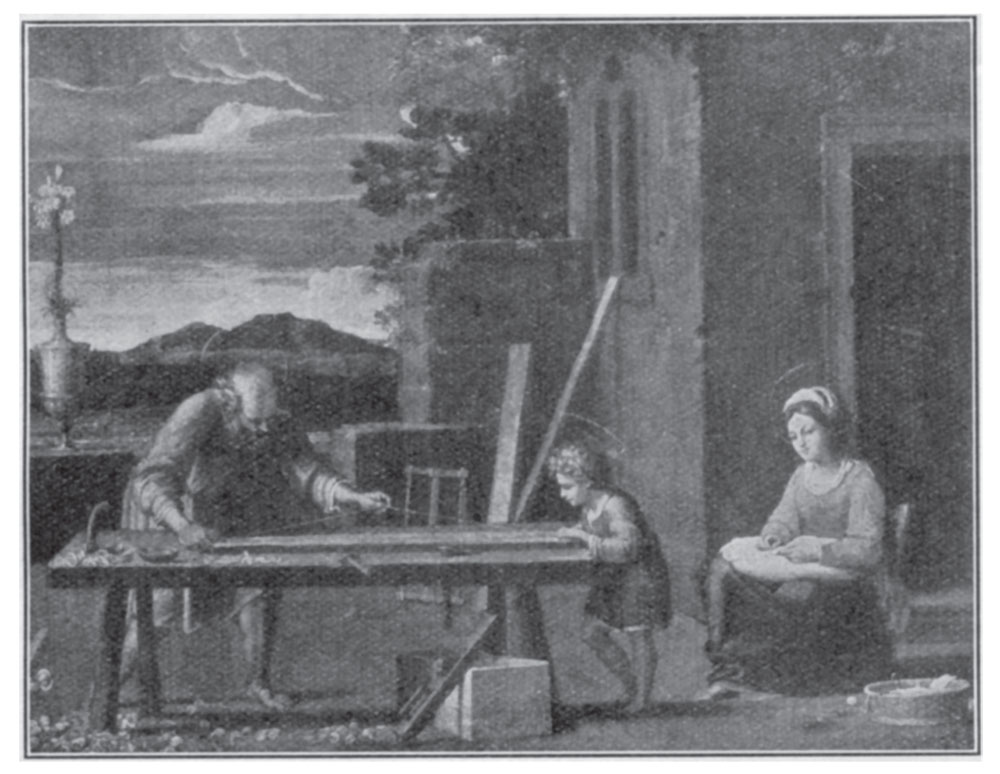
This is an excerpt from “The Woodworker: The Charles H. Hayward Years: Volume I” published by Lost Art Press.
One sometimes gets in an indirect sort of way, a remarkable light on the things that people used to make and use. A man may explore all the usual channels in an endeavour to investigate a subject with little result, and then tumble across a piece of information entirely by accident.
The writer recently experienced something of the sort when visiting the Royal Academy Exhibition of 17th century art still on view at Burlington House. One of the pictures is the famous “Christ in the Carpenter’s shop,’’ by Carracci, and it shows Christ as a boy watching Joseph at work at his bench.
The point of interest is that Carracci painted in his picture the sort of bench and tools with which he himself was familiar in his age. In other words, the tools shown are the sort that carpenters used during the 17th century in Italy.
Some of them are extraordinarily like the tools we have in use at the present time. There is a frame saw identical with the kind still used by German woodworkers to-day. It is rather like a large bowsaw, but has a much wider blade. It is used for much the same purpose as the handsaw with which we are familiar. Then there is a claw hammer that might have been bought at a modem tool store, except that the head is square instead of rounded; also the handle. Passing through the bench is a holdfast, similar in principle to the modern type but without the screw arrangement. The carpenter placed the end over the wood to be held, and struck the pillar passing through the bench, so that it wedged itself in. A sort of small adze intended for use with one hand is interesting. It is rather like a small axe, but with the blade turned at right angles with the shaft. The latter is curved, and finishes with a curved scroll which would prevent it from flying out of the hand. Joseph himself is engaged in marking out a board, and is using a chalked line to mark a straight line.
Most interesting of all, however, is a trying plane which lies propped up on a box beneath the bench. It would be about 22 ins. long with a cutter of, say, 2-1∕ 2 ins. Its depth appears to be certainly no more than 2-1∕4 ins. Probably it may have been deeper originally, and became thinner from having been planed true many times.
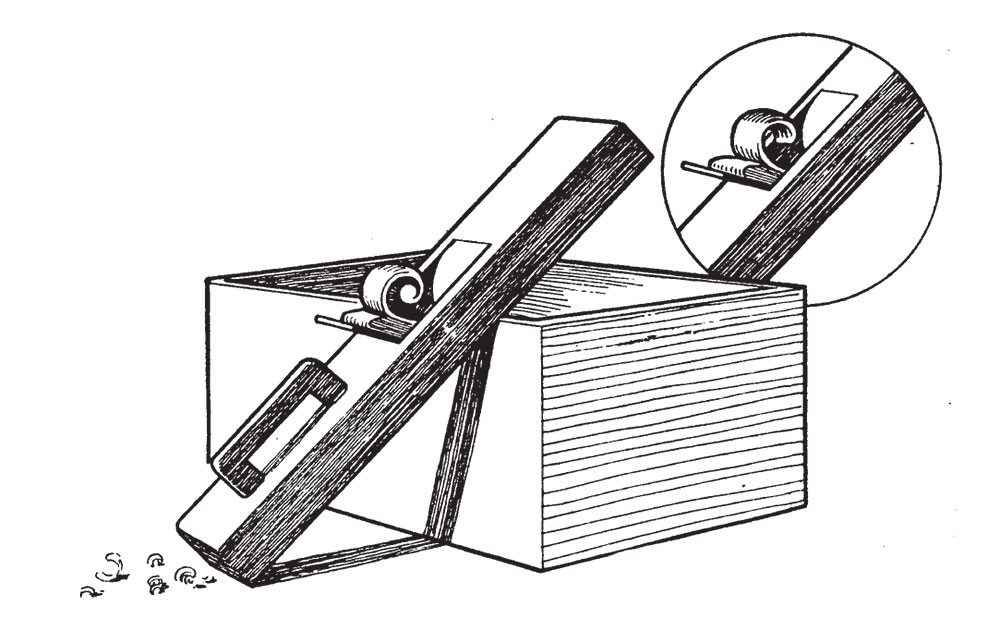
One feature that immediately arrests the attention is the pitch of the cutter. It is extremely high; so much so that its action must have been almost that of a scraper. Yet there are scrolled shavings lying on the ground such as one might expect to take off with a plane of normal pitch. It is, of course, possible that the artist has gone astray in this respect, and that the cutter was set lower, but, as shown, it is not more than 15 degrees out of the vertical. It must have been extremely hard work using such a plane, and the shaving can only have been thin.
There is just this in it; planes in those days had no back irons, and the tendency would be to make the pitch as high as would be practical to minimise any tendency to tear out. So high an angle, however, seems an exaggeration.
There is one point which has puzzled us a good deal; that is the rounded piece immediately in front of the cutter. When, in the first place, we saw a black and white photograph of the picture, we immediately assumed it to be a shaving. On examining the actual picture, however, there were several things to suggest that this was not the case, but that it was in reality a handle formed out of the wedge. The detail is admittedly not clear, but whereas all the shavings on the floor are light, the detail in question is of the same colour as the rest of the plane. Many old trying planes had handles at the front, though in front of the escapement. One would imagine that a handle just in front of the wedge would be liable to cause the shavings to choke, but, there it is. Readers may like to consider the matter for themselves and draw their own conclusions.
— MB