If you are a fan of our digital products (pdfs, videos, plans, etc) then you know that they are sent to you as a link via email after checkout. But did you know that you can also access any of your digital purchases by logging into your Lost Art Press account? This prevents you from having to dig through emails or lists of links when you want to find a project that you finally have time for.
I will walk you through that in a minute, but I do have one more piece of good news for customers who have been tracking their purchases with their accounts for years. I frequently receive emails requesting that email addresses be changed or accounts be merged. I have been unable to do this in the past. Not any more! So, if you are one of those customers that somehow ended up with multiple accounts, feel free to reach out to the help desk and I, the Meghan that is not Fitzpatrick, will get you sorted out. You will no longer have to wonder if you ordered “By Hand & Eye” in 2018.
OK: back to how you access your digital content in your account. Start by clicking on the little person in the top right corner of our website and log in…or create an account if you haven’t been using one for your purchases.
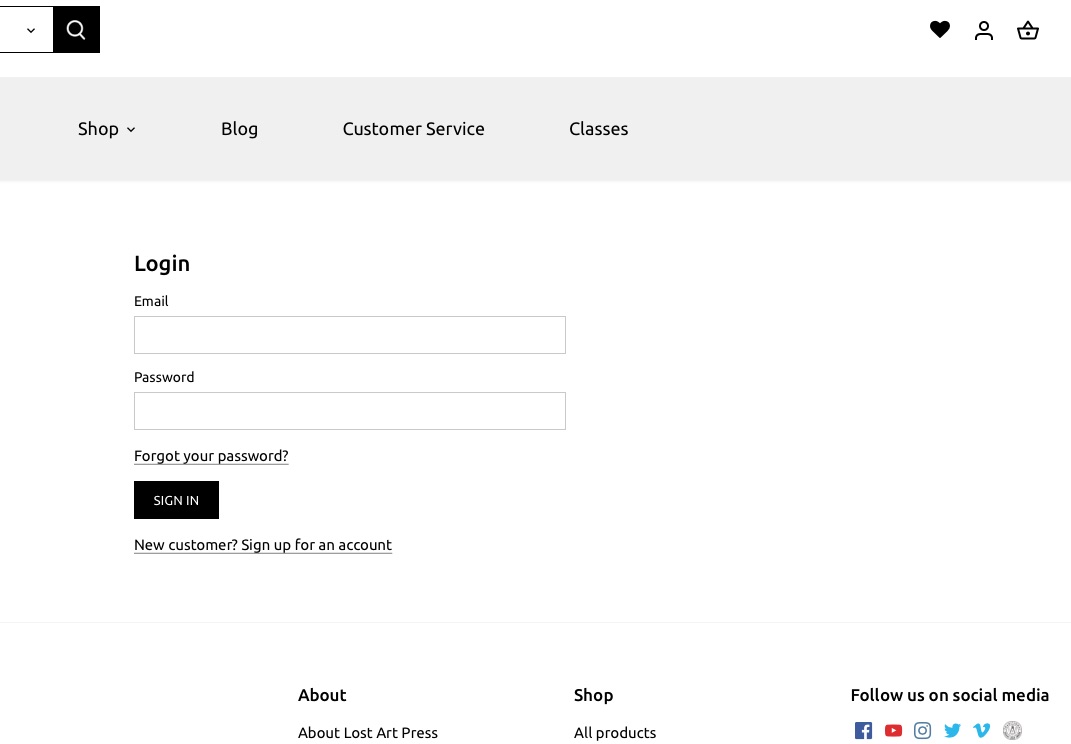
Once you are logged in you will click on the “My Downloadable Files” tab.

You will then see all of the digital content that you have purchased. Here is what the pdfs will look like:

And what your videos will look like::

From here you can stream your video or download it. To download it you will click on the “vimeo” icon in the bottom right corner. This will open the video in a new window with the download option showing.
As always, you can email help@lostartpress.com if you have questions.