We will begin taking pre-publication orders for the deluxe version of “With All the Precision Possible: Roubo on Furniture” at noon Eastern time on Wednesday, Feb. 22.
The book will be $550, which includes delivery in the U.S. International customers will pay an additional charge based on the actual cost to ship it to them (you’ll be contacted before the book ships about this additional charge). We are printing 1,000 copies. No more.
This book is expected to ship in summer 2017, barring production or transportation delays. Before you order, please read the following important information on being a “subscriber” to this book.
The Important Part: Please Read
Customers who order before March 15 will be listed as a “subscriber” at the back of the book. By default, we will print your first name and last name exactly as it appears in your order for the book (so please spell your name correctly). If you do not wish your name to appear in the book, you must send an email to meghan@lostartpress.com before March 15 along with your order number and a request to have your name omitted.
After March 15, no changes can be made to the list of subscribers.
The Scary & Amazing Part
As we were negotiating the print job with the plant, I calculated that by the time we pay for this press run we will have spent more than $500,000 on the Roubo translation project, a mind-blowing figure for someone who drives a beat-up 10-year-old truck.
I am not saying this to impress you, but to 1) Thank you for your support and 2) Thank you in advance for your support on this deluxe version.
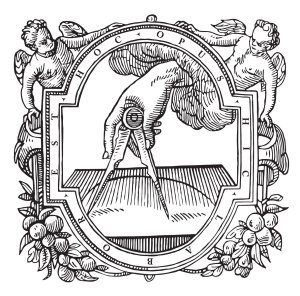
The Manufacturing Details
Measuring 12-1/4” wide x 17-1/4” tall by almost 2-1/4” thick, “Roubo on Furniture” will be the largest and most luxurious book we have printed since Lost Art Press was founded in 2007.
The 472 pages of text will be printed on #100 Mohawk Superfine paper, perhaps the finest domestic paper available today. To match the fine paper, the images and plates will be printed in full color at a linescreen few presses can achieve.
The result is a level of detail and clarity rarely seen in any book of any era.
The book’s signatures will be sewn, casebound and reinforced with a fiber tape that will ensure the binding will outlast us all. The hardbound boards will be covered in a beautifully printed pattern with a cotton cloth cover on the spine. The spine will be then debossed in gold and black.
The entire book will come in a custom-made slipcase covered in a complementary-colored cotton cloth.
Our deluxe version of “Roubo on Marquetry” (long since sold out) was manufactured to these same high specifications and was named one of the “50 Books of the Year” by by the Design Observer, in association with AIGA and Designers & Books.
Questions?
We are happy to answer any questions about the book – just leave us a comment and we’ll do our best. Tomorrow I plan to post a video tour of the deluxe version of “Roubo on Marquetry” so you can get a feel for the manufacturing details of the deluxe “Roubo on Furniture.”
— Christopher Schwarz
Like this:
Like Loading...