The following is excerpted from Matthew Bickford’s “Mouldings in Practice.” In this book, Bickford shows you how to turn a set of complicated mouldings into a series of predictable rabbets and chamfers that guide your hollow and round planes to make any moulding that has been made in the past or that you can envision for your future projects.
The first half of the book is focused on how to make the tools function, including the tools that help the hollow and round planes – such as the plow and the rabbet. Bickford also covers snipes bills and side rounds so you know their role in making mouldings. Once you understand how rabbets and chamfers guide the rounds and chamfers, he shows you how to execute the mouldings for eight very sweet Connecticut River Valley period projects using photos and step-by-step illustrations and instruction.
The term “moulding plane” is an inclusive one. Dedicated moulding planes (also called “complex moulders”) have soles that consist of multiple curves, flats, quirks, steeples and anything else centuries of art have imagined. Dedicated planes create one profile and do it well.
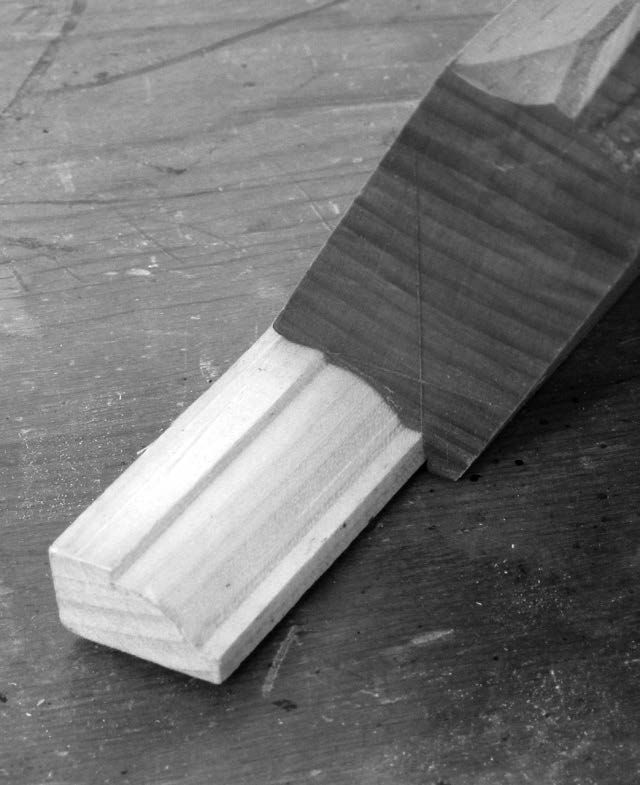
is similar to that of a window sash.
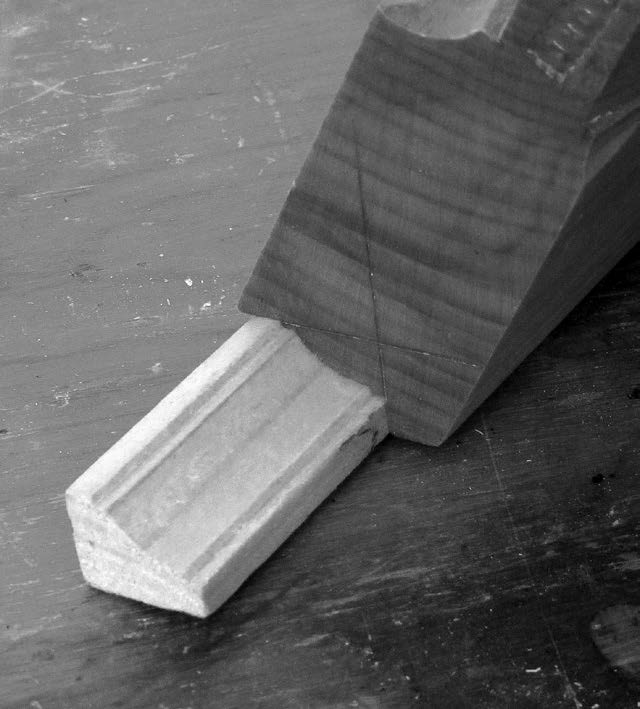
these planes are held relative to the
wood. These planes are sprung; the
angle at which they are held is the
“spring angle.”
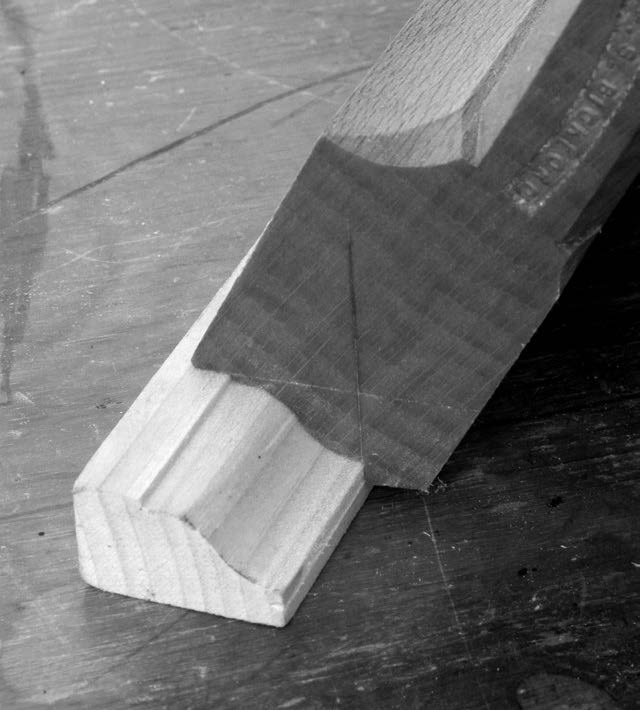
ogee plane creates this single profile
at a single location relative to the
edges of the board, at a single angle.
These planes, when small, are easy to push and are often much quicker to produce a profile than any router bit, if only because the router surface needs to be sanded. A 1/8″ side-bead plane creates a bead along an edge that is ready for finish after 10 quick strokes. A thumbnail plane creates a convex ovular shape and adjoining vertical fillet, and can consistently and quickly cut profiles along 20 edges of five drawers in a dressing table. A 4″-wide crown moulder, with help from a few friends (and perhaps a horse), creates a complex cornice that is completely uniform from piece to piece across splices and from wall to wall and through mitered corners.
The profiles these planes create are precise, uniform and consistent. Therefore, any time a uniform profile is needed, but the mouldings cannot be cut from a single long piece, a dedicated plane is desirable. A drawer, after all, has four sides – and the lips of individual drawers may sit a mere 1/2″ apart – so efficient consistency is required.
There are dedicated planes that execute just about any moulding, including all those already mentioned. Many of these dedicated planes are also desirable for the craftsman who produces the same edge many times, such as a harpsichord maker who adds a small quirked ogee to the bridge of multiple harpsichords made months apart.
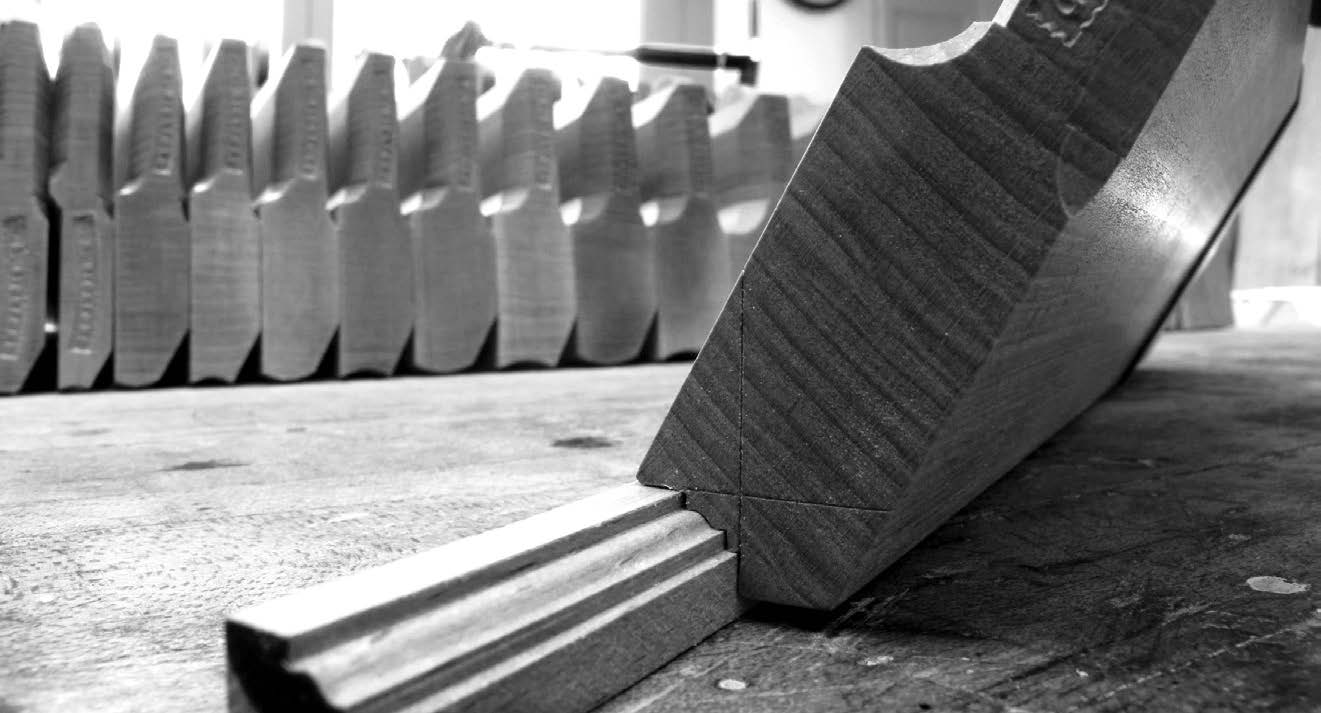
These dedicated, single-profile planes, however, serve little purpose to the craftsman who produces numerous small lengths of moulding in an ever-changing portfolio. These single-profile planes are dedicated to one profile and, like most router bits, they do only one thing. Though the profile these create can often be manipulated to some degree (by removing a fillet, for example) specialty planes are without value if you need to control the details of a profile, or create something with major or even minor differences.
To fresh eyes, the complex profiles integrated into these planes’ soles are apparent; the integral fences and depth stops the planes often include, however, are not. The fences require the plane to contact the edge of a board as a reference, limiting the plane’s angle, spring and location. The depth stop ensures a consistent depth of profile, but often makes it impossible to use the plane to create part of a larger, more complex moulding.
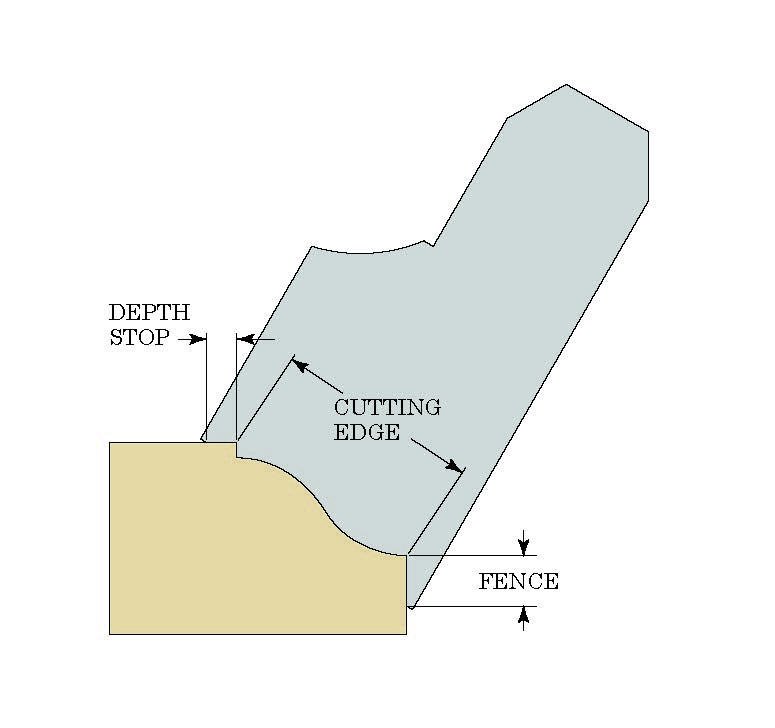
Most dedicated planes also demand proper setup steps to be performed prior to their use.
Without the minimal rabbeting setup in the example in Fig. 2-6, significant edge maintenance will be required because the edge closest to the fence takes dozens of passes more than the edge closest to the depth stop. When the edge nearest the fence deteriorates, the entire blade profile will need to be sharpened in order to keep the iron matching the sole.
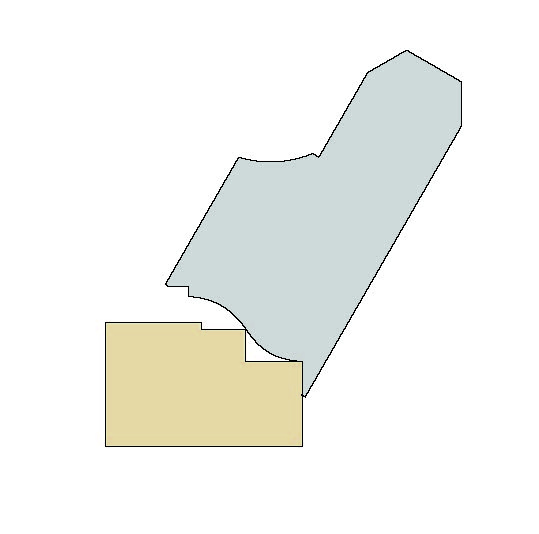
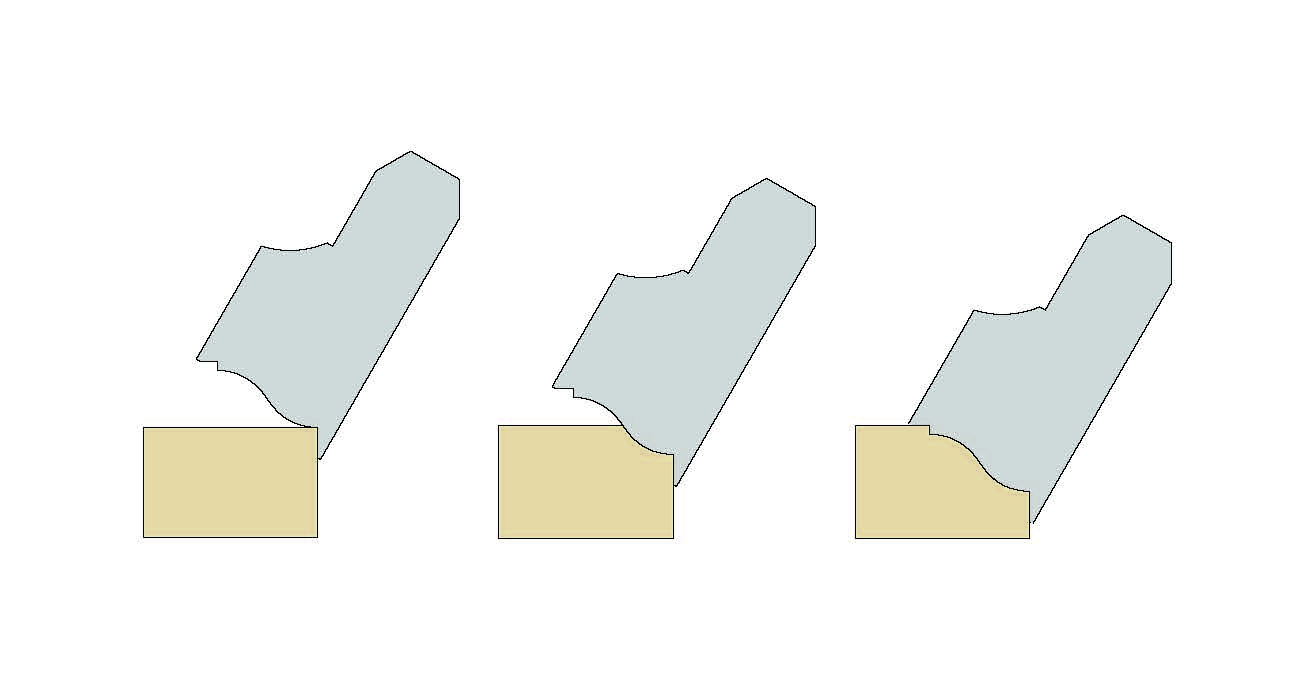
The genius of dedicated moulding planes is in their absolute consistency, made possible largely by their integrated fences and depth stops. However, these same features also limit the versatility of the planes, and make them poorly suited to address many people’s primary motivation for investigating moulding planes: eliminating excess tooling.
The planes we will discuss in the pages to follow do not share these limitations. We are going to focus on rabbets, hollows, rounds, snipes bills and side rounds. Each of these planes serves a different function. All these planes, however, share a similar characteristic: They have neither integral fences nor depth stops. Without these two characteristics the planes are remarkably versatile. And by using simple stock preparation techniques, the user can impose steering and depth control on the planes to direct and focus their versatility to create all manner of profiles precisely and simply with just a handful of planes. These planes have no fences. We will make guides. These planes have no depth stops. We will make gauges.
But how do these tools work? These planes cut specific portions of an arc in a profile. Each size cuts a segment from a circle of a specific radius. While a plane’s cut matches the circumference of a specific circle, the percentage of the circumference is up to the user. There are no fences that need to be registered on the work, no spring lines to obey and no depth stop to adjust.
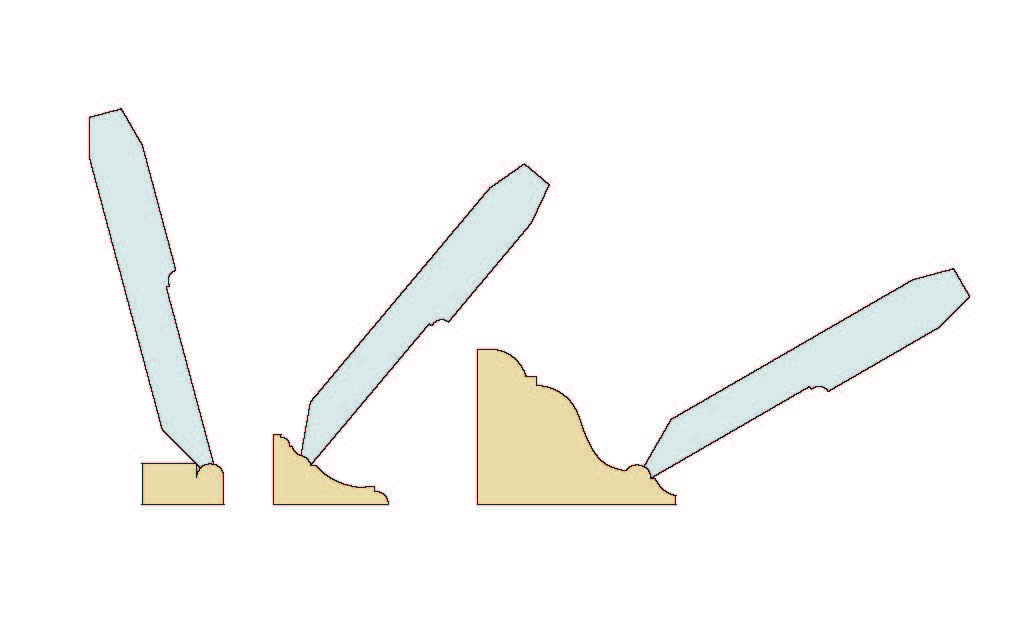
With hollows and rounds, the plane that cuts a side bead on the edge of a board is the same plane that cuts the convex portion of an ogee set 1″ from the edge of a complex waist mould. Unlike a dedicated moulding plane or even a Stanley No. 45 plane, these planes do not need to reference an edge while being held at a specific angle.
Whether the specific arc created by these planes falls along the narrowest edge of a board or onto the widest portion of a linenfold panel, the arc’s location is not predetermined. If the arc you need is a minimal 60° of a circle or more than 180°, that function is not determined by a depth stop. Whether the arc stands alone or in a sequence is a decision made by the user, not the planemaker.
These planes do not have predefined purposes other than cutting an ideal radius. Executing any moulding along a straight edge is achievable with these planes – whether you are making moulding on a board that will be applied beneath the top of a piece or even to the top itself.
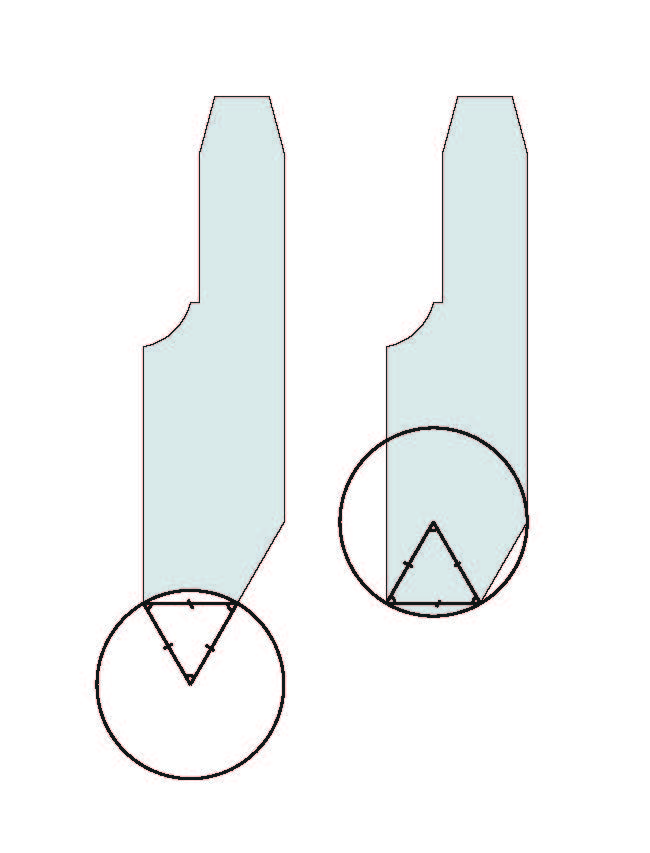
The soles of hollow and round planes represent 60° of a circle. Thanks to basic geometry and the properties of an equilateral triangle, we know that the width of each plane’s sole is equal to the radius of the circle each creates.
These hollow and round planes generally come in pairs, one convex sole (round planes) and one concave (hollow planes). The pairs vary in radius, which means they also vary in width. There are several numbering systems used when describing these planes, some dependent upon the maker, some on the origin of the tool. For this book, the following numbering system will be observed.
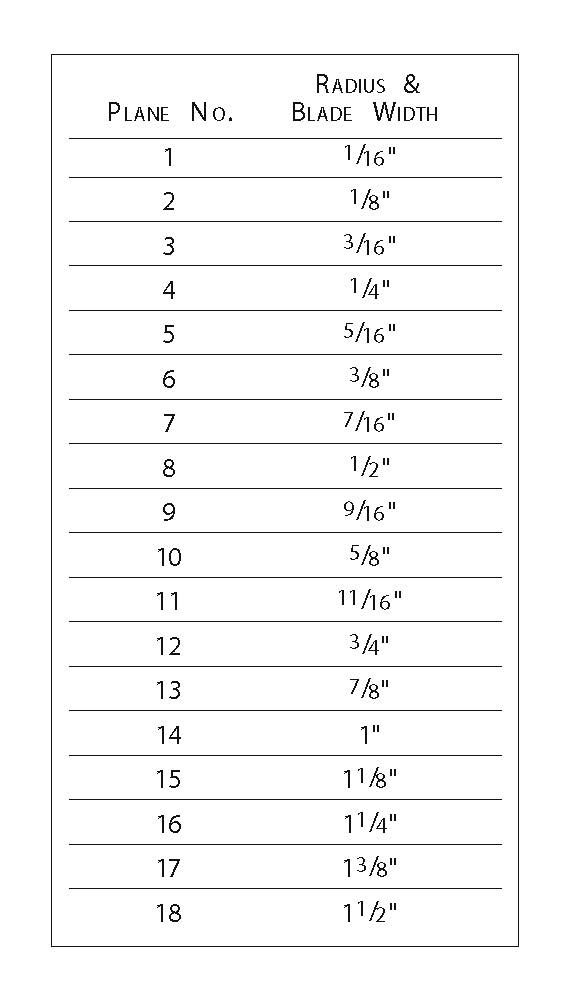
In this system, the plane’s number (usually stamped on its heel) designates its radius in 16ths of an inch up to 3/4″, or 12/16″. The numbering system then breaks, as subsequent planes increase in radius by 1/8″ instead of 1/16″.
There are a few other planes we need to learn about that assist the hollows and rounds – snipes bills, side rounds and rabbet planes.
Hollows are to rounds as snipes bills are to side rounds: The first has a concave sole and cuts a convex shape, while the second has a convex sole and cuts a concave shape.
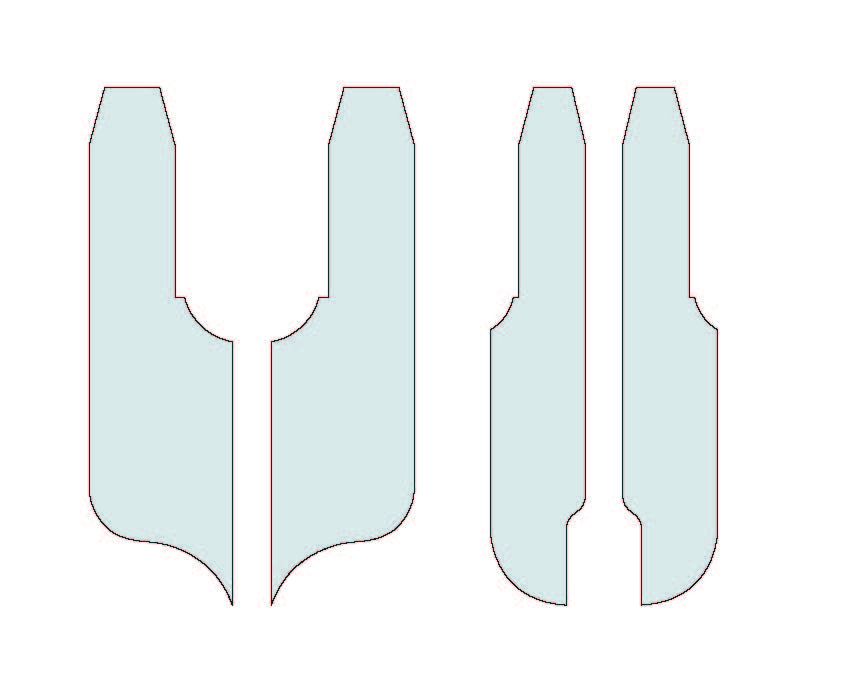
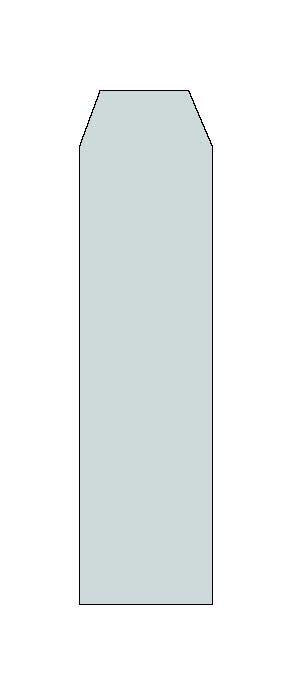
The rabbet. A rabbet plane is
rectangular in form and
cuts square rabbets.
Many people look at the above planes and, for good reason, do not recognize their purpose. But you soon will.