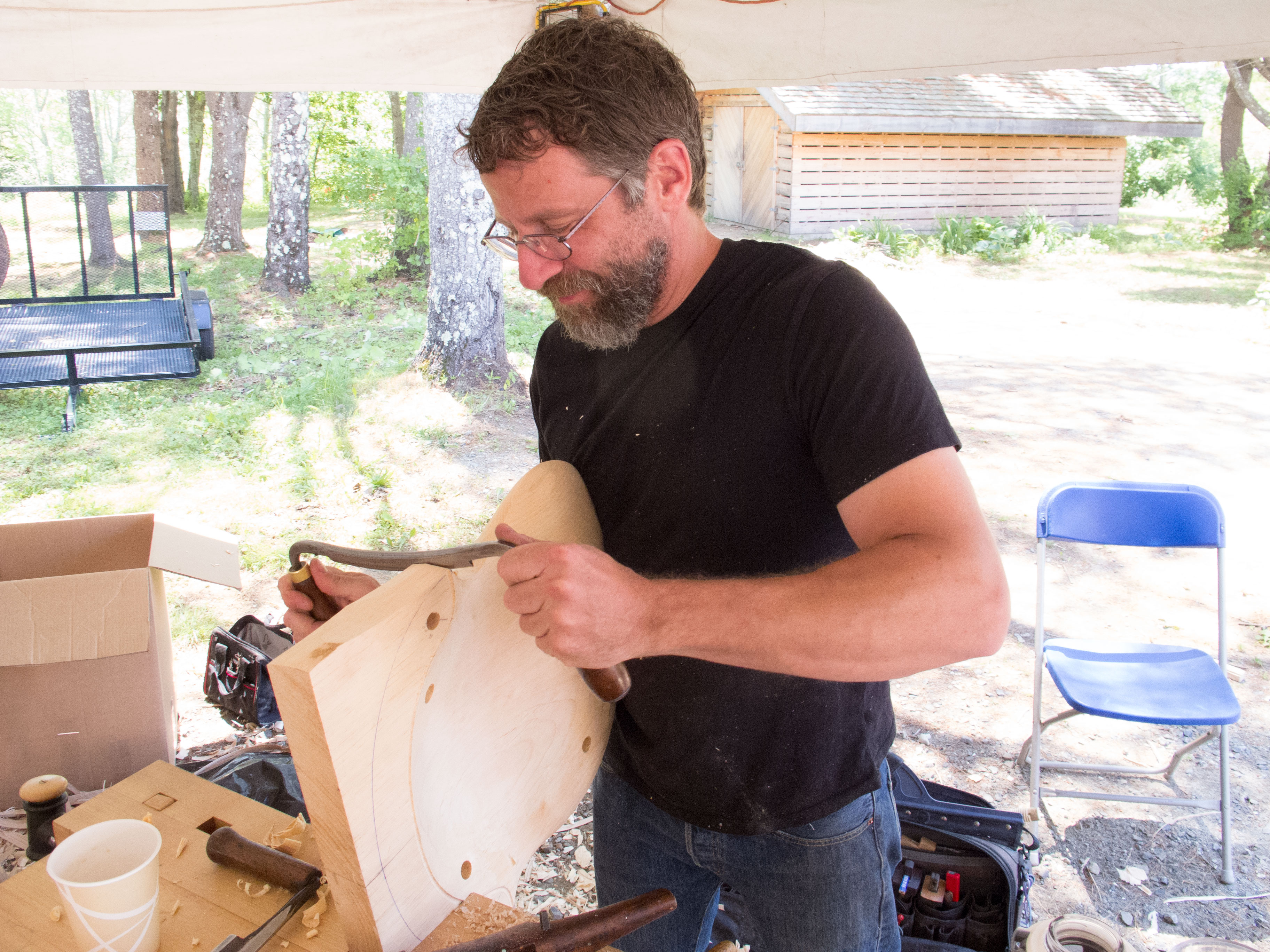
Peter Galbert, author of “Chairmaker’s Notebook,” is widely considered to be one of the finest chairmakers alive today. He’s also a sculptor and painter. And teacher. And writer. He’s an inventor of clever chairmaking tools, which have propelled several prosperous toolmaking businesses. He’s lived in Manhattan, in upstate New York and central Massachusetts, raising goats and chickens, and in Boston. He cooks. He travels (most recently with his partner, renowned landscape architect Stephanie Hubbard, to Baja where they dreamed of another life spent rescuing Mexican street dogs together). Nick Offerman, in his book “Good Clean Fun,” dedicated an entire chapter to him. The man is not yet 50.
And yet, he’ll probably cringe when reading this.
A self-described introvert, Peter says he feels like he’s already received more exposure in life than he should. Fellow woodworkers joke, using the word “hate” when talking about him, which is actually another word for “admire” (tinged with jealousy). For Peter is a rare human — talented, yet approachable. Intelligent, yet unpretentious. And he’s a strong believer in the importance of connecting with others — a belief that stemmed from several isolating stints in high-end furniture and cabinetmaking shops in Manhattan.
But first, the beginning.
Peter was raised in the northern suburbs of Atlanta, before it became the definition of urban sprawl. His neighborhood was surrounded by farmland and plenty of wooded space. “We didn’t have the Internet then, so we played in the creek a lot,” he says. In his immediate family he has a sister and two brothers, but then he mentions a half-sister and says he’s very close to her half-brothers. “When we get together, there is a lot of us,” he says, laughing.
Early on Peter showed an interest in drawing and making things, pursuits his mother always encouraged. It wasn’t the typical teenage comic book art, although he says he imagines he would have enjoyed that. Rather, even at a young age Peter was most interested in depicting things realistically, transposing the world around him.
Peter attended the School of the Art Institute of Chicago, where he studied drawing and painting, and did some sculpture work as well. He dropped out for a couple years, worked and travelled, and then enrolled at the University of Illinois at Urbana-Champaign, “mainly because I knew I wanted to be a college graduate,” he says. He majored in photography, while continuing his art studies, and graduated in 1995.
Without a broad skill set but an eagerness to learn, Peter moved to New York City. His friends were there and it was the mid-1990s. Things were booming and rent, even in Manhattan, was reasonable. “It was a very positive time to be there,” he says.
Peter landed work in a cabinet shop, but it was physically demanding and mentally isolating. He knew he wanted — needed — something else. He hopped around a few places, even landing a gig with the Smithsonian, building everything from pedestals to grass huts to help display extraordinary artifacts and art. He describes that work as amazing — simply because he was able to be so close to objects he loved — and yet he wanted a more intimate relationship with wood.
By chance Peter noticed a “for rent” sign one day while walking the streets of Manhattan. Inside was a 20’ x 12’ storefront workshop, partly occupied by a guitar maker, Justin Gunn.
“He was so capable of building his whole guitar on simply a benchtop with hand tools and I was so impressed with how organic the process was,” Peter says. “The fact that he took wood and transformed it into something that was quite appreciated for more than just its structural ability or its surface appearance, it was there for its tonal quality, too, and the way that he built it, I was super jealous. I wanted something like that.”
Peter paid $400 a month to share the space with Gunn (who later fell in love with a Dutch woman, moved to Holland and became a musician). Given the space, the fact that he could only use hand tools, and his desire to build something both beautiful and functional, chairs made most sense. And so, Peter became a chairmaker.
“Woodworkers are notoriously a romantic lot,” he says. “They pour their heart and soul into it and get pennies out. It’s a very tough, tough business.” Chairs required little overhead. “You can make them essentially for nothing, the materials are almost free they’re so cheap. And then the question was: Could I get the buying public to respond in such a way that I could start to capture back some of my input in the form of their purchase? And then it just became about communication. The more they could understand about why I was committed to doing things the way I was and what I was doing the more they started buying. So I found that education was one of the biggest components to what I was trying to do.”
By 2000, the low-rent-in-Manhattan gig was up. Peter was faced with a choice: rent another workshop way out in Brooklyn and continue to struggle with the lack of materials (trees) or move to the county. Two hours north he found a farmhouse with 50 acres that he could rent for the same amount of money he would have spent on workshop space in Brooklyn.
At first, Peter lived the country life only part time. He and his wife at the time commuted back and forth each weekend. But when his then-wife became fed up with corporate life in New York City, and they recognized the fact that they were never very happy on the return drive each Sunday, they took it as a sign and moved to upstate New York for good.

In 2010 Peter moved to central Massachusetts, lived there a couple years, divorced, and lived there for a couple more years. In the last few years he met his partner, Stephanie, and last year he moved to Boston, where she worked and lived.
Despite it being city living Peter has a small yard (where you can find him barbecuing most summer evenings) and there’s a separate garage. He works in a 20’ x 20’ workshop, listening to classical music or operas he can’t understand, or Sherlock Holmes books on tape. The location is ideal, as it’s close to North Bennet Street School, which is where he’s spending most of his teaching hours this year.
Eventually he says he’d like to get back to the country. “I love that life, it’s an amazing life to live, it’s really charmed.” But for now, he’s happy.
When I spoke with Peter he was at the State University of New York at Purchase, where he had been since early October, experimenting with new work thanks to a grant.
“This is way more than I could ever ask for,” he says about life in general. “I can do a lot of what I love doing and like right now, this thing I’m doing in New York, getting paid to explore anything I want to do which is crazy but it’s come my way because of my efforts in chairmaking and writing — people want to see me do creative things.”

Peter’s residency ended in mid-December. While there he worked mostly on sculptures, carving logs while also splitting them to make it look as if objects were embedded in them. “It’s a fun, interesting way to re-approach the split log,” he says.
He also dabbled in chair work, hoping to develop new methodologies to use at home, and taught three hours a week. His workspace was completely accessible to students all day long. He admitted it was weird at first — he had become quite used to his private hovel, but he says the experience enabled him to break open some long-held habits that weren’t necessarily positive. “It was very inspiring,” he says, when asked about interacting with the students. “They’re very creative and thoughtful people.”
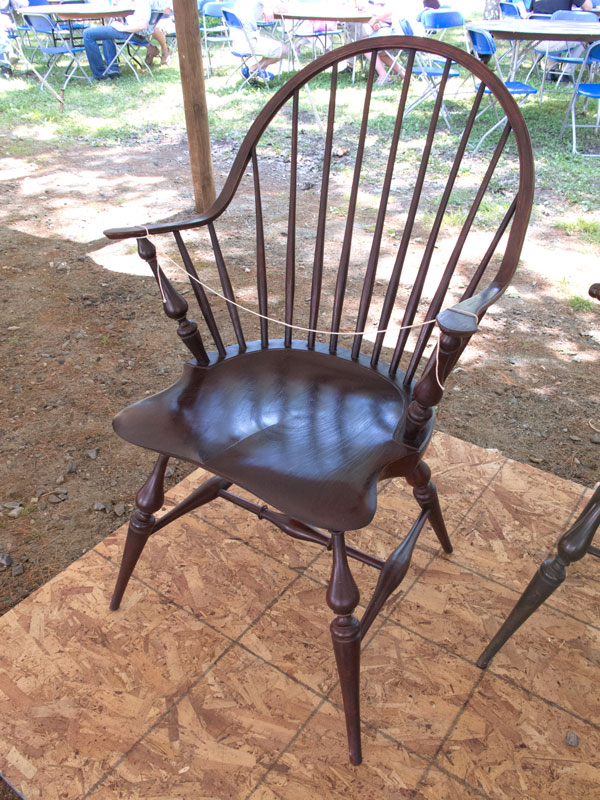
At home, the makeup of Peter’s day is largely spent taking care of chair orders for clients. But his days vary. There are speaking engagements, the occasional trade show (which is where he basically hangs out with friends, he says) and teaching gigs. (In addition to the North Bennet Street School, Peter’s taught at the Penland School of Crafts, the Center for Furniture Craftsmanship, Peters Valley School of Craft, Kelly Mehler’s School of Woodworking, Highland Woodworking, Arrowmont School of Arts and Crafts and Port Townsend School of Woodworking.)
“It’s a strange business,” he says. “People want to quantify it somehow. I simply engage the craft. I don’t see myself as a furniture maker. A lot of other things I do now fund what I do. They all complement each other.”
Throughout the years toolmaking also has complemented Peter’s work. “When I first started I had to make a bunch of my own tools,” he says. They weren’t commercially available, they weren’t designed for chairmakers (rather they were being appropriated for the craft) or they weren’t good. “Plus I didn’t have a lot of money so I just started making my own tools because I needed the jobs to get done that I was doing quicker.”
Peter says he also was suspicious of the amount of tools for sale. “In woodworking, they’ll sell you a tool to help you open the doorknob to get to the shop.” He wanted to be closer to the process than simply flipping through a catalog.
Peter developed a travisher, reamer, adze and drill bits, which he has since handed off to dear friends who have further developed and improved the tools, and now sell them as their own businesses.
Claire Minihan produces and sells the travisher, Tim Manney produces and sells the adze and reamer, and Charlie Ryland produces and sells the drill bits.
Peter also developed a caliper and a sharpening jig for drawknives, which he sells. Next up? Maybe the sightline ruler he writes about in his book. He has an opportunity to do a short run of them — something he’s considering for 2017.
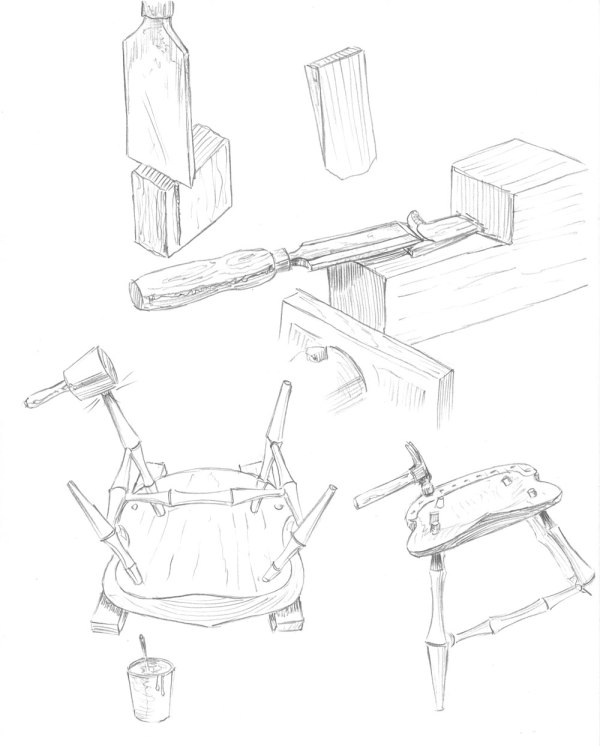
While Peter says folks have been overly enthusiastic about his book, writing a tome of that scale (he spent three years hand-drawing more than 500 of the book’s illustrations) was exhausting. And yet, he’s proud of it, and is open to more (smaller) book-writing projects.
When asked to choose a favorite woodworking book, he spoke of the difficulty in that but then mentioned Eric Sloane’s “A Museum of Early American Tools.” “That really was a huge influence; exciting me about what could be made with simple tools,” he says. “My drawings are just sad imitations of what he did. It’s just the most stunningly descriptive book in drawings and that’s what inspired me to draw my book.” Peter says he aspires to Sloane’s economy of means, being able to create textures and visual awareness in simple drawings — in Sloane’s drawings, Peter says it’s easy to differentiate what’s wood, what’s metal, what’s shiny, what’s matte.
When not building chairs or developing tools, or sculpting, painting, teaching, speaking, drawing or writing, Peter says he enjoys Scotch. And visiting museums. And traveling. He and Stephanie have been all over California, Mexico, Toronto and Australia. I asked him for a favorite place. “It’s more about who you’re with than where you’re going,” he says.
For a man who seemingly has everything, what does he want most from life? “Just to continue to develop and share my own interests and abilities,” he says. “At this point I feel so lucky for what I already have that I feel guilty for wishing for more, but I definitely feel that it comes down to tailoring your efforts so they both maximize your joy and then connect with other people through it. Because that’s the one thing I learned early on — when training and observing, the isolation is really intense. And even though I’m an introvert by nature — I need a huge amount of down time in between social encounters — I was really disturbed by how isolating that trade was. One of my biggest priorities now is my connection to Tim, Claire and Charlie, and so many other people I have come to adore. That’s my community, and that’s huge.”