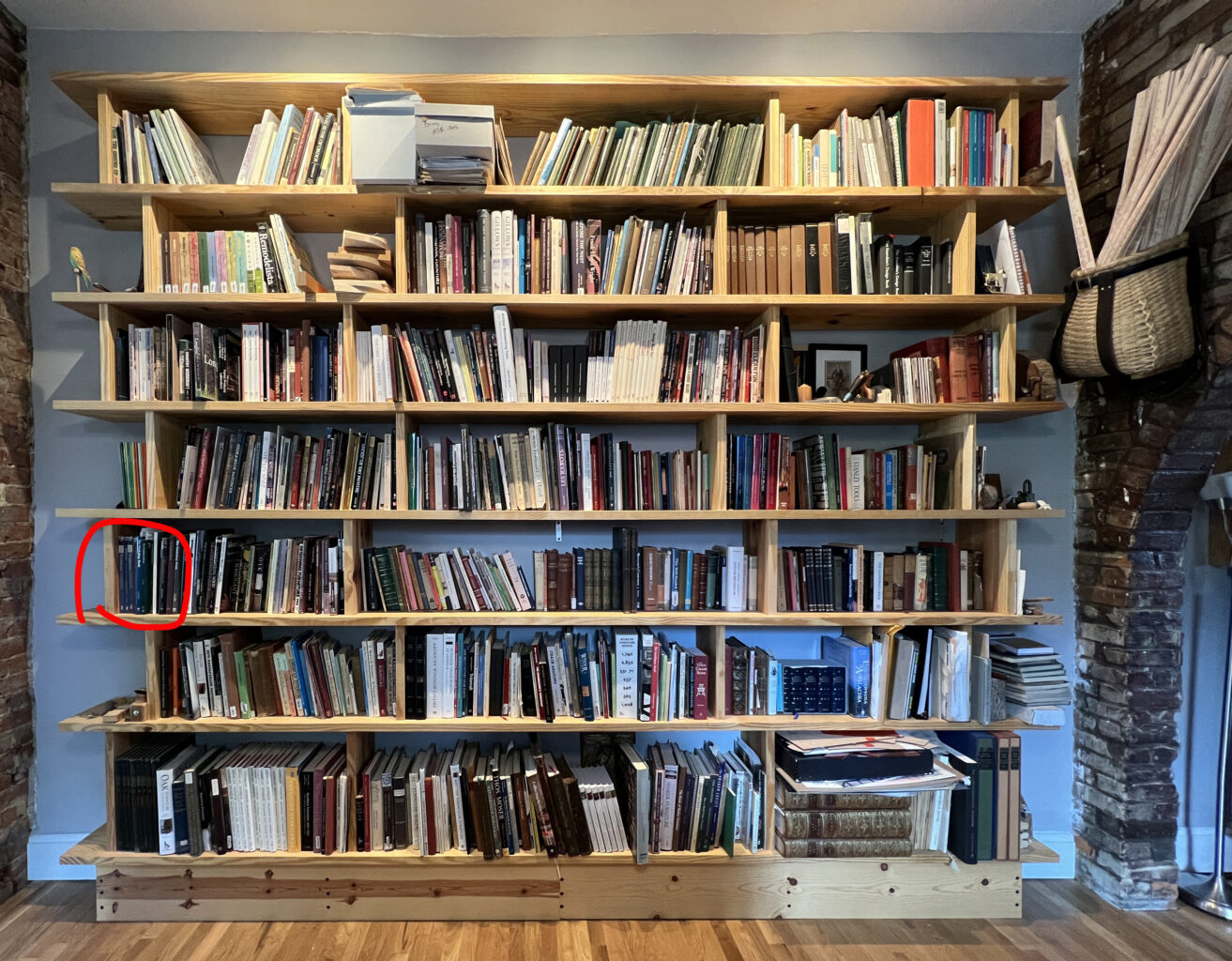
Christopher Schwarz might disagree, but I’d say this is the formative section of the collection: books on workbenches and tool chests – two things that are not only of importance in any shop, but of great importance to Chris’ woodworking history (and now mine – at least on the tool chests side of things).
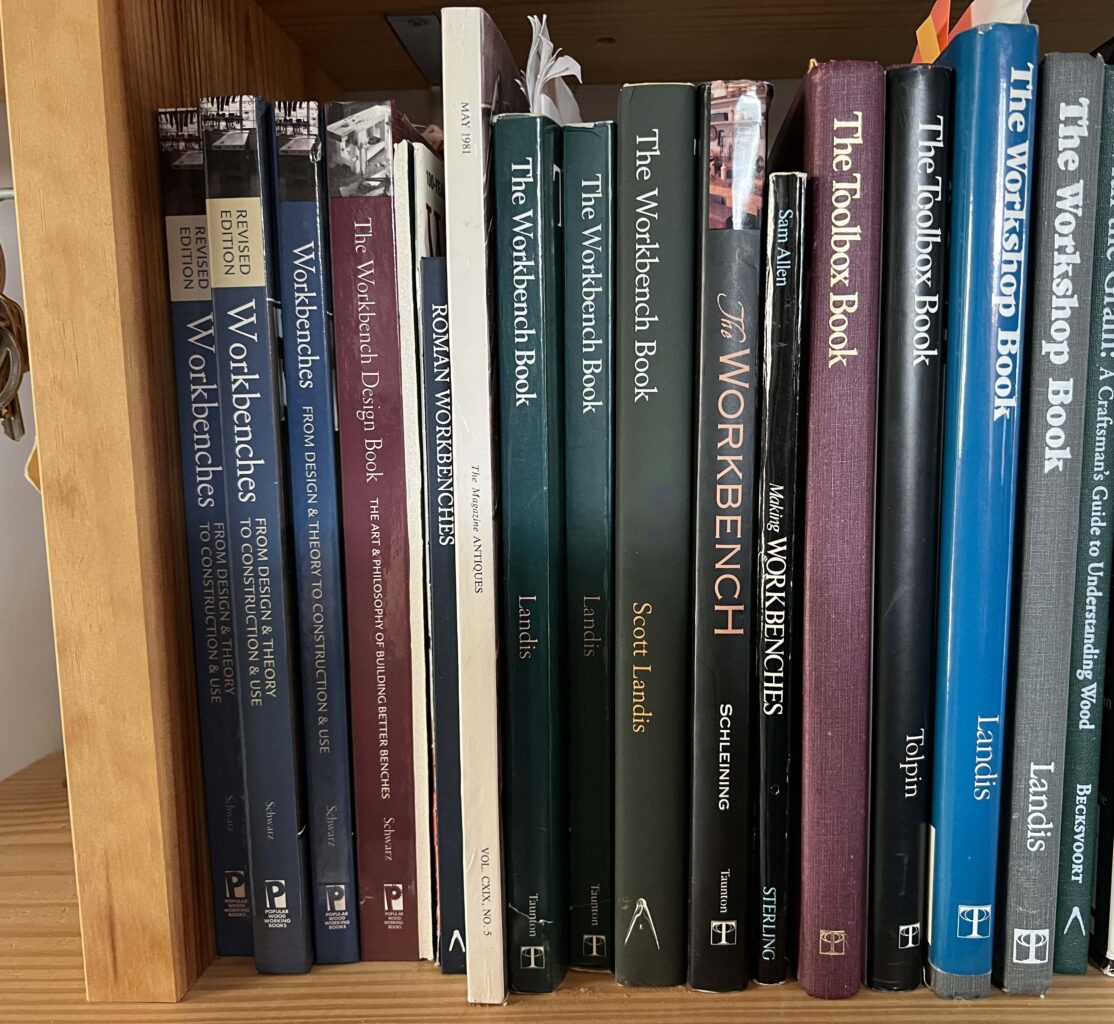
I don’t know how many benches Chris has built over the years, but my guess is at least 150 when you add up all the articles for Popular Woodworking Magazine, the various “ancient” forms in “Ingenious Mechanics,” “The Anarchist’s Workbench,” the many bench-building classes he’s taught…. It’s a lot.
The first book in this section reflects everything Chris knew about bench building circa 2007, when “Workbenches: from Design & Theory to Construction & Use” (Popular Woodworking) was first published. It’s alongside a couple copies of the revised edition from 2015, to which PW added a couple appendices Chris wrote for the magazine after he’d left to concentrate on Lost Art Press full-time. It’s followed by “The Workbench Design Book: The Art & Philosophy of Building Better Benches” in which all the benches published in Popular Woodworking Magazine up until that time (2010) were collected, followed by a critique of each after it had seen some use. (“The Anarchist’s Workbench” is a distillation into one perfect-for-him bench of everything Chris learned in his many years of bench building…a time he claims has concluded. I don’t believe that.)
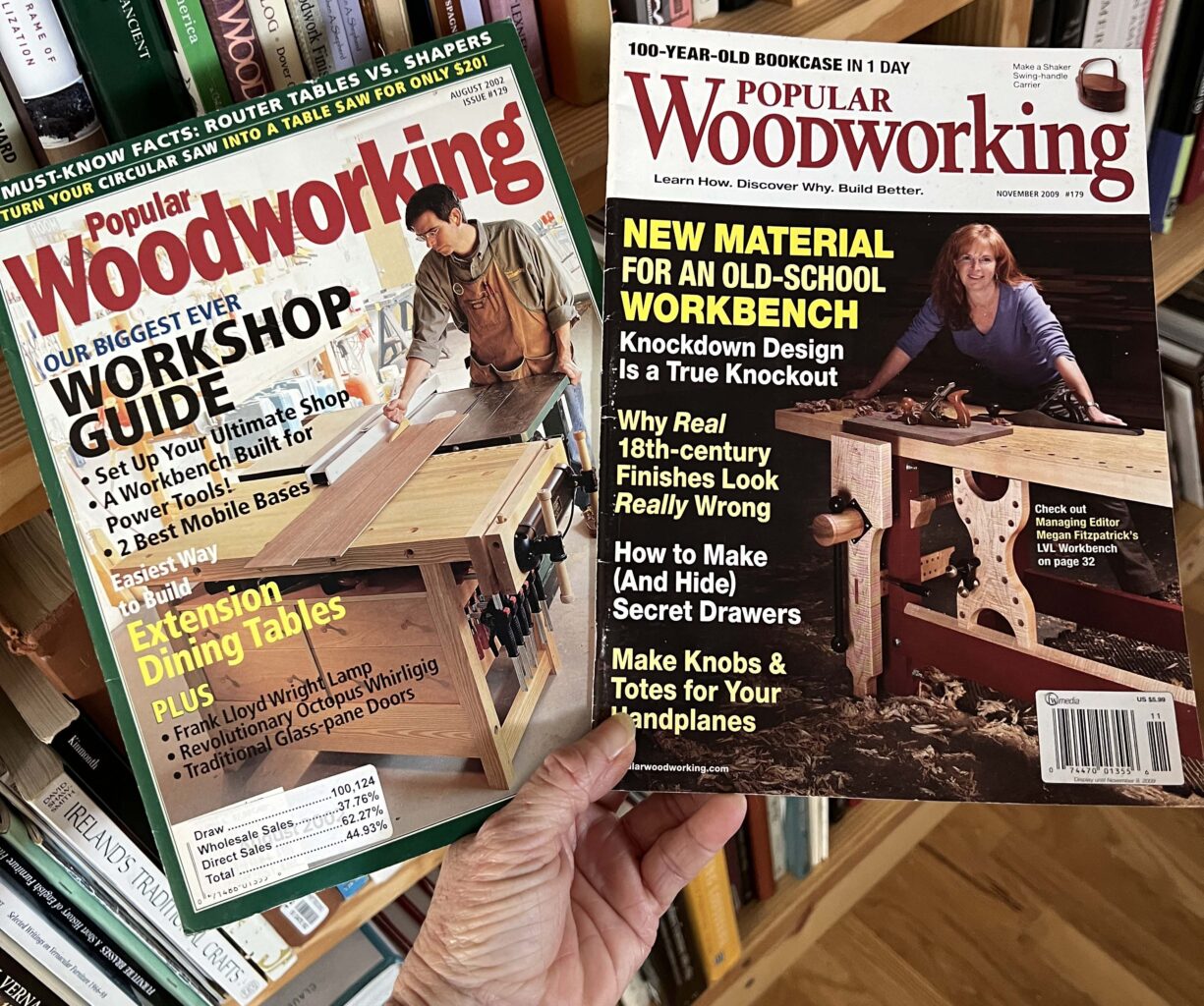
Tucked alongside those PW books are two bench-building magazine covers…the benches featured are in better shape than their builders, I fear. (The bench on the left is currently holding a pile of linden in the horse garage – parts for American Peasant pieces; the bench on the right is currently holding a pile of linden in my basement – parts for an upcoming tool chest class.)
Next up is a copy of “Roman Workbenches” that Lost Art Press published in 2017; it was a short run of letterpress books printed on an old Vandercook proofing press (the book was later incorporated into “Ingenious Mechanics”), and the May 1981 issue of The Magazine Antiques – a look at the cover (below) will tell you why.
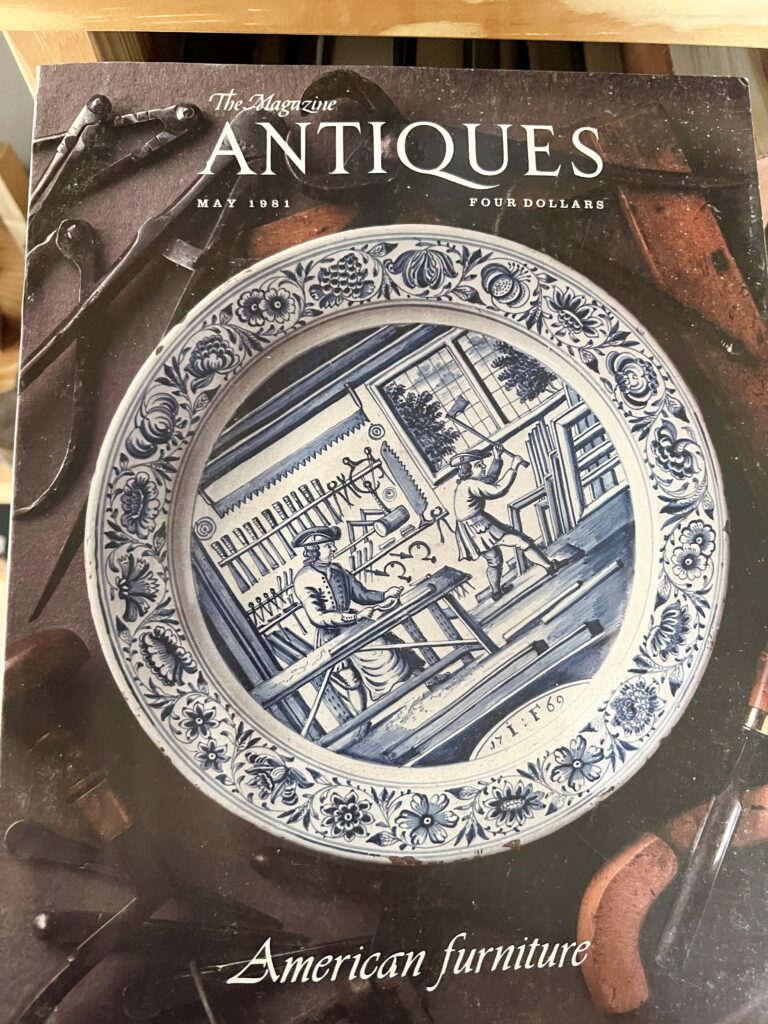
We have several copies of Scott Landis’ “The Workbench Book” – early editions from Taunton (it was first published in 1987) as well as our 2020 hardcover edition. Those are followed by Lon Schleining’s “The Workbench” (Taunton, 2004) and Sam Allen’s “Making Workbenches” (Sterling, 1995). These were all purchased for research – before one writes on a subject, it’s good practice to read as much as one can about what’s already been written on it.
And that concludes the workbench section (though I suspect there are others lurking elsewhere on the shelves), and takes us to two copies of Jim Tolpin’s “The Toolbox Book” (Taunton, 1995) – a must-have introduction to the world of the many ways to contain one’s tools (it’s also, to the best of my knowledge, where the Dutch tool chest first shows up in contemporary literature…but not the last – stay tuned). (“The Toolbox Book” is also of course research for Chris’ “The Anarchist’s Tool Chest.”)
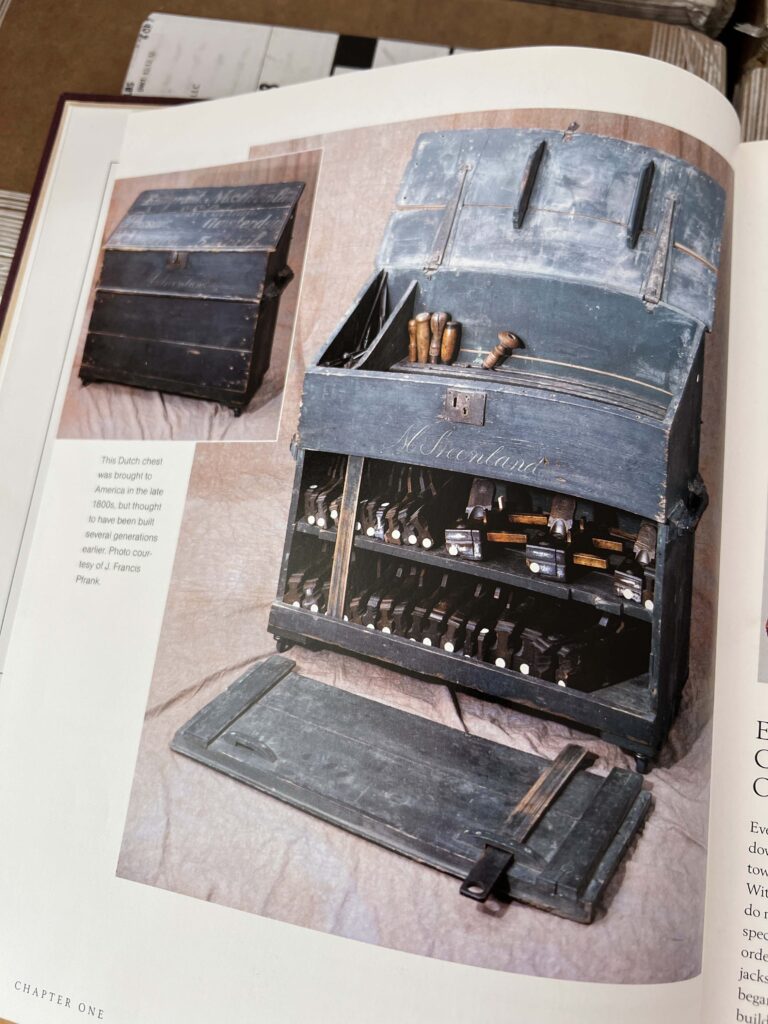
Finally, we have in this small sections two copies of Scott Landis’ “The Workshop Book” (Taunton, 1991) – another must-have, the most complete book about every woodworker’s favorite place: the workshop. It includes inspiring workshops, from garage to basement shops, from mobile to purpose-built shops. In fact, we think it’s important enough that we reprinted it in 2021.
– Fitz
This is the 11th post in the Covington Mechanical Library tour. To see the earlier ones, click on “Categories” on the right rail, and drop down to “Mechanical Library.” Or click here.