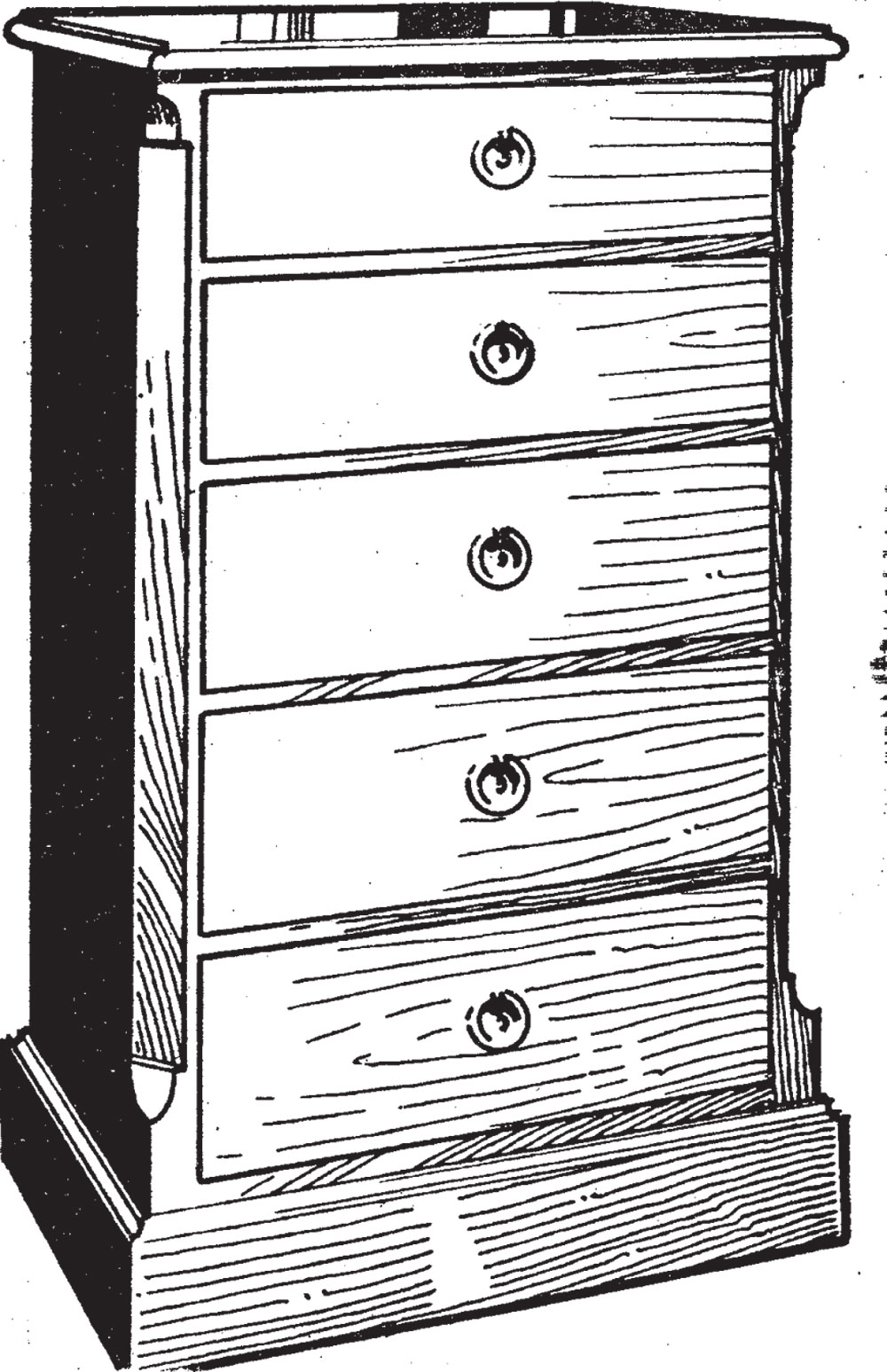
This is an excerpt from “The Woodworker: The Charles H. Hayward Years: Volume II” published by Lost Art Press.
We will assume that the chamfer is to be, say, 1-3/4 to 2 ins. wide and that the stops are to be shaped as shown in Fig. 1. In the best construction the uprights would be in the form of solid squares, the ends and the drawer rails being jointed into them. Any such joints should be marked out, cut and fitted first. In fact it is an advantage to chamfer after assembling because cramps are more easily applied.
The position of the chamfer is marked out in pencil. If the gauge is used it will make a mark which cannot be removed in subsequent chamfering. Square in the line of the stop and prepare a template in cardboard giving the shape of the stop. This is shown in Fig. 2. It is merely necessary to lay the template in position against the squared line and mark round it with pencil. The template does for both front and side.
Working the Chamfer. A saw cut has to be made up against the stops, but in addition it is advisable to make a series of cuts across the grain throughout the length of the chamfer. The purpose of this is to cut up the grain. If, in the subsequent chopping away process, a split should develop it cannot run past the next saw cut. These cuts should stop about 1/16 in. short of the finished depth. They are shown in Fig. 2.
A great deal of the waste can be removed by chopping with the chisel. Use a wide chisel and, holding it bevel side downwards, strike the handle with a mallet. Watch carefully the grain and if it appears to run downwards work in the opposite direction. In any case, however, stop about 1/16 in. short of the line. This is shown in Fig. 3.
It is immaterial whether the ends are finished first or last. The bullnose plane is extremely useful, but much careful paring with the wide chisel is also necessary. The ordinary smoothing plane can be used for the bulk of the middle part of the chamfer. It will have to run out towards the ends, of course, and these parts will have to be finished with the bullnose plane or spokeshave. When approximately down to the finished line use the scraper, and make smooth by rubbing with glass-paper wrapped around a flat block.
The Decorative Stop. It will have been seen that saw cuts are also made across the grain of the decorative stop. Note that they stop well short of the pencil line. Fig. 4 shows how the bulk of the waste can be cut away in steps with the chisel. Afterwards a gouge can be used to bring the shape approximately to the line. Following this the file is used as in Fig. 5. Give this a compound movement, rocking it sideways at the same time as it is pushed forwards. Scraping follows and finally glasspaper, this being wrapped around a rubber.
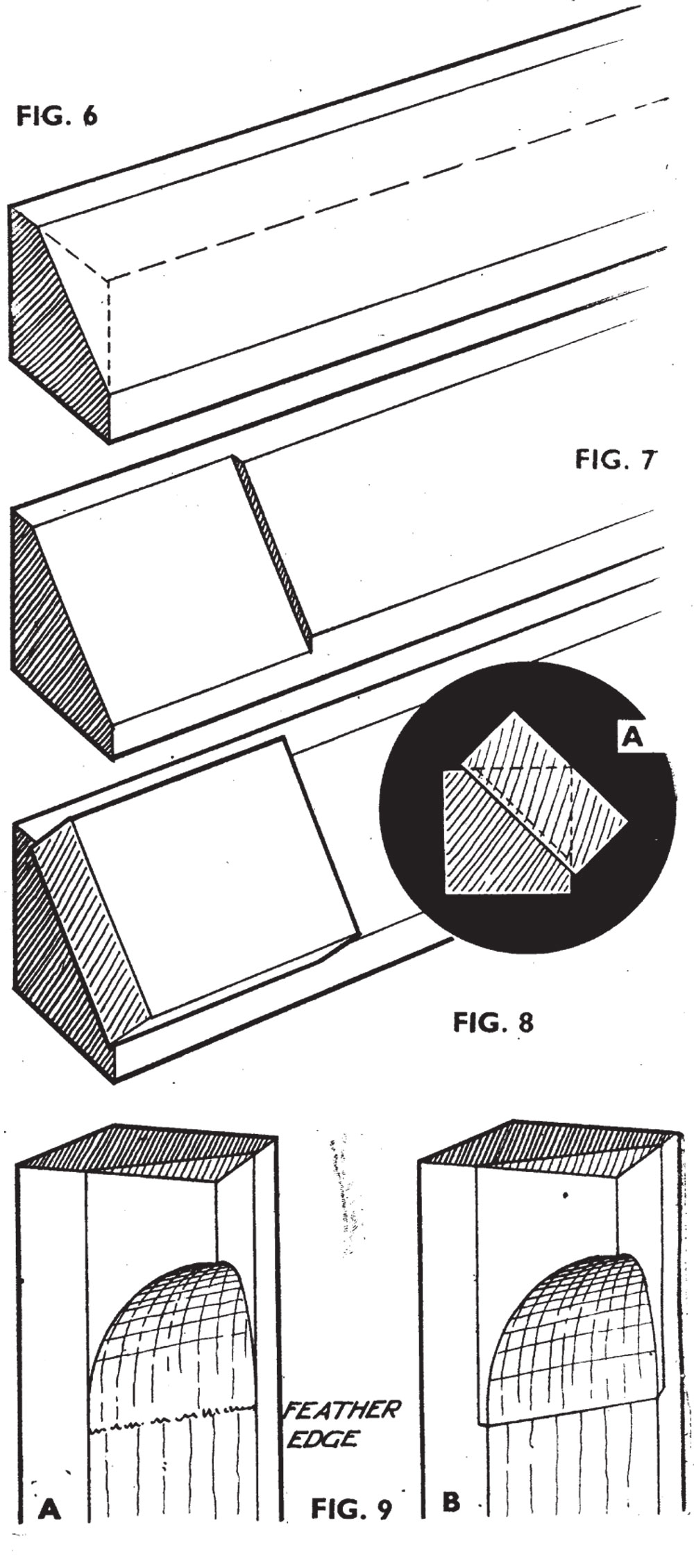
Planted on Construction. To avoid the troublesome necessity of working a wide chamfer up to a stop, the method of planting on the stops is sometimes adopted. The advantage is that the ordinary plane can be worked right through from end to end.
The first stage of working the plain chamfer is shown in Fig. 6. The blocks for the stops could be glued straight on at the ends but this is not very satisfactory, the better plan being to cut away the chamfer to a depth of about 1/8 in. as in Fig. 7 and plant the blocks in this recess. This is really essential in the case of a curved stop which forms a continuous sweep with the chamfer. At A, Fig. 9, for instance, there would be a feather edge in the event of the block being planted straight on.
Fig. 8 shows how the block is glued on, It must be thick enough to enable a square corner to be worked.
— MB