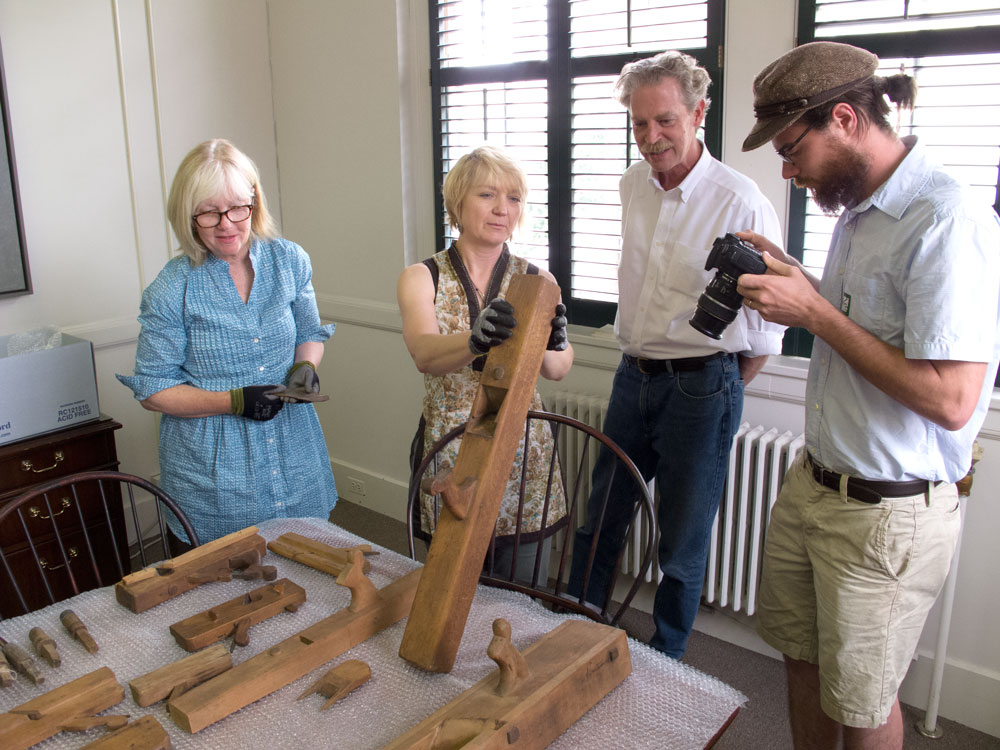
Immediately after arriving in Maine last week, Thomas Lie-Nielsen took me and some of his key employees to the Farnsworth Art Museum in nearby Rockland, Maine. The trip was to view the tools contained in Jonathan Fisher’s tool chest.
Joshua Klein, a woodworker who has been studying Fisher, met us at the museum and we were quickly taken to the Farnsworth’s administrative offices upstairs. There, in a corner room, the employees had laid out about 50 of Fisher’s tools with his tool chest sitting on the floor against the wall.
It was an interesting, and somewhat unusual, collection of tools. Of course, Fisher was an interesting and unusual fellow who invented and built all sorts of contrivances and recorded them in his illustrated journal. Some of the things on the table we couldn’t identify. Could that be a slitting tool used to make woven hats (the Fisher family made a lot of hats)?
Other tools were quite familiar.
With the help of the museum staff we examined the tools, asked a lot of questions out loud and simply puzzled over some of the objects in this unique collection. Klein was interested in the tools because he has been researching Fisher’s woodworking (perhaps for a future book). Lie-Nielsen was particularly interested because Fisher is one of his relatives.
(By the way, if you haven’t read anything about Jonathan Fisher, check out the web site for his house museum here. The Wikipedia entry on him only scratches the surface. He was a remarkable and industrious man.)
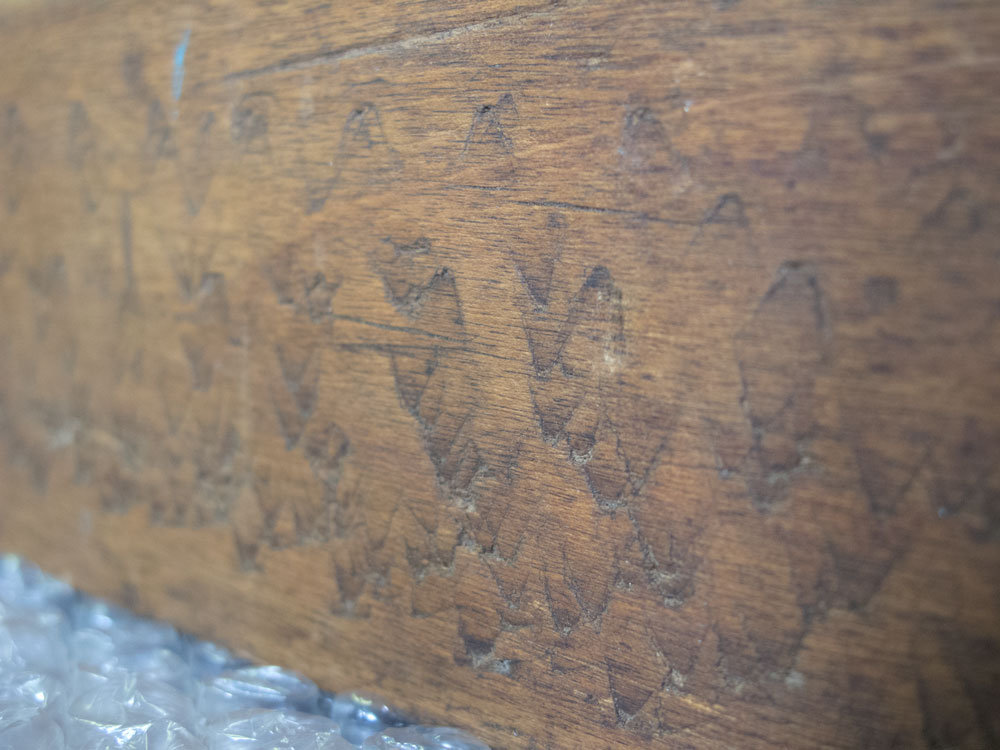
During our visit to the Farnsworth, I kept focusing on Fisher’s long planes, especially his jack, try and jointer planes. All three of them were festooned with an unusual triangular indentation. The “stippling,” for lack of a better word, was only on the sidewalls of these planes. It wasn’t on top of the stock. And it wasn’t on the sole. (Interestingly, it also wasn’t on his smoothing plane nor any of the moulding planes we examined.)
What was this this for? Deneb Puchalski of Lie-Nielsen Toolworks wondered if it could be something to improve one’s grip on the plane. But the stippling was everywhere on the sidewalls, and not on the top of the plane where you grip it.
There was no rhyme or reason for the marks, and so my speculation is this: It was done by a bored child who was allowed to decorate the sides of the planes with a hammer and some sort of triangular tool.
We might never know the answer. Or perhaps Klein will uncover the answer in one of Fisher’s letters or an unread journal entry.
Next time: One (or perhaps two) of Fisher’s many workbenches.
— Christopher Schwarz
Like this:
Like Loading...