
I buy and process at least 900 board feet of red oak each year for chairmaking and chair classes. When chosen and cut with care, red oak can look much better than the ugly 1980s kitchen cabinets it is associated with.
But before you embrace this inexpensive and plentiful wood, here’s a quick lesson on what I look for at the lumberyard.
Most red oak in our area is from two different species: Northern red oak (Quercus rubra) and Southern red oak (Quercus falcata). These trees look nothing alike in the wild. Their leaves, bark and acorns are radically dissimilar. And the wood they produce looks different and works different.
(We also get some Quercus velutina around here, which is also a red oak. But this particular red oak isn’t put with the other red oaks in our lumberyards. It gets its own bin that’s labeled black oak. To me it looks a lot like Northern red oak [Quercus rubra] at times. Boy, is wood confusing.)
There are a lot of red oak species out there that are sold as red oak. This blog entry can only deal with the two common ones.

In general, most furniture makers prefer the Northern red oak. It grows slowly and has a finer grain. I find that it’s a little browner than other “red” oaks, so you don’t get as much of the pink cast that turns some people off.
You can usually identify the Northern red oak by looking at the end grain. The growth rings will be very tight – usually less than 1/16” apart (though there are exceptions I’ll discuss later).
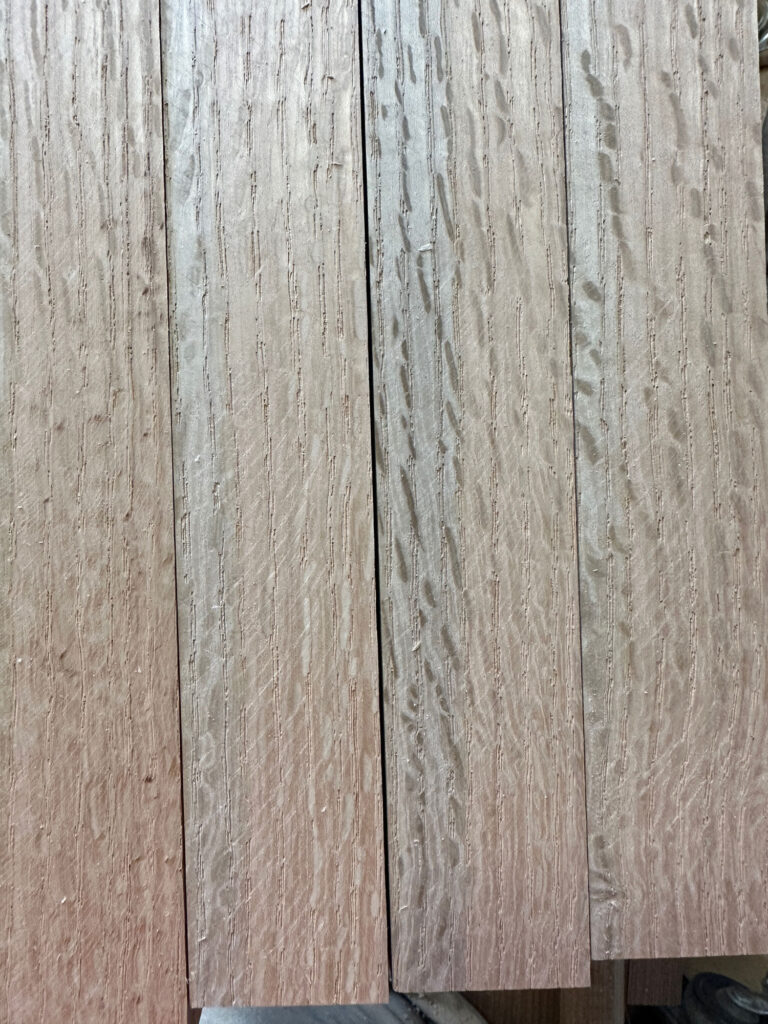
Southern red oak typically grows quickly. I’ve had pieces where the growth rings are 3/8” apart. The wood has a pinkish cast compared to the Northern stuff. Sometimes you will find gray stripes in the wood. Most people consider it the uglier of the two red oaks.
However, I prefer the Southern stuff for one simple reason: it’s usually stronger.

The tight growth rings of the Northern red oak mean that there are a lot of pores running through each board. And these pores are filled with air. Chair parts made from Northern red oak are lightweight and can be quite fragile. I’ve had Northern red oak sticks and stretchers snap – even when the grain was dead straight. It’s simply a matter of too much air and not enough woody fibers.
The Southern red oak has fewer pores. The fibrous wood between the annular rings is heavy and springy. So thin sticks and stretchers are more likely to bend than snap.
As I’ve said many times before, however, trees are weird. Sometimes you get a Northern red oak that grew quickly and is strong. And other times you find a Southern red oak that grew slowly and produces some weak wood.
And that’s why I remain open (but cautious) about both of the common commercial species of red oak. Choose your oak based on its color – you don’t want gray, pink and brown all clashing in one piece. And choose your oak based on what you want it to do: Buy fast-grown oak for strength; slow-grown oak for character.
— Christopher Schwarz

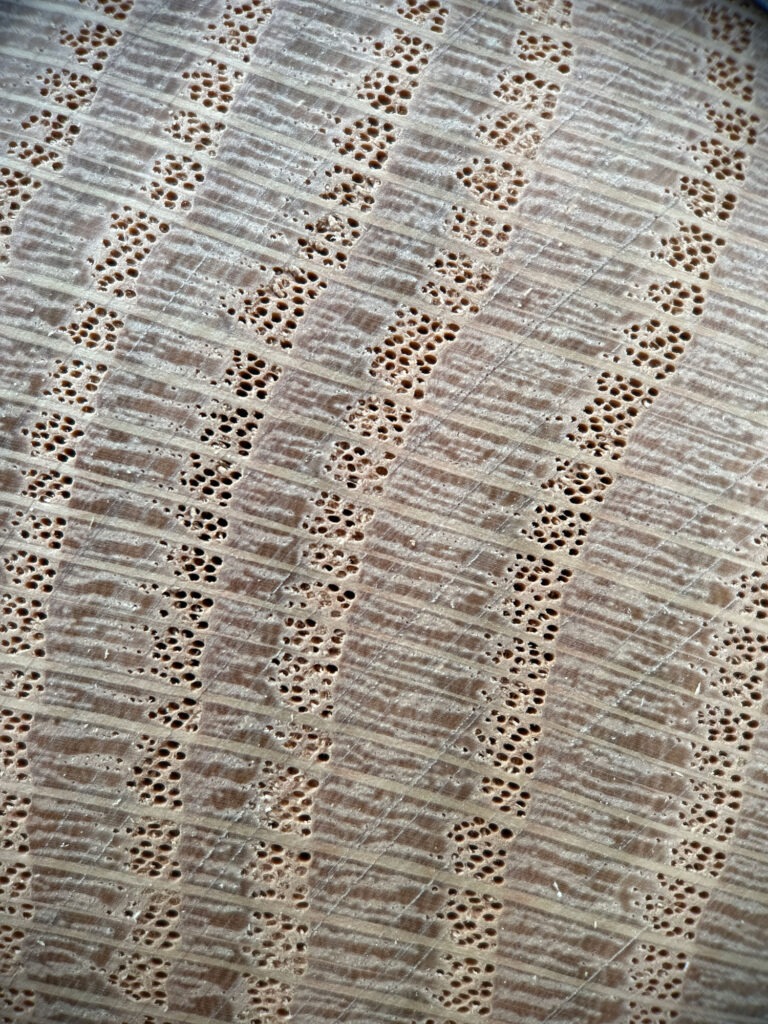