
I recently had a conversation with a professional woodworker and carver who was shocked that other pros use dovetail jigs for casework when making high-end commissions. I pointed out the irony of his statement: He never makes mouldings by hand before adding carving to them.
Everybody sees the process differently. To each his own.
A lot of people get into this hobby through machinery and then add some sort of handwork. Dovetails appear to be most woodworkers’ transition point. Once you know how to make this joint by hand, your drawers do not have to be made to fit the jig. Even if the jig has variable spacing, dovetails done by hand are nearly unanimously seen to be more attractive than those done by machine. Additionally, the skill is recognized by even the most novice among us. If nothing else, it’s a way to immediately transmit our prowess to others who are in the know. It’s a secret handshake of sorts.
Like making dovetails with a saw and chisel, making mouldings with hollows and rounds has real advantages. You will make profiles that highlight a piece exactly the way you want. You will manipulate the light and shadows to fit the piece and your eye, not in a predetermined fashion made by a manufacturer. By making mouldings by hand you will dictate your results.
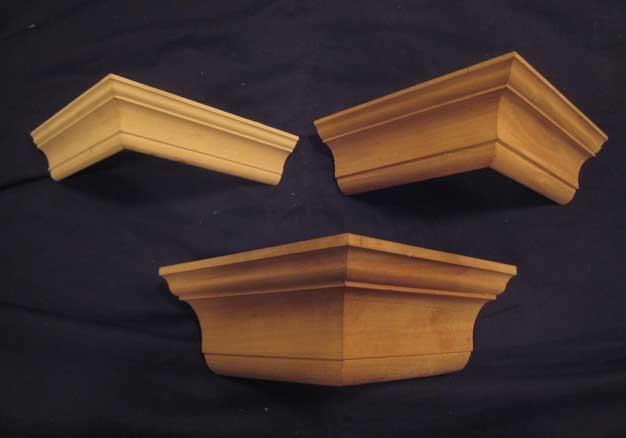
Unlike making dovetails by hand, the tooling, method, purpose and starting point for making mouldings with hollows and rounds is not always apparent. After all, any dovetail on furniture can be cut with a single saw. Every moulding cannot be made with two, four or even 10 moulding planes.
The good news is that most of us have no need to be able to make every moulding. Most of our work does not encompass the full range of furniture and decoration. We may all include ogees in our pieces, but not all of us make ogees that range from 1/4” in width to 3”. Most of us do not need a half set of hollows and rounds (nine pairs, 18 planes that range from 1/8” radius up to 1-½”) along with snipes bills, side rounds and plows.
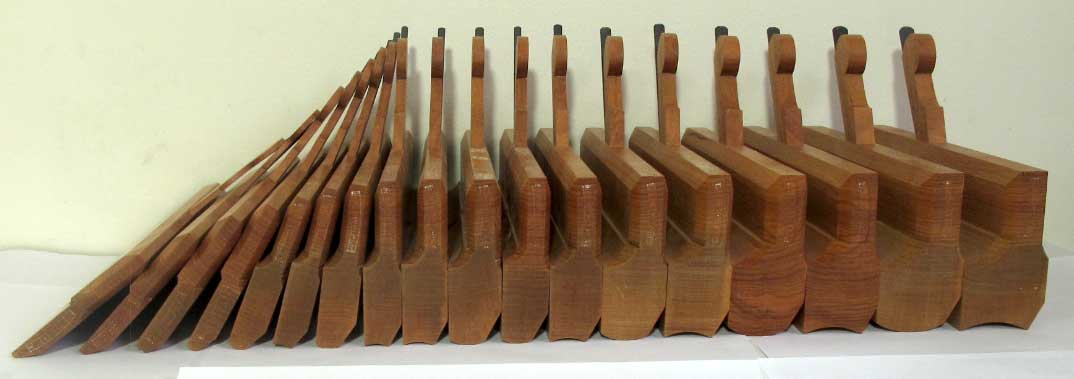
The inevitable question of “where do I begin?” is one I’ve addressed a lot. The first answer is that you must have a way to accurately and efficiently make many varying rabbets. If you are not comfortable with making the following rabbets then you will need a method to do so.
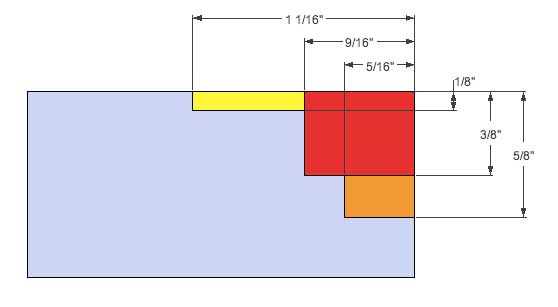
I opt for a rabbet plane (often supplemented with a table saw) to make rabbets. A simple rabbet plane has no fence and no depth stop, which is an absolute advantage. No fence and no depth stop means no adjustments, which means that you can hop from one rabbet to the next in the course of a recoil from a forward stroke.

Like a rabbet plane, hollows and rounds also lack fences and depth stops, which, again, is an advantage to those making small runs of profiles. Hollows and rounds make a specific circumference – not a specific profile. “Mouldings in Practice,” my new book to be published by Lost Art Press, will walk you through the process from holding the planes and setting the irons to making large profiles composed of several different shapes.
With one hollow and one round and a method for making rabbets you are able to make a few dozen profiles. Each profile, however, will be derived from the same circumference. You will learn which tools you need as you learn the process of using them. I think you need at least two pairs to learn how to truly use them.
If you start with two pairs of hollows and rounds, you are able do far more than twice as much. With two pairs you will, of course, be able to make the same moulding profiles in two different dimensions. You will also be able to mix and match the concave with the convex to mimic profiles that are more representative of those that you will see upon the pieces throughout the ages. By adding a second pair of hollows and rounds you are also able to make ovular or elliptical shapes by using two different sized pairs.
With two pairs of hollows and rounds you are able to make multiple moulding profiles that complement each other and are not simply derivatives of the same circle. By adding that second pair of planes to your repertoire you are able to recognize the true versatility that these planes both allow and encourage.
If you do not know where to begin but you know you want to make one specific profile, find the various radii included in the profile with a circle template and you’ll have your answer.
If you still do not know where to begin then I often recommend starting with either pairs of 6s and 10s (radii of 6/16 and 10/16, respectively) or 4s and 8s (radii of 4/16 and 8/16, according to the numbering system to which I subscribe). If the largest piece on your “to do” list is a lowboy or small chest of drawers, then go with the 4s and 8s. If you want to make a high chest of drawers or something larger, go with the 6s and 10s.
These two pairs of planes may be all you ever need to execute the profiles of your choice. If you later decide to add more pairs you will know exactly where to go with the experience you have gained at the bench. Whether you end up with four pairs or 14, these sizes will certainly be included in your ideal set.
Moving the process from your computer to the bench is the most important thing to do in acquiring this skill. As you progress, you will learn to sharpen more accurately, lay profiles out better, and to design as you see the profile take shape knowing that you can change it at any point.
By using the methods I describe on my blog and in my book you will never get to the end of a profile and wonder what went wrong. The answer is always apparent.
But what do you do in a few months when you recognize that your first attempted profiles aren’t perfect? Tell anybody who notices that you once bought cheap router bits and didn’t have the control like you do now. And be content knowing that you’ve distracted them with the great work you have done on your dovetails. That’s the secret handshake that most people know. This one – hand-cut moulding – is still a secret.
— Matt Bickford, author of the forthcoming “Mouldings in Practice”
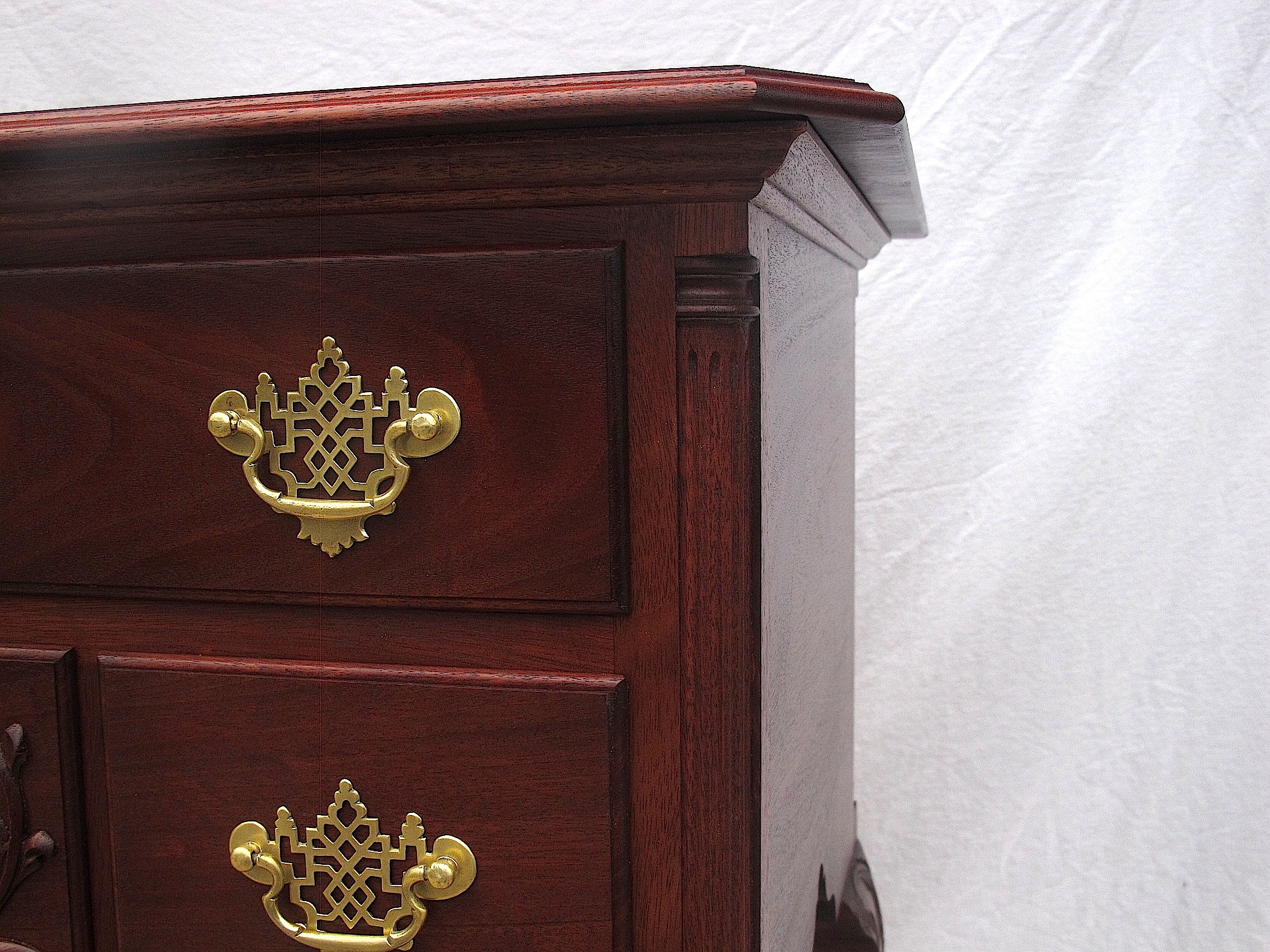
Like this:
Like Loading...