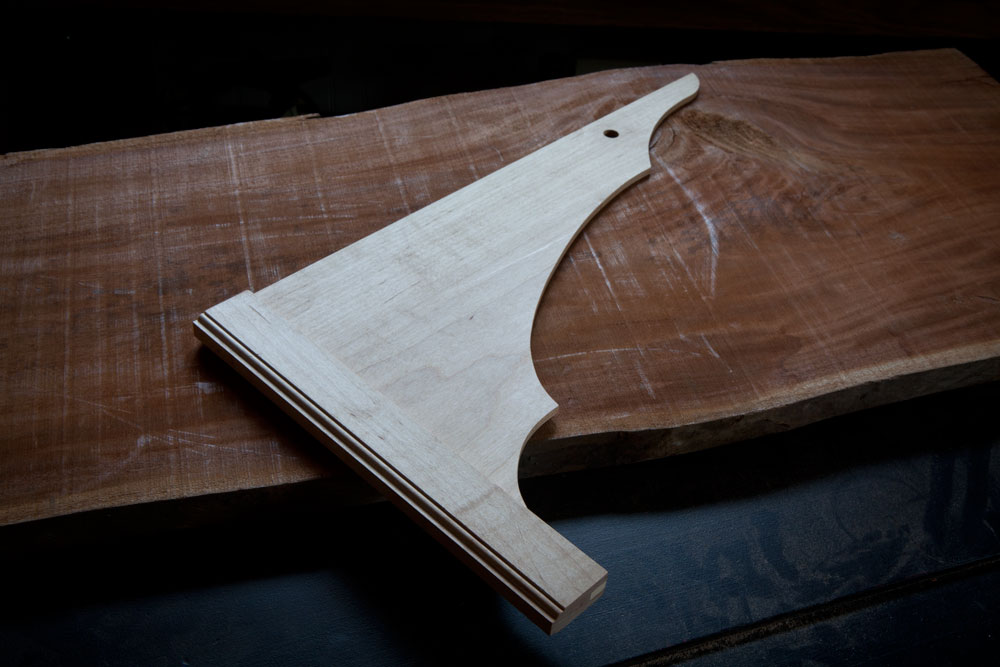
One of the variants on the Melencolia I square has its blade stretched out in width until it looks almost like a bat’s wing.
This square shows up in the late 16th-century Wierix plates shown from my first entry on this topic. A nearly identical square shows up in the title page to the book “The Childhood of Jesus,” by Hieronymous Wierix. (By the way, that plate is a treasure trove of rabbit holes for investigation.)
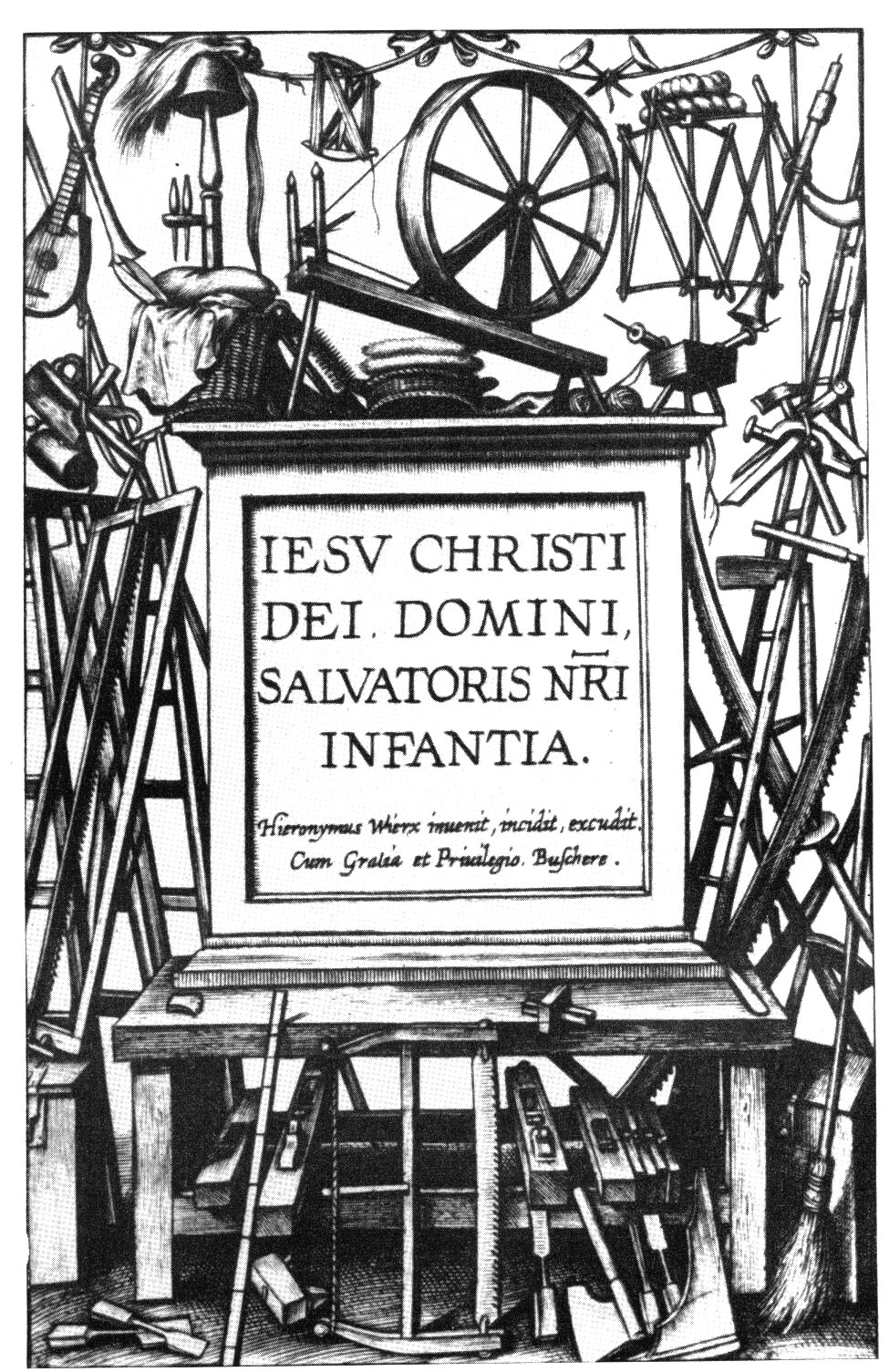
The Wierix square looks a lot like a modern SpeedSquare, with a wide and triangular blade and a small stock. The curves on the blade have a gothic look to them.
While it is easy to start thinking of uses for these curves, I think they primarily serve two purposes:
1. To make it efficient to cut two blades from one rectangular blank. After cutting out about a dozen of these early-style blades this week, I’m struck by how often the waste can be used to make an identical blade. This, I think, is more important than the decorative shapes on the blades.
2. The decoration exposes more end grain along the length of the blade, making the tool more responsive to changes in humidity.
These squares are even easier to make than the Melencolia I square. The stock in this example is 3/4” thick, 1-3/4” wide and about 12” long. The blade is 1/4” thick, 12” wide and about 20” long.
The stock of these squares isn’t always moulded – sometimes it’s just a rectangular stick. I planed two moulded edges on mine using a 1/2” square ovolo plane. Then I plowed a 1/4”-wide x 1/2”-deep groove along one edge.
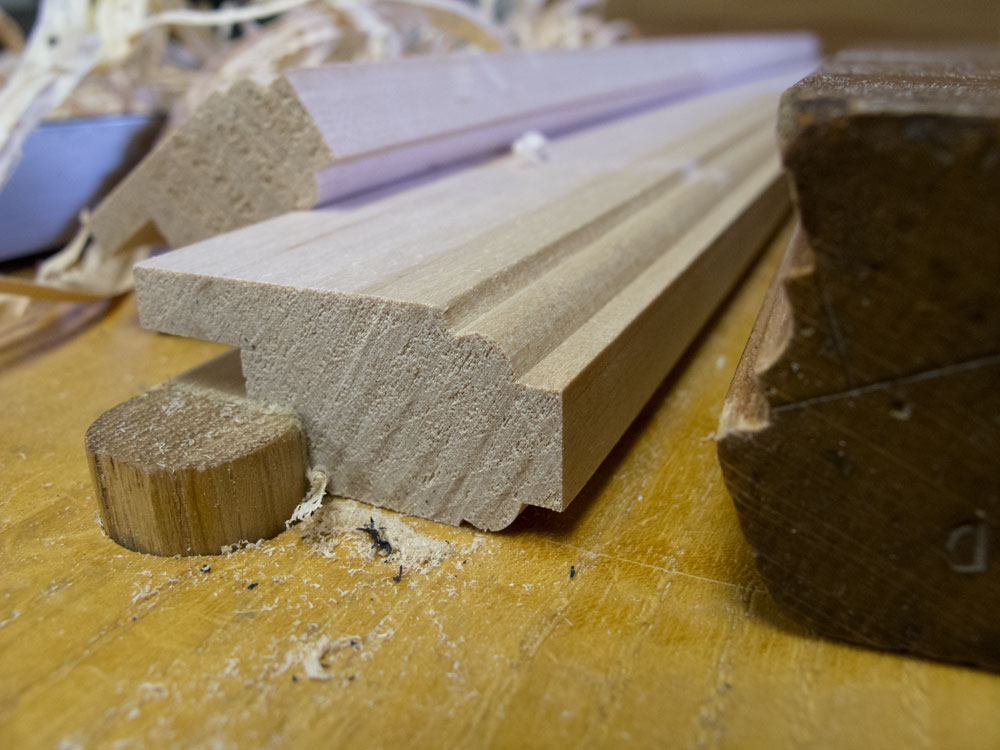
The shape of the blade was the most difficult part. I mucked around in SketchUp for a while, but then found the correct arches by drawing them out on paper with a set of French curves. A saw and a rasp finished the blades.
Then I glued up the two parts, trued up the blade and added a coat of finish.
These are handy for layout because the blade rests on the work and won’t let the stock totter. This makes it easy to mark square lines across a board. As a result of the large blade, however, these squares are no good for checking an assembly for square on the outside of the assembly.
But for two scraps of wood, they are pretty handy.
— Christopher Schwarz
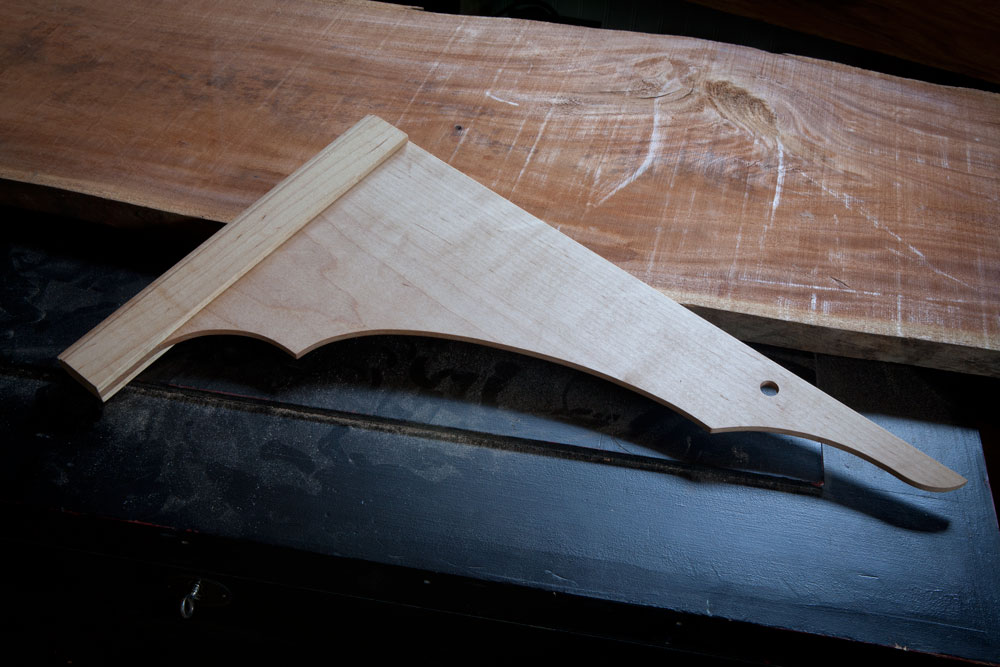
Like this:
Like Loading...