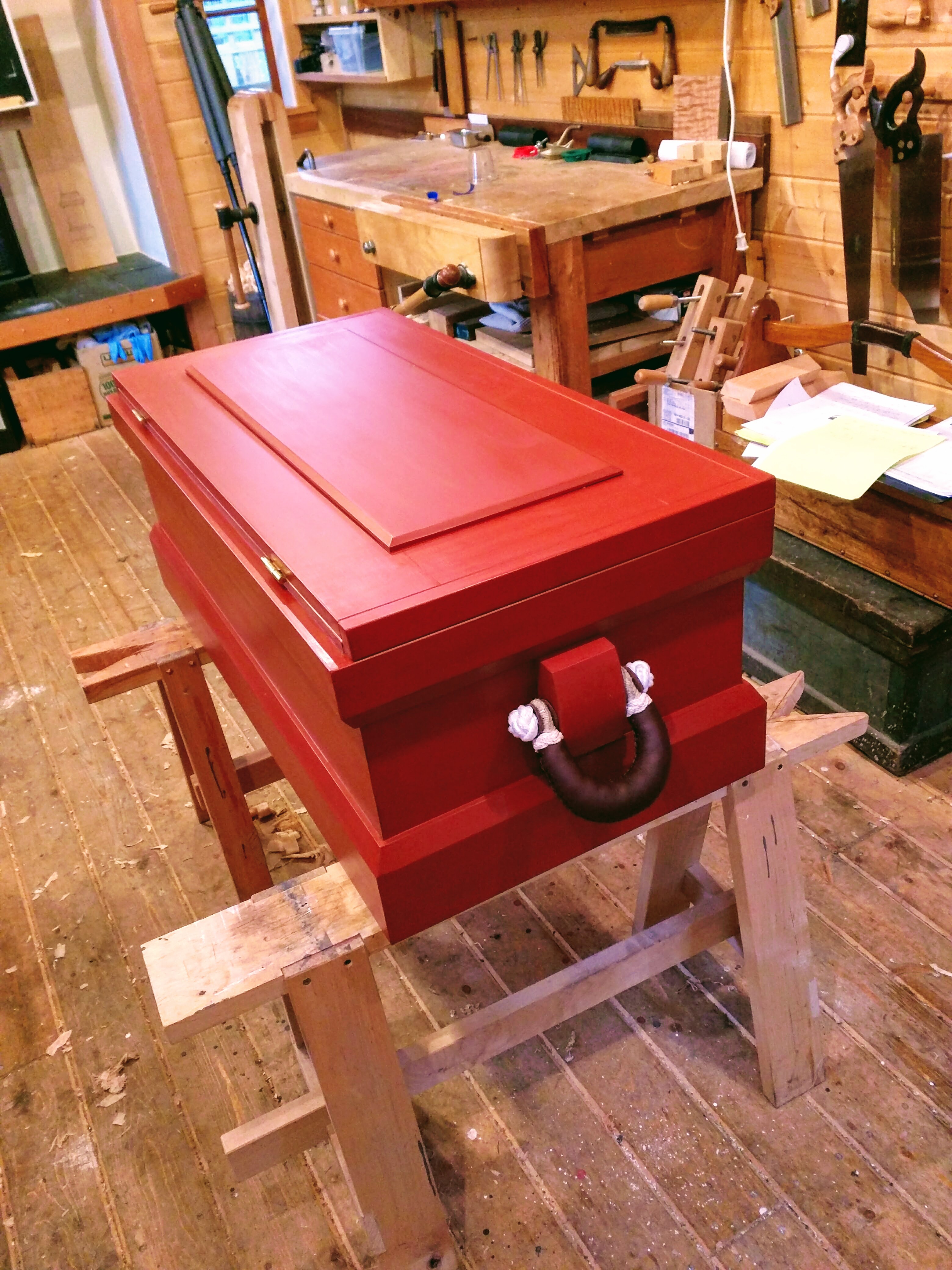
This chest is a close reproduction of a traditional joiner’s tool chest. Chris designed the chest and constructed the box portion during a course he taught with us several years ago. I (Jim Tolpin) finished it by building the lid and sliding till and applying the traditional milk paint. The hand grips (traditional sailor’s beckets of rope and leather) were made and donated by Keith Mitchell – a boatbuilder currently in Vermont. (You can follow Keith on his instagram feed @shipwrightskills). The chest is signed by Chris and me on the underside of the lid.
The box and lid are made from clear poplar boards. The box, the wrap-around skirt boards and the till’s corner joints are dovetailed and glued with hide glue. The bottom boards are set into rabbets and nailed in place with traditional cut nails. The lid’s frame is mortise and tenon, drawbore pinned with hewn, air-dried white oak. Chris and I did the work with hand tools beyond the initial surfacing of the stock to dimension. Dimensions are 20″ wide by 16″ high by 40″ long.
About the finish: Traditionally, these tool chests were always painted to protect the wood from moisture because they might occasionally be exposed to outside conditions. I went with three coats of black followed by two coats of red to create an “oxblood” hue. As you probably know, milk paint is one of the most durable paints available. I applied several coats of linseed/tung oil to build a sheen and to provide additional protection.
All the proceeds of this sale will go to the Port Townsend School of Woodworking youth-in-woodworking scholarship fund. A portion of the cost of this chest is tax deductible as the school is a 501 (C) (3) non-profit educational institution. To purchase, go to the auction site here on ebay.
— Jim Tolpin