As requested: A detail of the face vise on the 1764 bench from “Hallens, Werkstätte der Künste.”
Category: Workbenches
Workbenches from The Empire of Germany/Holy Roman Empire and etc.
One of the workbenches in Andre-Jacob Roubo’s French masterwork on the craft is called out as a “German” workbench in Plate 279 of “l’Art du menuisier.” It features a sliding deadman/leg vise, lots of storage and a complex tail vise.
While I am still searching, I’ve yet to find an historical bench that matches the image of the German bench in Plate 279 (in contrast, I’ve seen hundreds of benches that match Roubo’s Plate 11).
So what did 18th-century benches look like from the area we now call Germany? The answer, of course, varies. Here we’re going to look at a 1764 bench from “Hallens, Werkstätte der Künste” (I think I have that right; I’m not the best at reading German blackletter type).
This entire plate could occupy a book of discussion because there is so much to see and explore. But let’s stick to the bench for the most part.
It is drawn as being made from fairly thin components with joinery providing the rigidity. Tusk tenons do most of the work in keeping the base from racking. And lest you think tusk tenons are weak, please ready this fun article from Will Myers where tests them to destruction.
The first thing I noticed about the bench (besides that the tail vise was missing its dog), was the tool well. This might be the earliest depiction of a tool well I have in my archive – I’ll have to check.
Also interesting: the face vise. It’s a shoulder vise that looks like it hasn’t quite cast off its crochet origins. Check out the nice bead to the left of the hook, which is really the only ornamentation on the bench.
Finally, we have the system of dogs that works in conjunction with the tail vise. I usually curse modern manufacturers for placing the dogs and drawer so they interfere with one another, but it appears this is not a modern problem. Two of the dogs are in the way of the drawer. Sigh.
And finally finally, look below at Fig. 20. A bench like this (where the legs are not coplanar to the front edge of the benchtop) requires a board jack. And this is a nice one.
I hope you enjoy the plate as a whole – there’s lots to see here.
This is the most conventional of the German benches we’re going to look at. Next up, some vise mysteries.
— Christopher Schwarz
The Rules of the Workbench
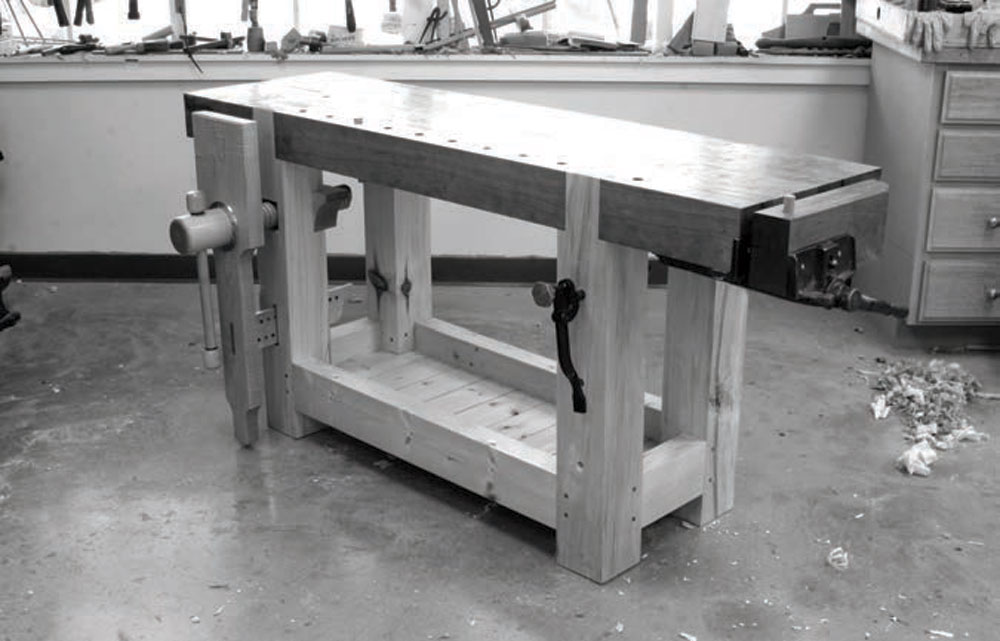
This is an excerpt from “The Anarchist’s Tool Chest” by Christopher Schwarz.
Workbench
I have written two books on workbenches that agonize over the details of joinery, wood selection, vises and so on. But if you don’t want to buy those books, here is the down-and-dirty data you need to pick a bench design.
Note: Before you write me an angry letter about this list – you don’t have to have a good bench to be a good woodworker. You can work on the kitchen table and make world-class work. But a good bench will make many operations easier. It’s simply a tool: the biggest clamp in the shop.
Rule No. 1: Always Add Mass
For workbenches, here’s my maxim: If it looks stout, then make it doubly so. Everything about a workbench takes punishment that is akin to a kitchen chair in a house full of 8-year-old boys.
Early Roman workbenches were built like a Windsor chair. Stout legs were tenoned into a massive top and wedged in place. Traditional French workbenches had massive tops (up to 6″ thick), with legs that were big enough to be called tree trunks. Later workbenches relied more on engineering than mass. The classic Continental-style workbench uses a trestle design and dovetails in the aprons and vises to create a bench for the ages. The 19th-century English workbench uses an early torsion-box design to create a stable place to work. And good-quality modern workbenches use threaded rods and bolts to tighten up a design that lacks mass.
Many inexpensive commercial benches are ridiculously rickety. They sway and rack under hand pressure. You can push them across your shop by performing simple operations: routing, sawing, planing. If the bench looks delicate or its components are sized like a modern dining table, I would take a closer look before committing.
A big thick top and stout legs add mass that will help your work. Heavy cabinet saws with lots of cast iron tend to run smoother than plastic ones. The same goes with benches. Once your bench hits about 300 pounds, it won’t move unless you want it to move.
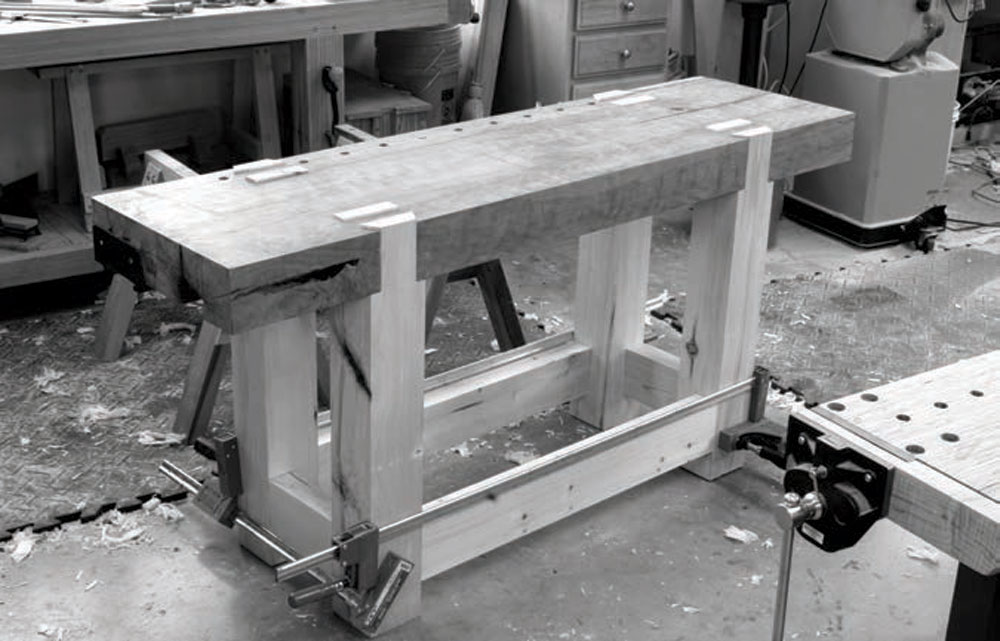
Rule No. 2: Use Stout Joints
Overbuild your workbench by using the best joints. These are times to whip out the through-tenon and dovetail. If you followed rule No. 1, then rule No. 2 should be no problem. Your joints will be sized to fit the massive scale of your components. If you cannot rely on mass, then you should beef things up with superior joinery. While dovetails and through-tenons are overkill for a towel rack, they are de rigueur for a bench.
That’s because you are applying wracking force to the workbench with typical operations and your vises will do their best to tear apart your bench. All wooden vises need to be overbuilt or they will self-destruct when you cinch them down hard. I’ve even seen a vise rip a benchtop from its base.
Make your tenons thick and your mortises deep. If you know how to drawbore a mortise-and-tenon joint, this is one good application. Have you ever been in a timber-framed barn? Did you look at the joints? They’re massive and pegged. Imitate that.
I think benches are a good place to practice your skills at cutting these classic joints, but some woodworkers still resist. If that’s you, you should investigate hardware to strengthen your bench. Threaded rods, bed bolts, special bench bolts or even stove bolts can turn a spindly assembly into something rigid that can be snugged up if it loosens. The hardware won’t give you mass, but it will strengthen a rickety assembly.
— MB
Another Workbench Journey Begins
About 8 a.m. Wednesday morning I’ll pack a thermos of coffee and hit the road for North Carolina in the hopes of gaining some small understanding of the craft culture of ancient Rome.
Thanks to Will Myers, there’s a large load of dry oak waiting for me in North Carolina that I’ll use to build two Roman-style workbenches. The benches are separated by about 1,400 years but share the same DNA.
The reason I do this stuff, which is admittedly a bit bonkers, is the same reason I started building nearly vanished French and English style workbenches in 2005. I’m not looking for a better workbench, just another one that might make sense for your work and mine.
For me, the appeal of 18th-century French and English workbenches is that they are simpler. They are far easier and faster to build than your typical Scandinavian or Germanic bench. I don’t have anything against those central and northern European benches. The ones that are made by woodworkers for woodworking are great.
But not everyone wants to build a bench that is that complex, with a tail vise and a shoulder vise, a fifth leg, a dovetailed skirt and square dogs. Some of us would rather do something else with our time.
In the same vein, the Roman workbench has always interested me. It is even simpler than a French or English bench. No stretchers. Simpler joinery. Less mass (perhaps). And during my last 11 years of ongoing bench research, I’ve concluded that the Roman workbench has never fully gone extinct. Instead it has gone out to pasture, so to speak.
By building and using these two Roman benches in my shop, I hope to learn their strengths and weaknesses – all bench forms have upsides and downsides. None is perfect. My hope is that I can show how these even simpler benches can be used to hold boards so you can work on their faces, edges and ends. Because that goal has never changed for woodworkers, whether they wear togas or flannel.
— Christopher Schwarz
Advice Needed on the Forum
I went out of town for one weekend and it seems like the forum exploded while I was gone. A lot of advice is what people are after. Remember, if you have a question about our products, procedures in our books or anything related to Lost Art Press, the fastest way to get an answer is our forum. Check it out here.
Wear to the Sliding Tills in the ATC
We all know wear is inevitable, especially to something you use as often as your tool chest. Joshua is looking to make his in a way that will prevent some of this from the start. A couple preventative measures have been given, perhaps you want to give them a try? Perhaps you have other methods that have worked for you?
WoodOwl Bits – Sharpening
Jason hit a steel plate with his WoodOwl nail chipper and is curious to know if he can use the small knife-edge files that Lee Valley sells to sharpen it. Are they the same angle? Help him out here.
Soft Wax
Has anyone used a wax recipe on their tools as a rust preventative or to lubricate? Did you have success? And did you use a specific wax recipe?
‘I remember a post on here a while ago about a leg vise with no lower guide’
Peter is looking to add a leg vise to his bench and is thinking about taking this approach. It turns out it is the bench from Plate 11 in Roubo. Now it seems he is not the only one looking to use this method. Has anyone given this a shot and able to give some feedback?
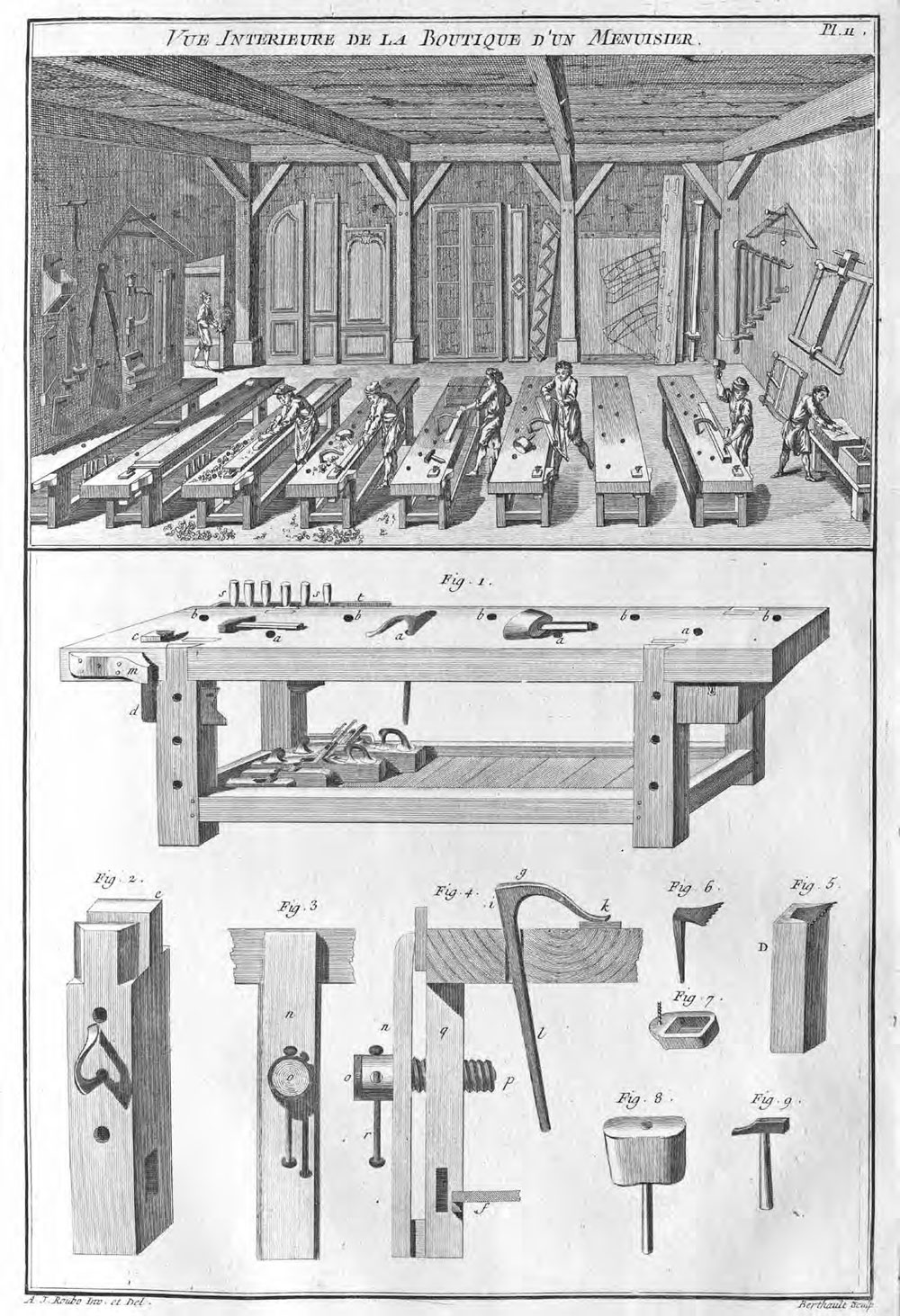
Moulding Plane Choices
Anyone have a favorite older wooden moulding plane? Neal wants to get one and is looking for suggestions. What shape do you like? Why? Ogee? Reverse ogee?
— MB