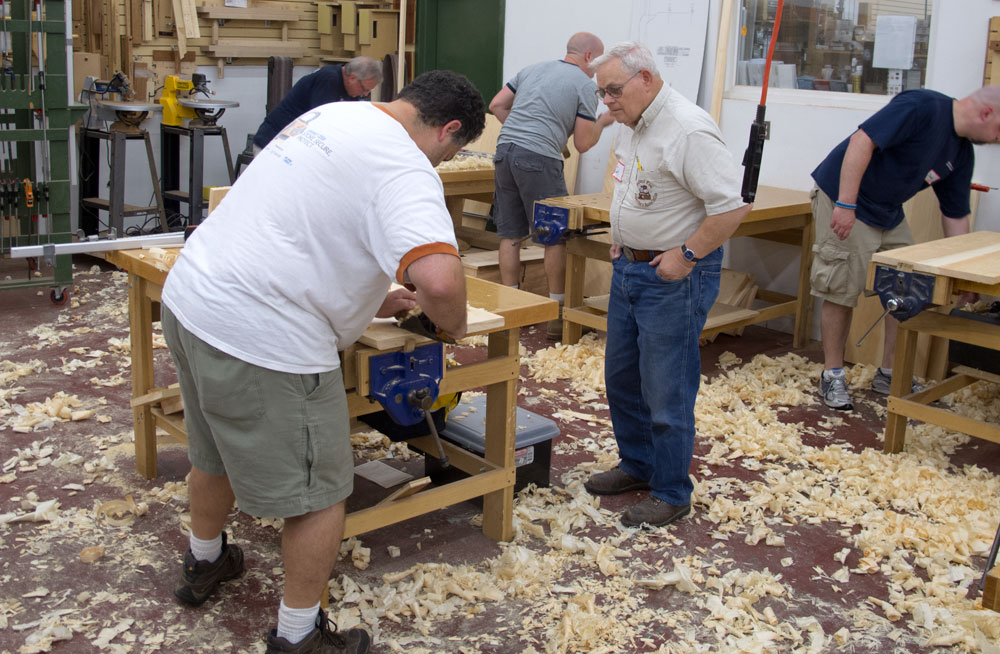
My good friend Carl Bilderback passed away tonight after a hard-fought battle with cancer.
If you are a member of the Mid-West Tool Collectors Association (M-WTCA), then you almost certainly knew him. (And if you are not a member, then he most certainly would want me to twist your arm to do so.)
I first encountered Carl when I was a junior-level editor at Popular Woodworking Magazine in the 1990s. Carl subscribed to all the magazines, and he enjoyed calling up editors and pointing out their factual errors and typos. But he was also generous with his praise when you did something well.
After years of phone calls I finally got to meet Carl in person at a M-WTCA meeting and we became fast friends. For the next decade or so whenever we met at shows or woodworking events, he’d take me aside to show me something.
Usually it was a cache of gorgeous user-grade tools. And he’d ask: Do you know any young woodworkers here who could use these tools?
I usually did. And Carl would seek them out and give them the tools – no strings attached.
He did this all over the country. Sometimes he’d read about a young woodworker and simply send them some tools they could use. He knew that the future of the craft depended on us helping young woodworkers take their first steps into the craft.

For me, he personally stood as an example of both intellectual rigor and endless generosity. He never pulled punches when he thought you were wrong. He wanted the written record of hand tools and techniques to be correct. But he never hesitated in helping you with information, tools or encouragement.
He also was a ridiculous showboater and prankster.
Carl, a union carpenter, had a voice like an angel and would amaze the members of M-WTCA when he would sing at their shows. He also sang at church, funerals, weddings and (occasionally) at a Lie-Nielsen Hand Tool Event.
During one event in Cincinnati, Carl walked into my office wearing a blonde wig and began signing a pitch-perfect rendition of “Tiptoe Through the Tulips” a la Tiny Tim for show attendees.
And even to the end, he sang at karaoke bars with his girlfriend Sue (though they are both teetotalers). She sang country and western. He sang show tunes.
And it was this funny combination of being a carpenter, singer and prankster that leads to my favorite Carl Bilderback story of all time. It’s just slightly off-color, but in a sweet way.
Carl worked as a carpenter mostly in the Chicago area, and during his career he was in charge of a remodeling job at Oprah Winfrey’s place. Winfrey (or her interior designer) had requested that all the screws used for attaching the switchplates be gold plated.
So they sent out all the screws to be plated. When they came back, Carl was put in charge of them so they didn’t get “lost.” At the end of the job, there were a few left, and Carl got to keep them.
Carl traveled a lot as a carpenter. And when he landed in a new town he’d seek out a piano bar or karaoke bar so he might get to sing. When he walked into the place, he’d sit next to a woman who was alone.
After some small talk, he’d tell the woman: “I am going to give you the most incredible screw of your life.” And then Carl would give them one of Oprah Winfrey’s gold screws and tell them the story.
I sometimes wonder where those gold screws are. And I wonder where all the block planes, chisels, miter boxes and saws are that Carl gave people over the years. I hope they’re in good hands and bring joy every time they come out.
I know he’d like that.
— Christopher Schwarz
Like this:
Like Loading...