This is an excerpt from “Campaign Furniture” by Christopher Schwarz.
Brass-bound campaign chests that can be split into two parts are likely the most iconic pieces of the style – like the Morris chair of the Arts & Crafts movement. The archetypal British-made chest is mahogany with four rows of drawers, brass corner guards and flush brass pulls. Most chests would fit nicely into a box that is 40″ H x 40″ W x 22″ D.
However, there are lots of variants of campaign chests and details about their construction that you should consider as a maker when you plan to build your own. The following details apply to British-made chests. Campaign chests made in China or India are outside the scope of this book.
As far as dating the chests, a good rule of thumb is that earlier chests had fewer brass corner guards and used pulls that are “skeletonized.” That is, the early pulls look more like the classic swan’s neck type. In addition to the skeletonized pulls, there are also some early pulls that have pointed ends and other shapes. Early chests are also more likely to have moulding than a later chest, though the ornament is usually is more subdued than that on a high-style chest for domestic use.
Because early chests were more likely made as one-off pieces (and not in a manufactory), you are apt to see more variation in their design and construction. So you can encounter (or use) almost any joinery variant of the dovetail family.
Later chests in the mid-19th century became more standardized. More brass was added. The pulls became rectangular and fairly uniform among the manufacturers. From a builder’s perspective, these later chests are well built and are worth studying and reproducing.
Here are some other construction details of the chests, both early and late.
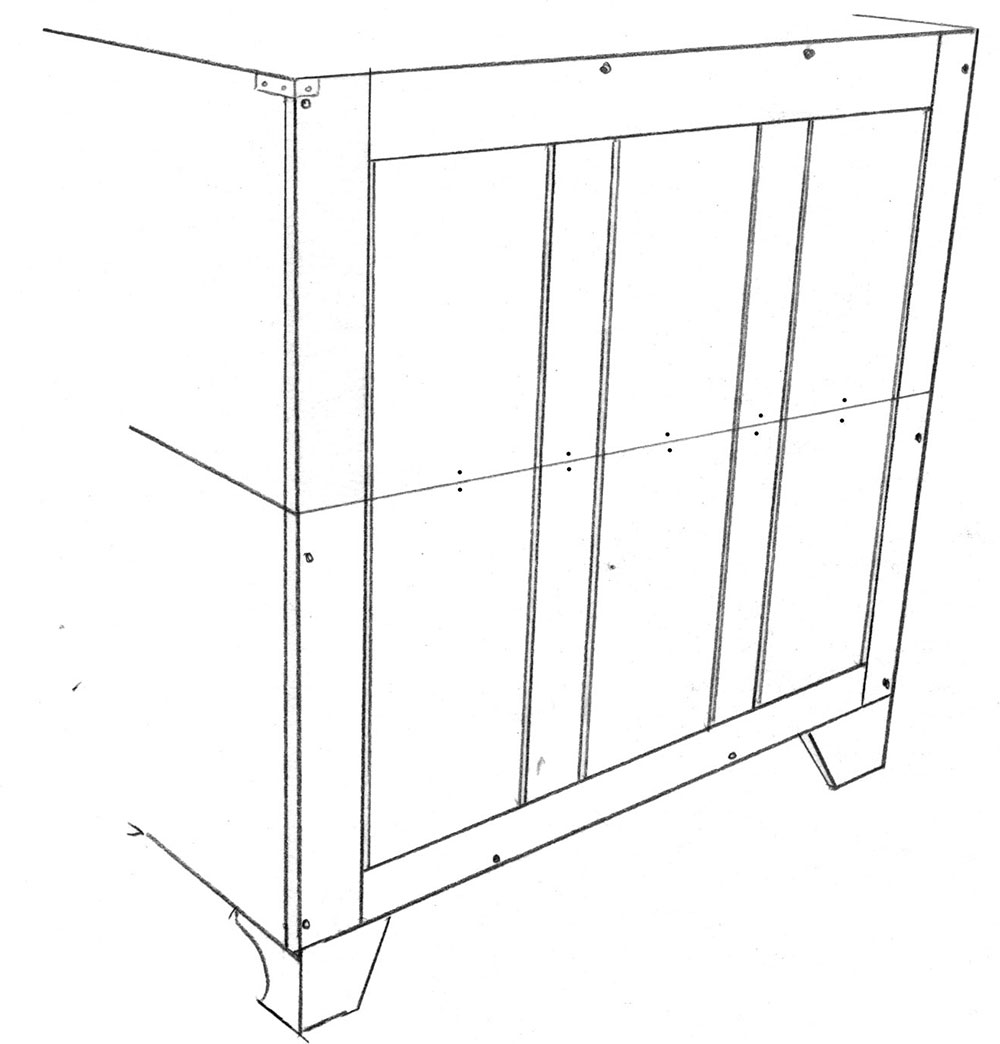
Backs of Campaign Chests
The backs of campaign chests can run the full gamut of techniques. I’ve seen frame-and-panel backs all the way down to backs that were simply nailed into a rabbet in the rear of the carcase.
A frame-and-panel back is by far the lightest in weight (because of the thin panels) and adds the most rigidity to the carcase, which is a frameless cabinet that benefits from the rigidity. You’ll also see backs that were paneled (usually via tongue-and-groove) and simple full panels that are inset into a rabbet or a groove. These options are preferred to a simple nailed- or screwed-on back.
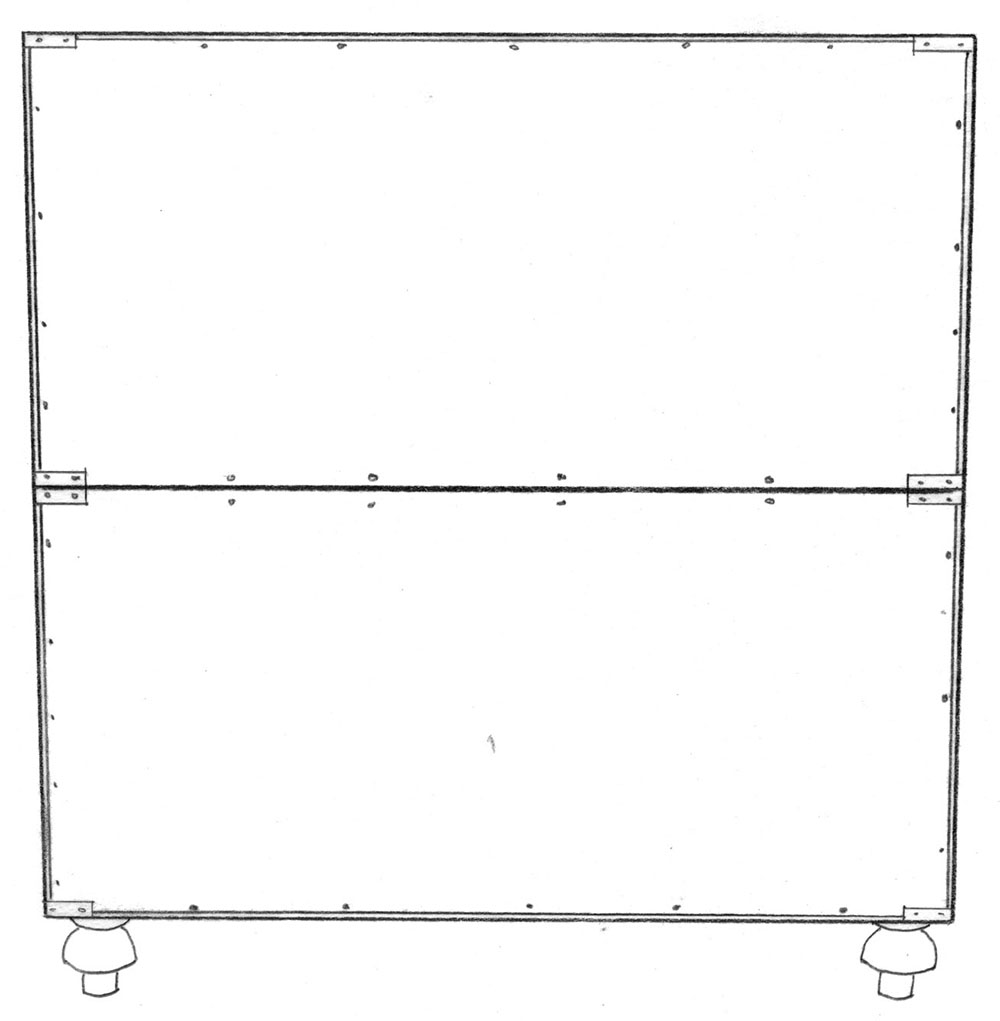
Corner Joinery
When it comes to the joinery, most of these chests were dovetailed at the corners. Except for the very top board of the cases (which were joined with full-blind dovetails), the remaining tops and bottoms were typically joined to the ends with half-blind (also called lap) dovetails.
On all the examples I’ve examined so far, the tail boards have been on the tops and bottoms, and the pin boards are on the ends of the carcases. This violates the typical practice of putting the tails on the end boards, which makes the joints stronger for lifting.
My guess is that this is for simplicity’s sake. With the tails on the tops and bottoms, these joints are laid out and executed exactly like cutting the joints for a drawer. If you put the tails on the end boards, removing the waste in the blind tails would be a little more difficult. But most of all, it would be a less-common way of cutting the joint.
The tops of campaign chests were typically joined to the ends with rabbeted full-blind dovetails. Details of this joint are covered in the chapter on building campaign chests. After pulling the drawers out of a number of these chests and poking around with a flashlight, I’ve found that for this joint, it was typical to put the tails on the end boards and the pins on the top. (You can easily discern this in a glued-up joint by paying attention to the overcuts from the dovetail saw and if they are angled or vertical.)
Sometimes the corners of the carcases will be joined with through-dovetails, though I haven’t seen many of these in the wild or in auction catalogs. There are also a few chests where all the joints are half-blind dovetails and you can see the tails on the top.
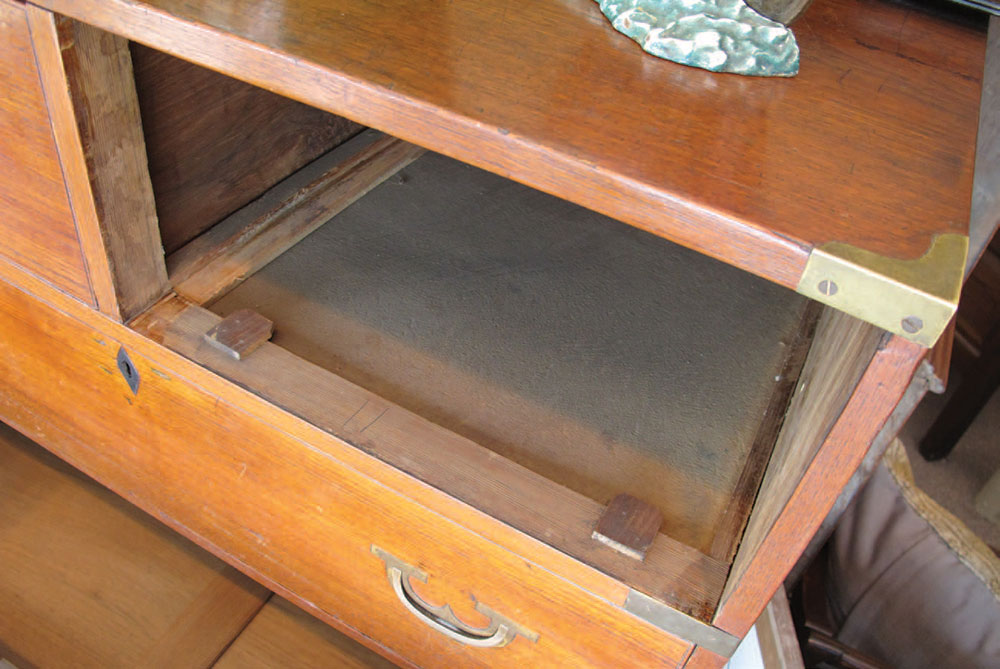
Interior Joinery
Because these chests have to be strong, the interiors are usually mortise-and-tenon web frames with dust panels – again, first-class joinery. I’ve seen a few chests where the interior dividers are solid slab panels. These are simpler to build, but the slabs add weight.
The web frames are usually attached to the end boards with dados or, in some cases, sliding dovetails. You can tell which joint the maker used by removing the brass corner guards covering them.
As far as attaching the top case to the bottom case, it is typically done with two to four dowels that stick up on one of the cases and slide into matching holes in the other case. There are other methods of registering the top case on the bottom, including brass hardware that is incorporated into the corner guards, but I haven’t seen enough of these to know which other methods are typical and which are not.
— MB