Comfort, v. 1. To strengthen; to encourage; to support; to invigorate.
— The Shorter Oxford English Dictionary on Historical Principles
Had it not been for COVID-19, many of us would have been in southwestern Massachusetts this weekend for Fine Woodworking Live. Even as a hard-core loner I had a blast there last year, and while the news that this year’s event had been cancelled did not surprise me, I’m really missing the opportunity to reconnect with some people I met there. Among them is furniture maker Aspen Golann, whom I profile here as part of my “Comforting Soups” series* of interviews with woodworkers I find inspiring, especially in this current moment.
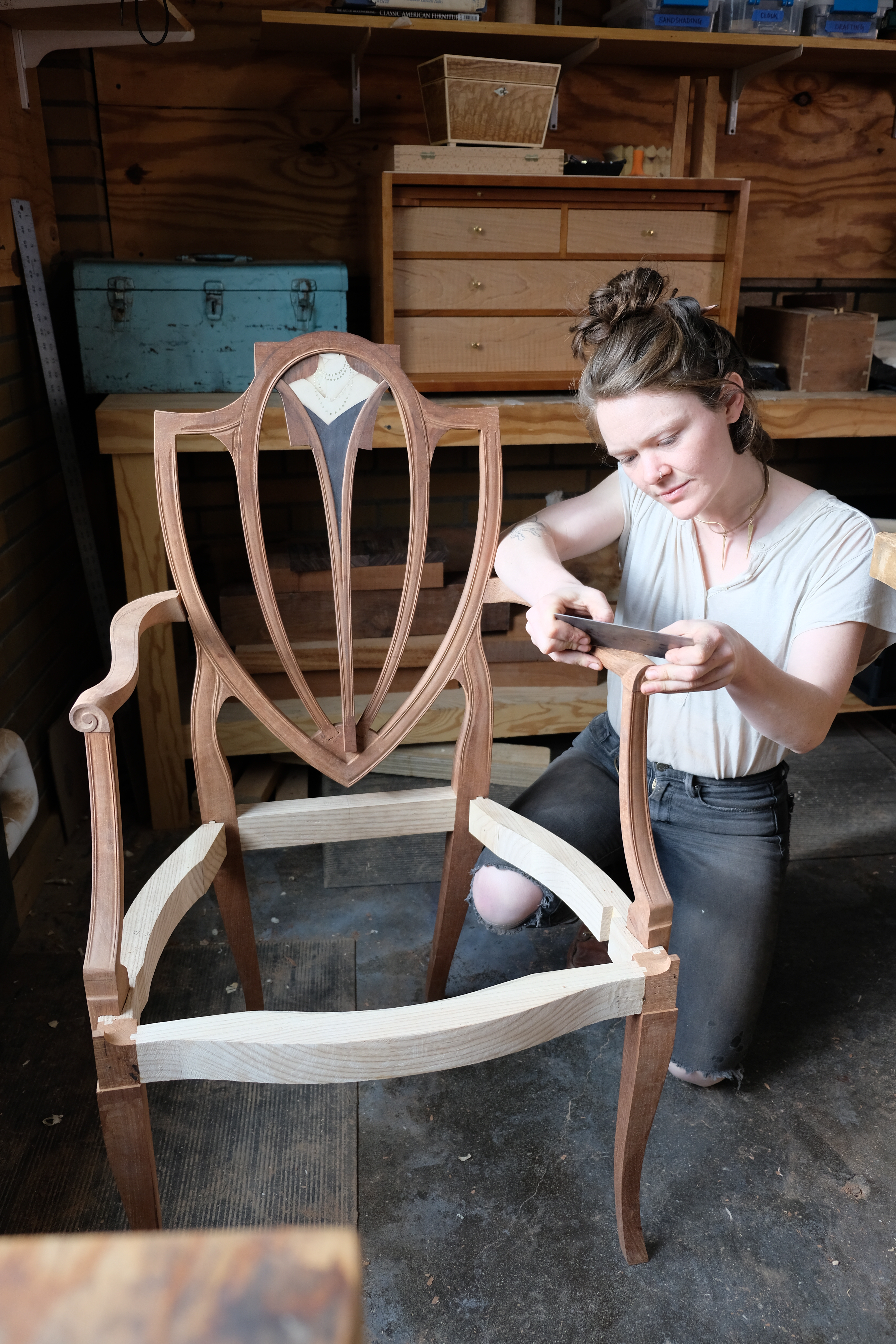
On April 6th Aspen Golann published a video on Instagram titled “One way to make a brush.” Knowing Aspen as I do (which is to say, not well — we’ve met just twice, but every contact I have with her is a riotous explosion of ideas and laughter and empathy), I anticipated a piece of work that would be thoughtful, as well as beautifully put together. But it was so much more: a detailed instructional video that takes viewers through every step of the process, from design to finishing, with hand-lettered instructions written in real time – and humor! – all sent out to the universe at no charge. Even better, Aspen includes instructions for improvising with tools and materials that most of us are likely to have on hand, knowing that we’re staying home in response to the current pandemic (and many folks have seen their income reduced, if not slashed to nothing). Even though I’m probably not going to make a brush, I’ve watched the video multiple times for fun, because (let’s be honest) even the loners among us are feeling isolated and could do with a bit of cheer.
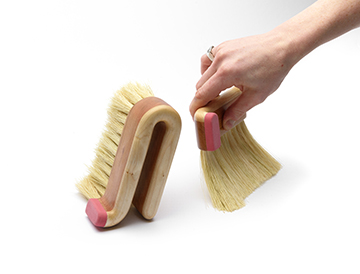
Aspen, 33, is the Wood Studio Coordinator at Penland School of Craft near Asheville, North Carolina, where she has worked since May 2019. As with other schools and colleges across the country, the campus is currently shut down. So Aspen made the video in her garage, using an old desk reinforced with 2x4s, to which she bolted a vise.
Before taking the position at Penland, Aspen did a residency at the Center for Furniture Craftsmanship and collaborated with Peter Galbert for a few months.
“Hang on a sec,” I hear you thinking. “Collaborated with Peter Galbert? How did she make that happen?”
They met when she was a student in the two-year furniture program at North Bennet Street School in Boston, where Peter is a guest lecturer and instructor. “Pete’s an artsy nerd, and I think he saw some of that in me,” Aspen says with characteristic modesty. “He’s always excited to meet maker-weirdos even if they’re students – and I was so jazzed to connect with someone excited about styles outside of iconic period furniture. Pretty soon we were just regular friends.”
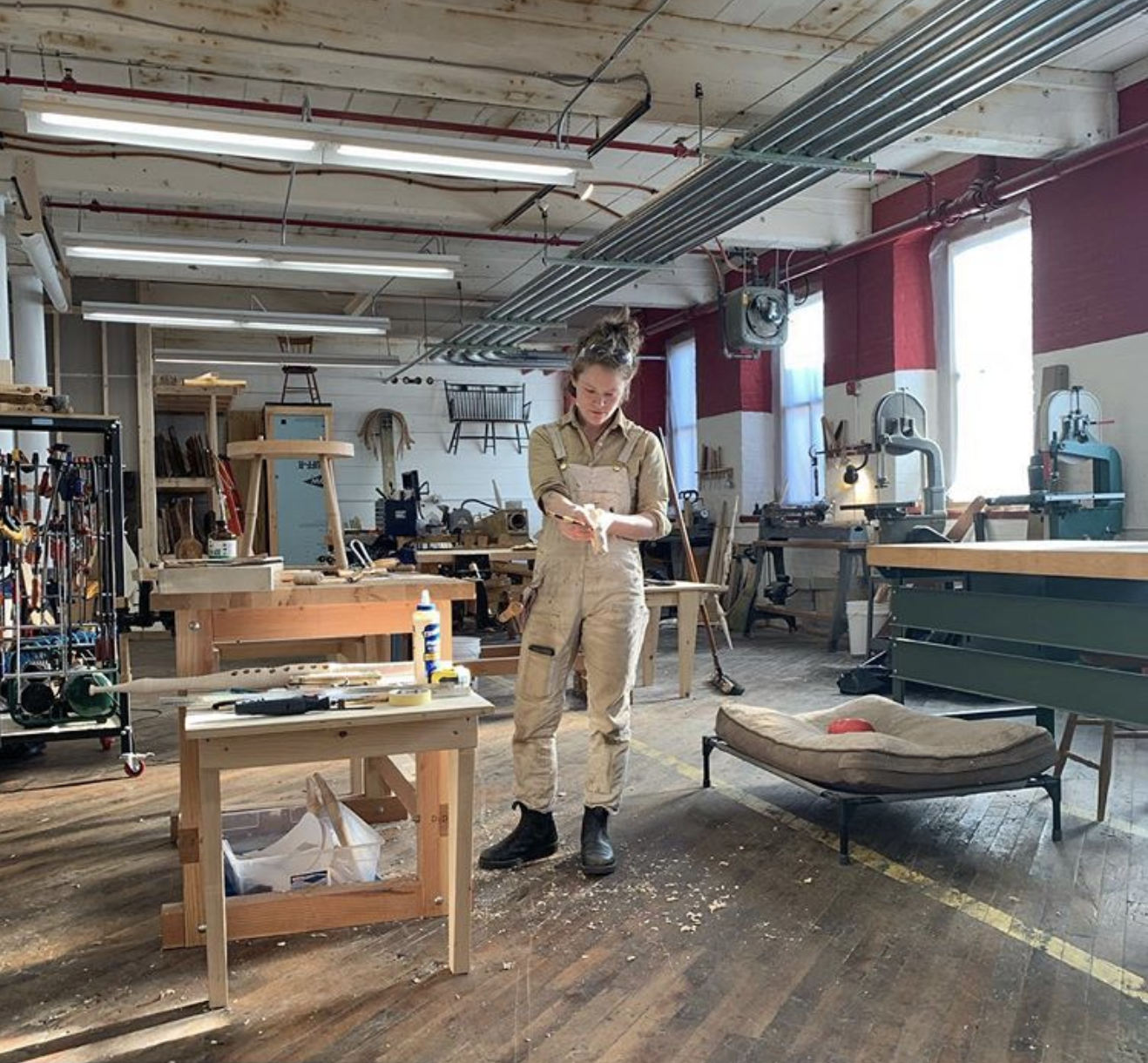
After graduating from NBSS she received a commission she considered out of her league: to make a Windsor settee. Not just any Windsor settee, this one “needed to perfectly kiss the wall of the clients’ spiral staircase.” The designer Beata Heuman chose her to build it because she had made a table for her the year before. She pitched the collaboration to Peter: “We split the dough and make the chair.” He agreed. “In some ways, making that chair felt like a master class,” she says. “I got to ask every question and see him work through every problem and work through them with him and alone. It was really cool.”
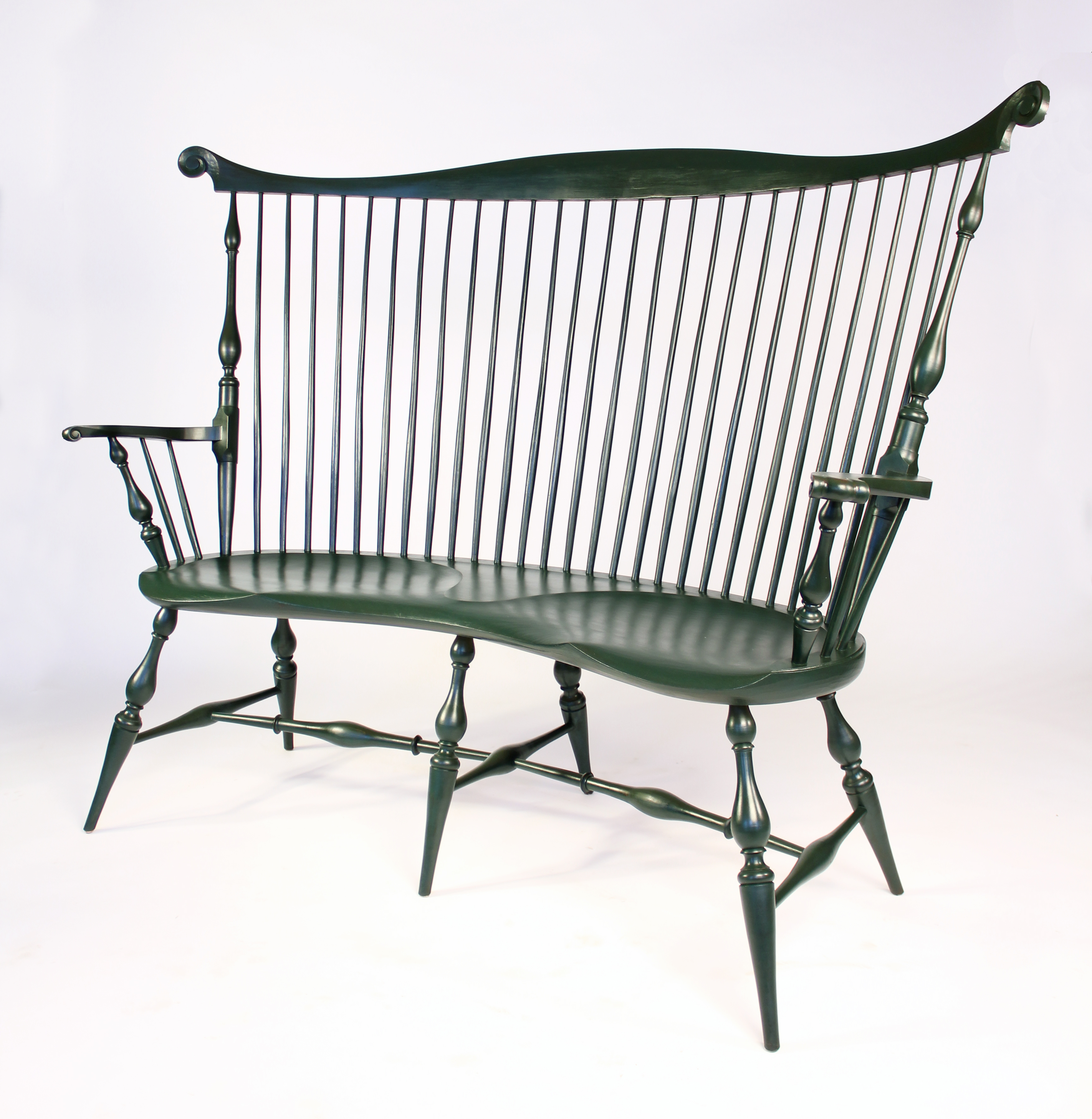
For a creative fix while she was a student in the program at North Bennet Street, which is renowned for its focus on high traditional East Coast furniture techniques and forms, Aspen took classes in glass enameling and lost wax casting at Penland. She also co-taught a sculptural spoon carving class with Julian Watts during a residency at Anderson Ranch. “We were scheduled to teach an experimental carving course with him at Penland this summer,” she says, disappointed.
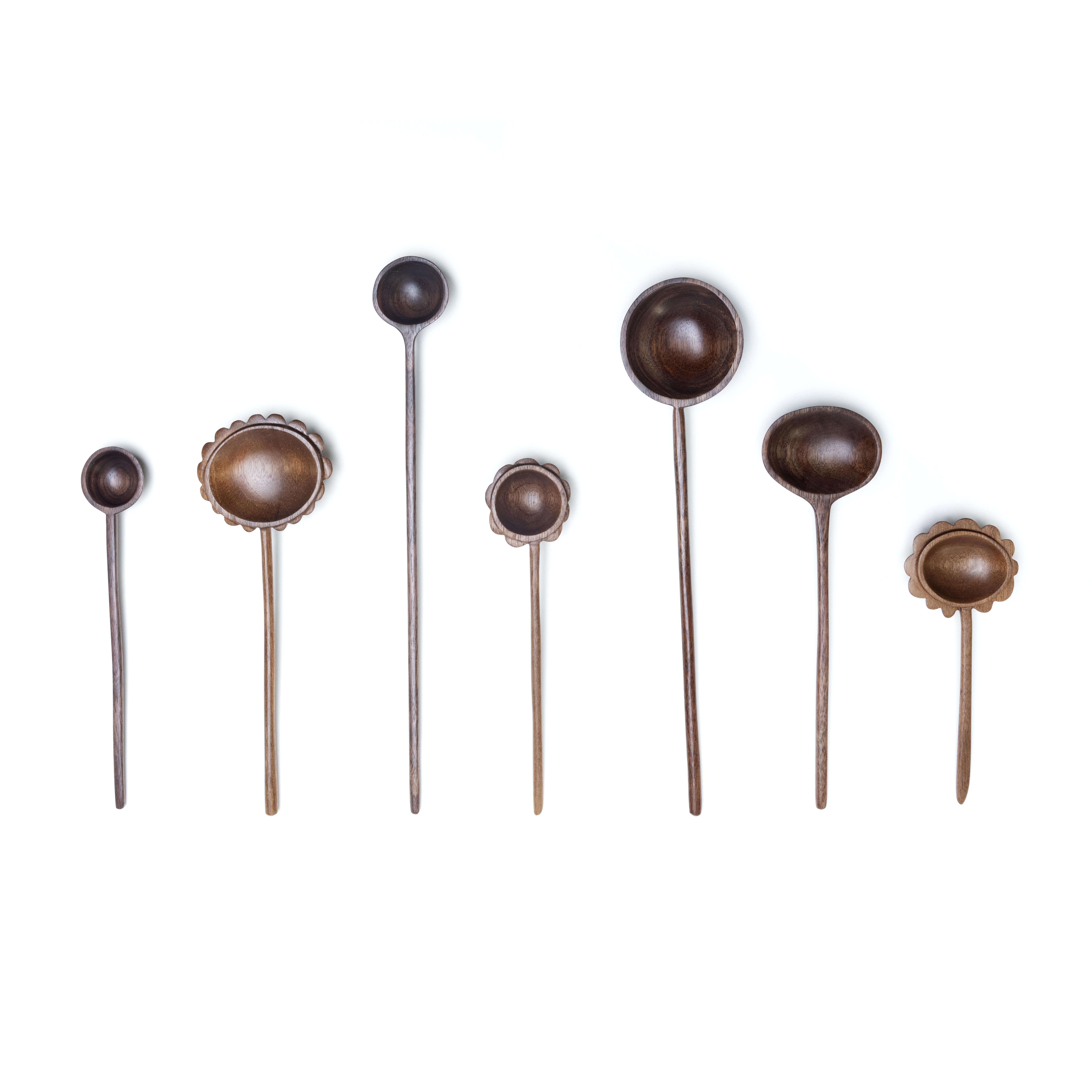
Having seen a number of Aspen’s spoons online, I’ve been struck by their fine lines, so different from those of greenwood spoons. I wondered whether she makes them from kiln-dried wood. Yes, she answers, adding that some of the bowls are so thin “you can read the newspaper through them. The handles are three pieces of veneer thick; because they’re sandwiching a piece of shop-sawn ebonized maple veneer, they’re super strong.” To glue the material together she uses Titebond III.
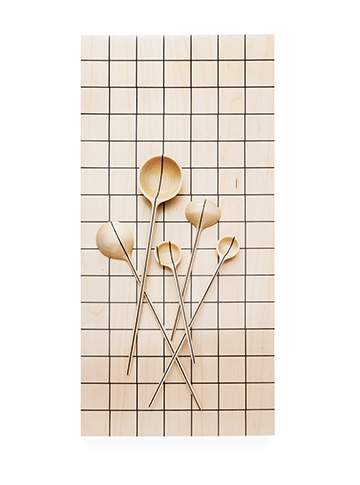
Before her studies at North Bennet Street, Aspen spent six years teaching art and Russian literature at a couple of private high schools, The Cate School in Santa Barbara (“It wasn’t a great fit for me culturally – no jeans, no first names, water polo – but I loved my students; I still text with them”) and The Putney School in Vermont, which was more progressive; it had a full farm and strong focus on art and student independence. But this is Aspen Golann we’re talking about, so you won’t be surprised to hear there was more – in this case, a class called “From Sheep to Shawl,” in which students learned to shear a sheep, spin the wool and weave it into a shawl. And because color is important, there was also a dye garden, where they grew plants such as marigold and indigo to color the wool.
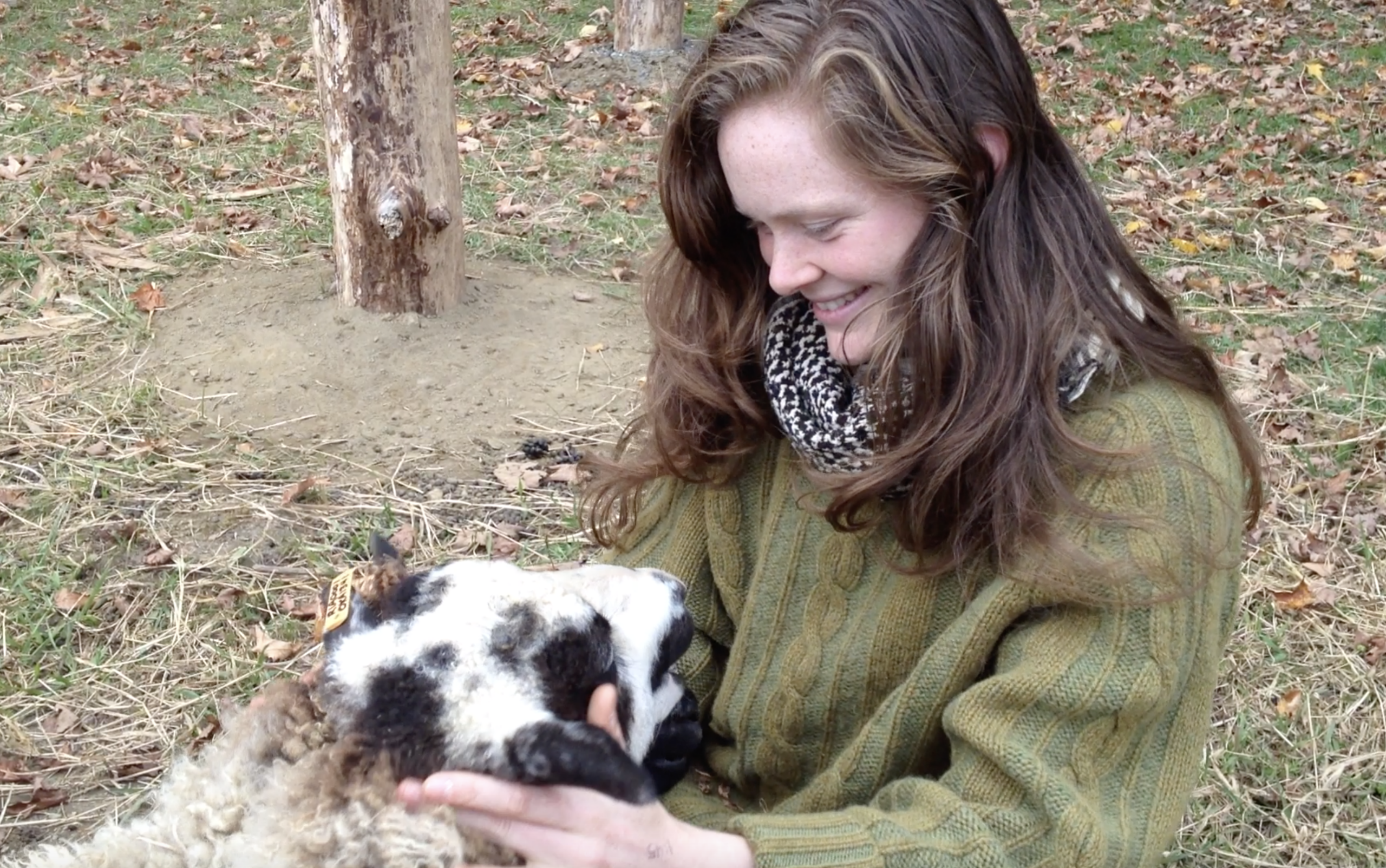
“I loved teaching,” Aspen says. “It wasn’t a ‘safety plan’; it was my whole plan, a big-kid job. I did it long enough that I could do it, leave it, go back to it. But [at 28 I realized] there was [still] time to do something really dumb” – here she’s indulging in her trademark self-deprecation – “and that was going to furniture school.”
“School is a place where people don’t mind if you’re terrible at things.” She had taken an ‘art with a function’ class as a student at Kenyon College in Gambier, Ohio. “I had always loved art, but it wasn’t as fulfilling as it needed to be for me to pursue it as a full-time job. Somehow, when you add functionality, it was like this now matters. It’s a sculpture you can read by. It’s a sculpture you can sit on, and even better, it’s comfortable.”
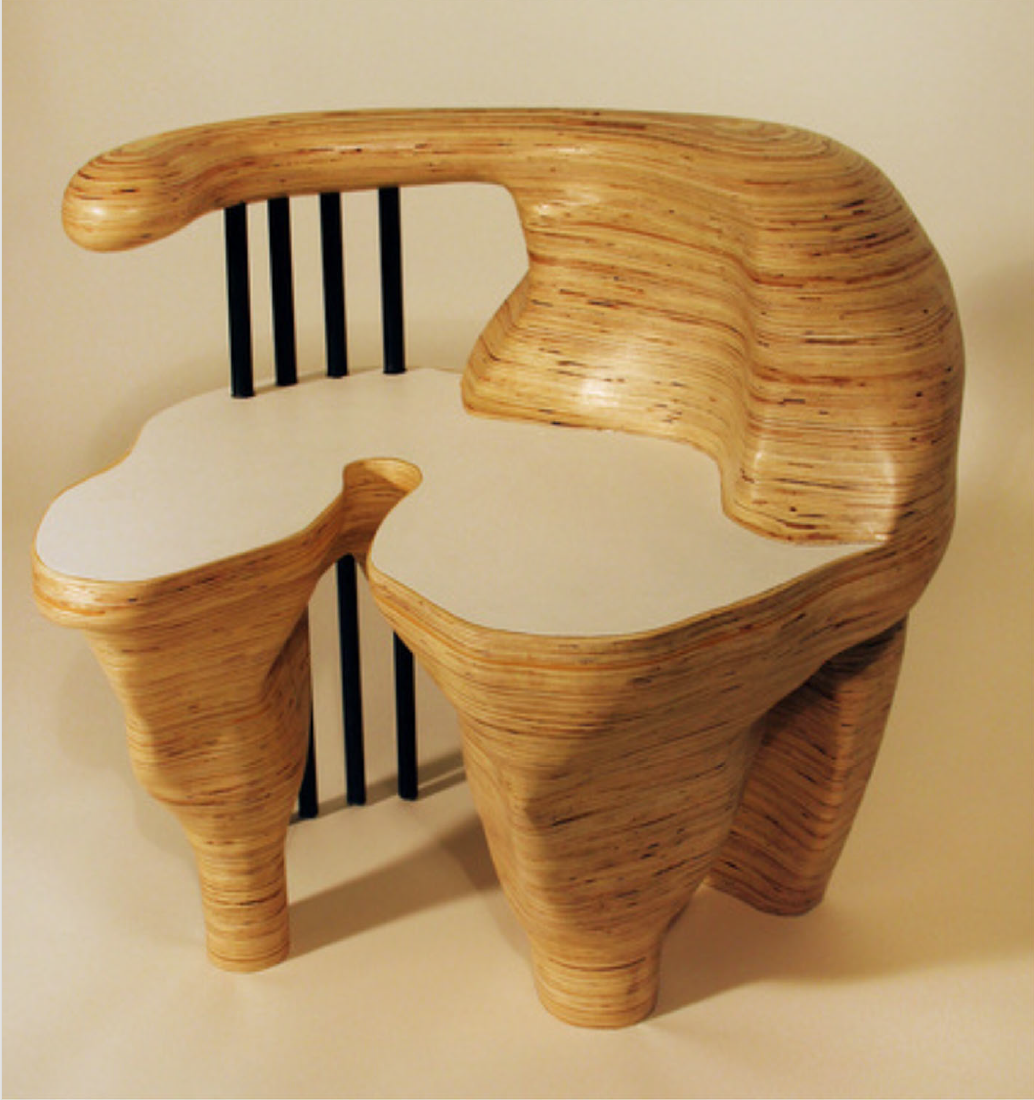
Now, at 28, she wanted to explore furniture. “I’ve taught myself to do a lot of things, but furniture…I couldn’t even imagine how I’d approach it. Furniture felt like the most inaccessible art form, both culturally and technically, for a young woman interested in art. I felt I had to go to school for those things. I knew that my gender meant that if I was going to make it, I needed the pedigree.”
While visiting her parents in Boston in 2016 she visited North Bennet Street School, and “it was like, everything they were teaching seemed completely and impossibly out of my league. This is what I should spend money on: the thing that I can’t teach myself. I consistently invest in things that play to my weaknesses. I like doing things that are too hard for me.”
As a student at NBSS Aspen adapted historic forms to a feminist perspective. As she puts it, “I was one of the only women in a shop with male furniture makers, learning from other male furniture makers. When I feel isolated, I look for ways to express myself. At NBSS I was surrounded by masters of period furniture forms, so I committed to learning as much as I could from them – while simultaneously looking for ways to incorporate my artistic background and to talk about my experience as a woman.” In Aspen’s rendering, an Eli Terry shelf clock that would historically have had a farm scene reverse-painted on the glass panel now had the lower half of a woman’s body. “I like to blur the line between furniture and figure sculpture. I literally inserted myself in my pieces.
“I really worked with my instructors,” she emphasizes, as someone who in no way takes the work of dedicated teachers for granted. “I respected them and committed myself 100 percent to their expertise and put my own interests on the back burner. Being creative with the furniture allowed me to strike a balance – between traditional and contemporary styles, and between the roles of student and designer.”
She follows this earnest testimonial with a flourish of self-deprecation. “I had prior training in fine art, and at that point I just wanted an old master to criticize my dovetails for two years – I definitely got that, and a lot more.”
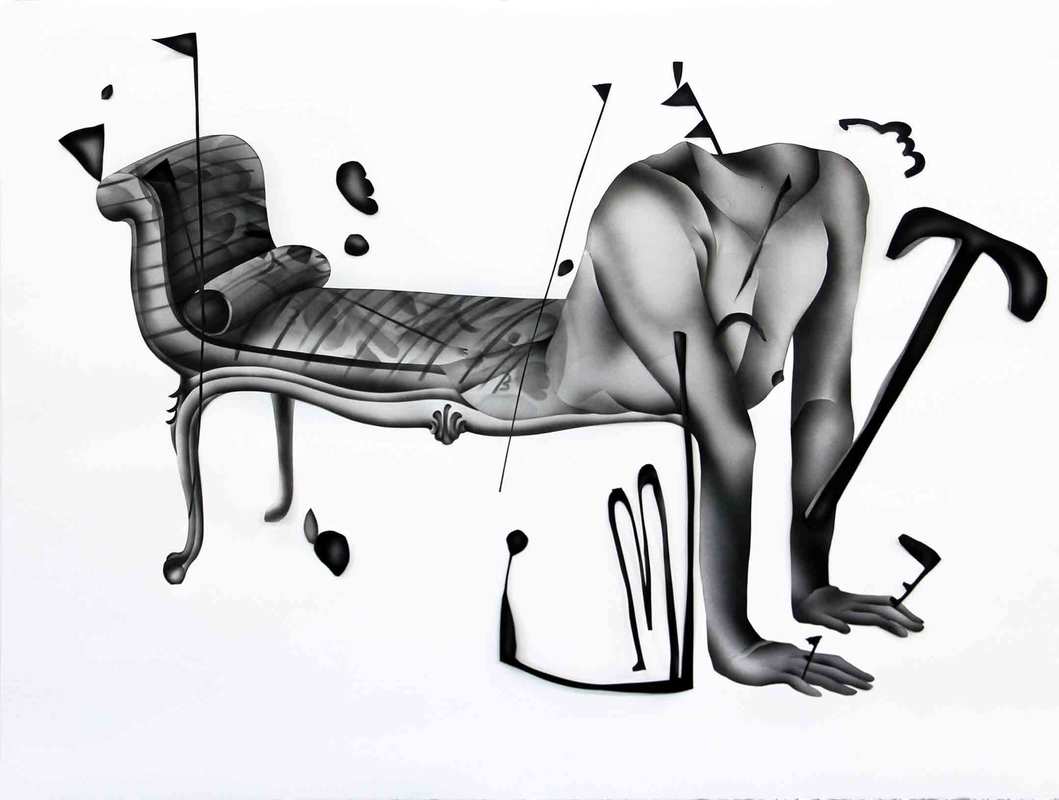
But before that…
Between college and teaching Aspen worked as a pig, turkey and apple farmer at a farm outside Austin, Texas. The property was run by a couple who needed help because the husband, a deep-water pipe layer, was gone for six weeks at a time. “And when he comes home, he’s a cross-dresser named Viviana La Tarte!” she exclaims. “The first time I saw him working, he had this really long red hair and looked about 6-1/2’ tall, with his hair blowing in the wind, and he was wearing a little secretarial outfit with a pencil skirt while chain-sawing posts for a pig fence to the same height. I woke up and came out of my cabin and thought ‘What is that beautiful being on the horizon in that beautiful outfit with that hair?’”
Not that her first sight of Viviana was any more unusual than her initial encounter upon arriving at the farm. She pulled up just as Viviana’s partner was attending to a pig in labor. Part of the pig’s uterus was stuck, and no sooner had Aspen emerged from her car than the partner shouted, “GO GET ME THE LUBE!”
“Where is it?” asked Aspen, a complete stranger to the place.
“IN THE BEDROOM, BY THE BED!”
“I ran into the house and retrieved an enormous pump bottle of personal lubricant. After I coated her entire arm in KY Jelly, she was able to get all of the piglets out safely.”
While living in the Austin area, Aspen also worked for the Haas Brothers. “They weren’t as well-known at that point,” she notes. “Their dad was looking for someone to work on a mosaic in glass, for minimum wage, for a client of his.” She worked on the project and they became friends, she and “this incredibly pleasant Austrian man who seems to appreciate my skills, affect and oddity.” He ended up commissioning her to make a painting for Leonardo DiCaprio, a friend of the Haas family.
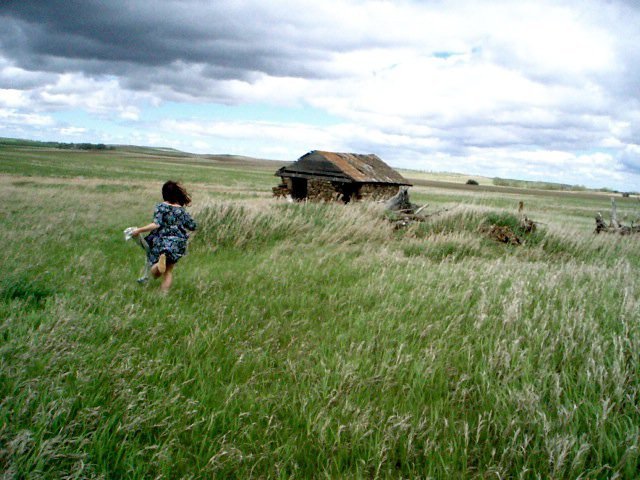
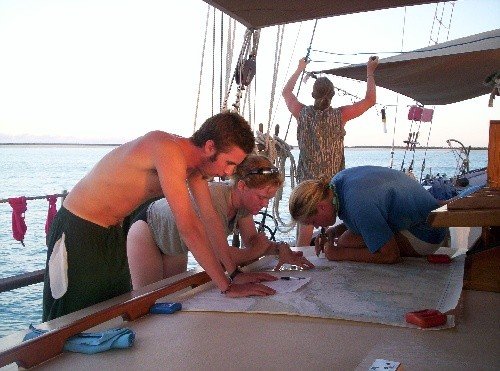
Exploring yet another layer of Aspen’s history, we find her living on a sailboat in the Caribbean during a gap year between high school and college, where she earned her professional coastal navigation and sailing licenses through the American Sailing Association. “I knew it was a once-in-a-lifetime opportunity. As long as I have food and meaningful work to do, I can pursue whatever other opportunities I want.
“I was the only crew member small enough to be lowered into the bilge for cleaning, so I think it’s fair to say I earned my keep. I worked so I got fed and did correspondence classes in coastal navigation and marine biology, out of pure curiosity. Meanwhile, we sailed from tiny island to tiny island…delivering half-food and medical supplies, and half b.s. t-shirts and [other] American stuff.”
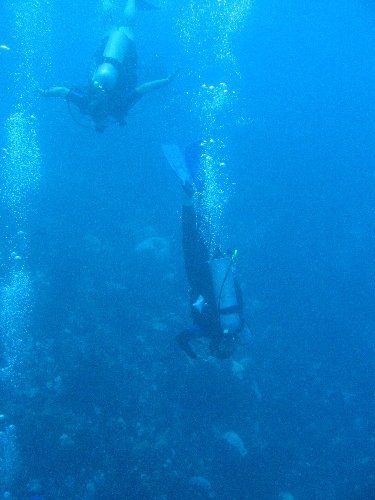
Family background
What accounts for Aspen’s relentless drive to challenge herself, to subject what is so often the self-indulgence of art to the discipline of function, to cement her ceaseless learning with so many types of accreditation? “On one level,” she answers, “I come from a long line of inventors. Things should work. On another level, some people’s creativity is sparked by having complete freedom, but most people’s is sparked by being asked to play within boundaries. When my sculptures became usable, I finally cared and saw a place for myself in the creative field.
“I’ve been trying to figure out where my set of interests came from. I don’t know anything about the women [in my family’s history], because that’s the way it goes. My mom’s parents were dairy farmers.” But her favorite possessions growing up were the small-scale pieces of furniture that her mother’s father, whom she regrets she never got to meet, had carved out of firewood. “If you’re a person who carves 15-drawer chests out of firewood, you’re a tender person, at least.
“I remember growing up in my paternal grandfather, Herbert Goldberg’s, shop. He was an inventor in a time before it was easy to commission custom hardware, plastic and glass so he knew how to make everything himself. I remember my grandmother got really mad because my brother and he snuck into the house to slump glass in the oven.” Herbert invented the refractometer and updated the pacemaker to make it more functional. Making functional things runs in the family, so Aspen says “credit where credit is due.”
Credit is also due to her paternal great-grandfather, Emanual Goldberg (1881-1970), whose inventions include microfilm and the first video camera. The first Jew to be kidnapped by the Nazi Party, he was held hostage until he handed over the rights to his inventions. He escaped to Israel; later her grandfather Herbert changed the family name to Golann, after the Golan Heights.
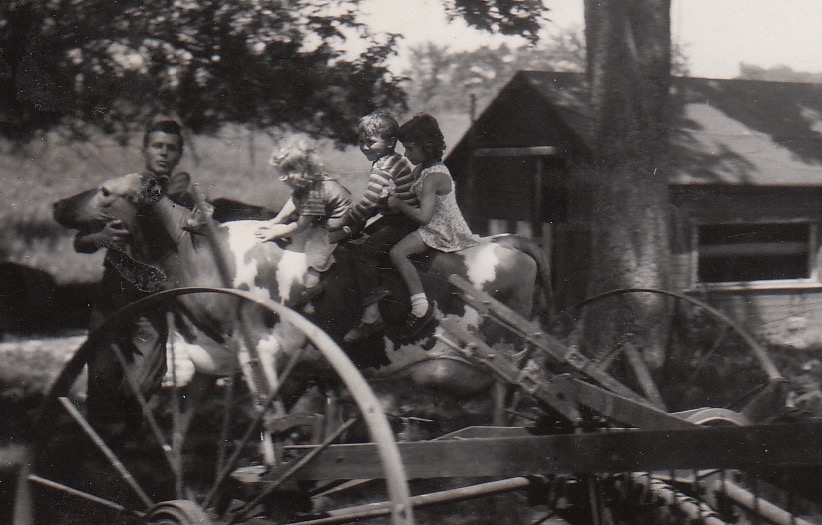
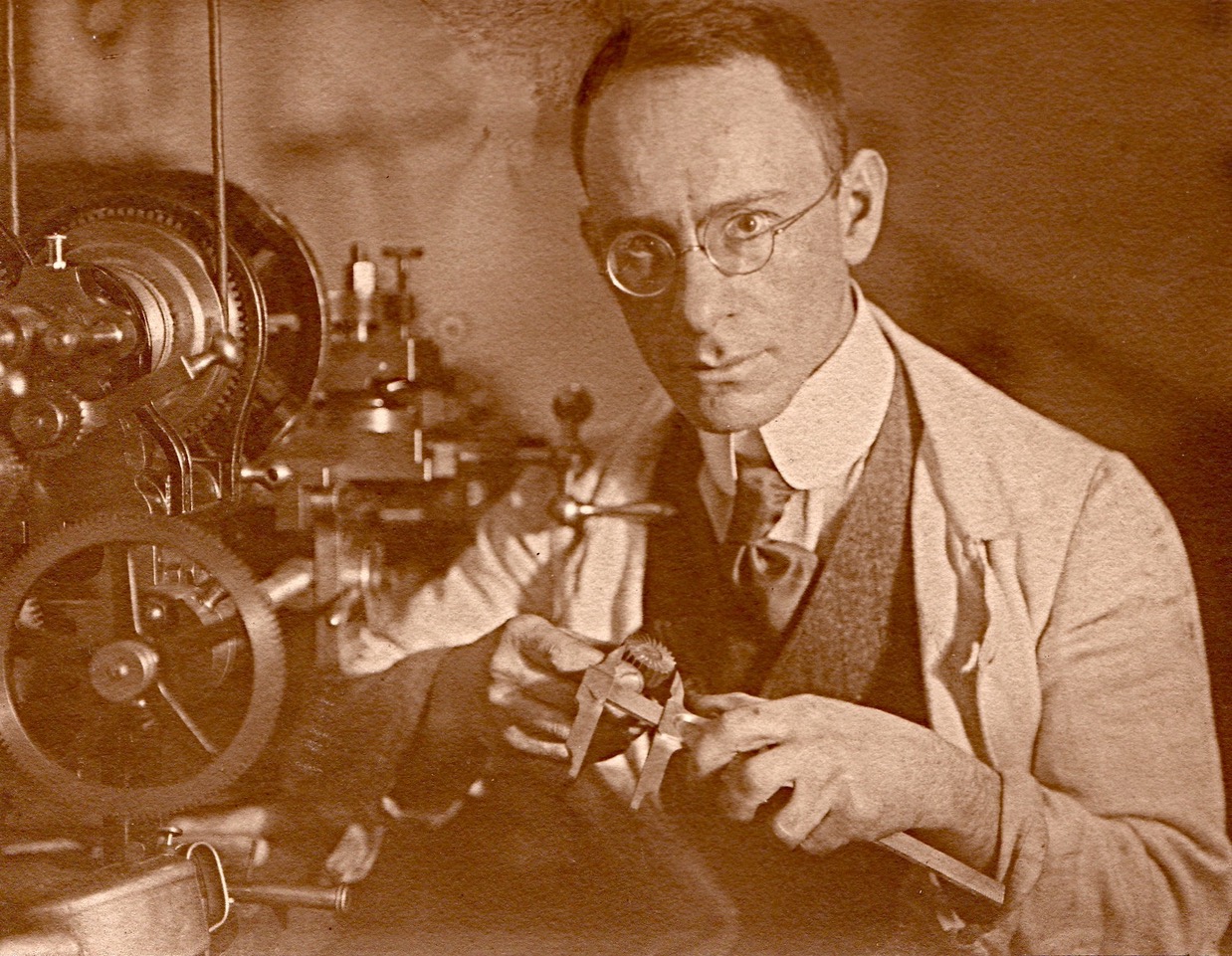
Her father, Dwight Golann, spent his career in law. After practicing as a litigator for many years he turned to mediation, which he taught at Harvard. Her mother, Helaine, is a retired psychologist and currently teaches yoga; she has worked with people living with post-traumatic stress and Parkinson’s disease. Her older brother, David, designs and teaches maker-space classes for a STEAM program in New York City that offers art classes to schools that wouldn’t otherwise be able to offer art at all.
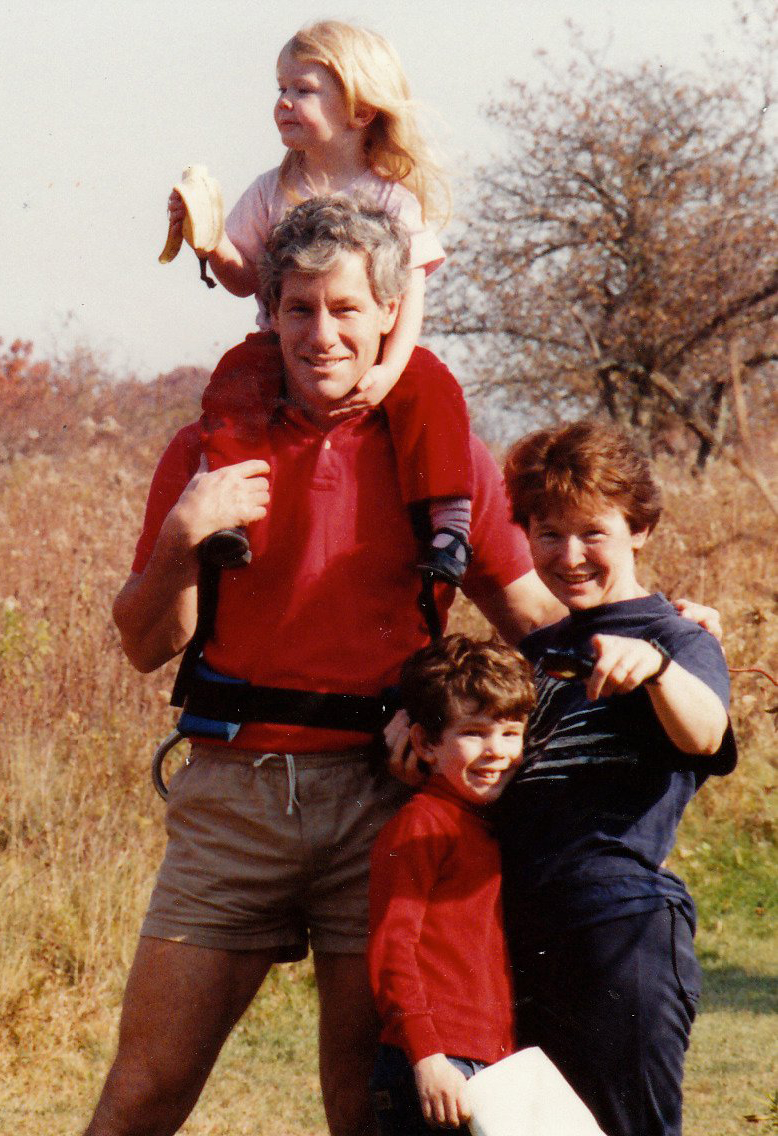
Back to today
The Penland campus is shut down through the summer of 2020. Although Aspen can’t get into her shop, she’s making pieces at home, some of which she sells through the Penland Gallery’s online store. She’s also doing some things she previously considered out of her league, such as electrical work and repairing small motors. In the past year she learned how to tune up all the machines in the shop. YouTube is invaluable, she says. “I’ve been watching kids’ videos about how small motors work and how electricity works, then working my way up.” I also highly recommend the book The Way Things Work!”
Addressing the strangeness of the current moment, she says: “It’s a good time to be patient with yourself, because you have time. The last time I remember having this kind of free time is when I was a kid on summer break. For the first time in my adult life, I have more time than anything else. I tell myself, ‘You have different resources, so you’ve got to do different things. The reason you’re feeling lost in all the time is…because normally time is our most limited resource. And now things are flipped. You don’t have money, but you do have time. So that’s why I made that video. Because I know people need support and distraction, and all it cost me was time.
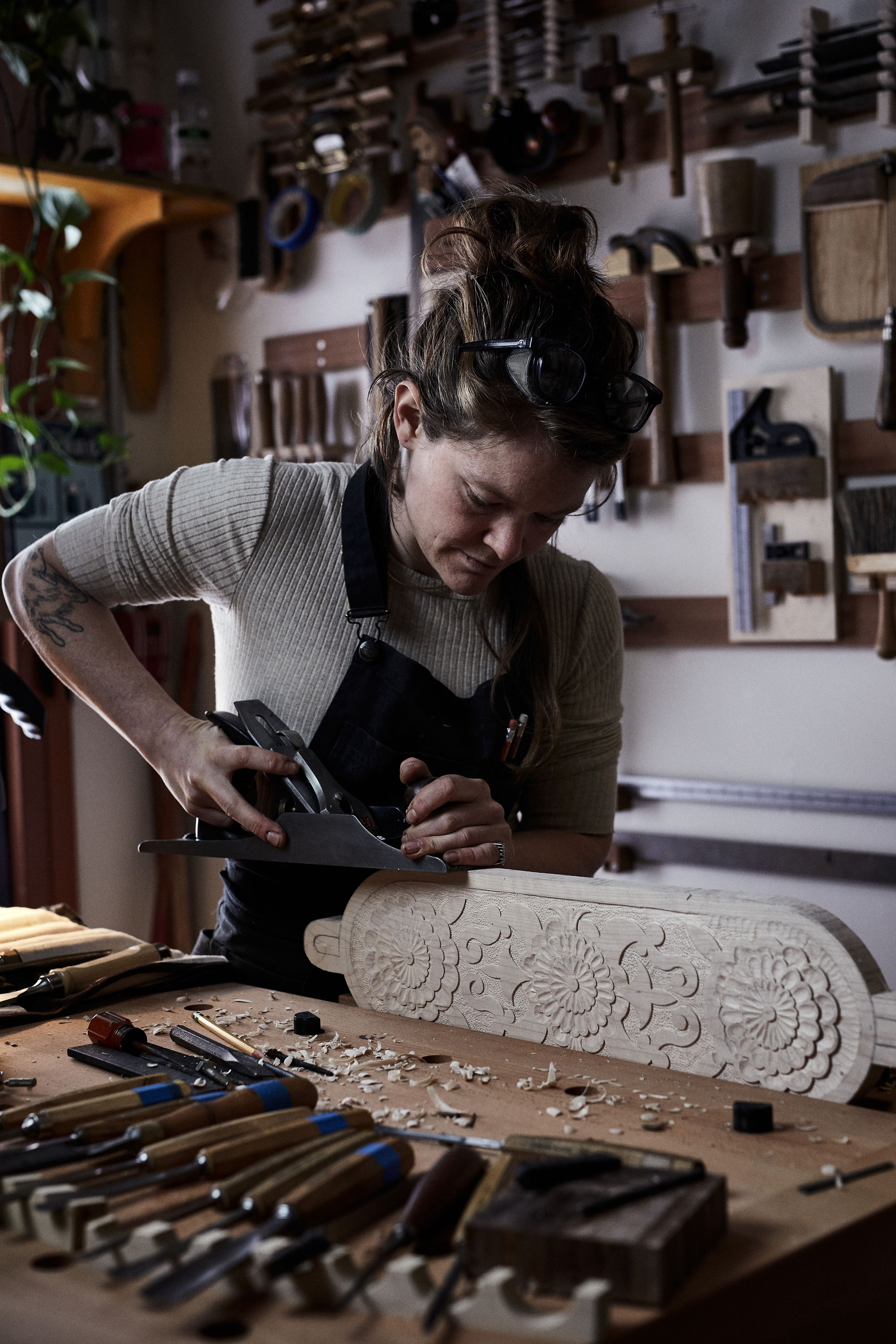
“I’m making peace with what I have at hand. This hearkens back – some people are inspired by limitations and boundaries. What can I do when I only have these things? I’m using it as an opportunity to apply the skills I have to a completely different kind of work. If you’re a furniture maker you’re already excited by rules and boundaries. This is just an opportunity to dig deeper into that perspective on making.”
The book Emanuel Goldberg and His Knowledge Machine (2006; Libraries Unlimited) tells the story of Aspen’s paternal great-grandfather.
— Nancy Hiller, author of Making Things Work
*This series is my version of all those recipes for comforting soups that have proliferated across the web in response to enforced isolation and anxiety.